Ready to proof -- Clare 03/8/22
KJ proofed on 3/14
Ready for author
Sent corrected version back for final approval - CLEAN
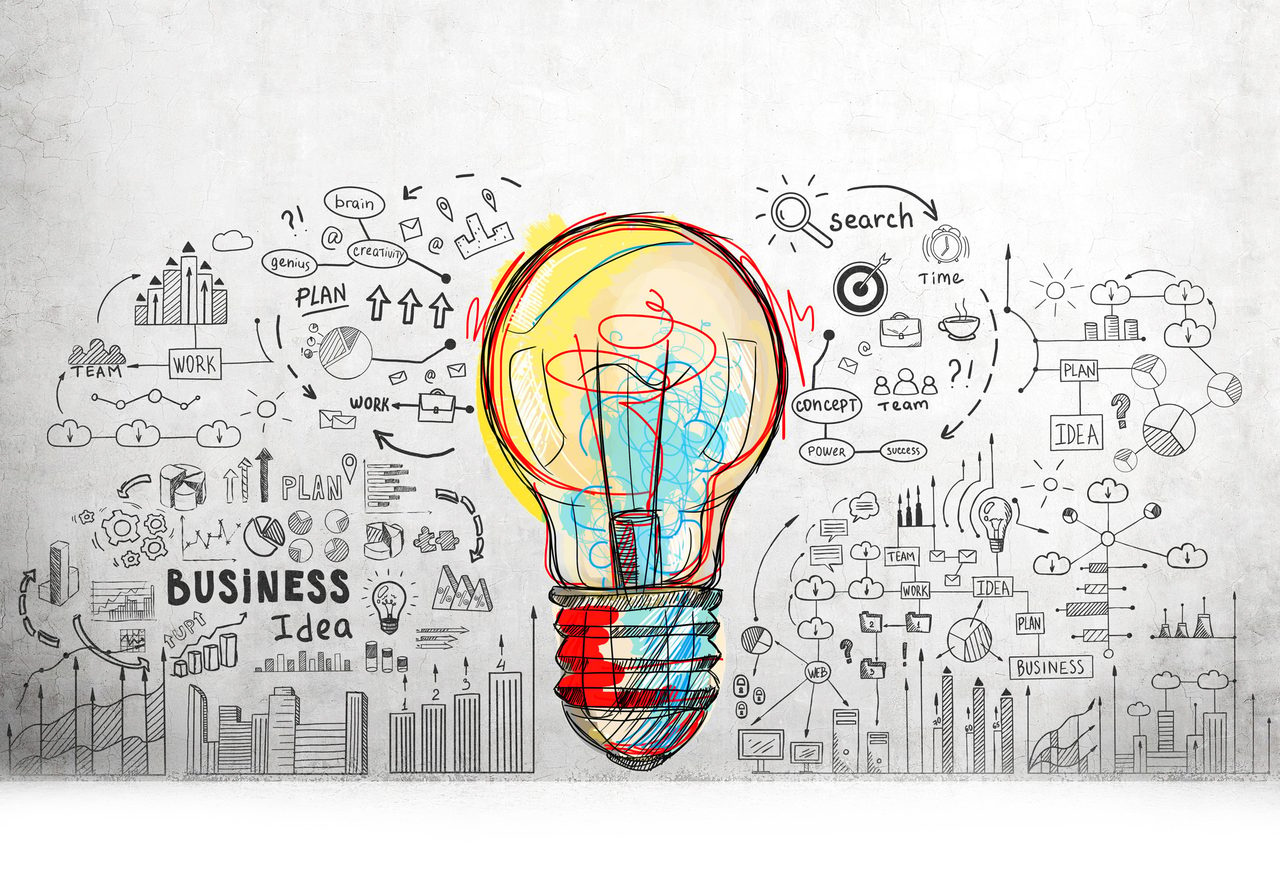
Photo: ismagilov, iStock/Getty Images Plus, via Getty Images
Five Key Insights to Help the Coatings Industry Plan for the Future
By Chris Fitzgerald, Global Vice President of Coatings, Adhesives, Sealants, Elastomers (CASE), Rubber and Plastic Additives; Univar Solutions
The coronavirus pandemic has been a complex, evolving experience that has created cascading effects on business, from demand shocks and labor shortages to raw material constraints and inflation. As the crises continue to unfold, suppliers and customers are still vulnerable to disruptions at all business levels, from tactical to operational to strategic.
Here are five insights on market drivers, pain points and opportunities moving ahead as businesses adapt in an increasingly uncertain world.
1. First Things First
Top of mind for this industry has been, and will be for some time, the volatility in the supply and pricing of a myriad of products. One key example is titanium dioxide (TiO2). Today’s market continues to experience a spike in the price and limited availability of this essential ingredient, brought on by logistical delays from China, which supplies more than 50% of the world’s demand for TiO2. At the same time, the market has seen increased demand for architectural paints and so many other end uses demanding brighter and whiter results. While the coatings market is the biggest user of titanium dioxide for pigments, the plastics industry is also driving demand. Plastics manufacturers like the mechanical strength and electrical properties of TiO2, and its ability to withstand harsh weather conditions and provide ultraviolet protection.
Although versatile, beneficial and crucial in many use cases, titanium dioxide poses many challenges for the coatings market. When assessing the future of the product in formulations, producers should know that alternative routes to achieving high-quality, bright white, opaque-based coatings exist. These should be considered not only due to supply and price concerns with TiO2, but also from a desire to remain flexible in formulations as regulatory changes could make TiO2 less desirable in some markets.
2. Prepare a “Plan B”
Titanium dioxide wasn't the only raw material in short supply last year. For much of 2021, almost 85% of all the specialty resins, rosins, monomers, silicones, surfactants, pigments and additives we sell were on some sort of sales control or allocation at some point in the supply chain. Several factors were at play, including production disruptions, surging demand and ongoing supply chain issues.
Raw material shortages have a domino effect. If suppliers don't know when ingredients will show up, they can't tell distributors or customers when their production will run or when the next truck will arrive at the dock. Consumers saw the impact firsthand at their local home improvement stores and dealt with depleted inventory in paint and many other categories.
How long the supply-and-demand imbalance will last is a matter of debate among policymakers and economists. It's challenging to figure out because the issue is magnified by logistical problems, such as the lack of shipping containers, the backlog at ports, and the truck driver shortage impacting the movement of materials into and out of ports and around the country.
As the world gets smaller, manufacturers must understand where their raw materials are made and stored, and if those production facilities have been approved to make multiple formulas in case another facility goes down. As such, we are beginning to see investment in new production facilities. For example, Dow recently announced plans to build a methylene diphenyl diisocyanate (MDI) facility in Freeport, Texas, that will expand production by 30% and add much-needed volume to the marketplace in 2023.
Product shortages have driven many in the paint and coatings industry to seek functional offsets and drop-in replacements, or “Plan B’s,” as I like to call them. In many cases, this results in formulation changes. Rarely do you see a specialty resin drop-in for another without some type of formulation changes.
But changing chemistries is a formidable task when resources, and research and development are stretched thin. More and more manufacturers are using independent labs to qualify or do the initial testing of new formulations. If an independent lab can prove an alternative formulation works, companies can save massive amounts of development time and move into production quicker. The key is having a playbook of options and knowing when to run which play.
3. Sustainability Matters
Despite the upheaval brought on by the pandemic, the industry still faces unrelenting pressure from two broad global trends: increasing regulation and the need to balance economic, environmental and social interests. The COVID-19 crisis has strengthened the resolve of many governments to organize a sustainable recovery from the pandemic.
Last year, for example, China expanded its air pollution curbs in Beijing and nearby provinces to more cities, according to media reports. Some experts said the country ratcheted up its blue skies initiative in the short term because it wanted to reduce smog for the Winter Olympics in February. But the government is also serious about increasing energy efficiency and becoming carbon neutral by 2060. The environmental policies have forced some chemical manufacturing plants to shut down, which has reduced the availability of key raw materials and specialty chemicals for the global market.
The industry is also bracing for tighter restrictions on air pollution in the United States, which could lead to regulatory changes related to volatile organic compounds (VOCs). VOC regulations are a complex, ever-changing landscape. In response, the coatings industry has had to reformulate or formulate new products that sometimes sacrificed performance. But today, customers expect coatings that are high-performing AND environmentally friendly.
As we evolve to waterborne replacements, raw material manufacturers have taken to the challenge and developed alternatives to several products typically found in solvent-based products. The low-VOC components provide performance benefits, such as corrosion and heat resistance, improved adhesion and scrub resistance. Suppliers are stepping up their innovation to help drive industry efforts to increase energy efficiency and enhance longevity, saving money and reducing waste. Products that offer UV reflectivity, allowing for cooler roofs and walls, or protecting coatings from UV damage, are prime examples.
Sustainability isn't as simple as just supplying customers with the right chemistry and products. It's also about reducing the carbon footprint of your supply chain, manufacturing operations and distribution network. It looks at the societal impacts of companies and their products. It considers profitability, or lack thereof. It's a holistic commitment to keep global communities healthy, fed, clean and safe.
4. Keep an Eye Out for Opportunities
Sustainability goals are creating new business opportunities worldwide. In Italy, for example, the government started providing generous financial incentives in 2020 to turn buildings green, from insulation to solar panels to replacing boilers and window fittings. The tax credits, known as a “superbonus,” are intended to cover 110% of the costs of energy efficiency and structural improvements. Reuters reports that the incentives increased Italy's gross domestic product and created 153,000 jobs last year. The program has been extended to 2022. How many companies were able to take advantage of this opportunity and grow their business?
The U.S. is counting on similar economic growth from the Infrastructure Investment and Jobs Act that became law in November 2021. This is a once-in-a-generation investment in our infrastructure. In addition to providing funds to rebuild roads and bridges, and upgrade airports and ports, the legislation prioritizes climate resilience and weatherization to deal with more frequent and severe droughts, floods and wildfires. Lighter and stronger has been a technology push for the automotive sector, but it also applies to construction projects. There are opportunities for a wide variety of businesses in everything from concrete coatings, sealers and membranes, to roof coatings and industrial bridge coatings. There is an additional need for modifiers for cement, mortar, grout, stucco and construction adhesives for these projects.
5. Be Prepared; Disruptions Will Happen Again
The pandemic has exposed several vulnerabilities in our global production and distribution networks. And while this industry has made progress in our recovery efforts, there's still a lot of fragility in our supply chains. It may take another three to nine months, for instance, to clear the backlog at ports, but I have yet to see a plan to increase the number of shipping containers in the U.S. That means operational resilience should remain a top priority, especially as severe weather has increased in the past decade. As we’ve all witnessed firsthand, events are multi-dimensional, and we need to take a holistic view of our analysis process as the events unfold. We will never have all the information required to make a perfect decision.
Even as supplies are expected to improve toward the second half of 2022, according to many sources, keeping adequate stock and having backup plans are some of the keys to protecting your business and your customers from future supply challenges.
At the end of the day, remember that you are not alone. Everyone today is facing the same challenges. It’s up to each of us to decide whether to be proactive and work on a new business plan with alternative formulations, to look for new opportunities, and to try to improve supply-chain processes with sustainability in mind — or hope things will improve and be reactive to the situation as it comes up again.