Ready to proof -- CLJ 07/15/21
KJ sent corrections on 7/15
CLJ revised on 7/15
Ready for author
A Single-Coat System
for the Most Highly
Corrosive Environments
Photo: Delpixart, iStock / Getty Images Plus, via Getty Images
By Earl Ramlow, Product Manager Protective Coatings, Polyset, Mechanicville, NY
Since the 1980s, there has been a coating technology used on all causeway systems for the U.S. Army and Navy, as well as offshore oil platforms, hydro generation facilities, wastewater treatment facilities, bridges, oil refineries, and many other highly corrosive environments. The most notable structure where this technology is used is the main steel frame that supports the Statue of Liberty at Ellis Island in New York harbor.
The technology is a 100%-waterborne, high-ratio zinc silicate known as WB HRZS®. When used as a single-coat system – or when complemented with a topcoat for aesthetics – the product delivers superior and complete corrosion-prevention benefits that are unmatched when compared to other “IOZ” systems used in the marine environment. This coating system offers complete galvanic and cathodic corrosion protection with a total thickness of 6-8 mil DFT, reducing total material and labor costs, resulting in lower total cost of ownership for the structure’s lifecycle.
The Chemistry Behind the Coating
Let’s examine the chemistry of WB HRZS to understand how it works. The coating consists of two components: Component A (liquid silicate binder) and Component B (pure zinc powder). The key to this technology is the liquid silicate binder. Silicate is liquid glass or liquid ceramic. Glass or ceramic is a hard, permanent substance, not a liquid, right? Not always. Silicate, by definition, is silica reacted with an alkaline metal and water in a high-pressure, high-temperature dissolver. Silicate is always identified by the alkaline metal that was used to formulate it and render it soluble. Those alkaline metals are lithium, sodium or potassium. For this technology we will discuss potassium silicate (inorganic). For it to remain in a liquid state, it must maintain a mole ratio of no greater than 3.2:1 – that is 3.2 moles SiO2 (silicate) to 1 mole K (potassium). However, WB HRZS has a mole ratio of 5.3:1 and remains not only in a liquid state but it is very stable. This high ratio is a key differentiator of WB HRZS from all other “IOZ” technologies.
The Reactions
Let’s take that liquid glass and formulate a coating for steel. We mix the two components: potassium silicate and pure zinc powder. As a liquid coating, it must revert to a solid ceramic film, and for that to happen a curing process must occur. The curing process will occur in three very discreet process reactions.
Reaction One: Chemical Bond — Iron Silicate
When applied to materials like carbon steel and aluminum, the silicate bonds to the exposed substrate surface to form iron silicate (FE-SiO3) at the surface (Figure 1). For this chemical bond to occur, all surface contaminants (solvents, oils, grease) must be removed. If there is hydrocarbon contamination on the steel surface, it will interfere with the chemical bond. Additionally, there must be a minimum of a 1.0-mil surface profile for the WB HRZS to first make a mechanical bond before the chemical bond reaction takes place.
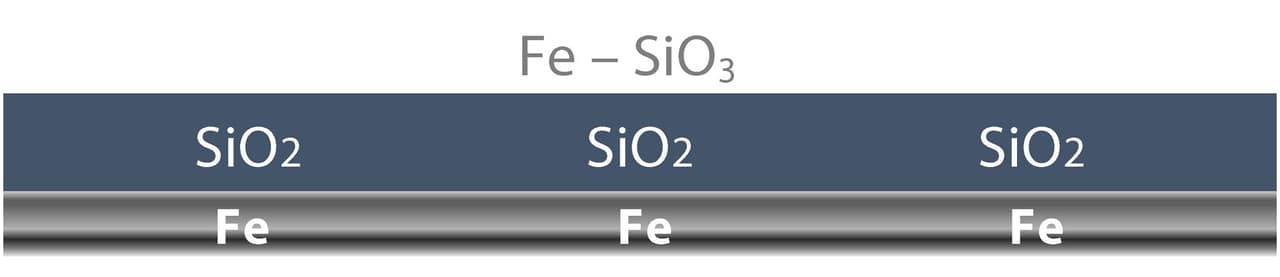
FIGURE 1 ǀ The silicate bonds to the exposed substrate to form iron silicate (Fe-SiO3).
Reaction Two: Galvanic Reactive Zinc
Once the coating is applied, it will start to cure very quickly due to the curing process of the evaporation of the water out of the coating. This generally occurs within minutes, rendering the coating initially cured (Figure 2). In 60 minutes, the cured coating is water immersible, and within two hours it could be top coated (if color is needed). At this reaction stage, it is very similar to HDG and thermally sprayed technologies. However, this is where the similarities end.
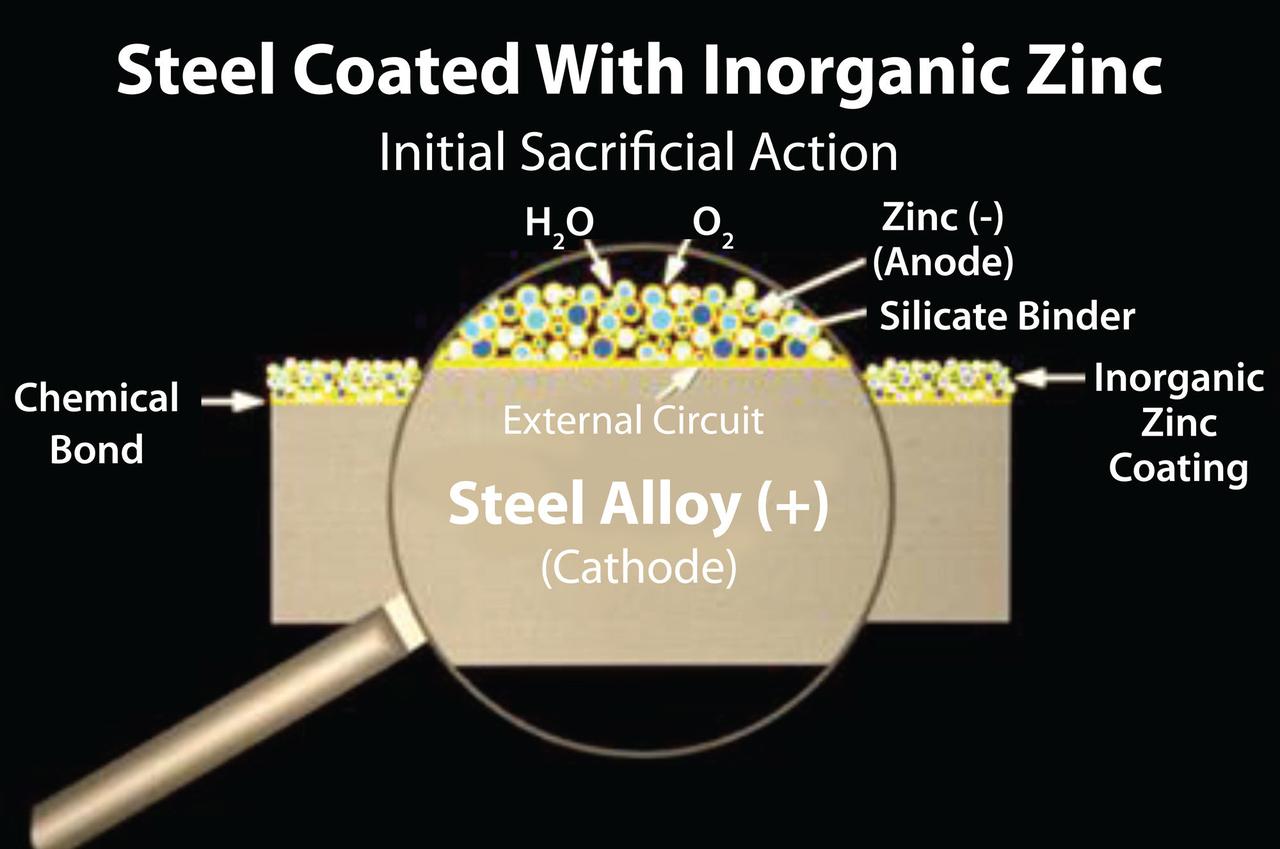
FIGURE 2 ǀ Initial sacrificial action.
Reaction Three: Barrier Seals Cured Film, Creating a Hard, Impermeable, Inert Film
The third reaction is what sets WB HRZS apart from all other “IOZ” coatings. As stated above, there is a brief sacrificial reaction. But, as this occurs over time, the zinc-reactive products continue to react, compounding and filling in the pores of the coating, ultimately creating zinc oxide and other compounding elements. As this happens, the coating becomes denser and much harder, eventually sealing itself off with a virtual glass or ceramic barrier, protecting the substrate and the coating itself (Figure 3).
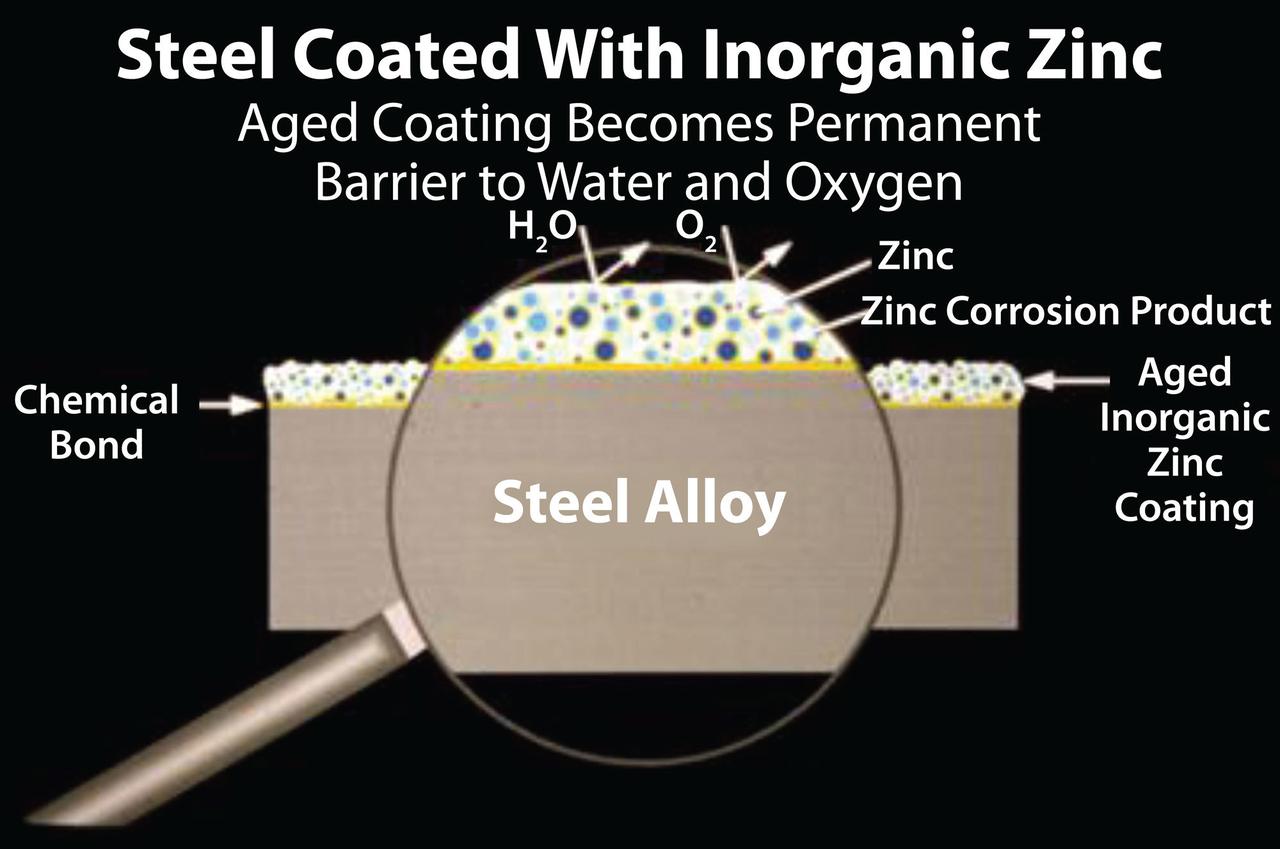
FIGURE 3 ǀ Aged coating becomes permanent barrier to water and oxygen.
What we have found is that after years or decades of exposure in basically any natural atmospheric environment, the dry film thickness (DFT) is normally the same as the original DFT applied.
Unique Features
When the formation of the outer ceramic film is created, the coating remains flexible due to the chemistry and reactive formation of the product itself, which is unique. It is also unlike thermally sprayed materials (TSM) and HDG, which are an expensive and not so environmentally friendly thermal application processes. Since these are molten applications that render the final product rigid and mechanically bonded to the substrate, any stresses or strains on the substrate will cause the TSM and HDG to crack. This cracking can occur as well with any thermal expansion or contraction due to dissimilar expansion and contraction rates of the dissimilar materials. Due to the complete chemical and technological features of WB HRZS, it will bend and expand/contract at the same rate as the parent substrate materials (Figure 4).
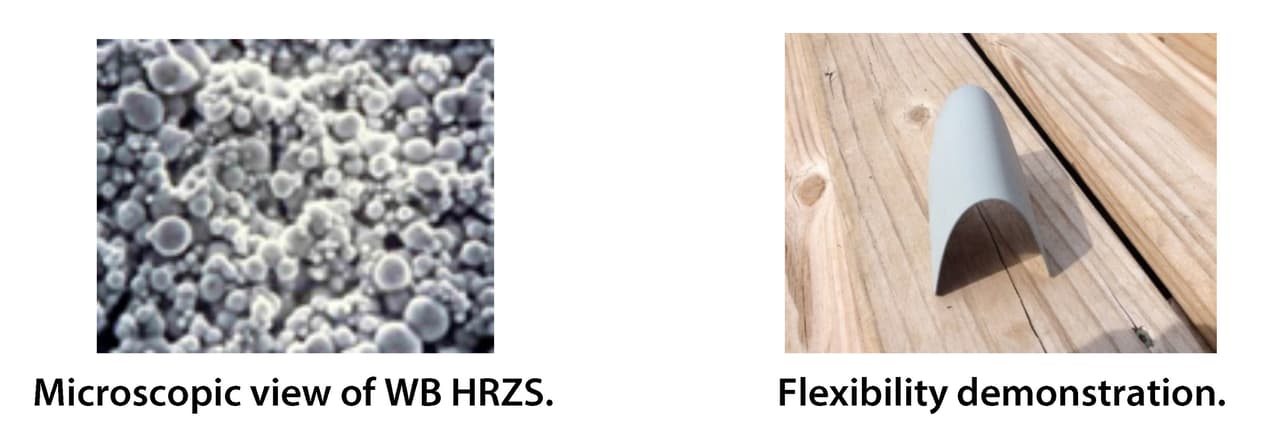
FIGURE 4 ǀ A microscopic view and flexibility demonstration of WB HRZS.
It is generally understood that this coating provides a true covalent chemical bond, which only a 100%-waterborne technology can provide. The curing and bonding process is why the technology can very quickly develop pull tests well beyond 1,000 lbs. and provide additional superior performance characteristics, unchallenged by most other technologies. Under normal drying conditions, manufactured products can be handled, stacked or assembled in a matter of minutes for rapid material processing during manufacturing. The coating provides full cathodic and galvanic corrosion protection, is self-healing when damaged, is weldable, flexible, and is easily applied and repaired in the shop or field. As a single-coat system in immersion, WB HRZS has demonstrated hard fouling resistance properties.
Conclusion
In conclusion, the benefits of WB HRZS are many, some of which include:
Excellent adhesion to steel, dual bonding (mechanical + chemical bond);
Cathodic and galvanic corrosion protection;
High temperature resistance (750 °F/400 °C);
Excellent abrasion resistance;
Self-curing (dry in 30 min);
Weldable;
Flexible;
UV resistant;
Very good hard fouling resistance;
No solvent needed for cleanup, just water.
The coating is also environmentally friendly, offering:
Zero toxic waste/non-hazardous;
Reduced application operations;
Reduced maintenance costs;
Reduced power consumption;
Reduced total cost of ownership;
Recyclable.
For more information, visit www.polyset.com.