Ready to proof -- Clare 3/7/23
CB proofed 3/7 - comments for clare on tables and figure 2 below.
CLJ revised on 3/7
KJ proofed on 3/9. I left notes for edits on four of the tables.
CLJ revised on 3/9
CB - clean on my end
High-Performance, Environmentally Compliant, Two-Component
Waterborne Urethane Dispersions
Photo: ChristinaKurtz, E+, via Getty Images
By Ximing Li, Alec Krienen, Gabor Erdodi and Miriam Peralta, Lubrizol Advanced Materials, Brecksville, Ohio
Environmentally compliant paints have come a long way since the 90s, and as the concept has grown in complexity, identifying sustainable paints and coatings is increasingly a challenge for the industry. Current sustainable labeling standards may not include complete life cycle analysis and/or result in compromise of performance. It is therefore important to design coatings where environmental impact is carefully analyzed, and its impact is contrasted with performance in a balanced way.
Some of the most important sustainability considerations for paints and coatings from the resin perspective include:
- Recycled and/or renewable content: use of plant-based raw materials, pyrolytic/reactive recycling, salvaged excess paints, and/or alternative paints.
- Reduction/elimination of toxics: e.g., formaldehyde, crosslinking additives like isocyanates and ADH, ammonia, odor masking agents, preservatives, and fungicides and volatile organic compounds (VOCs).
- Manufacturing methods: use of energy, resources in production, and effect on climate/environment.
- Durability: level of protection and service-life extension leads to a reduction in the footprint of the substrate (climate and environmental).
Over the years, Lubrizol has developed several technologies that address the most severe environmental issues. In this article, we demonstrate our innovative approach to create high-performance and environmentally compliant coating solutions with polyurethane dispersions (PUDs) for wood coating and protective coating applications.
Experimental
Synthesis of Waterborne Polyamide Polyurethanes
Three polyamide-based polyurethane dispersions were synthesized using the prepolymer method (described previously1-8). These three dispersions use three different types of amine neutralizer during synthesis: APT-2 used the most common neutralizer, Triethanolamine (TEA), while APT-1 and APT-3 used two new amine neutralizers for TEA-free requirement. Polymer properties are summarized in Table 1. All the polymers passed a stability test at 60 °C for six weeks, and bio content was verified externally, according to ASTM D6866-18 Method B. Resin viscosity has been measured under ambient temperature (~25 °C) using a Brookfield viscometer.
TABLE 1 ǀ Basic properties of the novel polyurethane dispersions.
Coating Preparation
Paints were prepared using the above listed experimental polymers in a standard clear formula (Table 2). All paints passed ambient temperature coalescence and low temperature coalescence at 4.4 °C.
Maple wood boards, with dimensions of 20 cm × 20 cm, were used for testing. A 5-cm-wide brush was used as applicator to draw the paint with the grain of the wood board. After applying the first coat on the board, it was allowed to dry for 2-3 hours at ambient conditions (21 °C, 45% relative humidity). New coating layers were applied after abrading and cleaning the previous coat to create a smooth surface for subsequent layers. The panels were cured at ambient temperature for a week before tests. The dry coatings were estimated to be 76 µm-thick for all the coatings. All paints passed 1-hour sandability.
TABLE 2 ǀ Coating formulation for the new urethane dispersions.
Test Methods
Taber Abrasion: According to ASTM D4060, CS-17-resilient Calibrase wheels were used to provide abrasion while rotating on tested sample for 1,000 cycles. The wheels were resurfaced, and weight loss was recorded per each 250 cycles.
Coefficient of Friction (COF): ASTM D2047-17 was followed to check the static coefficient of friction of painted maple board measured by James Machine coefficient of friction tester.
Konig Hardness: The prepared paints were applied on aluminum panels and cured at ambient temperature for a week. Following ASTM D4366, hardness was measured using a pendulum tester.
Gloss: ASTM Standard D 523 was followed to measure gloss by using a glossmeter.
Hot-Pan Water Resistance: A wet cheesecloth was placed on a painted wood surface and a 250-ml stainless-steel cup with boiling water was placed on top of the cheesecloth for 1 hour. The cheesecloth and cup were then removed and the area on which they were resting was given a rating from 0-5, with 5 being the best, corresponding to the level of whitening and printing that occurs.
Chemical Resistance: German DIN 68861-1:2011-01 standard was used, a spot test, with 16-hour exposure time in category 1A. Exposure time was shorter for chemicals that completely failed before 16 hours (category 1B or 1C).
Black Heel Mark: This scratch resistance test method was developed in the lab, as shown in Figure 1. An ice hockey puck, made of solid vulcanized rubber, was used to simulate black heel. In the test a coating sample board was placed on the floor at a 15° angle below the scuff tester, which was oriented horizontally then allowed to drop and hit the sample. The mark left behind was rated from 0 to 10, the higher score the better performance the coating provides.
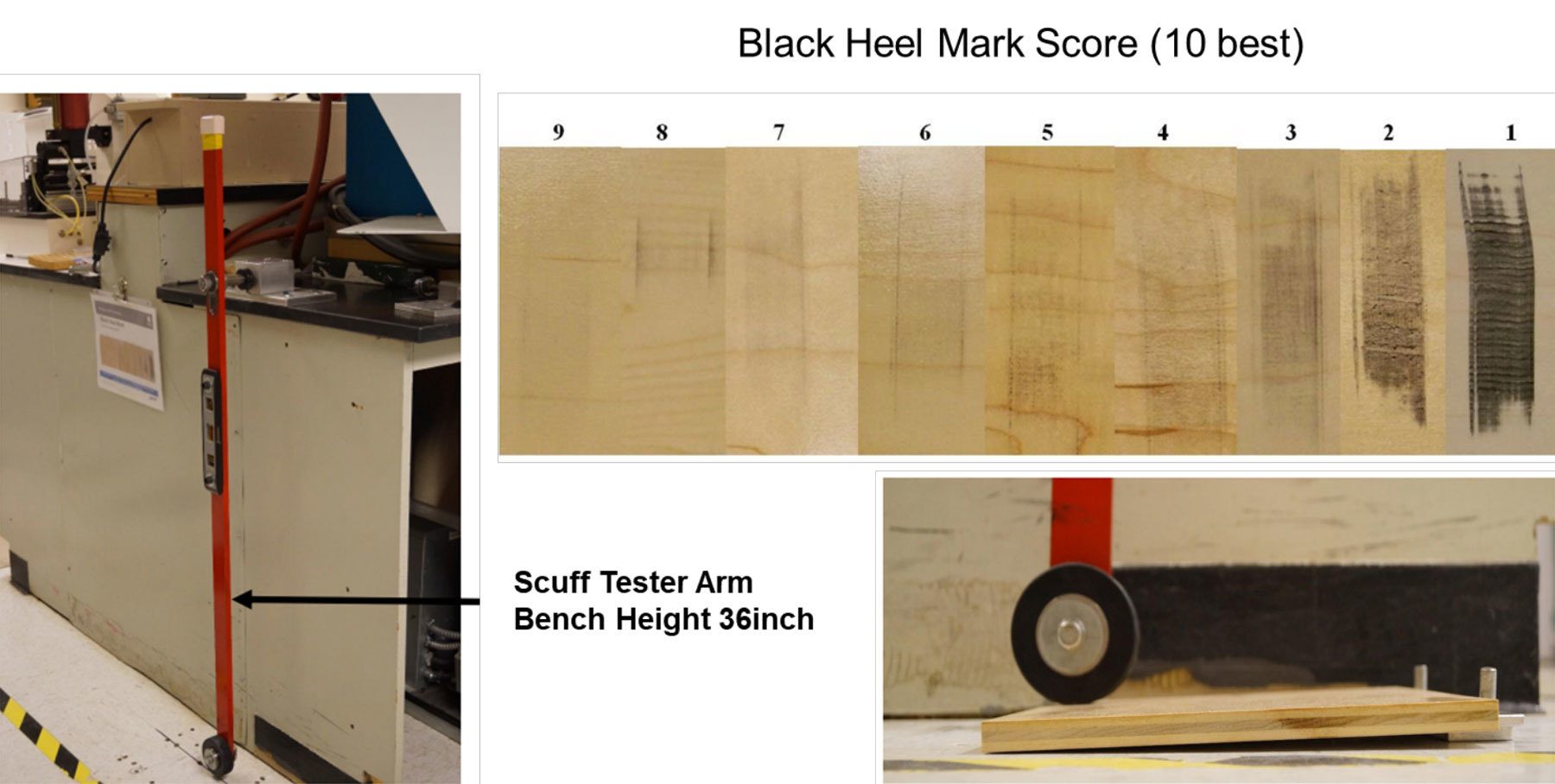
FIGURE 1 ǀ Black heel mark test.
Weatherability: Xenon Arc Weather-Ometer® and QUV weathering testers were used by following ASTM D6659 to determine the effects of long-term weathering on the gloss.
For all the tests described above, duplicates or triplets were run to verify the repeatability.
Results and Discussion
The Sustainability Profile of the Novel Polyamide Polyurethane Dispersions
Sustainability, carbon neutrality, and environmental friendliness are increasingly important concepts for paints and coatings, both on the individual level and for companies as well. Resins and the polymers play one of the most important roles in determining how these concepts apply for coatings, and in the next section we will demonstrate this analysis through the introduction of three novel waterborne polyurethane compositions that Lubrizol recently developed for sustainable coating solutions.
All experimental polyamide PUDs have been tested along with three commercial products, which are good representations for demanding interior and exterior wood coating applications. The abbreviation APT stands for Aptalon™ polyamide polyurethane technology developed in our group. The sustainability profile of the tested systems is summarized in Table 3. The benchmarks include two isocyanate crosslinked waterborne PUDs and one self-crosslinking waterborne PUD using ADH; the former with a high (>200 g/L US) recommended VOC and the latter with somewhat lower VOC. The selected benchmarks have typical solid levels (32% to 41%) and suggest applying three coats or two coats over a sealer.
TABLE 3 ǀ Properties comparison of tested systems.
*Maximum resin solid content calculated from formula.
**Three coat or two coats over a sealer.
In the following section, the sustainability profile of the polyamide-based PUDs will be examined and compared to industry practices, standards, and the selected benchmarks.
Renewable Content in Polyamide-Based Polyurethanes
Aptalon polyamide polyurethane technology has been developed by Lubrizol1-8, 12-14 to meet the demanding coating challenges. Polyamides, in general, provide an outstanding balance of mechanical performances, chemical resistance, and thermal stability, and due to the importance of durability in sustainable protective coating applications, polyamide was chosen as the main polyol in the discussed experimental compositions. One other benefit of using polyamide soft segment, however, is not performance related. Due to the unique monomers necessary to achieve low glass transition temperature (Tg), most polyamide polyols developed by Lubrizol have greater than 80% renewable carbon content, which, as Table 1 shows, can raise the overall renewable carbon content of the experimental PUDs substantially. The source of renewable carbon in the monomers is plant-based that cannot be used as food source.
Reduction/Elimination of Toxic Components: VOCs
Resins and binders in paints and coatings may contain a wide variety health or environmental hazards, but in protective coatings, where performance is key and high hardness and crosslinking are essential, the most relevant is probably volatile organic compounds (VOCs).
Most high-performance urethane coatings require VOCs for film formation. These VOCs can cause minor problems such as headaches and nausea, but they can also cause major health issues such as allergic reactions and damage to major organs. In polyurethane dispersions (PUDs), the VOC need of a coating is often proportional to the hard segment of the urethane and the performance of the coating.
Table 3 shows the VOC levels in the three novel PUD formulations, which compare favorably to most modern high-performance protective coatings, which often reach close to 288 g/L U.S. levels. In most situations, decrease in VOCs will lead to loss in performance. Lubrizol developed several technologies that can prevent paying the performance penalty at lower VOCs, one such advance was the development of non-uniform PUDs.9
We recently launched a PUD with a solid content ≥45% coupled with low viscosity (<250 cP), a unique combination, that among other benefits also had lower VOC requirement when formulated to the higher formulated solids.10 The VOC improvement is related to faster drying times, which prevent the evaporative loss of coalescing solvent during the drying phase so only the amount that is required for film formation is needed to be added to the formula. Table 3 shows that the three experimental resins have high solid content as well, which does contribute to lower VOC need.
Reduction/Elimination of Toxic Components: TEA
A common hazardous air pollutant in anionic waterborne polyurethanes is the neutralizing agent. TEA became the main source of neutralization due to its high pKa, its inertness, and optimal volatility but its eye-irritation and its effect on the respiratory system is a serious health concern. TEA is considered a VOC and has an unpleasant, potent odor. Hence, there has been much research on developing TEA alternatives. In this work, we explored two other amine neutralizers and studied their effect in a high-performance protective coating formulation.
TABLE 4 ǀ Physical parameters of the amine neutralizers used in the experimental compositions.
*Calculated value
Reduction/Elimination of Toxic Components: Crosslinkers
Crosslinking typically involves low-molecular-weight, highly reactive chemicals that can be a concern for the health of the coating professionals and the end user alike. They may not necessarily represent a large fraction in a formulation, but they often significantly increase the hazard level of coatings due to their participation in an ongoing chemical reaction at the time of the application and in the proximity of the individual applying the coating. However, isocyanates, aziridines, and hydrazides are common crosslinkers due to their efficiency in covalently connecting functional groups in coating compositions.
Carbodiimides have a better sustainability profile than the above-mentioned crosslinkers, having low toxicity, long pot life, requiring no catalyst, but their use is limited because of performance issues, likely due to slow reactivity. We addressed this reactivity issue by improving the reactivity of the functional groups on the resin so they work more efficiently with environmentally friendly polymeric carbodiimide crosslinkers.9-11 Several formulations were explored, and we found that the dispersion-type crosslinker E-07S provided the best performance and stability, and the study was performed using this additive. (The formula optimized is shown in Table 2, which is used for performance comparison with commercial products.)
Manufacturing Methods: Use of Resources, Energy, and Waste in Production/Application
Solid levels of waterborne resins have been steadily increasing over time due to the various benefits including lower shipping cost, higher film build per application, and lower VOCs, however, attaining high solid level in waterborne PUDs has been troublesome for protective coatings due to the high innate polydispersity in urethane dispersions. We recently introduced a 1K PUD with a solid content ≥45 wt% that solved these issues and can form hard crosslinked films without adding (2K) a crosslinker in high-solid formulations and we used the same technology to increase the solid level of the experimental coatings to be 45 wt% (Table 2). The high solid content offers broad benefits in energy efficiency from faster dry times to less layers of coatings and lower shipping cost/energy.
Performance Comparison
The experimental polyamide PUDs have been tested along with the three commercial products to evaluate their performance in highly demanding wood coating applications. The benchmarking was set up in three categories: mechanical/physical protective features, chemical resistance, and weatherability.
The physical protective features of the coatings were explored with abrasion resistance, hardness, black heel mark resistance, and thermal resistance. Table 5 shows the specific tests used and the results. The polyamide-based polyurethanes (APT-1 and APT-2) neutralized with amine A and TEA had high gloss on maple wood, which was like the isocyanate crosslinking benchmarks. The other amine B neutralized sample (APT-2) had lower gloss.
All three polyamide PUD-containing paints and the benchmarks had similar hardness and coefficient of friction by design to comply with industry requirements for high-performance wood coating applications. The fact that the hardness in the samples is nearly identical makes the interpretation of the Taber abrasion resistances more straightforward: the better it is, the better the overall “toughness” of the resin. The experimental polyamide-based PUDs provided good abrasion resistance, better than the benchmarks. Black heel mark (BHM), which is an internally developed aggressive scuffing test, showed similar ranking, but interestingly, the TEA neutralized version fell behind the polyamide-urethane APT-1. When the BHM grade was read after cleaning with 70% IPA, the damage was reduced, but this did not change the ranking of the resins significantly.
Overall, performance of the Aptalon technology was superior to ADH or isocyanate crosslinked benchmarks in three-coat systems as the TEA alternatives can offer an array of evaporative rates and can be tailored in performance.
TABLE 5 ǀ Mechanical properties, thermal resistance, and gloss of polyamide-based polyurethane coatings and benchmarks.
Table 6 shows the chemical resistances of the tested systems using the German DIN 68861 chemical test standard in spot testing. The test was done with 24 chemicals in total but the chemicals that got maximum score are not listed in Table 5 for simplicity (see experimental for details on the rest of the chemicals in the test). The three new polyamide-based paints provided better chemical resistance than the benchmarks, especially for 48% ethanol, red wine, acetone, and 2-ethylbutyl acetate. And APT-1 gives the best overall chemical resistance.
TABLE 6 ǀ Chemical resistance test summary. For all chemicals: 0 is worst and 5 is best.
*Tested for 2 minutes
**Tested for 10 seconds
It has been indicated that polyamide polyurethane dispersion APT-1 shows better performances than the other polymers. It is possible because that the favorable azeotropic properties of this amine lead to improved film formation and/or faster drying and thus to better performance.
Accelerated weathering testing results are shown in Table 7 only for the best performing benchmark and polyamide polyurethane: Benchmark-3 and APT-1. During the relatively short exposure times of the weatherometer, both coatings maintained high gloss after 500 hours exposure, but the benchmark showed significant gloss loss in the QUV after 750 hours, which indicates better durability for the experimental polyamide-based PUD.
TABLE 7 ǀ Gloss retention during weathering test.
It should be emphasized that all three benchmarks were applied in three coats and all three new polymers were applied in two coats. Due to the higher solid content, the actual coating weights and thicknesses are similar, and the polyamide polyurethanes outperformed the benchmarks with reduced application steps, making these novel PUDs even more remarkable.
Conclusions
Novel high-solid, TEA-free waterborne polyamide-based polyurethane dispersions with high bio-based content were developed for low-VOC 2K isocyanate-free wood coating and protective coating applications. Figure 2 shows that the novel resins had high performance and meet multiple sustainability requirements/conditions.
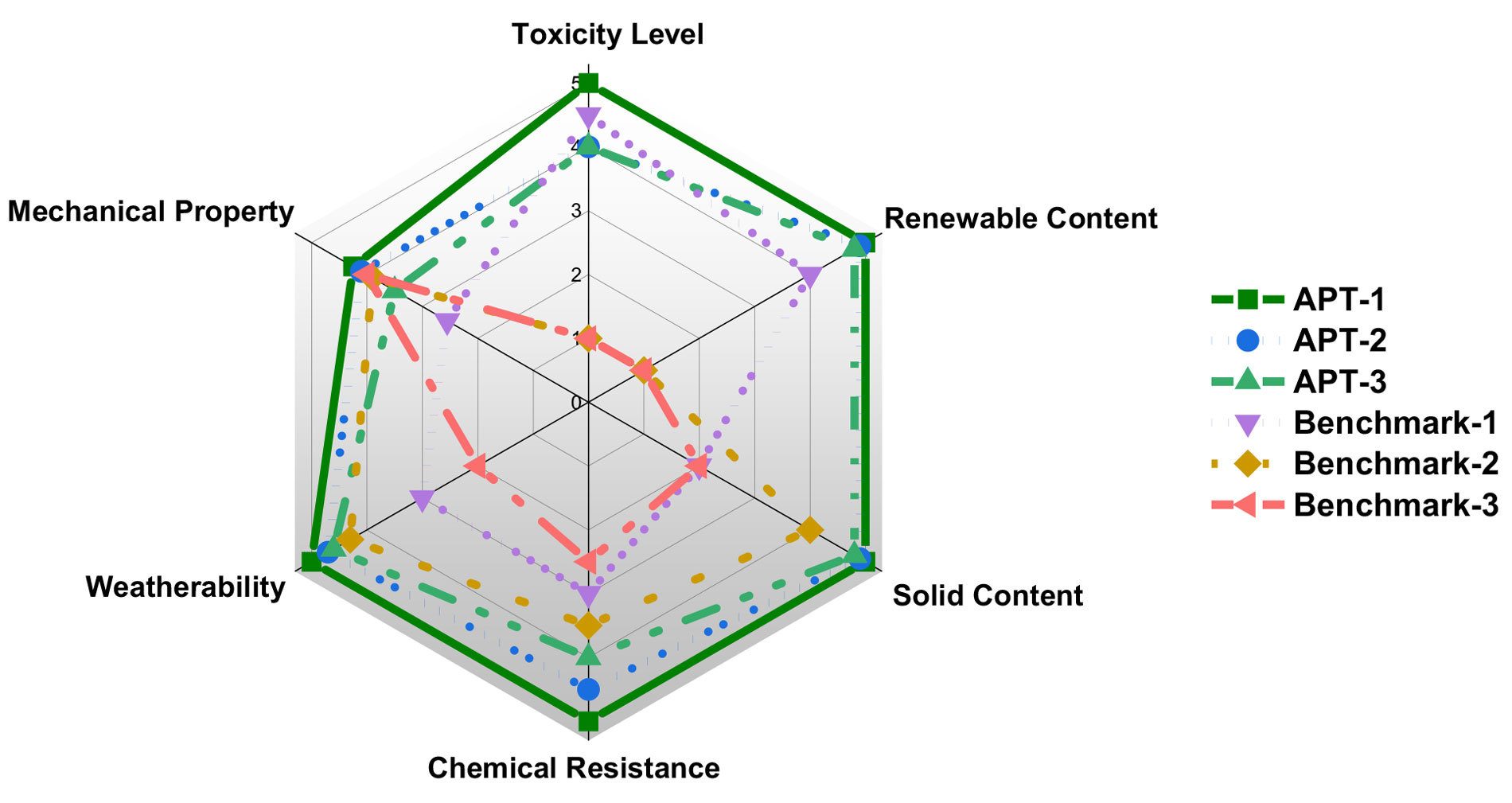
FIGURE 2 ǀ Balance of properties in high-performance PUDs for sustainable coating solutions.
This paper was presented at the 2023 Waterborne Symposium in New Orleans, LA.
References
1 Erdodi, G.; Pourahmady, N.; Ta-Yuan Lai, J. WO 2014126739, 2014.
2 Erdodi, G.; Pourahmady, N.; Ta-Yuan Lai; J.; A.D. Pajerski, A.D. WO 2014126741, 2014.
3 Pourahmady, N.; Makal, U.G.; Erdodi, G.; Ta-Yuan Lai, J. US Patent 9809675, 2014.
4 Erdodi, G.; Ta-Yuan Lai, J.; Pourahmady, N.; Skoff, I. WO 2016099726, 2016.
5 Erdodi, G.; Pourahmady, N.; Bird, J.; Skoff, I.; Swech, C. EP 3615590, 2016.
6 Erdodi, G.; Nagvekar, D.S.; Schroeder, K.; Pourahmady, N.; Pan, Y.L. WO 2016025319, 2016.
7 Erdodi, G.; Pourahmady, N.; Bird, J.; Skoff, I.; Swech, C. WO 2018201143, 2018.
8 Pajerski, A.D.; Erdodi, G.; Pourahmady, N. WO 2016100201, 2016.
9 Lubnin, D.; Malaba, V.; Stanislawczyk;Calhoun, G.D. US Patent 20050004306, 2005.
11 Tillet, G. Progress in Polymer Sci, 2011, 36, 191.
12 Musche, N.; Erdodi, G.; Bird, J.; Skoff, I.; Pourahmady, N.; Gibson, R. European Coatings Journal, 2017, (7-8), 24-28.
13 Pourahmady, N.; Erdodi, G.; Gibson, R.; Musche, N.; Bird, J.; Skoff, I. Farbe und Lack, 2017, 123(8), 42-47.
14 Erdodi, G.; Halstead, J.; X. Li, X. Farbe und Lack, 2019, 125(4), 22-27.