Ready to proof -- Clare 11/8/22
KJ proofed on 11/13 - clean from my end
CB - clean on my end
ASK JOE POWDER
Sponsored by Gema
Our popular Ask Joe Powder blog has made its way to the pages of PCI magazine. What are your powder coating questions and challenges? Joe Powder, aka Kevin Biller of ChemQuest Powder Coating Research, shares his powder coating knowledge and expertise by answering questions sent in from around the world.
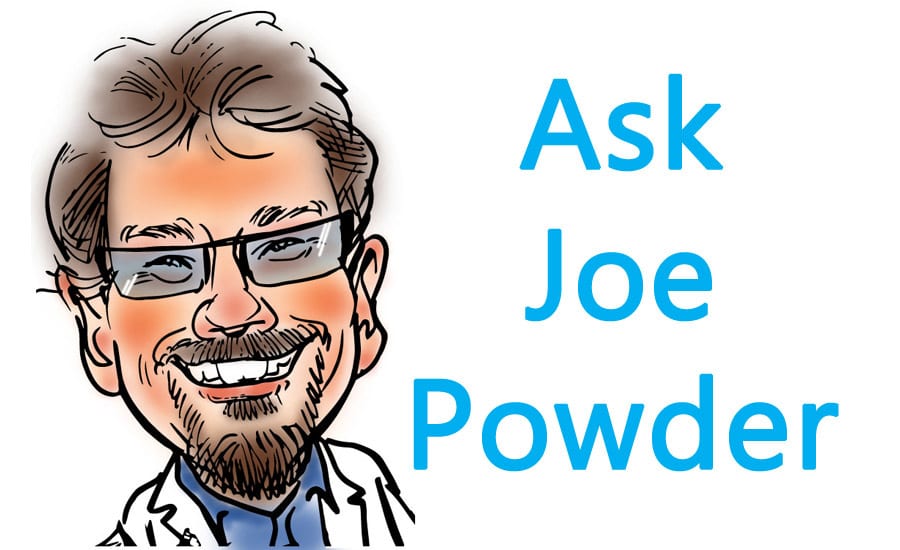
Dear Sir,
Can you please explain how the powder will charge in a corona-type gun? Is it charged with an electrode? Which type of nozzle should be used, a flat jet nozzle or round jet nozzle?
Thanks,
Shahroz Khan
Pakistan
Greetings Shahroz,
Your question is a good one. Basically, the electrostatic charge in a corona-type powder spray gun is created by ionizing air. The high voltage at the gun tip electrode pulls electrons off air molecules (N2, O2, etc.) and results in a field of negative charge. This electric field converges on the earthed target.
The deposition of powder is accomplished by passing a cloud of particles through the electric field. The particles pick up electrons as they traverse through the field. These negatively charged particles are attracted to the conductive surface if it is adequately connected to earth. As the negatively charged particles accumulate on the surface of the substrate, negative charge leaves the substrate to earth. The loss of negative charge at the surface creates a net positive charge at the interface. This positive face charge secures the negatively charged powder to the surface.
The nozzle type affects the manner in which the powder cloud exits the spray gun. It has only minimal effect, if any, on the charging characteristics of the powder.
I hope this helps answer your question.
Best regards,
Joe
Dear Joe,
What is your recommendation to guarantee an adhesion of powder paint for a hot-dip zinc coating?
Best regards,
Ozlem Ekinci
Turkey
Dear Ozlem,
This is a difficult question. One of the biggest issues is the variability in the quality of the hot-dipped galvanized (HDG). It can be very inconsistent, not only from batch to batch of HDG, but also on different sections of the same part coated with HDG. What I recommend is first careful cleaning of the surface. This can be an alkaline cleaner followed by a good quality rinse. You may also want to consider media blasting as well, however, this adds cost to the process.
As for adhesion, some powder coatings work better than others. A good quality epoxy will adhere better to HDG than a polyester powder. Hybrids (epoxy-polyester) fall somewhere in between. If this is for an outdoor-durable application you need to either use a zinc phosphate pretreatment with the polyester or the combination of an epoxy primer followed by the polyester topcoat.
Also, it is important to de-gas the HDG prior to applying the powder coating. Otherwise you may observe pinholes in the coating. De-gassing involves preheating the HDG and applying the powder to the warm substrate. Preheating to 150 ⁰C to 175 ⁰C usually suffices.
I hope that this helps answer your question.
Kind regards,
Joe
Hi Joe,
I am currently in the process of doing some R&D with powder coating on top of chilled, iron grit-blasted material, and we are currently experiencing problems. I thought you might have a good knowledge of the subject after reading your Q&As with other powder coaters.
The system we have in place is the SA 2.5 grit blasting, then coated with APP120 (a zinc-rich primer), and cured at 180 °C for 30 minutes. However, after this stage the topcoat refuses to adhere to the primed substrate and, when it does, it generally “stars up” during spraying. I have tried spraying it hot (metal temp greater than 150 °C), changing cure times for the primer (shorter bakes at higher temps), lowering gun kVs, and changing the base primer, but the results are not satisfactory. I wonder if there is anything basic that I could be missing or a variable that I have overlooked that might improve the results.
Kind regards,
James Breen, BSc Bio Med
Quality Technician
Hello James,
Thank you for your question. It sounds like you're getting rather frustrated in getting good parts off your finishing line. You are wise to select the materials and process you are trying to make work. Blasting the metal is a good idea, and the dual coat approach gives a very durable finish. To make this work, the devil is in the details.
The biggest problem seems to be getting a good second coat on these primed parts. The first place to investigate is "are you getting a good earth to your parts?" If you are seeing starring and poor film build, you probably have poor electrical continuity to the earth. Checking for earth requires a megohmmeter that not only measures resistance but also provides up to 500 VDC, which helps define resistance more accurately. You want to have 1 megohm or less resistance. If it is greater than 1 megohm start looking for poor contact points including hooks, hangers, racks, and conveyors.
Regarding the powders, I would stick with the original powders and work on the application process. It is wise to undercure (or "gel") the primer prior to applying the second coat, then fully bake the two coats. This provides the best inter-coat adhesion.
I hope this helps. Please let me know if you have any further questions.
Warm regards,
Joe Powder