Ready to proof -- Clare 3/8/23
CB and KJ proofed on 3/9. Courtney, I added notes to answer your questions. No other changes from me.CLJ revised on 3/9
CB proofed - clean on my end please turn off notes
FORMULATING WITH MIKE
Alkyd Resins, Part One
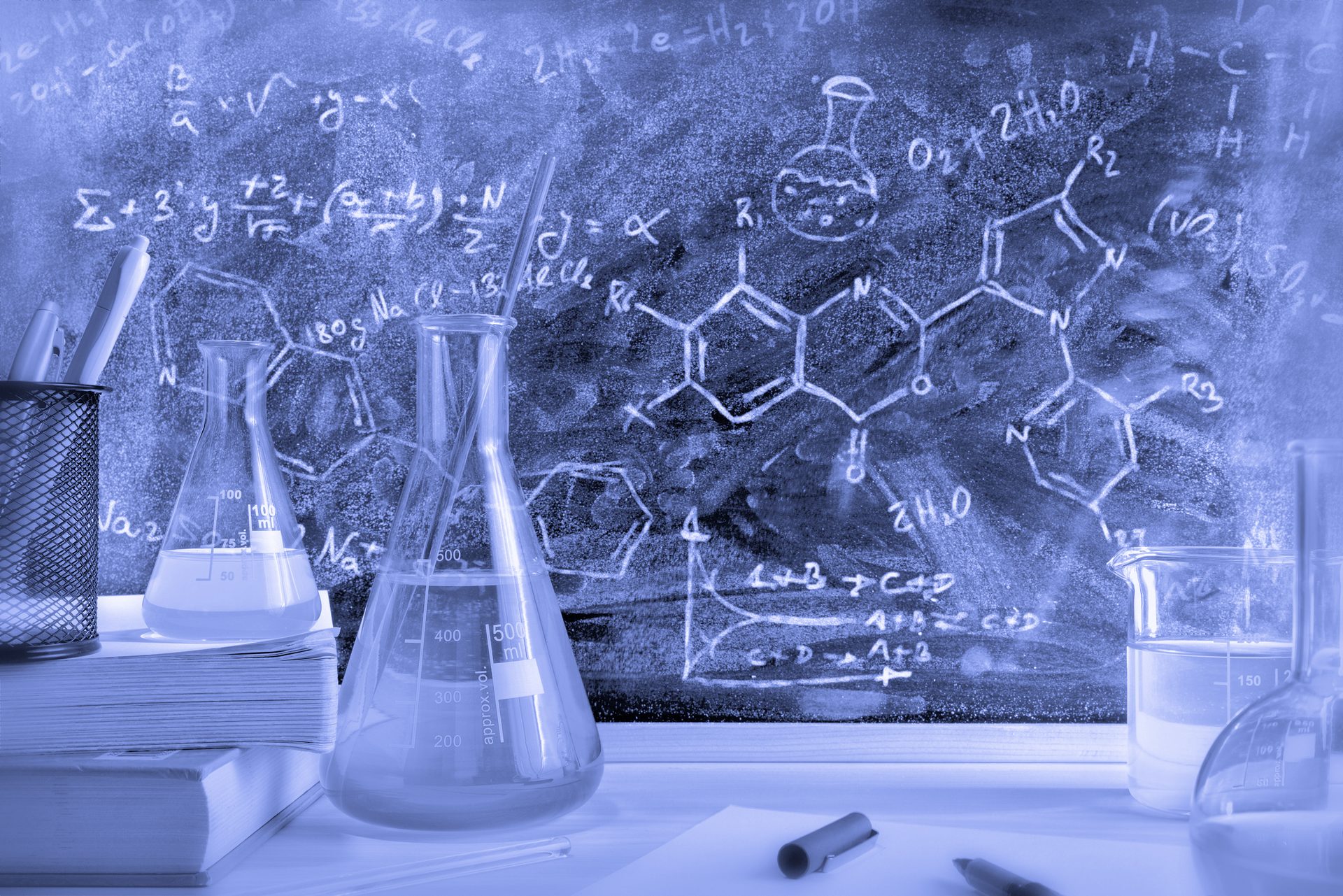
Davizro / iStock / Getty Images Plus, via Getty Images.
By Mike Praw, Technical Service and Development Manager – Coatings and Performance Products, Indorama Ventures: Integrated Oxides and Derivatives, The Woodlands, TX
In this month’s column, I will be discussing alkyd resins. I will start with a history of solvent-based alkyds and cover other topics in future columns. There is the old expression that history repeats itself, and alkyds are the perfect example. Drying oils such as linseed oil and tung oil have been used for centuries, and pigment / oil combinations were used in cave art thousands of years ago. The big breakthrough came when it was discovered that if you react an acid and alcohol, you get a polyester. In fact, the term alkyd comes from the combination of alcohol and acid to form alcid.
Traditionally, solvent-based alkyds were made from fatty alcohols reacted with an anhydride such as phthalic anhydride. The original polyester for alkyds was discovered by Watson Smith in 1901 and was the reaction of glycerol and phthalic anhydride to form a polyester (Figure 1).
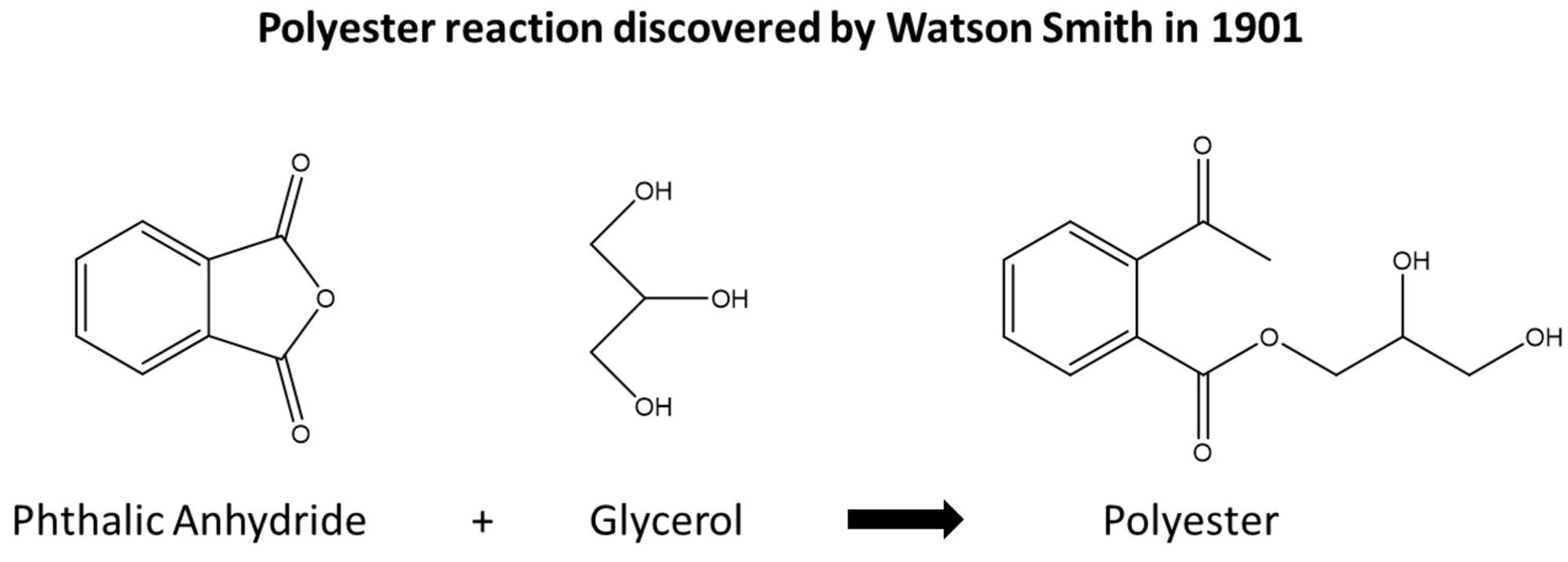
FIGURE 1 ǀ Watson Smith polyester reaction.
In 1920, Roy Kiente modified the polyester resin with the addition of natural oils, which improved the properties of the system and allowed it to air dry. Additional reactants have been added over time to greatly increase the capabilities and properties of this versatile resin. The low-molecular-alkyd natural oils would then crosslink through the oxidation of the unsaturated double bonds through the peroxide intermediate. The amount of oil in the oil / polyester system is known as oil length. Alkyds are referred to as short oil, medium oil, and long oil from this. Table 1 discusses oil length.
TABLE 1 ǀ Oil length.
The Watson Smith polyester reaction and the polymer’s final molecular weight and size is dependent on the ratio of reactants, reaction time and conditions, and other factors. If the molecular weight is too low, it will act more like a solvent or plasticizer than a polymer. If too high, it will be insoluble in solvents. The molecular weight, acid, and alcohol used will all influence solvency. Long-oil alkyds usually are soluble in mineral spirits, while short-oil alkyds normally will require a stronger solvent such as aromatics. Figure 2 shows the polymerization product of phthalic anhydride and glycerol.
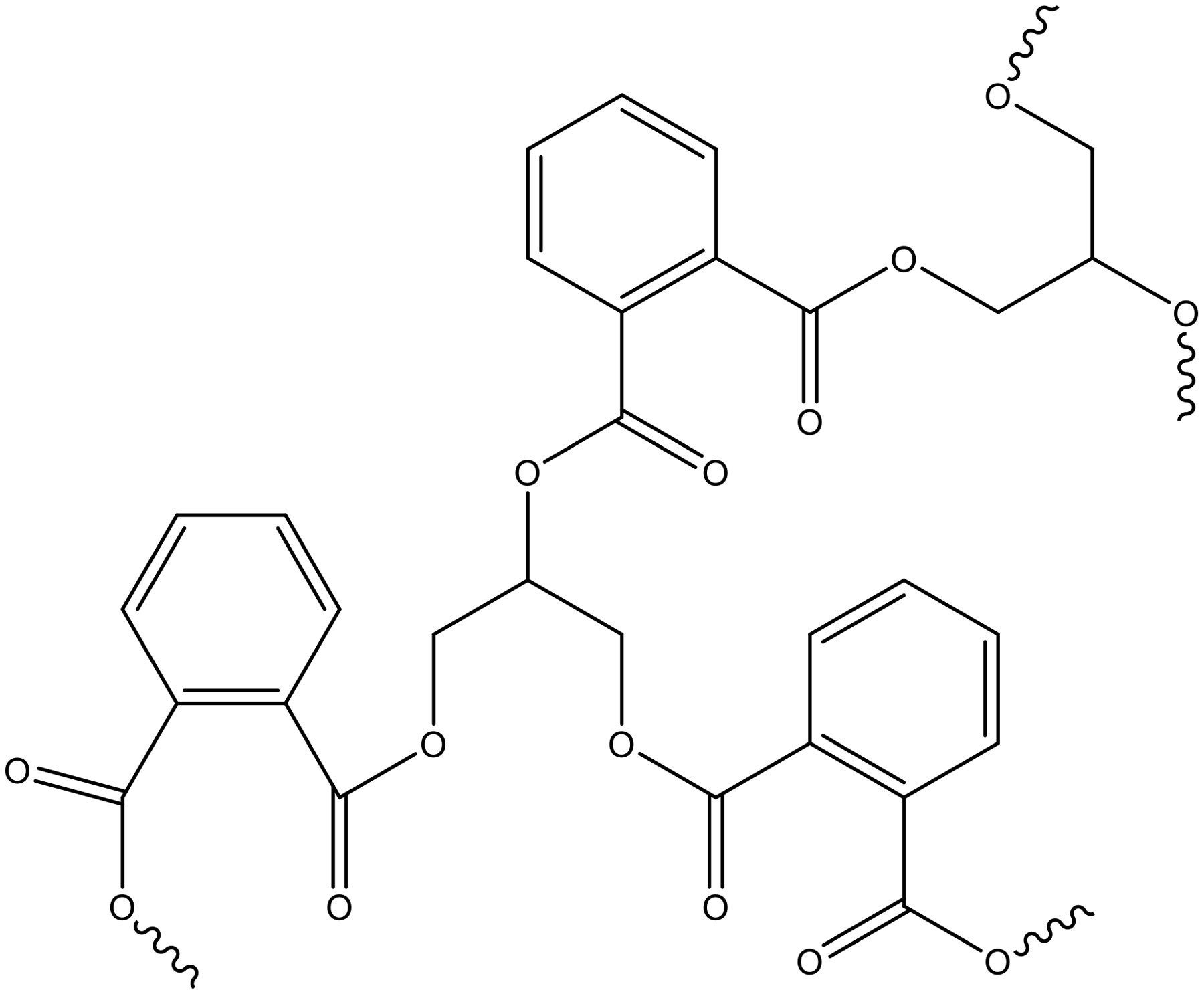
FIGURE 2 ǀ Watson Smith polyester polymerization structure.
It was soon discovered that metals could help catalyze the oxidative-cure reaction, speeding up the cure, and are often referred as driers. Originally, lead and mercury catalysts were used but environmental pressure had eliminated them, and other traditional replacements such as cobalt, manganese, and iron are under pressure to be replaced to eliminate heavy metals. For air-dry alkyds, you need a combination of driers, one to cure the surface and one for the through-cure of the film. Often a balance drier is added; this helps speed up both driers and ensures that cure at the surface and in the rest of the film is consistent, i.e. balanced. A traditional alkyd drier package included organometallic calcium, zirconium, and cobalt in the form of an octoate or hexanoate.
Balanced cure is critical. If the surface of the coating dries too quickly, solvent will get trapped, leading to surface issues such as wrinkling and solvent popping. Wrinkling happens when the surface crosslinks and afterwards the volume of the coating shrinks, leading to a micro-wrinkled surface that lowers gloss and reduces distinctness of image. It is most noticeable in high-gloss coatings or when coatings have too high a film build-up. In systems with a higher loading of pigments, shrinking is minimized due to the volume filled by pigments, and this becomes less of an issue. Solvent popping is when evaporating solvent creates tiny holes in the cured surface so it can leave the film. As the film cures it starts becoming rigid. If the force caused by the pressure of the solvent leaving the film exceeds the strength of the semi-solid surface layer, and the surface layer is too rigid to reflow, small pinholes or pops will appear in the film. Again, lower gloss and loss of distinctness of image results. If the surface cures too slowly it remains tacky, and contamination of the surface from dust and dirt results. Often a small amount of slower tail solvent is used to keep the surface open longer to prevent these issues.
During the cure of crosslinked systems like alkyds and urethanes, there is a recoat window. This is the period you can recoat the film without affecting the layers below the current coat. It is often expressed in two time frames, such as recoat in less than 8 hours or after 3 days. As the film crosslinks, the molecular weight increases. Even though the molecular weight is high enough that the film seems cured, until a certain minimum molecular weight is achieved (1 million to 5 million depending on the system and who you talk to), the film does not have resistance properties, especially chemical resistance. Top coating the system will cause solvent in the topcoat to swell the semi-cured base coat. This will lead to wrinkling and delamination from the substrate. Once the minimum molecular weight for the system is achieved, the base coat will have enough chemical resistance to the solvent in the topcoat to maintain its properties.
It was found that using non-drying oils and increasing the polyester content of the alkyd would allow it to be crosslinked with melamine formaldehyde resins using a strong acid catalyst (usually para-toluene sulfonic acid) and heat. This led to a whole range of baking coatings with significantly improved properties and performance. Oils used in alkyds are referred as drying, semi-drying, and non-drying. Drying and semi-drying can be used in air- / ambient-cured alkyd resins. Semi-drying and non-drying oils are used in baking systems. Table 2 lists some of the traditional oils used in air-dry and baking alkyds.
TABLE 2 ǀ Oil properties.
Look for the continuation of this topic in Part 2 of this article series, coming in the May issue.
All information contained herein is provided "as is" without any warranties, express or implied, and under no circumstances shall the author or Indorama be liable for any damages of any nature whatsoever resulting from the use or reliance upon such information. Nothing contained in this publication should be construed as a license under any intellectual property right of any entity, or as a suggestion, recommendation, or authorization to take any action that would infringe any patent. The term "Indorama" is used herein for convenience only, and refers to Indorama Ventures Oxides LLC, its direct and indirect affiliates, and their employees, officers, and directors.