Ready to proof — CLJ 3/23/22
Proofed by KP 3/23/22
KJ proofed on 3/23
COMPANY NEWS
LANXESS Offers EPDs for Synthetic Iron Oxide Pigments
COLOGNE, Germany – Specialty chemicals company LANXESS announced that it is the first manufacturer of synthetic iron oxide pigments to offer verified environmental product declarations (EPDs) for selected product groups. These EPDs allow LANXESS to deliver comprehensive information about the cradle-to-gate environmental impact of its pigments. The information provided is based on the international ISO 14025 standard as well as the European EN 15804 standard for construction products and services of all kinds.
“Publishing EPDs is a mark of our commitment to setting the highest sustainability standards in the pigments industry,” said Michael Ertl, Head of the Inorganic Pigments (IPG) business unit at LANXESS. “Our iron oxide pigments from the trusted Bayferrox brand are used to add color to concrete building materials, as well as for paints and plastics employed in the construction industry worldwide,” he added.
An EPD describes construction materials, products or components in terms of their environmental impact. These declarations are based on life-cycle assessments as well as the functional and technical properties of the item in question. The environmental product declarations for Bayferrox pigments from LANXESS are tested in accordance with international standards by Institut für Bauen und Umwelt e.V. (IBU), an association of building product manufacturers.
Environmental product declarations are increasingly being used in the construction industry and are among the key prerequisites for structures to be granted sustainability certification. “We are delighted that as a manufacturer of raw materials, LANXESS is striving to deliver this transparency at the product level and thereby enabling its customers in the construction products industry to make much more accurate assessments of the environmental impact of their products,” said IBU Managing Director Alexander Roeder. EPDs for construction materials can help to tip the scales in a building’s favor when it comes to certification.
As a general rule, assessments currently consider whether the building material used has its own certificate. “If raw materials used in production have verified EPDs, as with our Bayferrox brand, these can be taken into account in the construction material’s life-cycle assessment and have a positive influence,” said Holger Wendt, head of the Construction market segment at IPG. Furthermore, EPDs add transparency regarding the environmental profiles of the pigments and thus offer a solid foundation for comparing iron oxide products from different raw material suppliers. This gives manufacturers of building materials the opportunity to optimize and clarify the life-cycle assessments of their own products.
Comparing different products is a worthwhile endeavor because the manufacturing process for synthetic iron oxide pigments uses a great deal of energy. LANXESS has therefore systematically invested in improving the carbon footprint of its pigments over the past few decades by implementing sustainable production processes at its production sites. As Ertl explained, “With EPD verification of our core products, we are making our commitment to life-cycle assessments plain to see for our customers.”
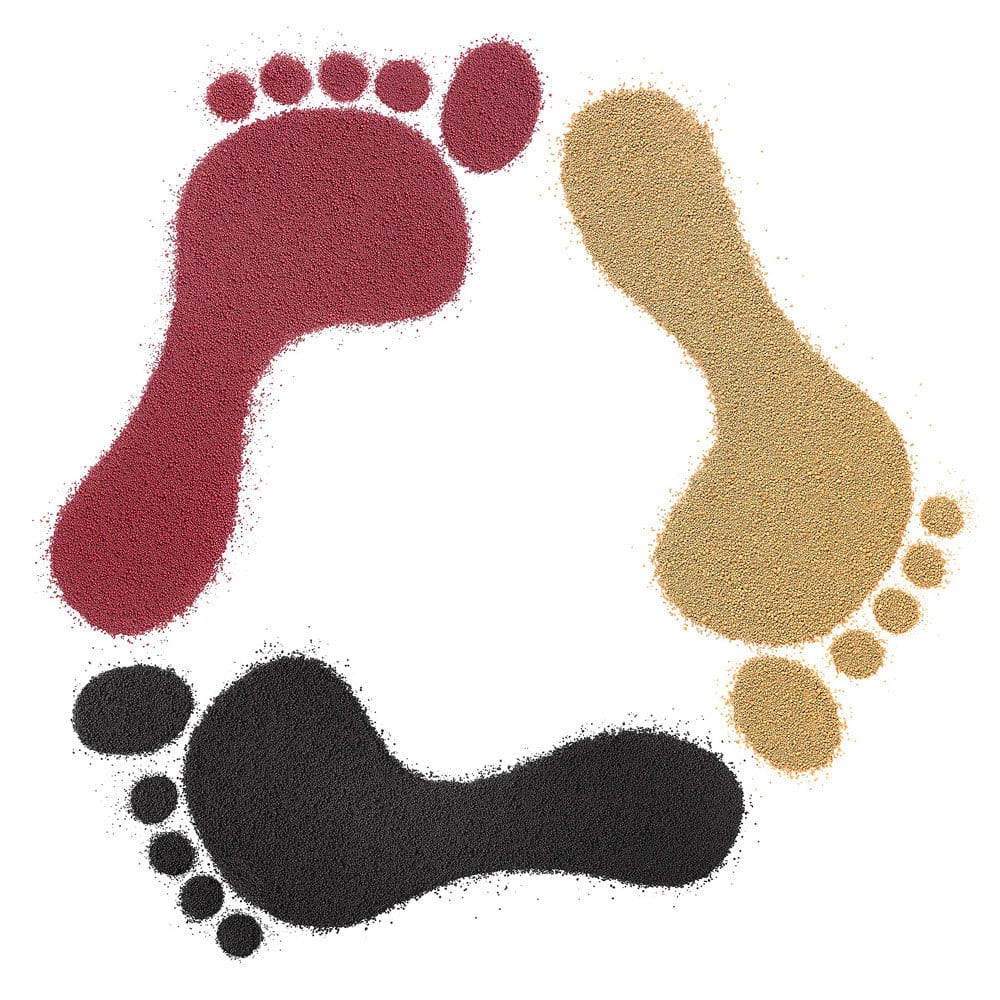
Image courtesy of LANXESS.
Solvay Explores Separation into Two Independent Companies
BRUSSELS – Solvay announced it is reviewing plans to separate the company into two independent publicly traded companies. The two separate companies would be named EssentialCo and SpecialtyCo.
EssentialCo would comprise the mono-technology businesses including soda ash, peroxides, silica and coatis, which are reported as the company’s Chemicals segment, as well as the Special Chem business. These businesses are reported to have generated approximately €4.1 billion in net sales in 2021.
Solvay reports that upon completion, the separation would establish two leading companies that would benefit from the strategic and financial flexibility to focus on their distinctive business models, market and stakeholder priorities. Under the separation plan, Solvay’s shareholders would retain their current shares of Solvay stock, which will continue to be listed on Euronext Brussels and Euronext Paris. The separation would be effected by means of a partial demerger of Solvay whereby the specialty businesses will be spun off to SpecialtyCo. Solvay shareholders at the time of separation would receive shares in SpecialtyCo pro rata to their shareholding in Solvay SA. It is expected that the shares of each company would be listed on Euronext Brussels and Euronext Paris.
SpecialtyCo would comprise the company’s currently reported Materials segment, including its Specialty Polymers, its high-performance Composites business, as well as the majority of its Solutions segment, including Novecare, Technology Solutions, Aroma Performance and Oil & Gas. These businesses are reported to have generated approximately €6.0 billion in net sales in 2021.
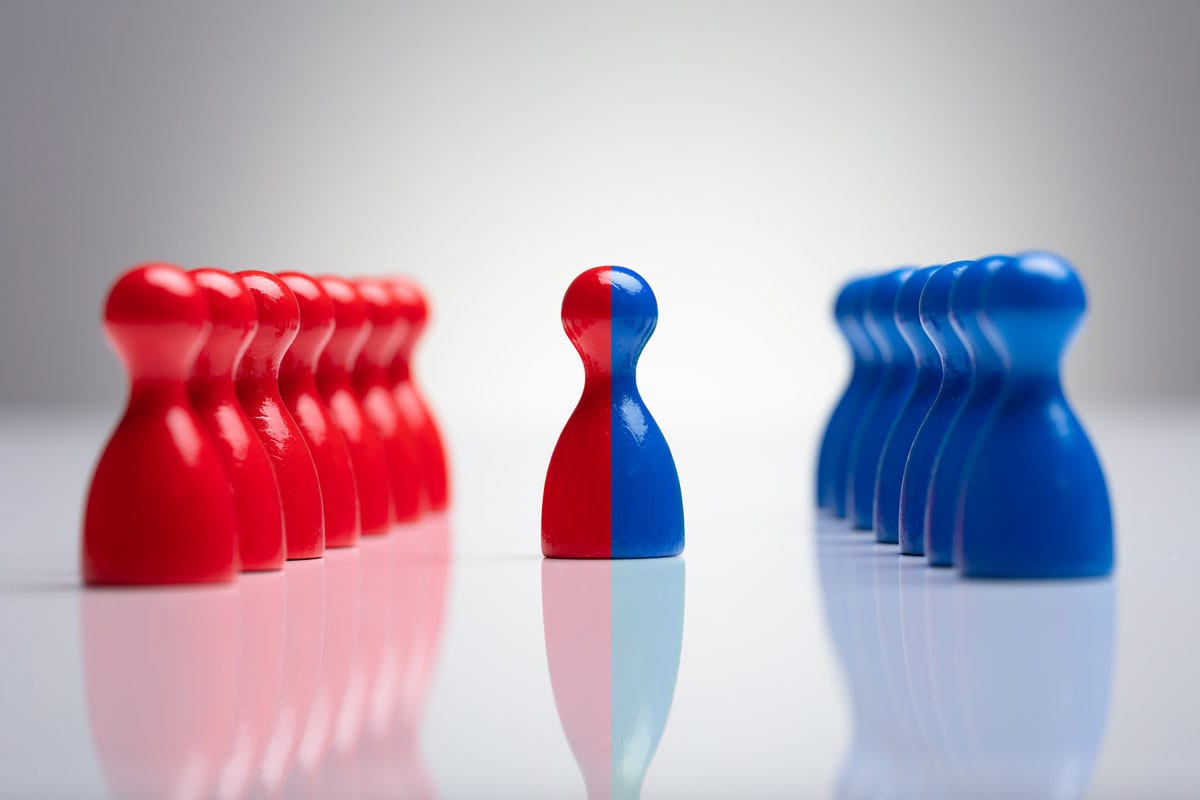
Photo: AndreyPopov, iStock/Getty Images Plus, via Getty Images
AkzoNobel Opens New R&D Facility in UK
AMSTERDAM – AkzoNobel has opened a new £10 million global research and development center at its Slough site in the UK. The facility — home to 120 specialists — will act as a major hub within the company’s worldwide R&D network and help to further advance the company’s innovation capabilities, particularly in the decorative paints space.
The official opening of AkzoNobel’s new R&D center in Slough. Photo courtesy of AkzoNobel.
The facility in the UK is the latest in a series of centers opened by AkzoNobel designed to advance the company’s product development. These include an automotive facility in Poland, an Application Training Center in Dubai, an Innovation Campus in Felling, UK, and a global innovation, development and training center in Qatar for the Marine Coatings business.
“The inauguration of this fantastic new center will help us to continue our long tradition of pioneering new products and developing more sustainable solutions for our customers through ground-breaking innovations,” said AkzoNobel CEO, Thierry Vanlancker, who attended the official opening. “As well as marking the start of a new chapter in the UK, it’s also a clear signal of our ongoing commitment to keep pushing boundaries as part of our People. Planet. Paint. approach to making a genuine and lasting difference to customers, communities and the world around us.”
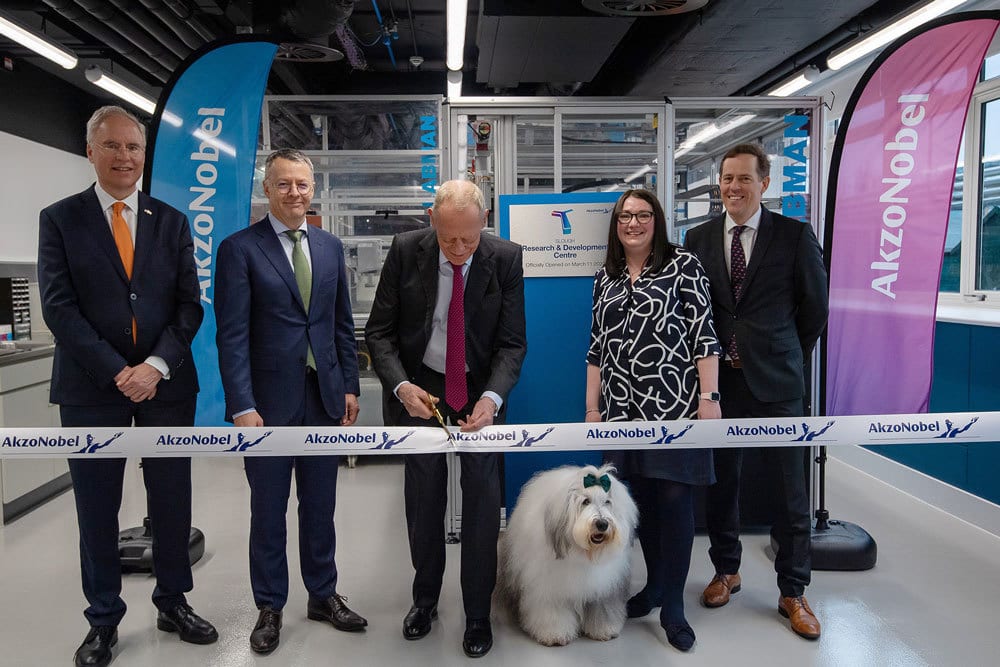
BASF Opens New Automotive Refinish Laboratory Building in Germany
MÜNSTER, Germany – BASF has opened a new laboratory building for the development of automotive refinish coatings and innovations beyond paint at its site in Münster, Germany. The addition reinforces the Coatings division’s global position as a future-oriented and innovative company. “It is another component of our positioning as a global innovation center of BASF Coatings. We are thus complementing a series of global technical innovations. This includes the ‘Lean Lab,’ which we started operating in 2018 at this site, as well as our plant for the functionalization of films for various industries,” said Uta Holzenkamp, Head of BASF’s Coatings division.
With its new building, BASF Coatings contributes towards BASF’s target to reach net zero carbon emission for 2050. “The laboratory building is a huge milestone for the development and formulation of sustainable product solutions. This includes our state-of-the-art waterborne refinish paint portfolio Glasurit® 100 Line and R-M® AGILIS. With the lowest value of volatile organic compounds (VOCs) on the market, they are the eco-friendliest automotive refinish paint lines available,” said Chris Titmarsh, head of Automotive Refinish Coatings Solutions EMEA.
The innovative arrangement of the laboratories, warehouses, offices and meeting rooms enables a completely new, agile form of collaboration that is intended to promote not only efficiency and effectiveness, but also overarching collaboration and creativity.
In addition to manufacturing sustainable products, the site is continuously investing in using energy for production more efficiently, and increases the use of renewable energies. The new laboratories are supplied with thermal energy by using the residual heat from the company's waste incinerator, which is released via under-floor heating. Since the beginning of the year, the electricity purchased at BASF Coatings’ sites in Münster and Würzburg, Germany, has been generated 100% ecologically from wind power. Compared to the previous year, around 4,000 tons of CO2 will be saved in Münster alone.
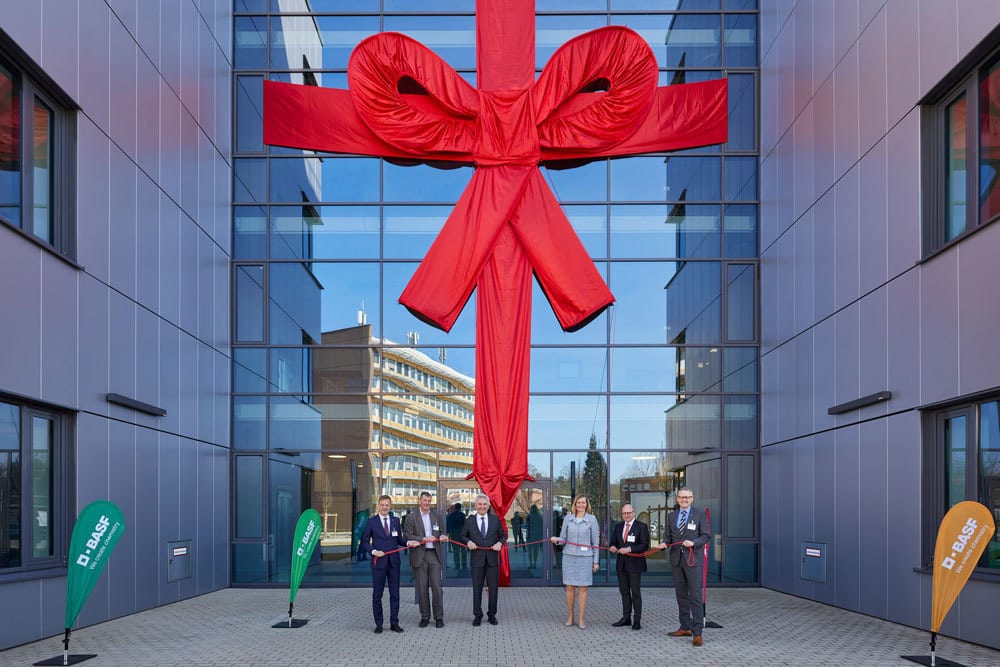
Ribbon cutting at the new BASF laboratory building in Münster, Germany. Photo courtesy of BASF.
Scott Bader Expands MMA Structural Adhesive Production
WELLINGBOROUGH, UK – Scott Bader announced that its Canadian site, based in Drummondville, will begin manufacturing Crestabond® structural adhesives in 2022. The expansion of Crestabond production to Scott Bader ATC will allow the company to meet growing demand for its high-quality methylmethacrylate adhesives (MMA) primerless structural adhesives within the North American market. It will also significantly reduce transport emissions and delivery times, helping the company to deliver a faster, more efficient service for its customers with less environmental impact.
Ingrid Skalleberg, Scott Bader’s Global Product Manager for Adhesives, said, “We are delighted to increase production of our Crestabond structural adhesives. North America is a key strategic growth area for us so to be able to produce Crestabond at our Canadian site, and offer our North American customers shorter lead times, is a great step forward.”
The initial production at Scott Bader ATC will focus on the innovative Crestabond M1 series of 10:1 structural adhesives, suitable for bonding a range of substrates including composites, thermoplastics and metals. The range benefits from varying working times to suit a host of applications in multiple industries, including marine, automotive, wind energy and construction.
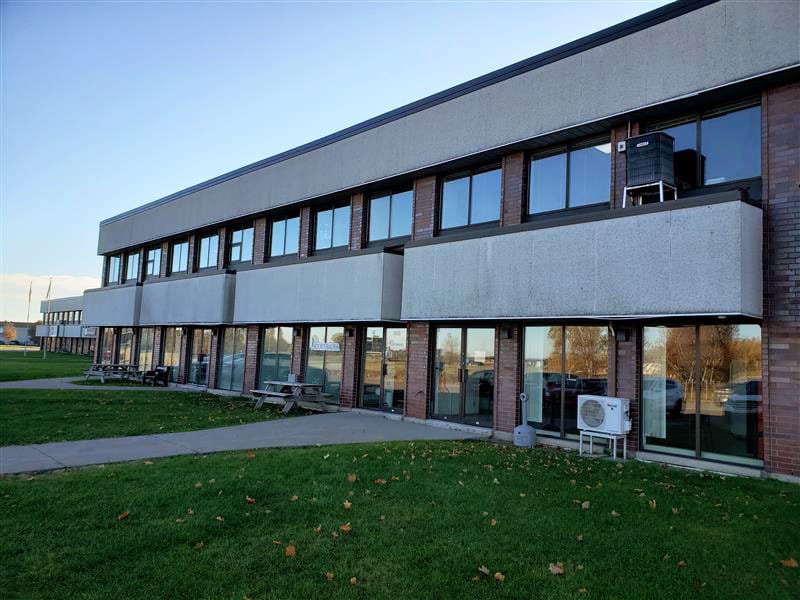
Photo courtesy of Scott Bader.