Ready to proof -- Clare 12/10/21. (I had to redo some of the figures because the text was blury)
KJ proofed and corrections sent on 12/10
Revised on 12/10
Ready for author
Photo: taka4332, iStock/Getty Images Plus, via Getty Images
Highly Efficient Organic Thixotrope for Non-Aqueous Industrial Coating Systems
Enhanced Performance Through Applied Innovation
By Chris Sieto, Regional Market Manager, Elementis Global, East Windsor, NJ
Marine and protective coatings typically have very high requirements in terms of sag stability. The systems are typically spray applied in high layer thicknesses of around 1,000 µm (or even more) in one pass. This high demand of the systems limits the selection of suitable rheology modifiers.
Organic thixotropes provide the properties to fulfil this specific need. However, especially older classes of this technology have complex requirements in terms of incorporation and activation. Elevated temperatures at a specified range, combined with high shear for a defined period of time, in accordance with the system that can be based on a manifold of binder chemistries and various solvent compositions, are required to achieve optimum performance (Figure 1).
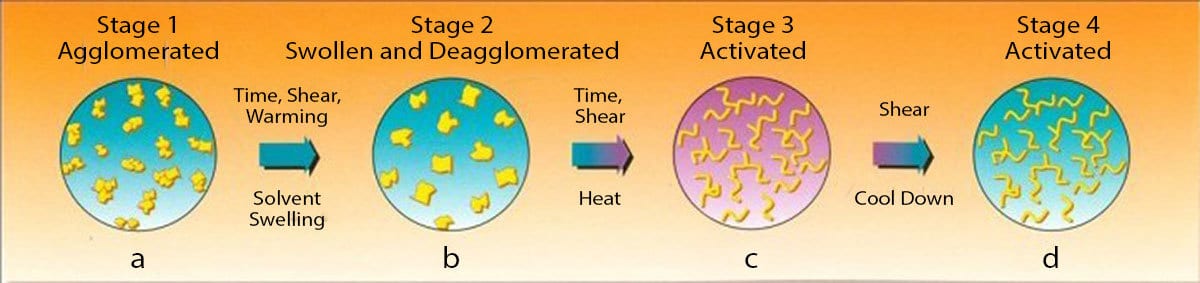
FIGURE 1 ǀ Activation of organic thixotropes.
From a processing point of view, usually the batch-by-batch technique is used. External heating or cooling equipment is often not available so that active temperature control during processing is either not possible or only available on a lab scale. The necessary energy to obtain and adjust the activation temperature is in such cases normally generated by friction during dispersion. The end temperature is dependent on parameters such as disperser speed and pigment/extender loading level, and has a strong influence on the entire processing time. Therefore, rheology modifiers that are suitable for use over a wider temperature range show significant benefits.
Product Class Comparison
Organic rheological additives provide outstandingly high low-shear viscosity in combination with a strong thixotropic flow character in non-aqueous systems. As shown in Figure 2, in comparison to, for example, fumed silica, the low-shear viscosity is much higher. With respect to practical relations, this means that organic thixotropes provide potentially the highest film build properties. On the other hand, fumed silica provides higher viscosities at high shear rates. This effect often adversely affects the sprayability, especially the atomization during application.
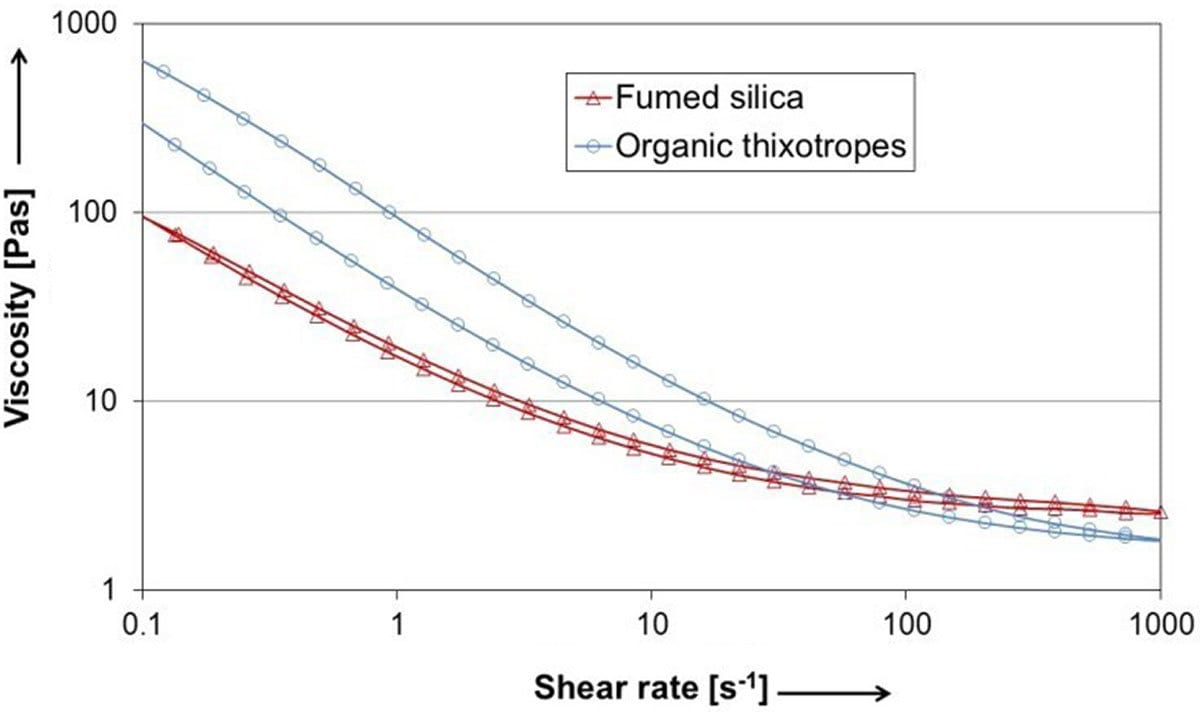
FIGURE 2 ǀ Comparison to other product classes.
Organoclays, which are used to a lesser extent in this market segment, are more beneficial in terms of levelling, combined with well-balanced anti-sag performance.
For activation, the diamide-based rheology modifiers need to be exposed to mechanical forces applied alongside with specific temperature over a defined period. The mentioned activation temperature needs to be in line with the relevant solvency forces.
Product Chemistry
After activation, the rheological structure is built up by the molecules orienting towards each other, forming a fibrillar structure due to the nature of the amide functionality, as shown in Figure 3. The driving forces for this process are intermolecular interactions such as hydrogen bonding and van-der-Waals forces.
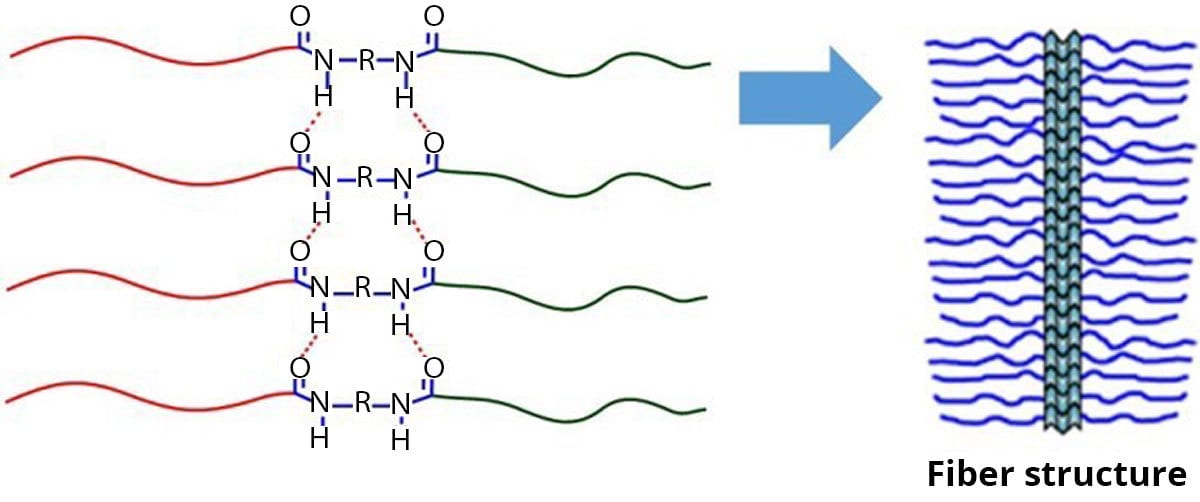
FIGURE 3 ǀ Thickening mechanism.
Castor waxes, the oldest class of organic thixotropes, require similar processing, however are much more sensitive to changes in the systems’ solvency forces and processing temperature. Further, they do not cover the entire solvent range. Additionally, they have a much higher risk of certain side effects such as seeding and false body.
The latest class of diamide rheology modifiers out of the THIXATROL® PM and THIXATROL AS series allows proper activation over a very wide range of application temperatures in order to allow formulators robust and predictable processing under real-life conditions where temperature variations often occur, e.g. between summer and winter.
Further, these products are applicable at markedly lower temperatures than traditional grades based on similar chemistries. This is especially of great importance in solvent-free systems where the activation temperatures are normally high. The main advantage of such low-temperature activation is energy and cost savings in the manufacturing process. The process can be carried out without external heating and is faster.
Renewable Resources
Also, from a sustainability point of view, these kinds of rheology modifiers are very interesting. The new rheology modifiers out of the THIXATROL product line are produced from renewable resources (>75% bio content).
However, even with these major improvements, not all formulations are covered. In systems of higher polarity, especially when formulating with various alcohols, e.g. benzyl alcohol or butanol, a drop in efficiency in comparison with less-polar systems is often the result. Alcohols are becoming more and more popular, and are being formulated often in higher concentrations to reduce the amount of aromatic solvent. In addition, they are required to stabilize the system and enhance the adhesion of the coating to the substrate.
New THIXATROL PM 8058 has been developed to provide solutions exactly for these kinds of formulations, utilizing higher amounts of highly polar solvents. Furthermore this product is significantly more effective than the other rheology modifiers in the THIXATROL PM and THIXATROL AS series.
Improvements with THIXATROL PM 8058 become obvious in the following model study, in which a high-solids epoxy-based primer with 83% solids content was formulated with varying solvent ratios in comparison to a commercially available reference organic thixotrope. In all cases, the concentration was chosen on a level of 0.5%. This was done to emphasize the effect of the organic thixotrope at lower viscosity levels and to visualize the effect of the various solvent compositions on the viscosity build.
As can be seen in Figure 4, in the standard formulation the solvent part was dominated by xylene. In the other versions, either isobutanol or benzyl alcohol are used in the highest concentration. The activation process was performed by a tooth-bladed Cowles dissolver at 16 m/s. The activation temperature was (in all cases) adjusted to 66 °C for 25 minutes.
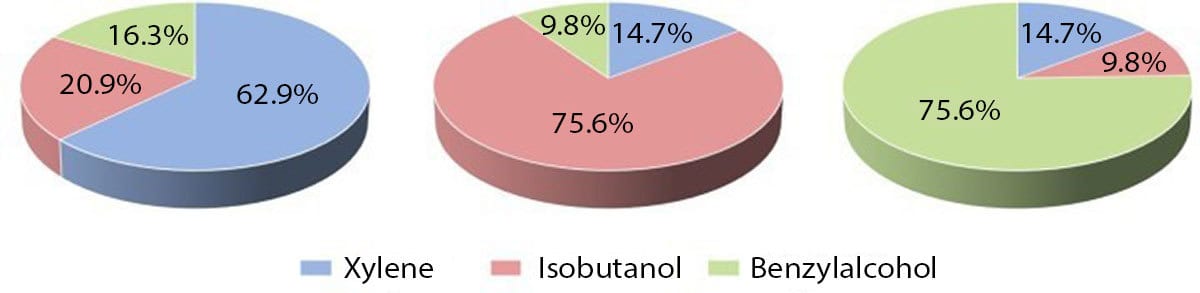
FIGURE 4 ǀ Solvent blends used in test system.
A comparison of the rheological characteristics was done 24 hours after manufacturing. The data visualized in Figure 5 show the performance of both organic thixotropes in the systems equipped with described various solvent compositions, with a special focus on the low-shear viscosity. The small graph in the upper right corner displays the viscosity variations of the alcohol-rich samples to the sample in the xylene-dominated system.
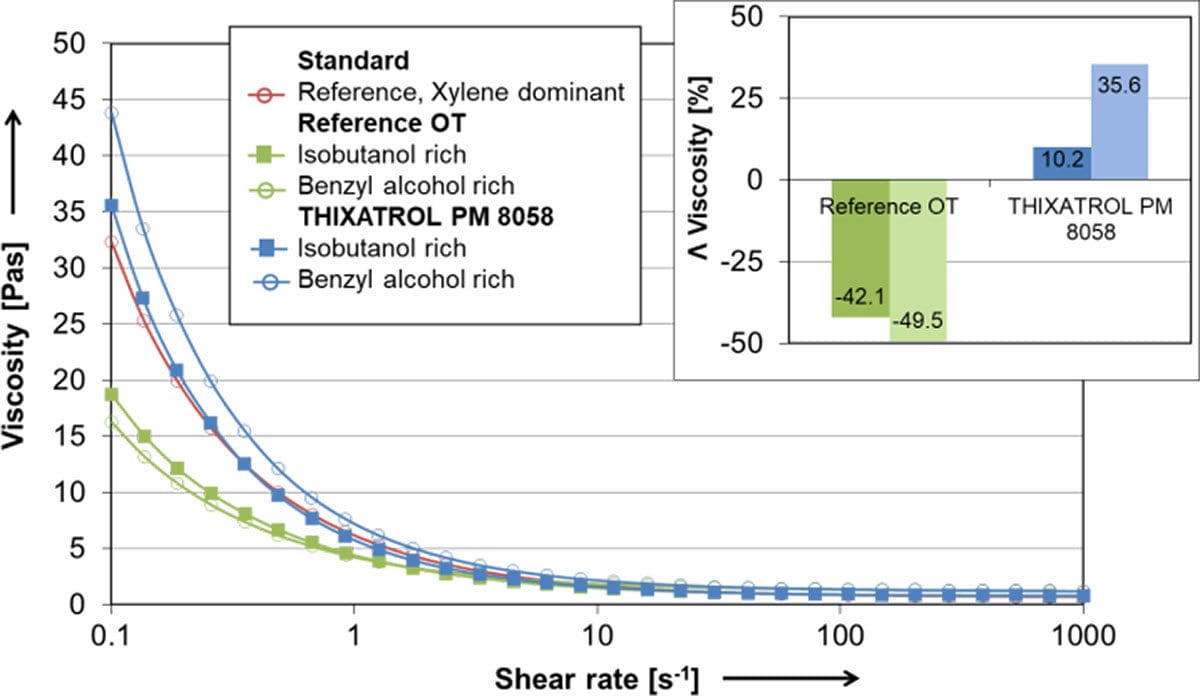
FIGURE 5 ǀ Influence of solvent blends on viscosity build.
It is obvious that the reference thickener significantly lost viscosity at low shear rates when formulated in both alcohol-rich systems. A different picture was observed when THIXATROL PM 8058 was utilized in the same range of systems. Contrary to the market reference product, a viscosity rise in comparison to the reference product was observed. This is especially the case when benzyl alcohol was dominant in the formulation. In the systems dominated by isobutanol, the difference was with a plus of about 10% somewhat lower.
The viscoelastic characteristics of the tested coating, generated in a structure recovery test, also underline the benefits of THIXATROL PM 8058. To simulate the post-application behavior, the structure of the coating was disrupted in a rotational measuring step by a high shear rate of 1,000 s-1. In a second, oscillatory step, the behavior after the removal of initially applied shear analyzes the properties of the coating after impacting the substrate. This is shown in Figure 6.
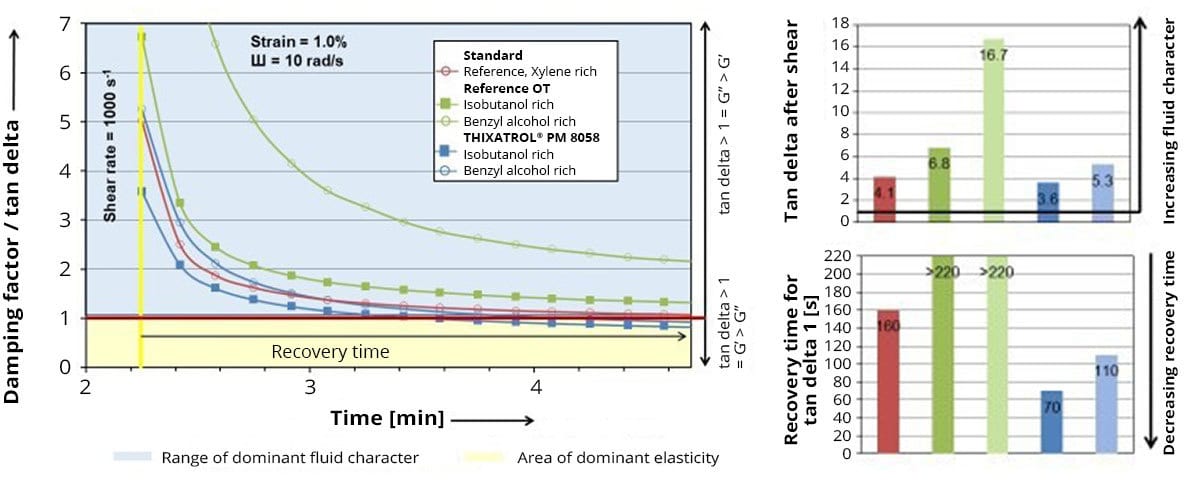
FIGURE 6 ǀ Influence of solvent blends on viscoelasticity.
When the damping factor (also called the tan delta value) is above 1, the fluid behavior of the sample is dominant and indicates that practically no structure is relevant, and the system flows. If the damping factor is below 1, the elastic behavior of the sample is dominant and indicates the presence of an internal structure. A strong structure indicates excellent sag stability and should consequently correlate with the results generated in practice.
However, in this testing the time behavior also played a major role. The faster the structure recovered, indicated by the crossing of the tan delta value of 1 coming from a higher level, the lower the time window for eventual sagging.
It can be seen in Figure 6 that all samples displayed a dominance of the fluid character, indicated by tan delta values of above 1, directly after shear removal.
With the reference organic thixotrope, a strong influence of the various solvent compositions on the viscoelasticity were observed. Directly after shear removal, both alcohols shifted the characteristics strongly towards a further fluid-dominated behavior. With respect to the time scale, no redomination of the elasticity could be detected. The effects were strongest with a dominant concentration of benzyl alcohol.
The influence of the various alcohols on the sample with THIXATROL PM 8058 was different. The absolute damping factors only slightly differed in comparison to the reference sample in the standard, xylene-dominated system. The main difference is the point in time when tan delta crossed the line of a value of 1. This structure recovery time in both alcohol-dominated systems was somewhat shorter. As a consequence, these data make potentially higher layer thicknesses expected after application of coatings with THIXATROL PM 8058 than with the reference rheology modifier.
In order to identify the optimum activation temperature window, the xylene-dominated system was chosen (Figure 7). In this study, individual samples were equipped either with THIXATROL PM 8058 or a reference thickener activated at individual temperature.
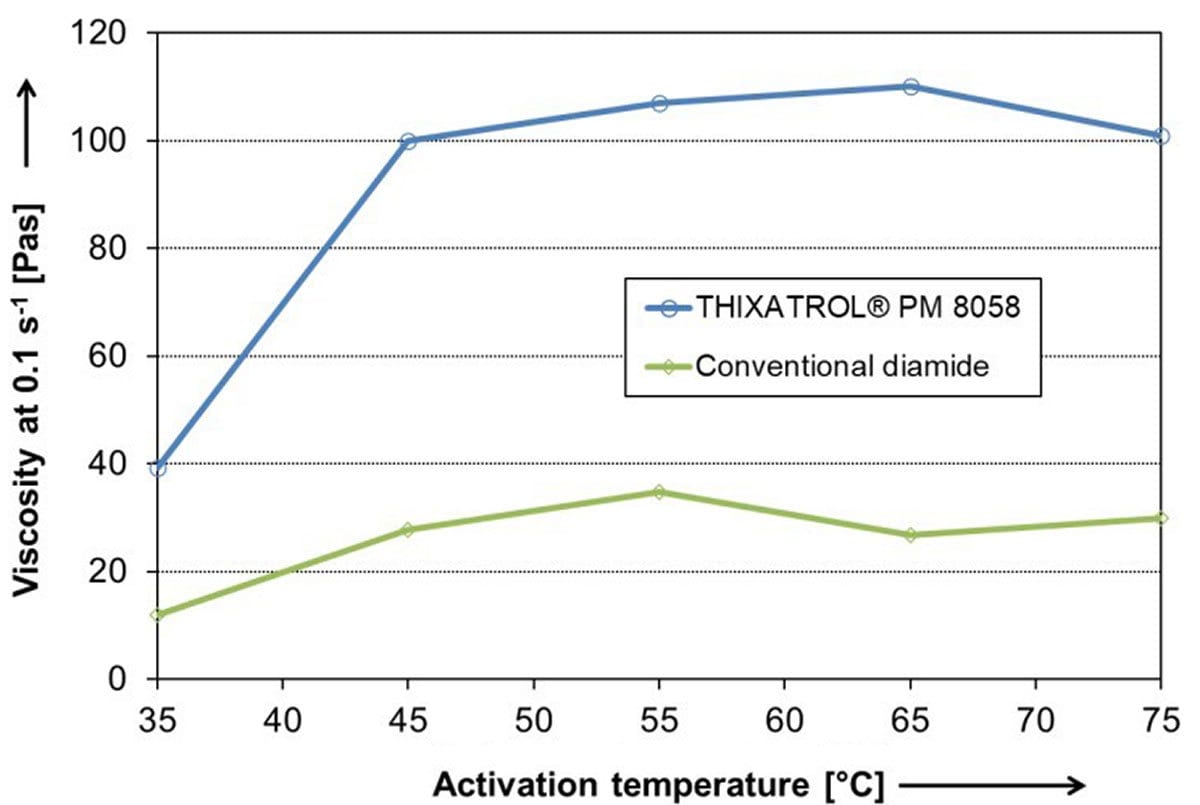
FIGURE 7 ǀ Viscosity build/activation temperature.
We observed that THIXATROL PM 8058 provided significantly higher viscosities at a shear rate of 0.1 s-1 than the reference product over the entire tested temperature range from 35 to 75 °C. Stable and predictable viscosity build with this product was obtained in a temperature range between 45 and 75 °C.
The influence on the activation time at various temperatures on viscosity build and sag control of THIXATROL PM 8058 is shown in Figure 8.
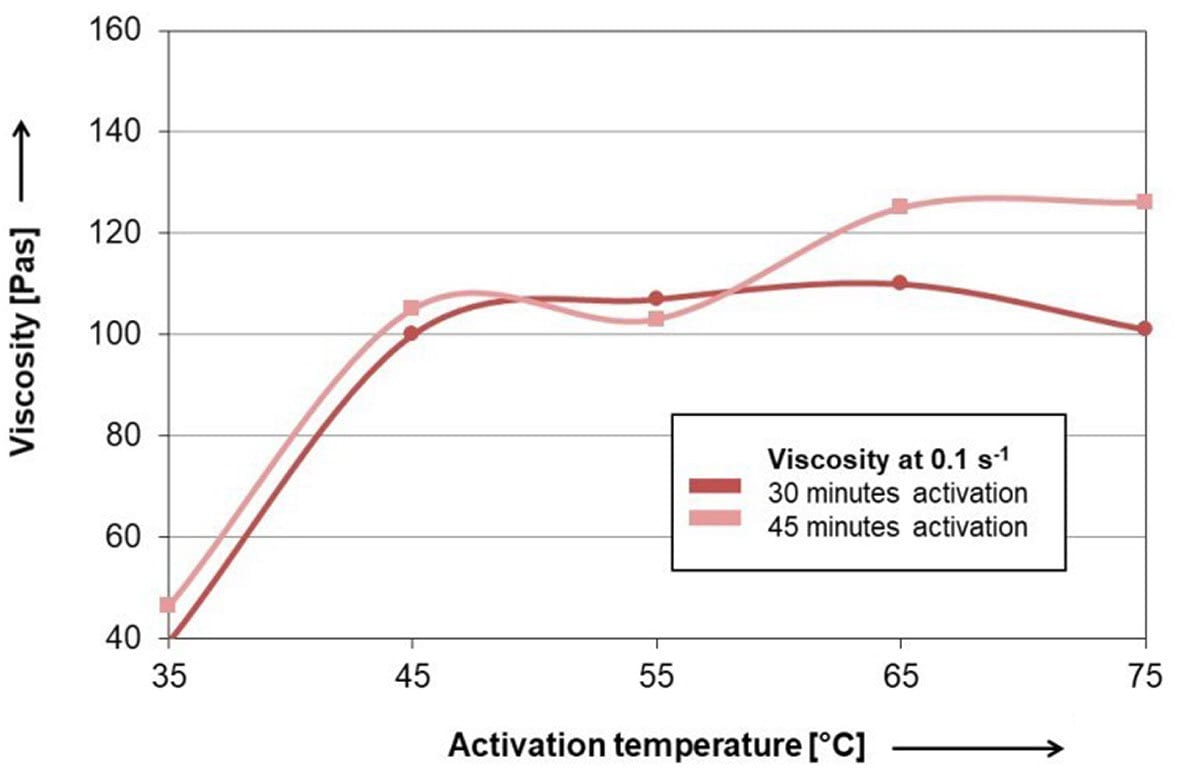
FIGURE 8 ǀ Influence of activation time.
Results confirm the wide activation temperature window. Excellent viscosity build at low shear of 0.1 s-1 could be detected with 30 minutes dispersing time at the lowest activation temperature of 35 °C. The most stable values were obtained in a temperature range from 45 °C up to 75 °C, and could be repeated. In this range, an activation time of 30 minutes is sufficient for proper viscosities. An extension of the activation period to 45 minutes generates a further slight increase in performance.
Also, in terms of stability, after 4 weeks of storage at an elevated temperature of 50 °C, THIXATROL PM 8058 provided excellent results. Figure 9 shows that only when activated at 35 °C were noticeable changes in the viscosity or the sagging stability observed. With an activation temperature of 45 °C, only a slight variation of the viscosity could be detected. In the case of sagging control, no changes at all were seen.
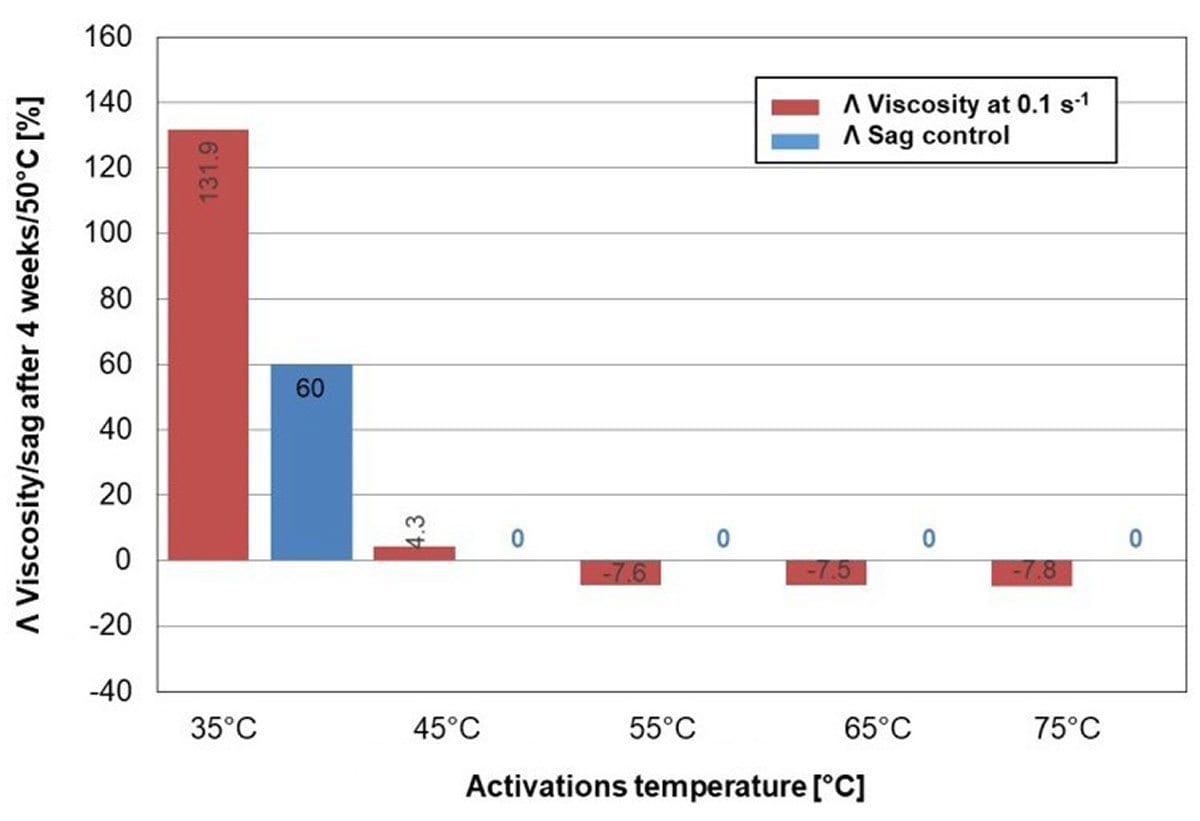
FIGURE 9 ǀ Storage stability.
Comparing the achievable maximum applicable layer thicknesses after application by airless spray, Figure 10 shows that THIXATROL PM 8058 clearly outperforms the reference rheology modifier. The market reference organic thixotrope allows a maximum layer thickness of 300 µm. THIXATROL PM 8058, formulated at equal concentration and activation conditions, guarantees sag control up to a range of 500-700 µm.
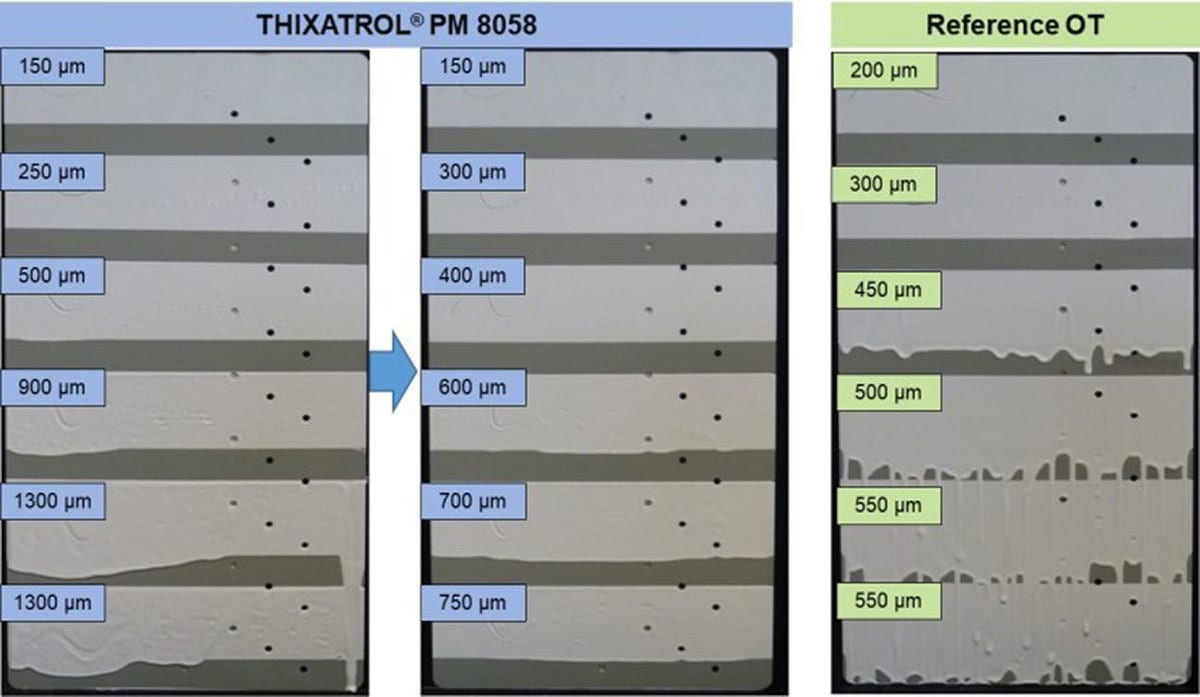
FIGURE 10 ǀ Sag stability after spray application.
The investigation of various processing conditions has shown that the activation of THIXATROL PM 8058 can be successfully performed by various methods (Figure 11). The best results were achieved when the product was added to the grind process at the beginning of manufacturing, or alternatively, in a readily formulated, but unthickened coating system. In the latter case, to avoid material squirting out from the vessel, the applied shear cannot be as high as with the grind activation.
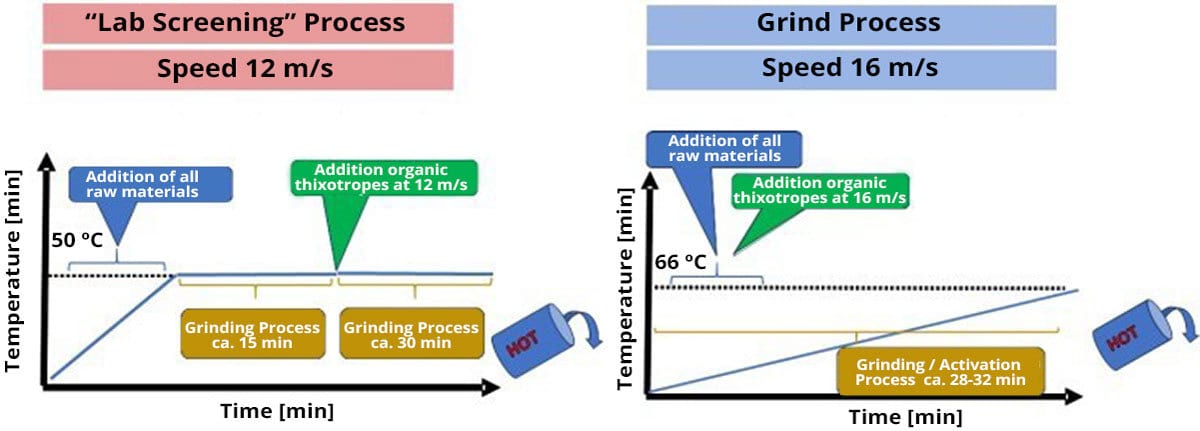
FIGURE 11 ǀ Recommended processing methods.
In post addition, a dissolver tip speed of 12 m/s should be used. The relevant activation temperature needs to be controlled externally. With direct addition, 16 m/s or even higher tip speeds can be used. Also, no artificial temperature control needs to be done, as the friction is high enough to generate the required energy.
Adding the organic thixotrope to the mill base has mostly been performed in factory-based production. Post activation offers additional options, e.g. a time-efficient lab screening.
Due to the low shear requirements of THIXATROL PM 8058 for activation, it might also be possible to create pre-gels in certain solvents or solvent/resin blends that can then be further used in coatings processing.
Conclusion
The discussed results and properties show that THIXATROL PM 8058 extends the series of efficient organic thixotropes. It utilizes the latest technology of highly sustainable diamide waxes, being based on more than 75% renewable raw material.
THIXATROL PM 8058 can withstand higher amounts of various alcohols and other highly polar solvents, and clearly outperforms other thickener classes. In comparison to other amide-based rheology modifiers, even higher viscosities and sagging stabilities can be achieved when compared to similar formulation conditions.
This product also provides a wide activation temperature window for very robust manufacturing under real-life conditions.
Further, it is storage stable when processed at lower temperatures for limited dispersing times. Short activation periods of 30 minutes provide viscosity-stable coatings systems. Additionally, the potential activation temperature starts at low levels. At 45 °C, a significant and stable viscosity build, as well as excellent sagging stability, were noticed. A further rise in activation temperature (up to 75 °C) at equal dispersion period resulted in only small variations.
In comparison to commercially available reference organic thixotropes, THIXATROL PM 8058 acts significantly higher in efficiency. This allows formulators to significantly reduce the loading level while keeping viscosity and sag control.
Consequently, THIXATROL PM 8058 is an ideal rheology modifier in the cost-effective and sustainable formulation of industrial, marine and protective coatings as well as other non-aqueous systems.
Test Methods
Rheology Measurements
Rheology was determined using the Anton-Paar MCR 301 rheometer, equipped with PP 50 measuring geometry at a gap width of 1 mm, at a temperature of 23 °C. In the case of the oscillatory, amplitude sweep data showed a fixed angular frequency of 10 rad/s was pre-adjusted.
Spray Application Conditions
The coating was applied airless by Grace XForce HD in stripes (1-6 spray passes) in order to obtain various layer thicknesses. Curing of the samples was done in a vertical position.