Ready to proof -- Niki 7/10/23
CB proofed 7/11 - comment below for Niki in references and also Niki is still adding decks
Revised Niki - 7/12/23
KJ proofed on 7/12 - left a few notes for Niki. Thanks.
Revisions set - Niki 7/13/23
Back to the
Credit: sergeyryzhov, iStock / Getty Images Plus, via Getty Images.
Future!
UV/EB Technology as a Sustainable Solution to the Energy Crisis
By Michael R. Bonner, Vice President, Engineering & Technology, Saint Clair Systems, Inc.; and Cara Bommarito, Sustainability Manager, RadTech North America
The foundation for ultraviolet (UV), electron-beam (EB), and UV-LED technology, also known as energy-curable technology, was developed in the late 1920s by Edwin Newton of the B. F. Goodrich Company to "vulcanize" natural rubber.1
UV curing began to evolve in the 1960s.1 Since that time, energy-curable technology has been, and continues to be, one of the most sustainable technologies used in manufacturing. These technologies deliver higher throughput efficiency, reduced waste, and reduced CO2 emissions, resulting in their recognition, by several regulatory agencies, as clean process alternatives. This article examines the factors driving this technology, supported by case studies demonstrating how UV/EB-curable technology enables innovative manufacturing processes that consume less energy, yet meet or exceed air quality standards without requiring add-on pollution controls.
Why is Energy the Issue?
The world’s thirst for energy is well documented. As Figure 1 shows, despite significant conservation efforts, since 1990 the total annual global demand for energy has increased by more than 67%. This graph extends through 2021, not 2020 (30 years), because of the exceptional 4.5% reduction in 2020 resulting from the pandemic shutdowns. This reduction was even more extreme than the 1.0% reduction in 2009 caused by the “Great Recession” – the only other year-over-year decline during these three decades.
From Figure 1, it is apparent that the greatest growth in energy consumption over the last 30 years took place in Asia.
FIGURE 1 ǀ World energy consumption since 1990 by region.2
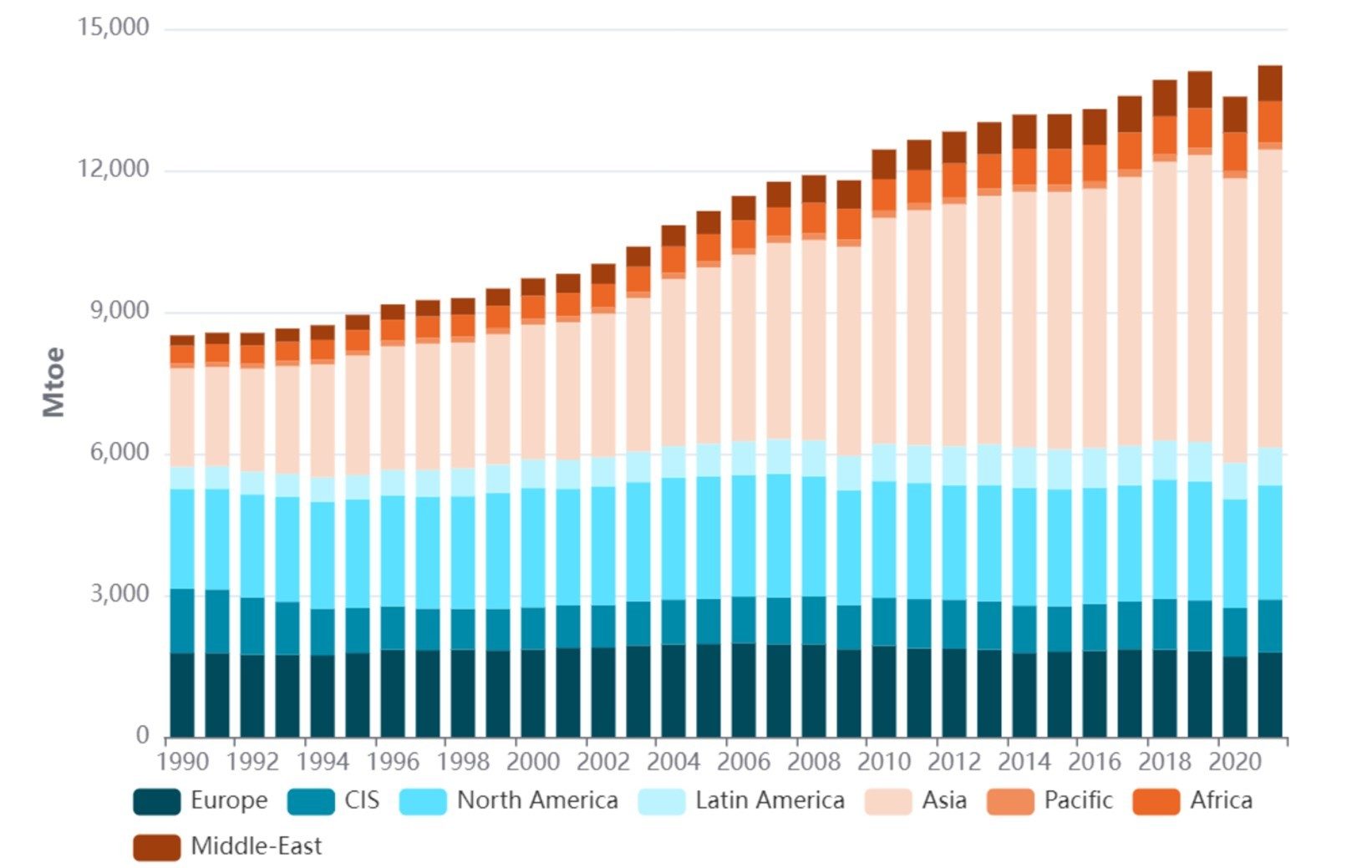
Figure 2 breaks down energy consumption by country. From this figure, we can see that China, India, South Korea, Iran, and Indonesia all showed triple-digit growth in energy consumption as a result of their increase in industrialization. On the other hand, Germany, Japan, and Russia all showed reductions in energy consumption over the same 30-year period.
FIGURE 2 ǀ Change in energy consumption by country since 1990.2
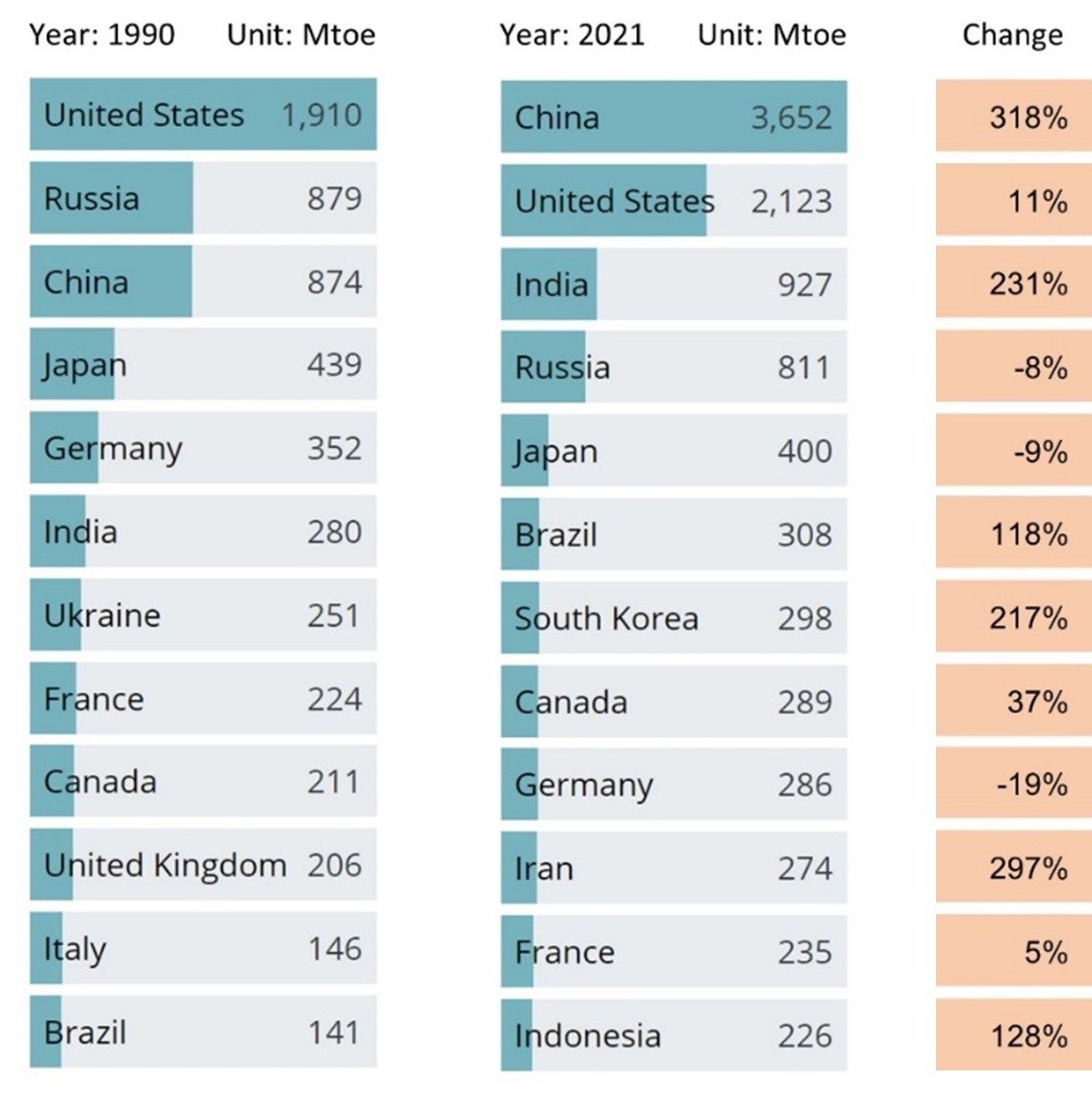
It’s interesting to note that Iran, South Korea, and Indonesia were not among the top 12 energy consumers in 1990, while usage in Italy, Ukraine, and the United Kingdom was so controlled that they were no longer in the top 12 by 2021. This truly shows how much the world has changed in just 30 years.
The Energy Crisis
In November 2022, in its Market Outlook Series, “Global Energy Market Outlook,” The Adhesive & Sealant Council noted, “Global energy markets are in an upheaval led by geopolitical conflicts, macroeconomic issues such as high inflation rates, and supply disruptions.”3
Despite concerted efforts to move to “clean energy” sources to reduce the impact of energy generation and consumption on the global environment, the demand has simply grown too fast for these technologies to meet the increased need by themselves. This gap leaves the energy supply just as susceptible to geo-political issues as it was in the 1970s. Nowhere is this more apparent than in Europe, where the cost of energy skyrocketed due to the war in Ukraine and the resulting sanctions against Russia. In October 2022, Gary Vasilash of Gardner Business Media’s On Automotive wrote, “S&P Mobility calculates that since Q1 2020 natural gas prices in Italy, Germany, France, and the United Kingdom have increased an average 2,183%. Wholesale electricity prices are up 1,230%.”4
As shown in Figure 3, these increases have driven up the cost of energy to produce an automobile in Europe by upwards of 1,700%. But this energy crisis is not limited to Europe alone. In November 2022, Sonal Patel added, “Power shortfalls could be rife over the next three months across a large portion of the North American bulk power system (BPS), particularly during extreme and prolonged cold conditions, the North American Electric Reliability Corp. (NERC) has warned.”5
FIGURE 3 ǀ Energy cost per automobile since 2020.4
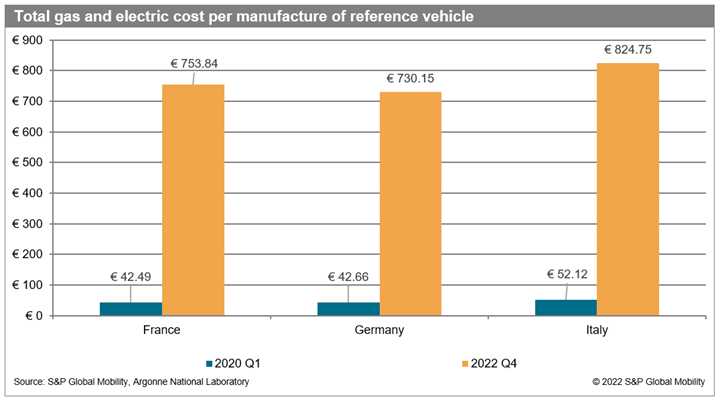
Though the mild winter provided some relief for both North America and Europe, this recent volatility in the energy market clearly demonstrates the need to migrate to solutions that are more energy efficient. Energy-curable technologies offer an attractive solution for a host of reasons, including increased energy efficiency compared to today’s conventional coating processes.
What’s the Difference Between Thermal Cure and Energy Cure?
Conventional coating technologies, often referred to as solventborne, waterborne, or powder coat, are thermal-cure technologies. Thermal cure means that the coating is cured by baking – or bringing it to an elevated temperature – which drives out the solvents (solventborne/waterborne) or melts the powder (powder coat), then initiates the cross-linking process. This baking process is performed in an oven, which consumes a great deal of energy to heat the oven, the air, the parts, the coating, etc.
Specifically with organic solventborne coatings, “driving out solvents” means releasing volatile organic compounds (VOCs) into the air in the oven. The release of VOCs presents a couple of problems. First, the solvent vapors are flammable (volatile), so they must be removed from the oven to prevent an explosion. However, VOCs are also harmful to the planet (and the life on it), so simply releasing them into the atmosphere is not acceptable. The solution is to incinerate the VOCs to remove them from the air stream before it is released into the atmosphere. This incineration is usually performed in a regenerative (or recuperative) thermal oxidizer (RTO). The RTO takes advantage of the flammability of the solvents in the airstream as a fuel, but it is usually necessary to supplement it with natural gas to ensure that the temperatures in the RTO are high enough to destroy the carbons in the exhaust stream. This further exaggerates the energy consumption of the thermal-cure system.
Energy-cure coatings, on the other hand, are formulated so that there are no solvents in the blend. The curing/cross-linking process is initiated by exposing the coating to either high-energy electrons or a high-energy light wave – often in the ultraviolet (UV) band. Because this energy is focused on the coating, it is far more efficient, requiring significantly less energy to perform the curing function – as much as 95% less! Moreover, there are no VOCs to incinerate, so no RTO or other remediation is required to protect the environment.
So how did energy-cure systems come to be?
The History of Energy-Cure Technology
As noted earlier, the origins of energy curing go back to work done by Edwin Newton of the B. F. Goodrich Company in the 1920s. Newton developed a method using high-energy electrons to "vulcanize" natural rubber for which he filed a U.S. Patent in 1929 (US Patent 1,906,402, filed February 19, 1929, and issued May 2, 1933). This came to be known as electron beam (EB) technology. The use of EB to partially cure tire components is still a standard practice in the industry.1
UV curing began to evolve in the 1960s with major commercialization during the 1970s, driven by the energy crises brought on by the OPEC oil embargo of 1973. At that time, as shown in Figure 4, the United States was importing most of its natural gas, and, as pointed out by HG Experts in their article, An Introduction to Ultraviolet Light (UV) and Electron Beam (EB) Curable Coating Technology, “The commercialization of UV-curable inks in the 1970s enabled beverage companies to accommodate a reduced availability of natural gas with a technology that depended solely on readily available electric energy.”7 Since that time, countless industries have recognized and exploited the advantages of energy-cure technologies in their processes.
FIGURE 4 ǀ U.S. natural gas imports and exports.6
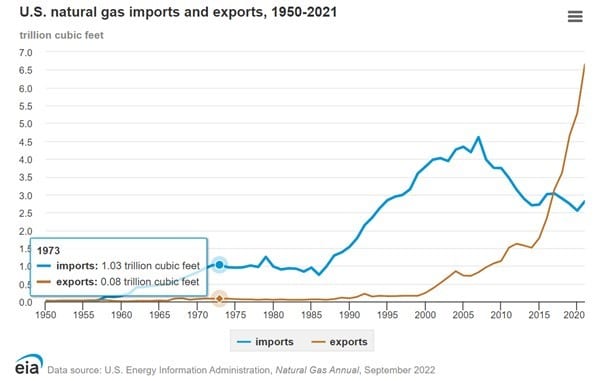
The Benefits of Energy Cure Coatings
Advancements in chemistry over the last 50 years have made an extensive number of options available to formulate coatings to meet a wide variety of cured-film properties. This makes energy-cure technology available for virtually any application.
In addition to the significant reduction in energy usage, and the natural sustainability since these formulations contain no VOCs, energy curing offers many other advantages:
- Durability: Energy-cure coatings are often more durable than their conventional counterparts, and therefore provide superior protection.
- Speed: The instantaneous curing of these materials eliminates wait time, resulting in shorter processing times and increased throughput.
- First-Pass Yield: Since full cure is reached instantaneously, handling issues like scratches, blocking, etc., associated with conventional coatings are eliminated. This reduces rejects, rework, and scrap.
- Footprint: Because large curing ovens are not required, energy-cure systems are much smaller and take up significantly less space than conventional processes.
- Less Waste: All these factors, combined with the fact that energy-cure materials can be collected and reused, result in a significantly reduced waste stream from the process.
- Clean Energy Support: The reduction in energy required to power the energy-cure process enables clean energy alternatives by reducing demand on the grid.
The benefits aren’t just limited to processing and performance. There are also significant advantages from a regulatory perspective, too.
Reduced Regulation
Federal, state, and local governments recognize the many advantages offered by UV-/EB-curable coatings in complying with VOC and HAP restrictions. For example, UV-curable coatings for metal can application have been reported by the EPA to contain less than 0.01 VOC/gallon of coating. Coors reported no significant emission of ozone or other undesirable emissions from a UV can line for one billion cans per year.7
In 2019, the California Senate formally adopted a resolution recognizing UV/EB technology as a pollution prevention process, which, unlike conventional technologies, emits little to no harmful emissions. The nature of the process is such that virtually no VOCs or hazardous air pollutants (HAPs) are generated. Additionally, UV/EB processes do not produce combustion contaminants such as NOX, SOX, or greenhouse gases, which are heavily regulated in California.8
The South Coast Air Quality Management District (SCAQMD) is the air pollution control agency for all of Orange County and the urban portions of Los Angeles, Riverside, and San Bernardino counties in California, which is the second most populated urban area in the United States and one of the smoggiest. Every three years, SCAQMD submits a plan showing how it proposes to achieve its air quality goals. In this plan, the SCAQMD includes UV/EB/LED as a means to improve air quality.8
Additionally, in 2005 a Clean Air Award was presented by the SCAQMD to RadTech – the Association for UV and EB Technology – in the category of Advancement of Air Pollution Technology in recognition of exemplary leadership, innovation, and foresight.8
Success Stories
Earlier, we noted that in the 1970s, UV-curable inks enabled beverage companies to compensate for the reduced availability of natural gas with a technology that depended solely on readily available electric energy. As a bonus, companies such as Coors found that switching to UV-curable inks for metal can decoration substantially reduced energy and operational costs. These savings amounted to more than $1 million per year.7
The printing example extends to the in-line application of UV-curable clear coatings in a conventional four-color printing process to eliminate the need for spray powder. Spray powder was typically used to prevent the wet ink from offsetting (transferring onto an adjacent surface), while the printed stock was stacked waiting to be fabricated. This is also commonly called blocking. By replacing spray powder with a UV-curable coating on the last station of the printing press, the coated stock can be immediately fabricated as it comes off the press. The use of UV coatings significantly increases productivity by eliminating the need to wait for the conventional ink to dry. Printers using UV-/EB-curable inks for general printing achieve additional advances in productivity and process versatility.7
The Case of Coil Coating
The coil coating process is a modern example that clearly demonstrates all of these advantages. If you’ve never seen this in action, it is a little like the movies you’ve seen of a newspaper printing line, moving at blurringly high speed – up to 300 mpm (1,000 fpm). The big difference for this process is that the substrate is usually either steel or aluminum, instead of paper (Figure 5).
FIGURE 5 ǀ Typical coil coating process.9
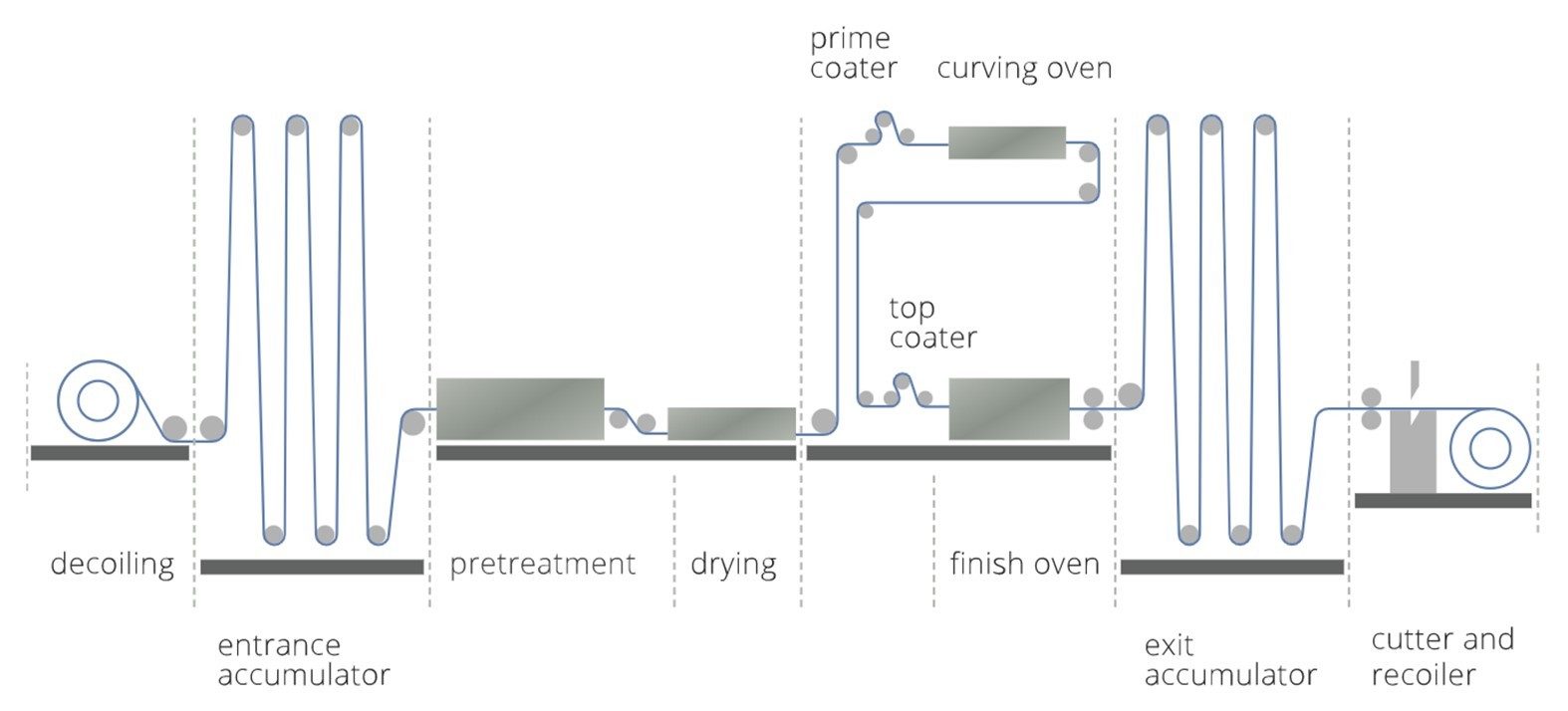
Key from an energy point of view is the fact that these coatings are baked on, which means the metal must be brought to a high temperature in a large oven to cure the coating after it has been applied. In addition, most of the coatings used are solvent based, which means that the VOCs that come out of the coating during the baking process must be removed from the air and not discharged into the atmosphere. The most common method for dealing with these VOCs is to incinerate them in an RTO (regenerative or recuperative thermal oxidizer) as shown in Figure 6.
FIGURE 6 ǀ Oven and RTO process.10
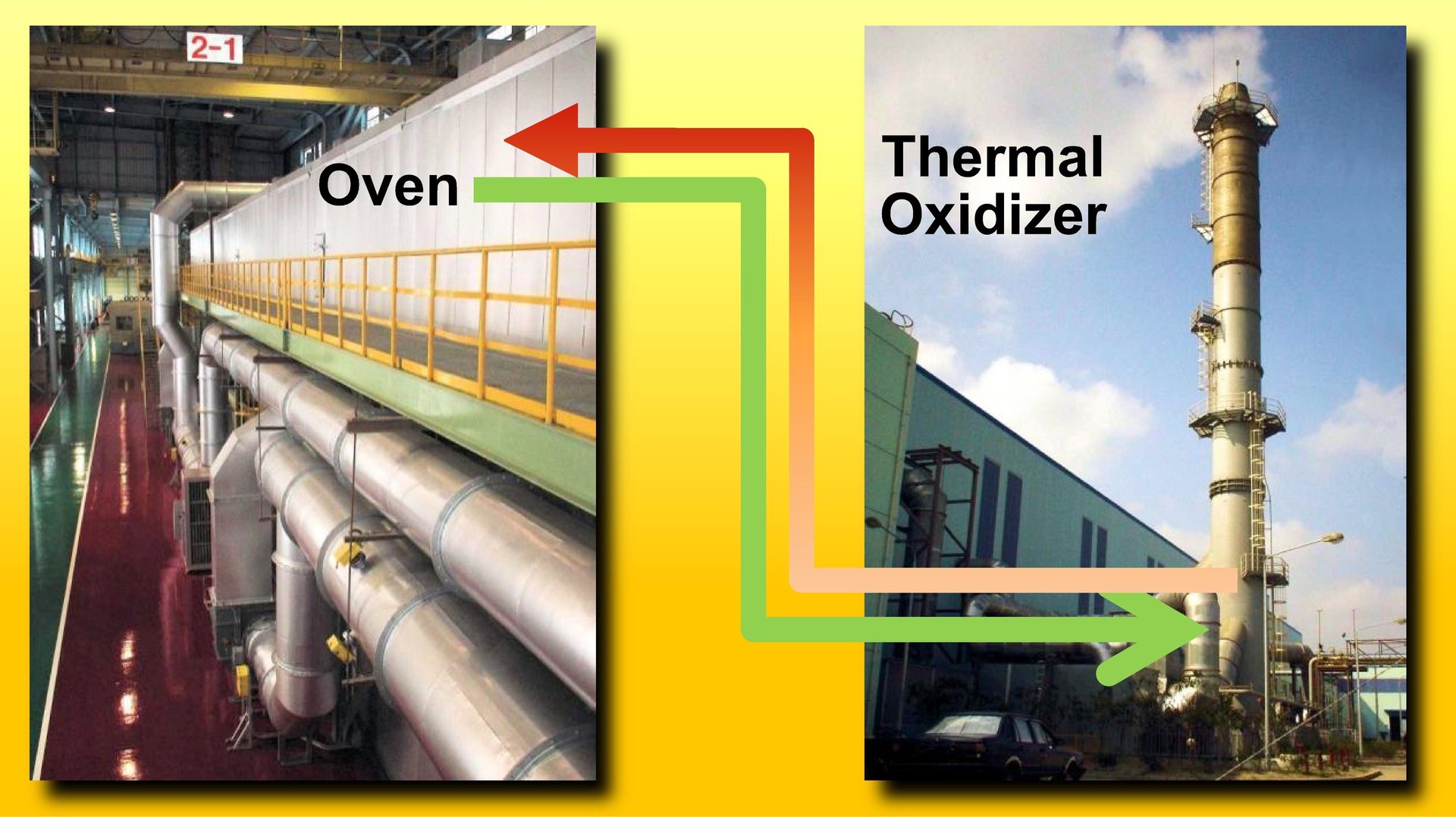
These two processes require a significant amount of energy in the form of both natural gas and electricity. In fact, despite the large transport motors and the cleaning and pre-treating process, this still consumes as much as 80% of the energy used in the plant.
The team at PCT Ebeam and Integration worked with a customer who required a new aluminum coil coating line and was interested in the energy savings possible with an EB-curing system. The required operating parameters for the new line were given as shown in Figure 7, and the operating cost data for the plant was provided as shown in Figure 8.
FIGURE 7 ǀ Required operating parameters.11
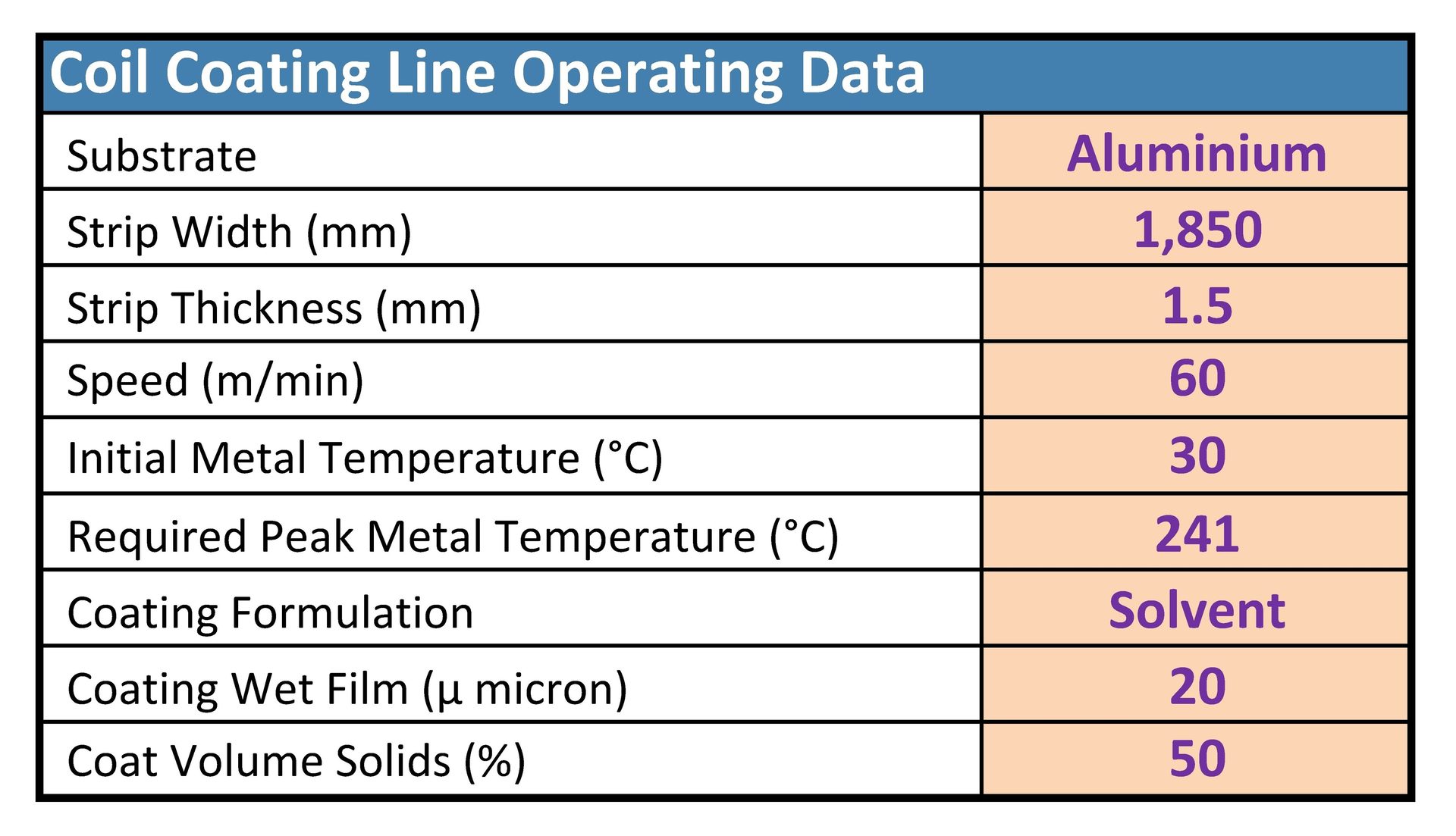
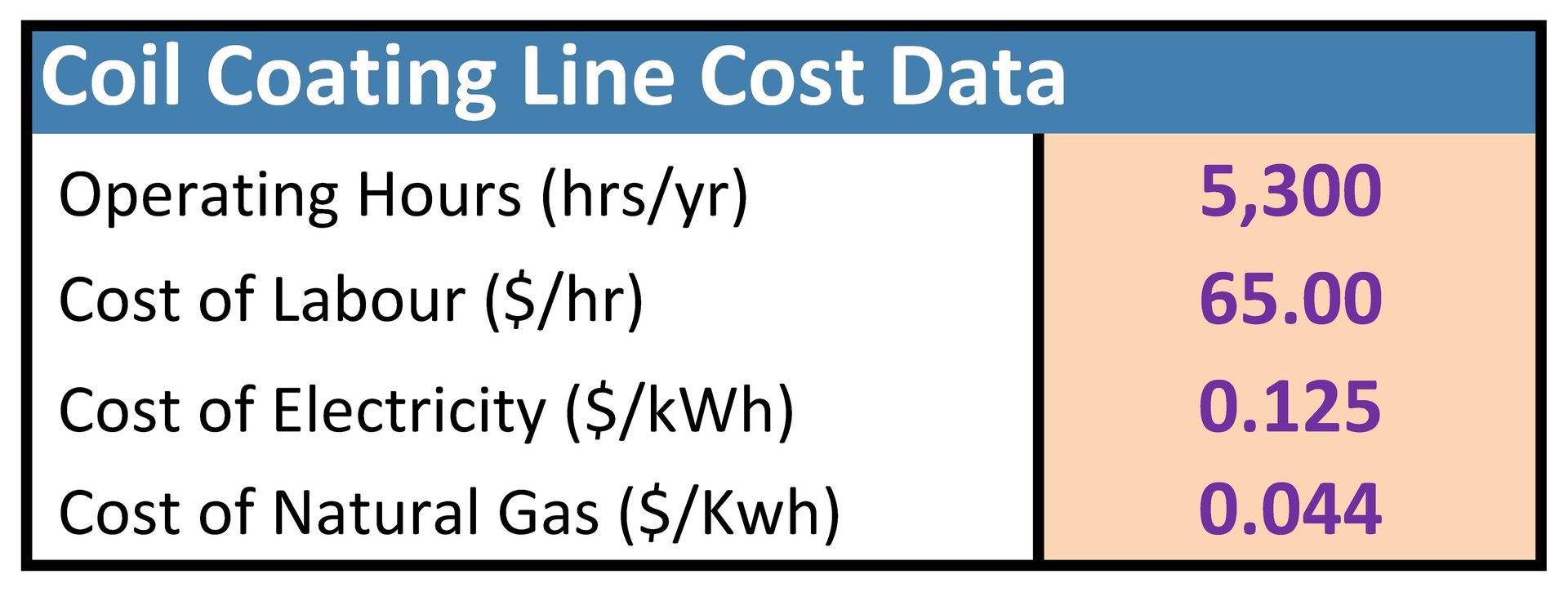
FIGURE 8 ǀ Plant operating cost data.11
PCT knew that the EB unit they would use to cure 20 µm of coating across a 1,850 mm-wide strip, moving at 60 m/min would require 130 kW of electric power. Because the EB-curable coating is 100% solids, there are no solvents to evaporate out and incinerate, so no RTO would be required.
To generate a comparison with the conventional solventborne coating, it was necessary to calculate the energy (electricity and natural gas) required to operate an oven and RTO (Figure 9).
FIGURE 9 ǀ Required drying energy.11
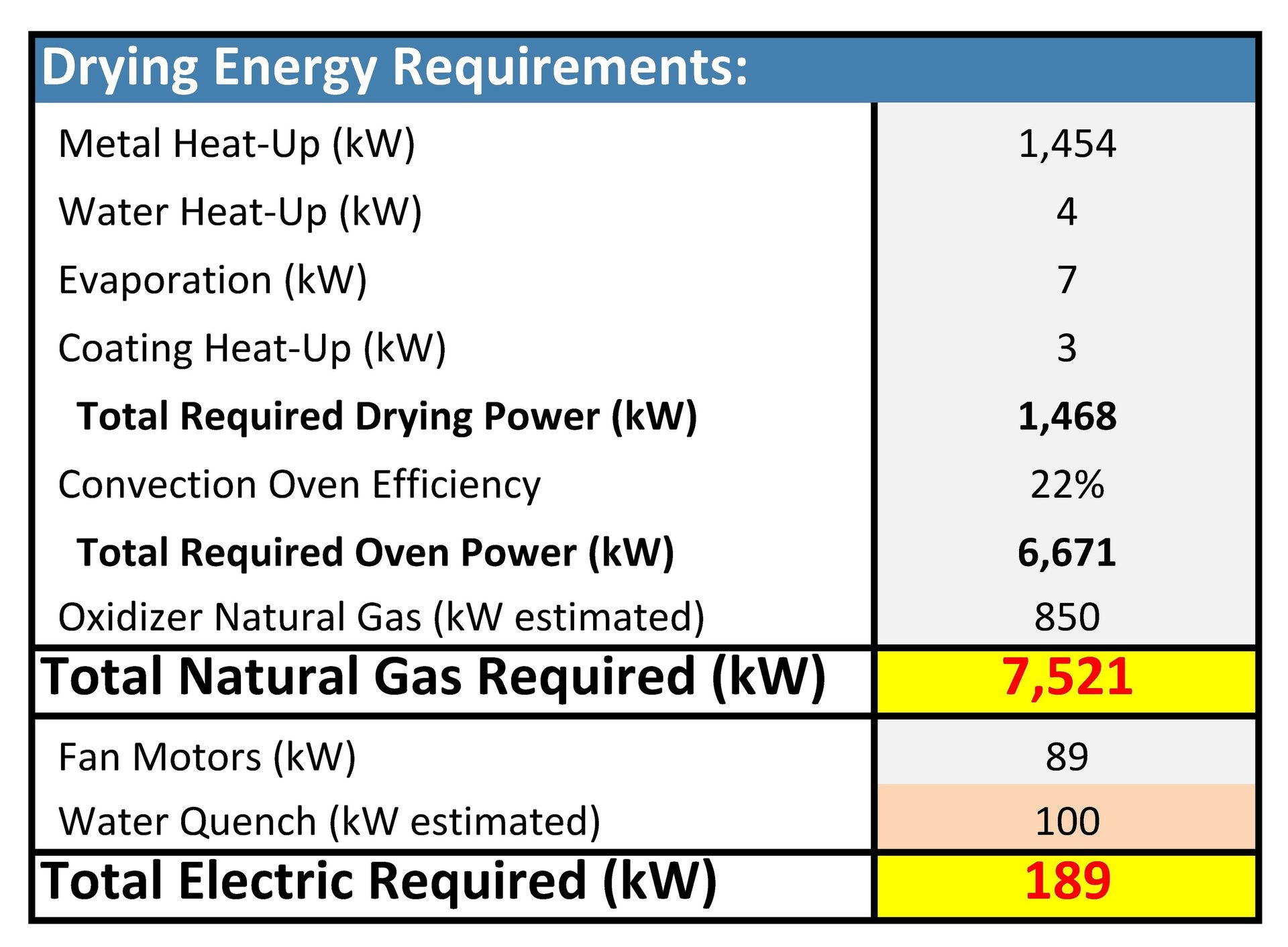
The 130 kW EB unit requires less electricity than the fans and water-quench system (189 kW) necessary for cooling the strip as it exits the curing oven. When natural gas is taken into account, this amounts to a greater than 98% reduction in energy consumption (Figure 10).
FIGURE 10 ǀ EB to conventional coating energy cost comparison.11
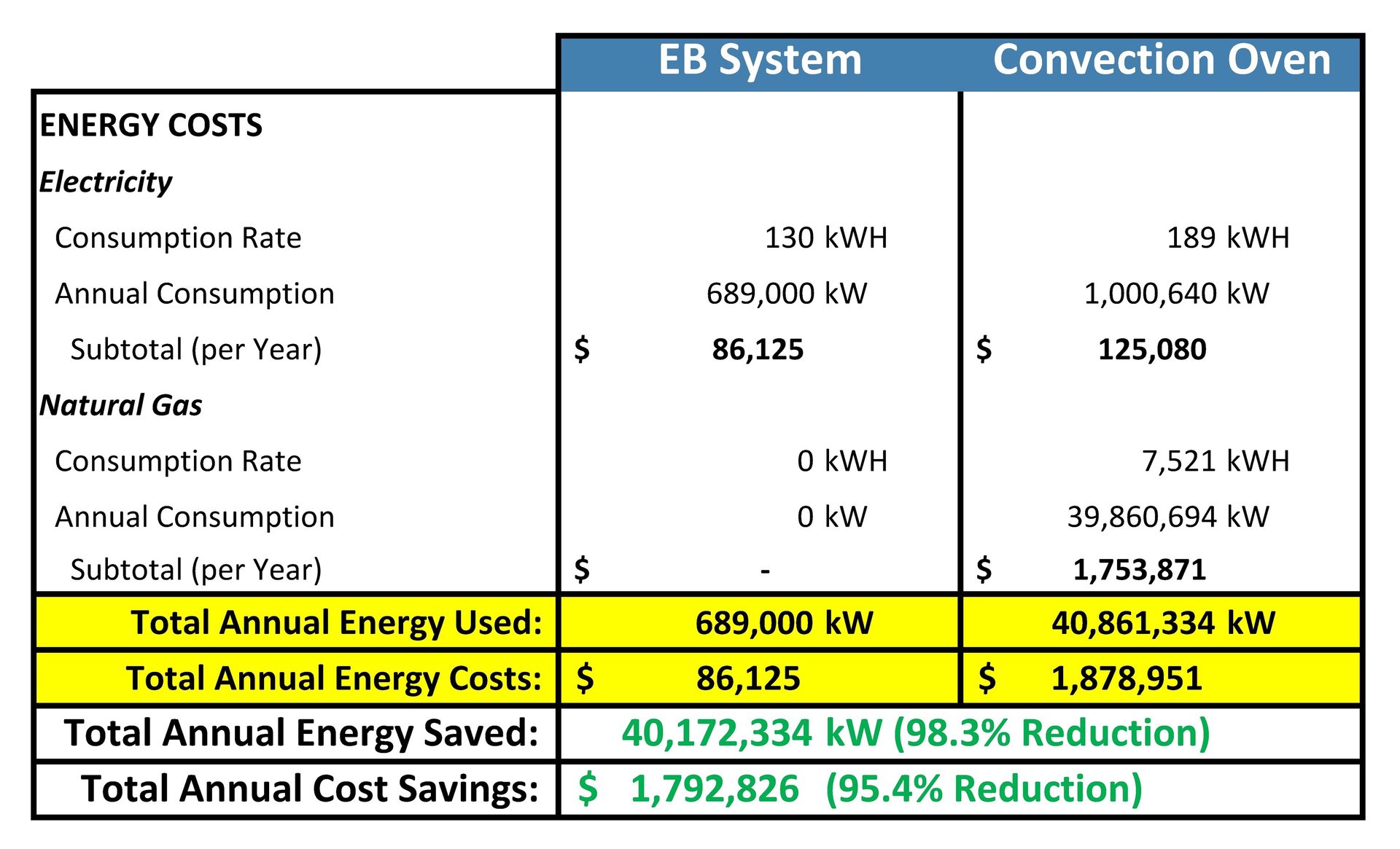
Yet, the key to any project is the dollars involved and the resulting return on investment, so using the data shown in Figure 8, the reduction in operating cost can be calculated. Referencing Figure 10, we can see that the 98.3% reduction in energy usage for the EB-curing system results in a 95.4% reduction in operating costs for energy. If the company operates at the expected 5,300 hours/year (Figure 8), this amounts to a cost savings of nearly $1.8M per year.
Conclusion
It is amazing how often the solutions to our “new” problems come from work started by those who came before us – often searching for answers to an entirely different set of problems. So, as we look at the problems our world faces regarding energy consumption, pollution, sustainability, carbon footprint, and their tangled relationship to the health of our planet, it should be no surprise to find solutions hidden in work from the past.
Energy-cured materials are a great example. Borne out of necessity early in the industrial age, and advanced through our last energy crisis, these offer the opportunity to improve the quality and performance of our products, streamline our manufacturing operations, and simultaneously reduce pollution and our carbon footprint – all while significantly reducing our operating costs. This is the true definition of sustainability.
So, can energy-cured materials solve the crises we currently face? Certainly not alone. But they do provide a pronounced step forward with a significant impact.
The only question is, what are you waiting for?