Ready to proof — CLJ 7/26/22
KJ proofed on 7/27
COMPANY NEWS
PPG Helps Ford of South Africa Upgrade Manufacturing Operations
The Ford Motor Co. of South Africa invested more than $1 billion to upgrade its manufacturing operations at the Silverton Assembly Plant, reportedly the largest investment in Ford’s 97-year history in South Africa and one of the largest ever in the country’s automotive industry. New technologies and equipment were installed at the plant, including utilizing PPG’s Coatings Services division to operate and maintain the electrocoat lines that are instrumental in the company’s plans to expand on-site production of the new Ranger pick-up truck.
The upgrades to the facility will increase the annual production capacity of Ford Rangers from 168,000 to 200,000, a step needed to meet both domestic demand and export needs in over 100 global markets. “This investment will further modernize our South African operations, helping them play an even more important role in the turnaround and growth of our global automotive operations,” said Dianne Craig, president, Ford’s International Markets Group. “Ranger is one of our highest volume, most successful global vehicles. This investment will equip our team with the tools and facilities to deliver the best Ford Ranger ever, in higher numbers and with superior quality.”
With the increase in the plant’s production capacity, it is critical for Ford to maximize efficiency to keep pace, and that includes upgrading its coatings operations. According to Rodolfo Ramirez, PPG’s global general manager, Coatings Services, PPG has three ways to serve customers: coat a wide range of parts in PPG Regional Coating Centers located around the world; operate a customer’s in-house coating line; and provide engineering solutions, including equipment design and installation. PPG also works with external partners on incorporating key components, such as ovens, tanks, and application equipment.
At the Ford Motor Co.’s plant in South Africa, PPG runs and manages an INSITE™ coatings system specifically designed for Ford that unites all the benefits of a dedicated in-house coatings system without challenges associated with managing one. “We can design, engineer and integrate a plan for a customer,” said Ramirez. “Then deliver it as a turnkey solution, or operate it for them, as is the case with Ford Motor Company of South Africa.”
For the coatings themselves, Ford uses low temperatures due to the introduction of PPG POWERCRON 6200HE technology, which cures at 15-20 °C lower metal temperatures than the previous fourth- and fifth-generation electrocoat products, while also helping to reduce VOC emissions.
PPG also introduced low-temperature chemicals for the degreasing tanks, such as PPG ULTRAX 94D, a liquid alkaline cleaner developed for use in low-temperature cleaning. For the phosphate application on multi-metal substrates, PPG introduced Chemfos 700AW and 700RW.
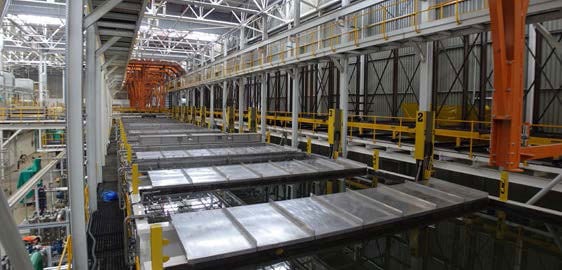
Image courtesy of PPG.
Green Chemistry Collaboration Receives Support from EU Innovation Fund
The European Union Innovation Fund has selected Project Air, a unique production facility for sustainable methanol in Stenungsund, Sweden, as one of 17 large-scale green tech projects to be granted more than €1.8 billion. Project Air, which is a collaboration between Perstorp, Fortum and Uniper, applied for €97 million, and the total investment is expected to amount to more than €230 million.
Project Air will help the chemical industry move from fossil raw materials to recycled and bio-based feedstock, thereby enabling sustainable chemical products for a variety of industries and end products. At full capacity, it will reduce global CO2 emissions with close to 500,000 tons from today’s levels, corresponding to 1% of current emissions in Sweden.
Project Air is based on innovative usage of existing technology in a large-scale industrial application. To produce sustainable methanol, the facility uses significant amounts of CO2 and other residue streams recovered from Perstorp’s ongoing operations, biogas from new dedicated plants, and hydrogen from a new large electrolysis plant. Existing wastewater treatment will be utilized as feed water for the electrolysis. All electrical energy for the combined project will be renewable-based. The ambition is to start up large-scale production by 2026.
Project Air will be built at Perstorp’s existing facilities in Stenungsund, strengthening the regional chemicals industry cluster, Hållbar Kemi 2030. The sustainable methanol from Project Air will be used to produce chemical products that in turn are used in a variety of applications and industries. As a result of the upstream positioning of the chemical industry in the value chain, the project has the potential to make many other production processes and industries more sustainable.
“The Innovation Fund’s decision shows that Project Air is an important future investment for the climate. This is a crucial decision for Perstorp, our customers and partners, as it creates increased availability of sustainable chemical products throughout our value chains. The chemical industry needs the carbons, but it must be non-fossil carbons and they must be put into circular flows so we get rid of CO2 in the atmosphere,” said Perstorp president and CEO Jan Secher. “I am proud to be the leader of a company that has the ability to drive such an industry leading transformation project.”

Image courtesy of Perstorp.
APC Announces Tank Coating Deal with James Fisher
Advanced Polymer Coatings (APC) is increasing production after striking a new deal with British marine services provider James Fisher and Sons plc. The deal will see Ohio-based APC supply its MarineLINE tank coating to the Sir James Fisher, a new LNG-powered, dual-fuel chemical tanker the company is building at the China Merchants Jinling Shipyard in Yangzhou, China. The ship is the first of two James Fisher is building at the yard; the second ship will be named the Lady Maria Fisher.
The Sir James Fisher. Photo courtesy of Advanced Polymer Coatings.
APC said it is set to complete the job by the fall. The coating application will be led by APC’s Shanghai-based China office. An experienced inspection and heat cure team, and APC’s head office in Avon, Ohio, will also be involved in the project.
Captain Onur Yildirim, APC global marine manager, said China is a key market for APC. “Over the last two decades, we coated and repaired a vast range of different chemical tankers in shipyards across China,” he said. “We are very pleased to continue to work with a company of the pedigree of James Fisher and believe the quality of MarineLINE and its broad range of benefits helped us win the work.”
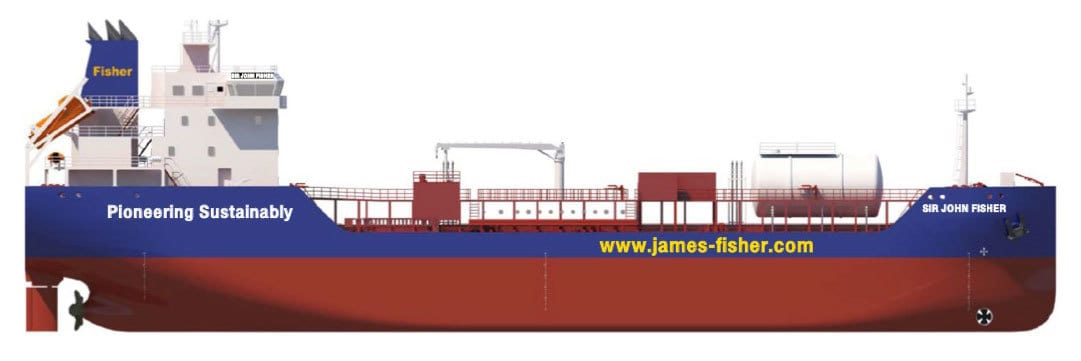
Teknos Group Exits Russia
Teknos Group, which suspended its Russian operations in March 2022 and in April 2022 announced a controlled exit from the Russian market, has completed the process of exiting the country. As of July 11, 2022, 100% of shares in the company’s Russian entity, Teknos OOO, were sold.
Teknos began operations in Russia in 2005. The company had offices in Moscow and a fit-for-purpose production plant in St. Petersburg, which opened in June 2015.
“This is a sad and unique moment in Teknos history. This was the only way to ensure any continuity for our personnel. I wish the new owners good luck in running the business, supported by the expertise and experience of our Russian team,” said Paula Salastie, Teknos CEO and owner of Teknos Group.
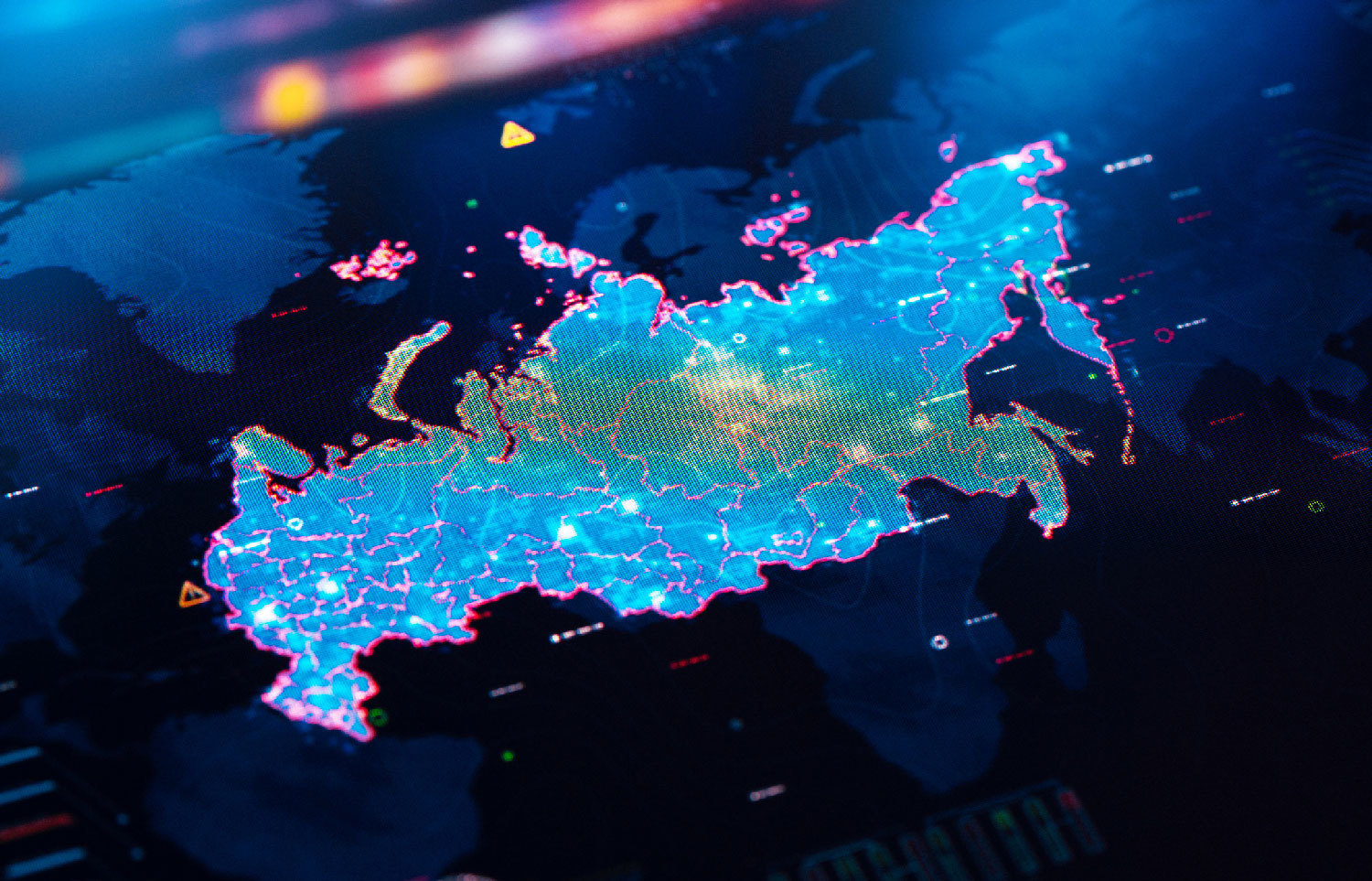
Credit: da-kuk, E+, via Getty Images
Thermal Product Solutions Acquires Redline Chambers
Thermal Product Solutions LLC (TPS), provider of thermal processing products and test solutions, announced the acquisition of Redline Chambers, an American manufacturer of vacuum chambers and systems for the aerospace, defense, energy, electronics, and medical industries. Located in Salt Lake City, Utah, Redline Chambers specializes in providing customers with vacuum technology and leak testing solutions.
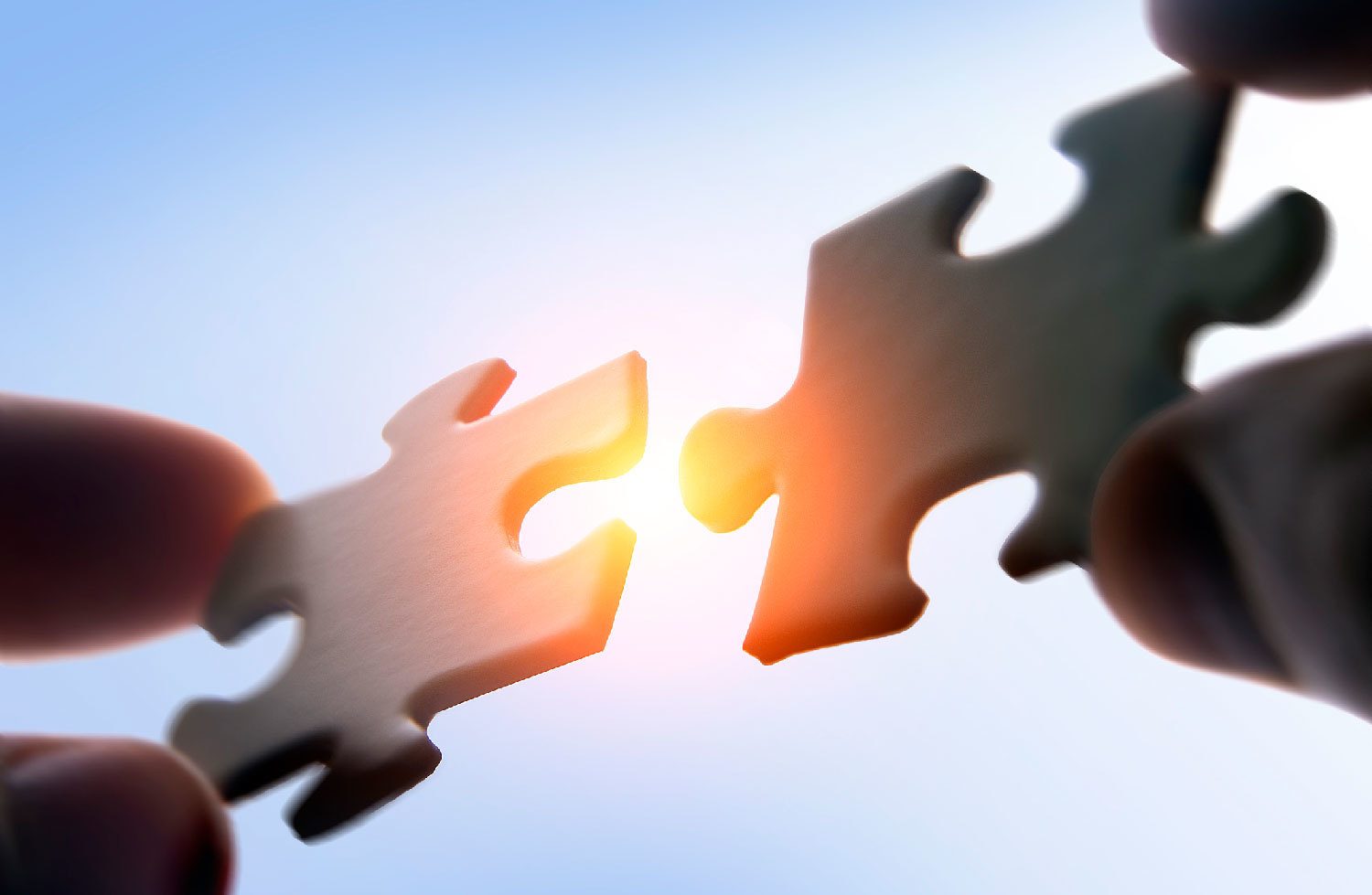
Credit: mikdam, iStock / Getty Images Plus, via Getty Images
TPS provides products for thermal processing and test solutions with brands including Baker Furnace, Blue M, Gruenberg, Tenney, Lindberg, MPH, Wisconsin Oven, and now Redline Chambers. The Redline Chambers acquisition supports the continued growth of TPS within the vacuum chamber market.
“We are excited to have Redline Chambers join TPS’s family of brands. Redline’s ability to engineer and manufacture vacuum chambers and systems will bolster TPS’s ability to serve customers in this expanding market,” said Greg Jennings, president and CEO of TPS.