Ready to proof -- Clare 03/9/22
KJ proofed on 3/14 and sent corrections
Revised 3/14
Ready for author - Clean
Problem-Solving Pigments
for Powder Coatings: Durable, Functional and Colorful
Photo: Cakeio, iStock/Getty Images Plus, via Getty Images
By Mark Ryan, Marketing Manager, The Shepherd Color Co., Cincinnati, OH
The pigments used to color powder coatings have a large impact on their color development, appearance and durability. The standard for high-performance pigments are the inorganic pigments known as Complex Inorganic Color Pigments (CICPs). They provide durable color that can stand up to the most challenging and aggressive processing and applications. They also have excellent dispersion properties so that color formulas are predictable and stable during production. Recent advances have found that besides color, CICPs have properties that give them the ability to address regulatory requirements that give not only color, but functional properties. Lastly, CICPs are highly durable and provide lasting color options for powder coatings formulated with long-lasting resins.
Background
CICPs are a specialized sub-section of inorganic pigments. They are often made from a blend of simple oxides that are then calcined in a kiln from about 600 °C and higher. At these elevated temperatures the metal ions transfer back and forth so that they are no longer simple oxides, but a matrix of multiple metals and oxygen. Perhaps the best known is cobalt aluminate blue (PBl28) used in artist materials. In this new chemical form they have new properties and are stable up to their firing temperature.
CICPs, due to their high index of refraction, are inherently good at scattering light. Particle size control and optimization allow for high opacity and gloss. CICPs are inert because of their inherent inorganic nature and high processing temperatures, and are stable in a wide range of acids and bases, and are resistant to solubilization and migration in solvents and resin systems. This inherent stability means that the CICPs gain widespread regulatory approval — especially when the inherent insolubility of the pigments means that they are able to pass leaching and extractable testing.
This inert nature also makes the CICPs the standard pigments for high-durability, long-term building products, especially coatings based in high-performance resins like fluoropolymers. While simple oxides are also stable, the CICPs have greater color range and chromaticity. CICP pigments come in a wide spectrum of colors, with the notable exception of a true red. They generally lack the ultimate chromaticity or tinting strength of organic pigments, but due to higher scattering they are more opaque.
Properties Beyond Visual Color
The color of a pigment is the prime attribute by which we judge its utility. CICPs, by their inherent nature and properties, can exhibit beneficial properties beyond selectively absorbing and scattering visible wavelengths of light to give the impression of color. Two of these functional benefits are the inclusion of CICPs into a number of food contact application lists around the world and the near IR reflectivity of visually absorbing pigments for ‘cool’ applications.
FDA Food Contact-Compliant and Approved CICP Pigments
CICPs are excellent pigments for FDA food contact applications because of their high heat, acid and base stability, along with their low migration and solubility. CICPs make excellent colorants for powder coated cookware due to their regulatory approvals and inherent stability.
Advances and Specialization in IR Reflective Black CICPs
Infrared (IR) reflective pigments have been used for decades in various applications. The use of IR reflective CICPs has matured into a wide range of pigments for specialized applications not only in building products like window profiles but also in a myriad of other applications where solar-induced heating of materials can cause issues.
The workhorse IR Black pigment is the CI Pigment Brown 29 (PBr29) class of pigment. While our eyes are only sensitive to wavelengths of light from about 400-700 nm, the sun’s spectrum extends beyond this narrow range. Roughly half of the sun’s energy is in the visible (400-700 nm) while the other half is in the near-infrared (700-2,500 nm), with a few percent in the highly damaging 295-400 nm UV range. A black pigment has to absorb in the visible range for color, and most, like carbon black, continue this absorption into the near-infrared. PBr29-based IR black pigments absorb in the visible so that they are dark in color, but near the 700 nm boundary between the visible and IR they start to reflect. When we look at the total solar range of 295-2,500 nm, a standard black will only reflect about 5% of the sun’s total energy, while an IR black will reflect 25% to 30%. The standard black has a Total Solar Reflectance (TSR) of 5% (or 0.05), while the IR Black pigments have around a TSR of 28% (or 0.28). This TSR can be read by a spectrophotometer (ASTM E 903) or specialized equipment (ASTM C1549).
The IR Reflective blacks continue to be one of the ‘hottest’ topics in pigments. The CICP IR Black pigments are the workhorses that provide high IR reflectance, durability, economical use and a broad range of properties that can be tailored to specific applications, especially building products like window and door extrusions.
Controllable Color
CICPs also have inherent coloring properties advantageous for powder coatings. The control of color in powder coatings depends on the predictable dispersion of the colored pigments. CICPs have predictable dispersion properties that produce color that is controllable and stable. CICPs give controllable color because the relatively higher use rates as compared to organic pigments allow more advantageous mixing ratios.
The color strength and dosing for correct color is most apparent when trying to tint and tone near-white colors. Most powder coatings made with straight TiO2 will have a yellow cast to them due to the yellowness inherent in the resin. Toning the whites to appear ‘whiter’ is often done with small amounts of violet. The addition of violet doesn’t actually make the white brighter, but it reduces the positive b* value to a more neutral/blue-shade value.
Two ways were examined to affect this color change in a TGIC-free polyester coating. The first used organic Carbazole violet CI Pigment Violet 23 (PV23) and the other the inorganic CI Pigment Violet 16 Manganese phosphate (PV16). The formulas used are seen in Table 1. The organic pigment is much stronger than the inorganic pigment. So much so that a pre-blend of the PV23 and TiO2 had to be made at a ratio of 59:1 (TiO2 to PV23), and then that used as a colorant.
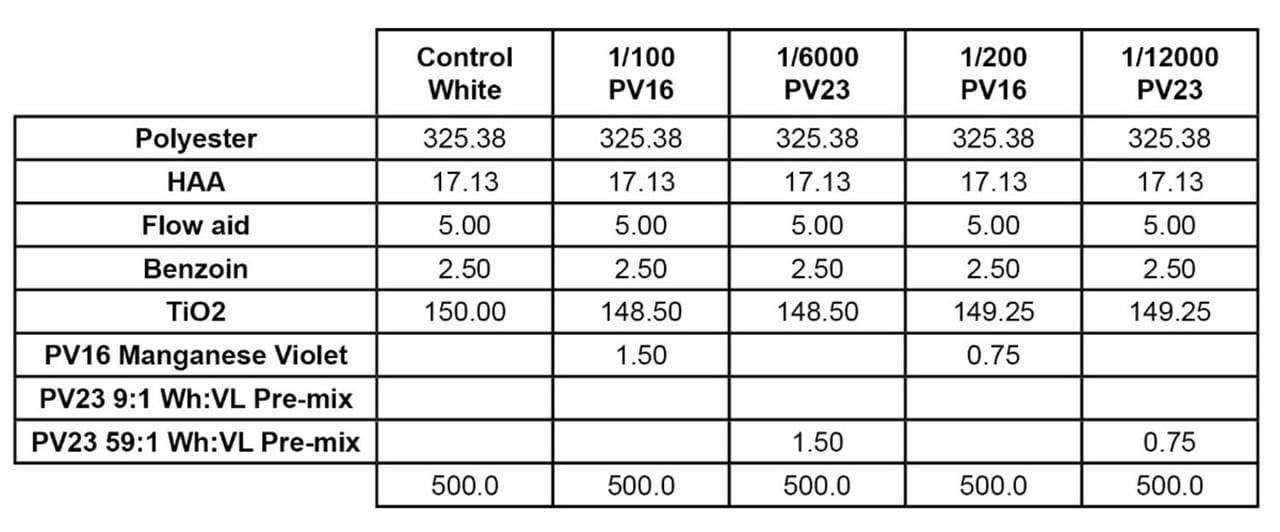
TABLE 1 ǀ Toning of TGIC-free whites with violet.
The color results from these formulas can be seen in Table 2. The material was run through the extruder and then run again so that three extrusions of each material were made to see how processing affected color (Figure 1). Instead of the first extrusion being used as a standard, a formula with no violet and only TiO2 was used as the standard. The deltas to this straight white are in Table 4, which can be viewed a bit farther down in this article.
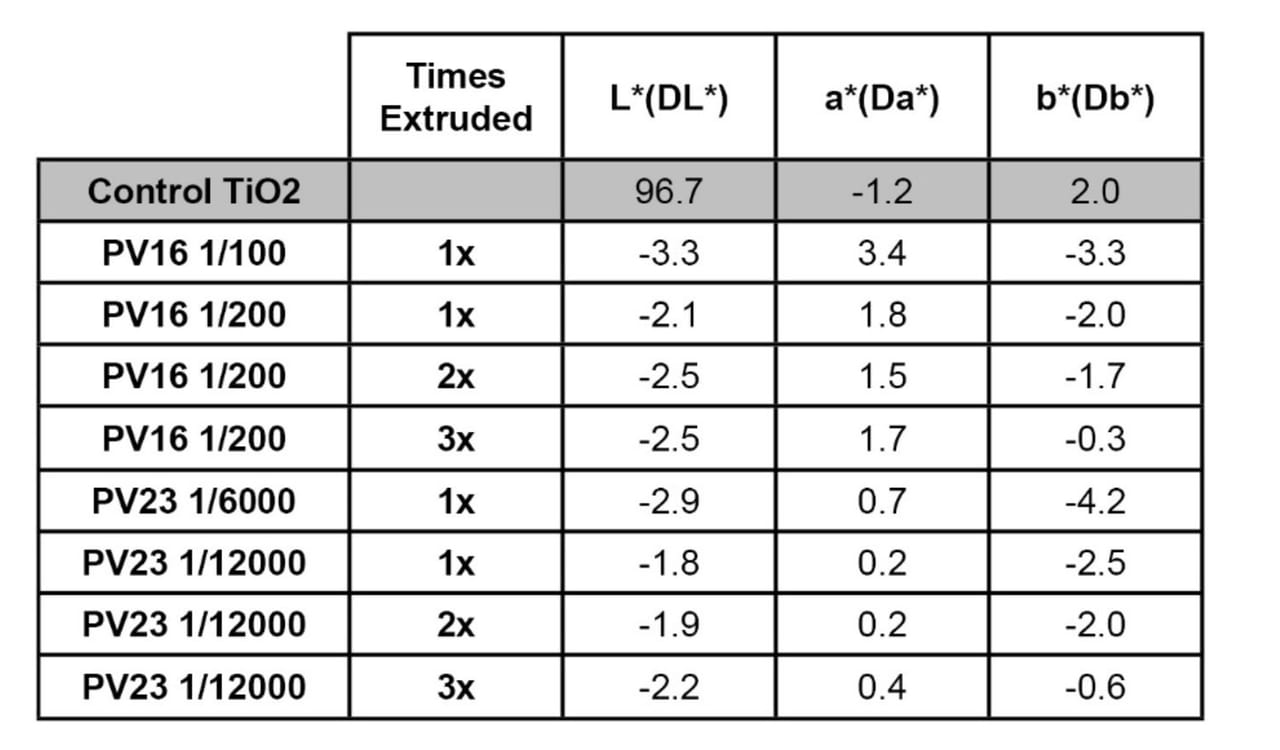
TABLE 2 ǀ Color results for toning of whites.
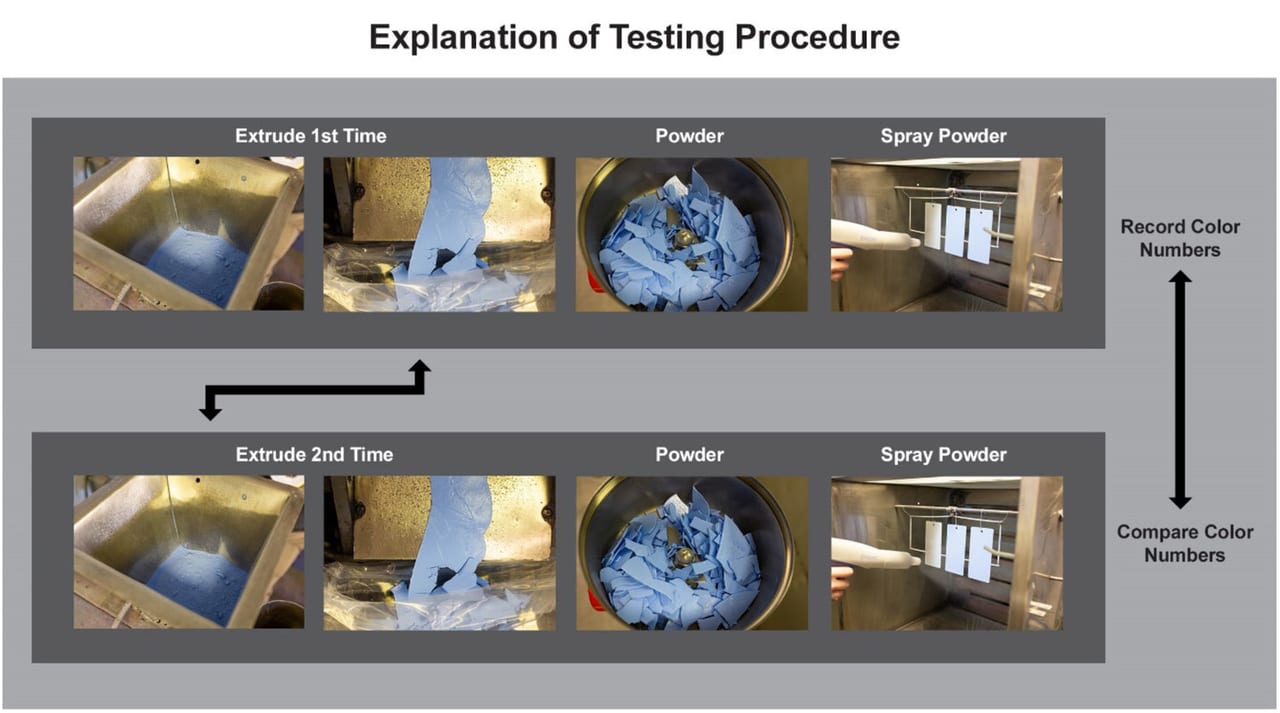
FIGURE 1 ǀ Explanation of testing procedure.
The results show that very little violet is needed to improve the appearance of the standard white, which has a notable yellow cast with a b* value of 2.0. Initial violet levels used were too high and were cut in half to get closer to the neutral values of 0,0 (a*,b*). The inorganic PV16 needed to use 1/200 (0.5%) based on TiO2, while the stronger organic PV23 needed to be used at a level of 1/12,500 (c. 0.017%). This very low use rate necessitated the use of a pre-blend.
The color shift from the multiple extrusions is interesting because the color shift is similar for both violets. This implies that the resin is adding more color to the system with each extrusion pass, and the violets are being ‘dragged’ more yellow (Figure 2). While the a* and b* values are more neutral, the L* value is dropping. Anytime an absorbing pigment like a violet is added to a broadly scattering pigment like white, the reflectance goes lower, here in the wavelengths associated with yellow because of the absorbing pigments violet tone.
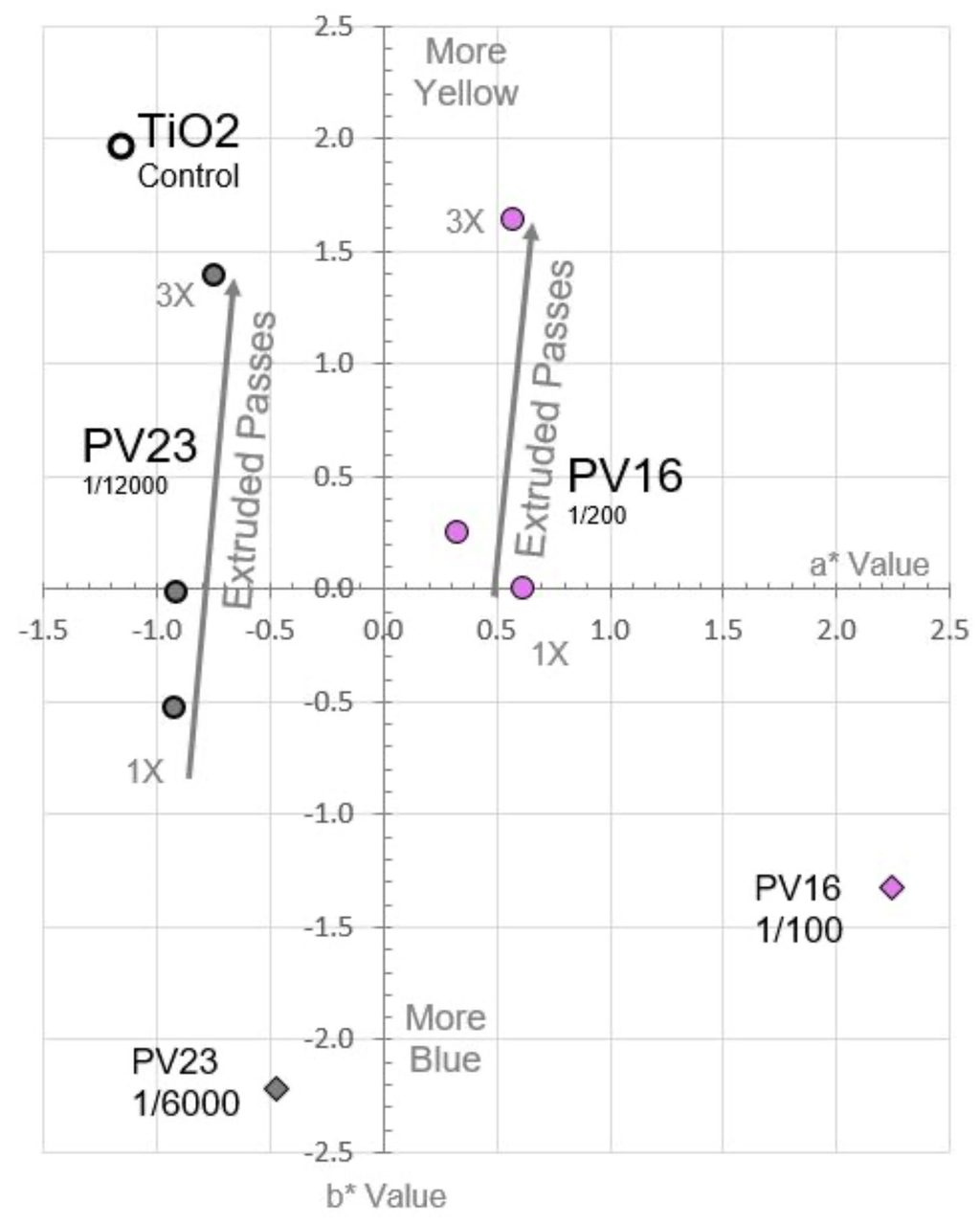
FIGURE 2 ǀ Toning whites with violet.
The key is that the inorganic PV16 manganese phosphate doesn’t require the additional step of making a pre-blend mix. Dosing such a small amount of organic PV23 (0.03 on a straight pigment basis) into that quantity of white would be problematic.
Durable Color
Powder coatings are an environmentally friendly way to protect substrates for a number of uses. One of the most demanding applications is for building materials in aggressive environments where heat, ultraviolet (UV) light, moisture, oxidation agents and chemicals, along with simple physical abuse, are present. For these applications, the highest-performance components have to be used if specifications such as those prescribed by American Architectural Manufacturers Association (AAMA) 2605 are to be met. Part of the equation is the resin used while the other is the colorant.
Fluoropolymer resins were developed in the 1960s and typified by the polyvinylidene difluoride (PVDF) chemistries for coatings applications. During initial testing, the white coating formulations performed well. An issue arose when colors other than white were formulated and tested in high-UV climates like South Florida. When tints were made using TiO2 with organic pigments, the tints would lose color within a few years of weathering (Figure 3).
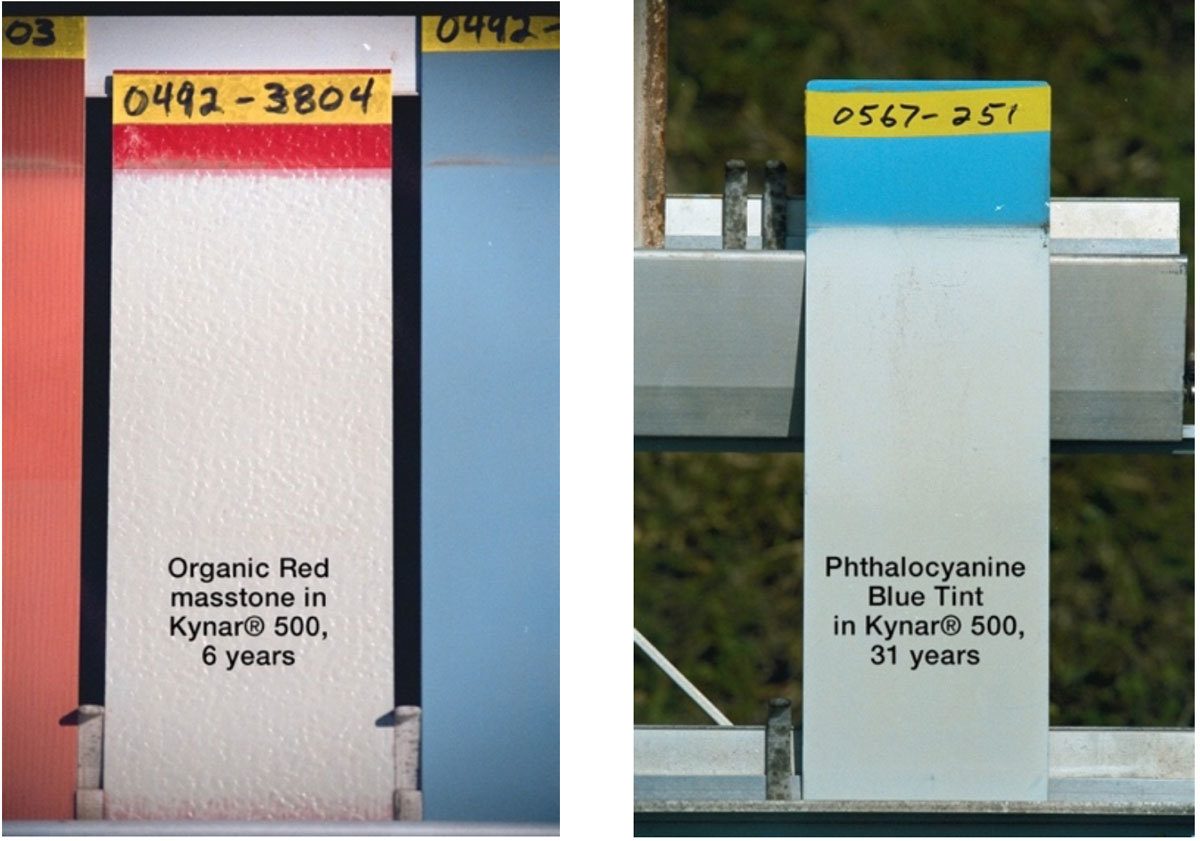
FIGURE 3 ǀ Titanium dioxide tinted with organic pigments in PVDF/acrylic in South Florida exposure. (Photos courtesy of Arkema).
The developers of the PVDF coatings turned to the CICPs because of their inherent properties and use at that time in high-temperature porcelain enamels. Some of the original panels from that study can be seen in Figure 4. The top area marked by the highest red marker is the unexposed portion, the next area is an unwashed portion and the bottom represents a washed area.
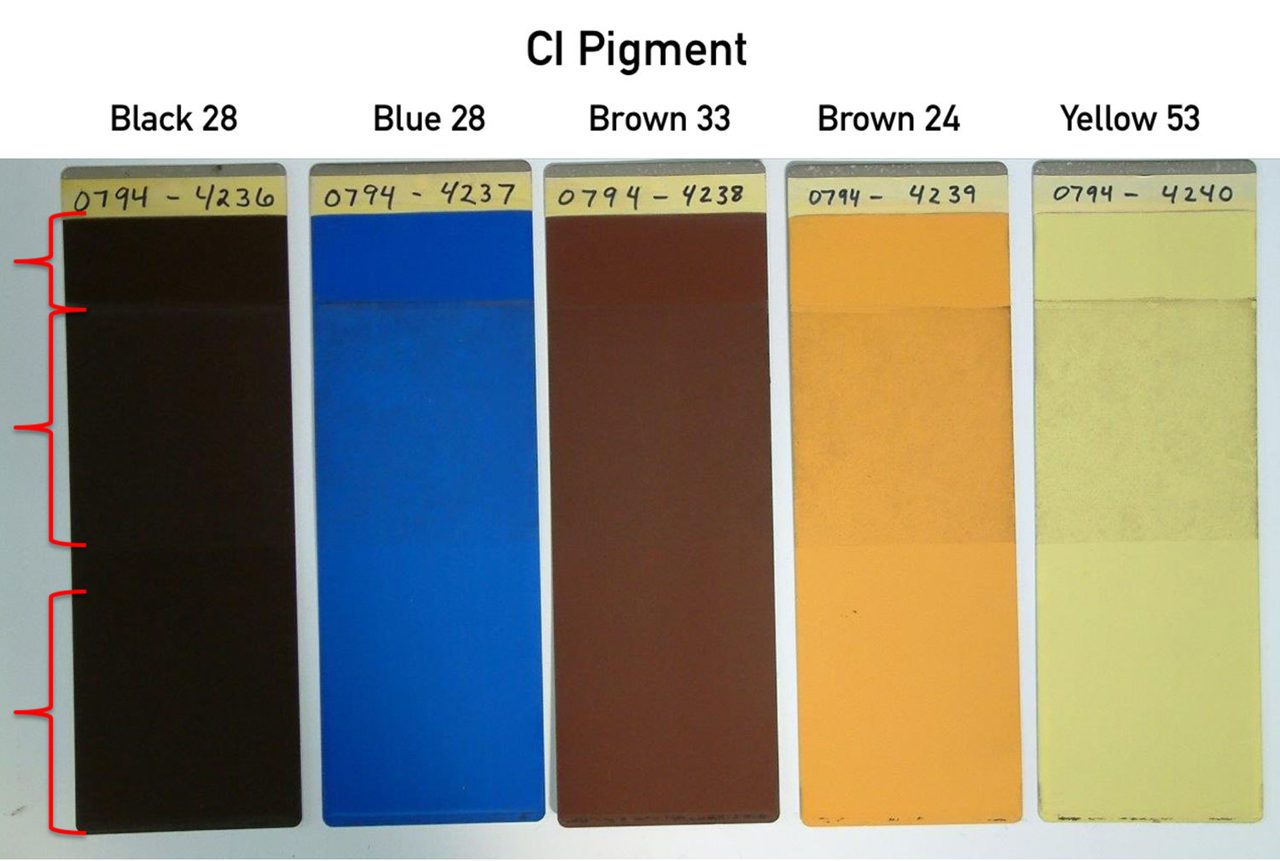
FIGURE 4 ǀ Photos of CICP pigmented PVDF/acrylic in South Florida (31 years exposure). (Photos courtesy of Arkema)
CICPs became the standard colorants used in high-durability coatings applications for liquid and powder coatings for building products. They are especially useful in powder coatings based on fluoroethylene vinyl ether (FEVE) resin chemistry due to their inherent weathering properties, excellent opacity and low oil absorption values, so they provide opaque and high-gloss coatings. The FEVE-based powder coatings give inherent processing advantages in that they can be extruded and processed into powder coatings without the need for specialized equipment.
To demonstrate the performance capabilities of FEVE resins with CICP colorants, a number of panels were coated with an FEVE, crosslinked with a blocked-polyisocyanate, processing additives and pigmentation for masstone colors1 and tints with white. The panels were electrostatically sprayed to thickness around 50 microns (2 mils). The panels were then exposed to a range of accelerated and real-world exposures:
- QUV-A (ASTM 154)
- Concentrated Solar Exposure (Emmaqua)
- South Florida Exposure
Initial results for color retention on masstone panels and tints with white (4 parts white:1 part color pigment) display low DE values (Tables 3-5).
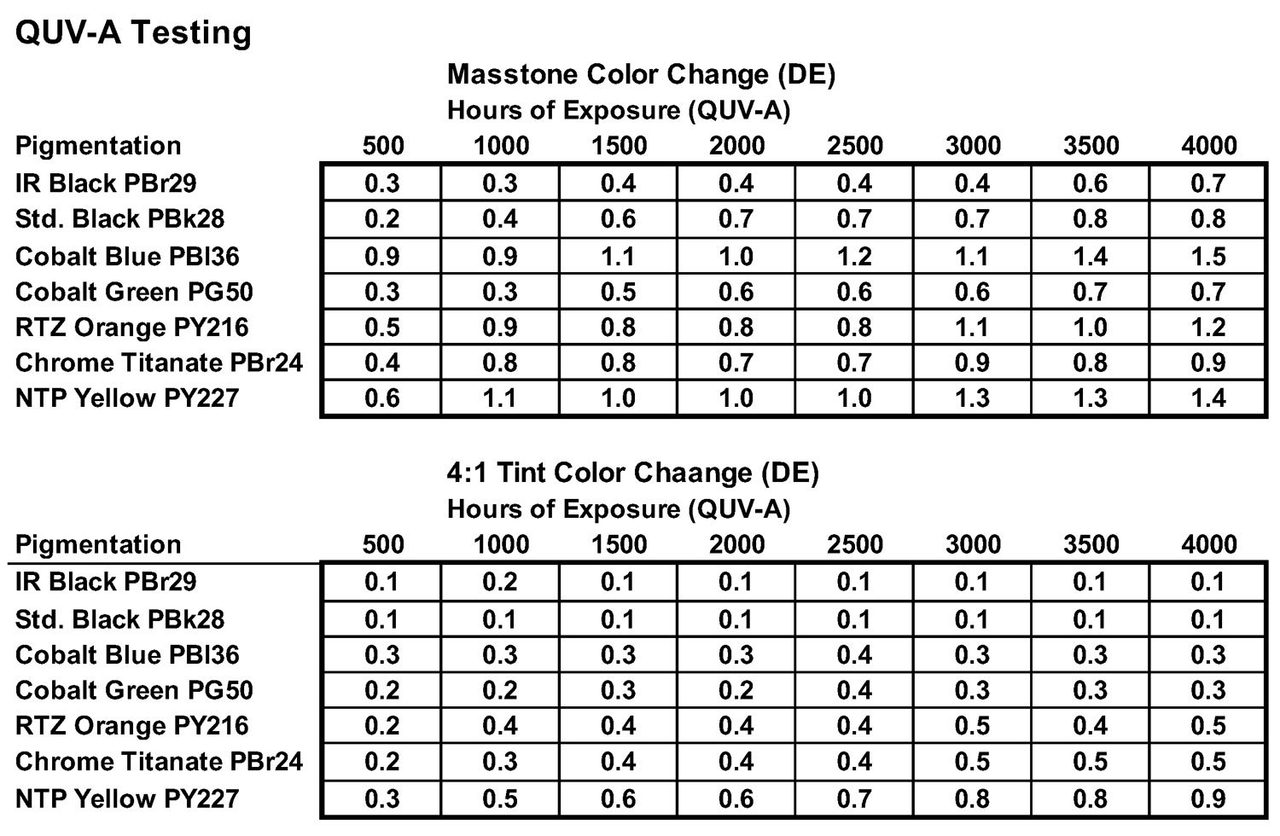
TABLE 3 ǀ QUV-A testing.
TABLE 4 ǀ South Florida weathering at 6, 12 and 24 months.
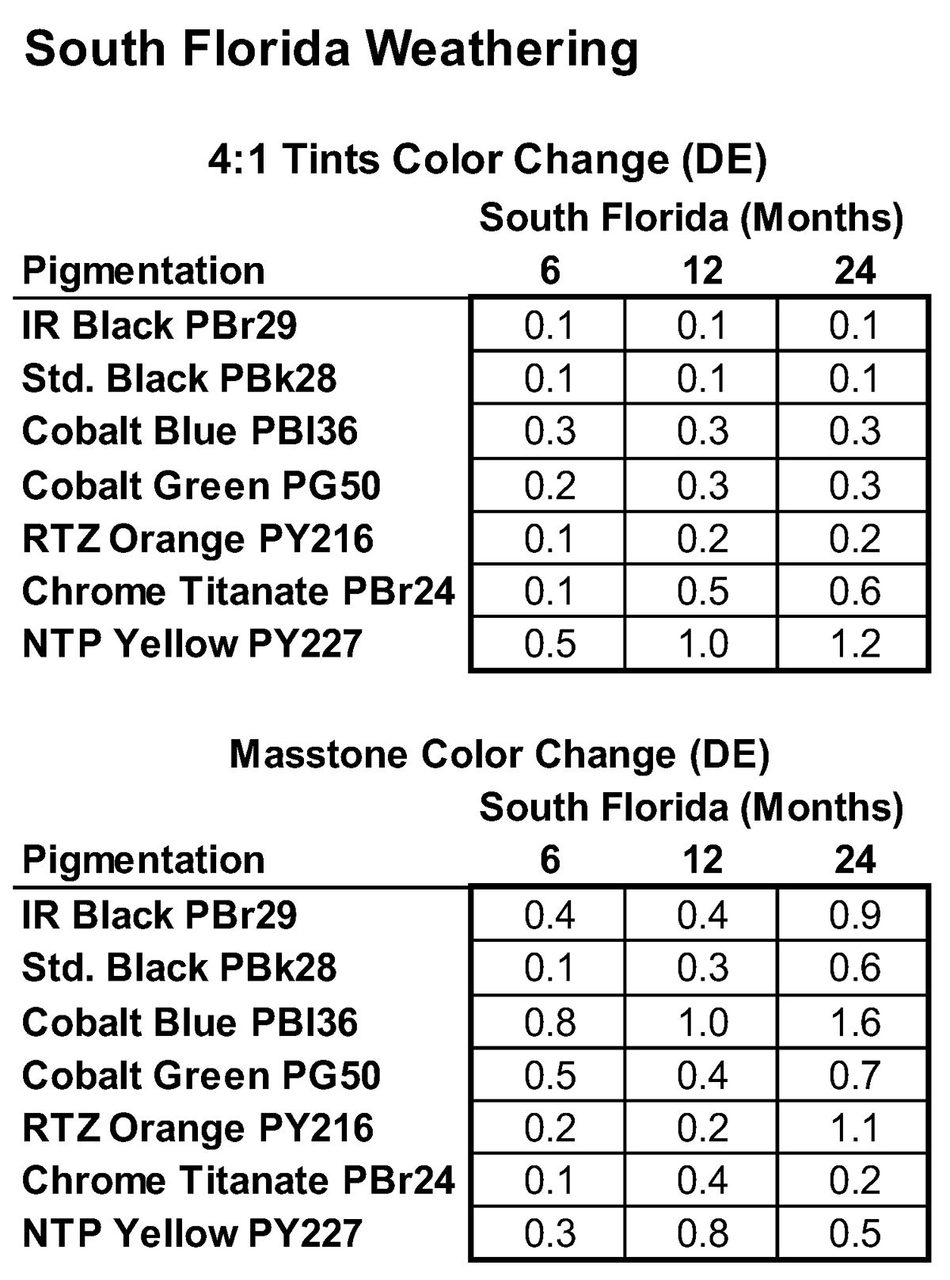
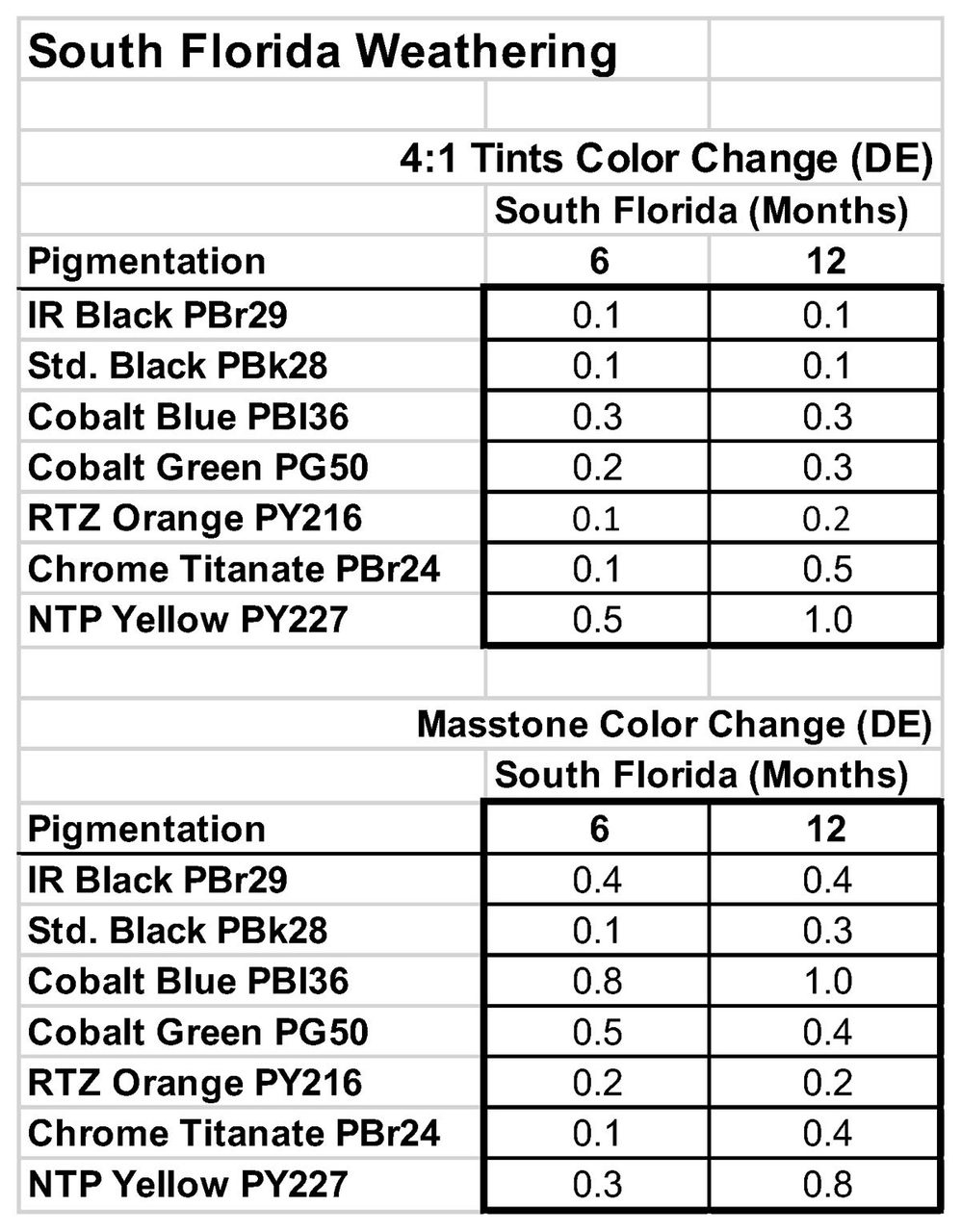
TABLE 5 ǀ South Florida weathering at 6 and 12 months.
A workhorse pigment in high-durability coatings is the Pigment Black 28 (PBk28) chemistry because of its weathering properties, controllable color, neutral blue-shade color and tinting properties. Many new formulations are based on IR reflective pigments, of which the IR black (PBk29) is the most impactful. By absorbing in the visible for dark color, but reflecting away the sun’s invisible IR wavelengths, building materials can remain cooler than if made with standard black pigmentation.
The cobalt-based blue and green pigments are used because the organic alternative phthalocyanine-based chemistries have been shown to change color over time, especially in tints. The Pigment Green 50 chemistry is also based on a composition without chromium(III) for applications that are looking for alternatives to Chromium Oxide (PG17).
While many powder coating chemists may be familiar with CI Pigment Brown 24 (PBr24) titanate yellow because of its heat stability for standard powder coatings, the pigment chemistry is also very useful in high-durability coatings because of its red-shade yellow tone and excellent weathering properties. Newer pigment chemistries to powder coatings are the NTP Yellow2 (PY227) and RTZ Orange (PY216). These two pigments together expand the range of durable colors available past standard inorganic pigments, into the range of organic pigments. Bright RAL colors such as RAL 1003 Safety Yellow can be matched with all inorganic pigments.
High-performance complex inorganic color pigments make excellent colorants for high-durability resin systems based in fluoropolymers. Continued studies in different weathering protocols will look at using accelerated weathering to better predict real-world performance.
Conclusion
CICPs have inherent inertness, color development properties and special attributes that make them perfect to add to the ‘tool-box’ of powder coating chemists and formulators. They provide predictable color and functional properties, and resist degradation when exposed to harsh environments. CICPs are the coloring answer to the most demanding powder coating applications.
These experiments show the benefits to using high-performance CICPs due to their color dispersion stability and controllability so that they provide powder coatings chemists and formulators a tool box of ‘problem-solving’ pigments.
References
1. Pigments used in study:
CI Pigment Violet 16 Manganese phosphate (PV16): Shepherd Color Violet 11T
CI Pigment Brown 29, IR Black PBr29: Shepherd Color Black 10G996
CI Pigment Black 28, Std. Black PBk28: Shepherd Color Black 430
CI Pigment Blue 36, Cobalt Blue PBl36: Shepherd Color Blue 211
CI Pigment Green 50, Cobalt Green PG50: Shepherd Color Green 10G655
CI Pigment Yellow 216, RTZ Orange PY216: Shepherd Color Orange 10P340
CI Pigment Brown 24, Chromium Antimony Titanate PBr24: Shepherd Color Yellow 10C229
NTP Yellow PY227: Shepherd Color Yellow 10P150
2. NTP Yellow Pigment technology is protected under the following patents: US Pat. RE45,382, Australian Pat. 2011 264994, Chinese Pat. 103097299, European Pat. 2580163, Japanese Pat. 5778264, South Korean Pat. 10180902.