Ready to proof -- Clare 6/7/21
Corrections sent to Clare on 6/8
CLJ Revised 6/9
KJ sent revised corrections on 6/10
CLJ Revised 6/10
Ready for author
Photo courtesy of shuttersock.
Antimicrobial Paints and Coatings
In recent times, people have become more aware that everyday products can be affected by microbes such as bacteria and mold that can cause odors, staining and material degradation. In response, demand for products containing integrated antimicrobial additives, which significantly reduce the growth of a wide range of microbes, has increased. PCI asked Jennifer Collier, Partner Development Manager of BioCote® about antimicrobial paints and coatings, and their benefits.
Watch PCI’s recent interview with BioCote.
PCI: How do you make a paint or coating antimicrobial? How does the technology work?
Collier: An antimicrobial* paint or coating is created by integrating antimicrobial additives directly into the product during manufacturing. The additives, which we supply as a concentrated powder, a liquid suspension or as masterbatch pellets (depending on the type of product being treated and its end use, and the production process), are formulated by harnessing the properties of antimicrobial materials, or ‘active ingredients’.
The antimicrobial active ingredient generally used in paints and coatings is silver ion — it’s well proven, offers excellent efficacy and is suitable for use in all types of paints and coatings in a wide range of applications.
Once an additive has been integrated, the paint or coating becomes antimicrobial, providing permanent, homogenous protection for the paint or coating against the growth of a wide range of microbes, including bacteria and mold, which can cause odors, staining and material degradation — providing the product itself is not compromised.
Antimicrobial additives work by making surfaces inhospitable to microbes, by causing, for example, protein, cell membrane and oxidative damage, or through DNA interference. Our technology can reduce the number of microbes on protected paints and coatings by up to 86 percent in just 15 minutes, and by up to 99.5 percent in two hours. The antimicrobial technology will work continuously for the expected lifetime of the paint or coating; it does not wear out or wash off.
PCI: What benefits do antimicrobial paints and coatings offer?
Collier: Once integrated into a paint or coating, antimicrobial additives will permanently prevent the growth of microbes that can cause negative effects such as odors, staining or material degradation, meaning surfaces become easier to keep clean. It’s important to understand that antimicrobial technology is designed to protect the product alongside stringent cleaning regimes; it should never be regarded as a substitute for these practices or good hand hygiene procedures.
PCI: Can the technology be applied to any type of paint or coating, and is there any impact on the finish, etc.?
Collier: Antimicrobial additives can be easily and cost-effectively manufactured into all types of paints and coatings, whether solvent-, oil- or water-based, liquid, powder, ink, lacquer or varnish, and whether used internally or externally. We formulate our additives to suit the type of paint or coating being treated, but also the material it may be applied to, the environment it is designed for, the production process in place and any specific manufacturer and end customer requirements.
The color and finish of the paint or coating won’t be affected, and the way it needs to be applied won’t change either. Furthermore, since antimicrobial additives reduce staining, unpleasant odors and premature material degradation, a product’s usable lifetime can, in some cases, be extended compared to an unprotected product, increasing sustainability.
PCI: Is demand increasing, and why?
Collier: Yes, most definitely — our sales have been rising over several years and our business has gone from strength to strength thanks to our fantastic customer base. We are now living in a more hygiene-conscious world, and an increased focus on cleanliness and a heightened awareness of microbes has led people to regularly sanitize their hands, the surfaces they touch and the products that surround them. In addition, more manufacturers are integrating antimicrobial additives — the practice of protecting products against the growth of microbes that cause issues such as odors, staining and material degradation to bolster cleaning regimes is certainly becoming more popular.
And, according to a report from Grand View Research, the increased demand is set to continue for many years; the global antimicrobial coatings market is expected to grow at a compound annual growth rate of 12.8 percent from 2020 to 2027.
PCI: How is an antimicrobial paint or coating verified/classified as such? What tests are carried out?
Collier: Once additives are formulated, we carry out stringent quality control tests and checks on matters such as particle size, moisture content, visual appearance and active substance concentration, as required for the specific chemical. Once they pass this process, the additives are then sent to the customer to manufacture them into their products. Following this, the customer will send their treated paint or coating to us for analysis at an independent laboratory, so we can ensure the product is delivering the required levels of efficacy. Microbiologists will measure and validate the product’s antimicrobial performance using the appropriate certified test method.
We also give customers the option of including fluorescent chemical markers (taggants) in their paint or coating, achieved by using special additives. Although invisible to the naked eye, taggants can be identified with a detector that will verify the presence of additives — this can help end users to better understand what is being achieved.
BioCote is also the only antimicrobial additive supplier in the world to be certified by leading food science organization Hazard Analysis Critical Control Point International. This means the antimicrobial technology we supply, and the quality processes around it, have been formally verified as ‘fit for purpose’ and safe for manufacture into food-contact surfaces.
PCI: Which partner businesses do you work with in the U.S.? Which sectors do they operate in, and how are their antimicrobial paints and coatings used?
Collier: Our three main U.S. coatings partners are AkzoNobel U.S., Cardinal and Powder Technology Inc. (PTI). The powder coatings produced by all three companies have been tested according to ISO 22196, and their efficacy rate against microbes that could affect the product has been shown to be over 99 percent.
AzkoNobel’s coatings protect and decorate some of the most famous buildings and stadiums in the world, as well as residential properties, technology, vehicle components, metal furniture and household appliances. The company partnered with us to expand its Interpon brand, creating the Interpon AM and Interpon D AM antimicrobial powder coating ranges — the latter adding extra functionality for architects and specifiers and being suitable for internal and external surfaces.
Meanwhile, Cardinal offers a wide range of liquid and powder coating systems developed to meet and exceed demanding performance and emission standards. Its specialty is creating attractive industrial coatings that can withstand daily wear and tear. By working with BioCote, Cardinal has developed liquid and powder antimicrobial industrial coatings that provide high-performance protection to a wide range of applications and environments, including aerospace, transportation, architectural and medical.
PTI specializes in collaborating with OEMs and has customers in virtually every industry, including aerospace, medical, ATV and motorsports, garage/race cabinets, outdoor furniture, power generation, transportation and ACE, and also offers U.S. Military-approved CARC coatings. The company introduced BioCote antimicrobial technology to its powder coatings, which are used on a variety of items such as lockers, handrails, appliances, food preparation and storage equipment, office and cafeteria furniture, playground equipment, park benches, bus stops, medical beds and laboratory equipment. PTI also formulates coatings with taggants — the fluorescent chemical markers mentioned earlier.
PCI: What do you think the future holds for the antimicrobial paints and coatings industry?
Collier: Our sales over the last year — and the projects we have in the pipeline — certainly support the growth forecast outlined in the Grand View Research report. We are making changes to our business so we can adapt and meet the anticipated increase in demand. We’ve already expanded our headcount by 30 percent and have doubled our production capacity on certain product offerings, for example.
And, with antimicrobial paints and coatings in such high demand — and for so many different applications — the technology is unlikely to stand still. We have been developing new and exciting antimicrobial additives to deliver new features and benefits for our customers.
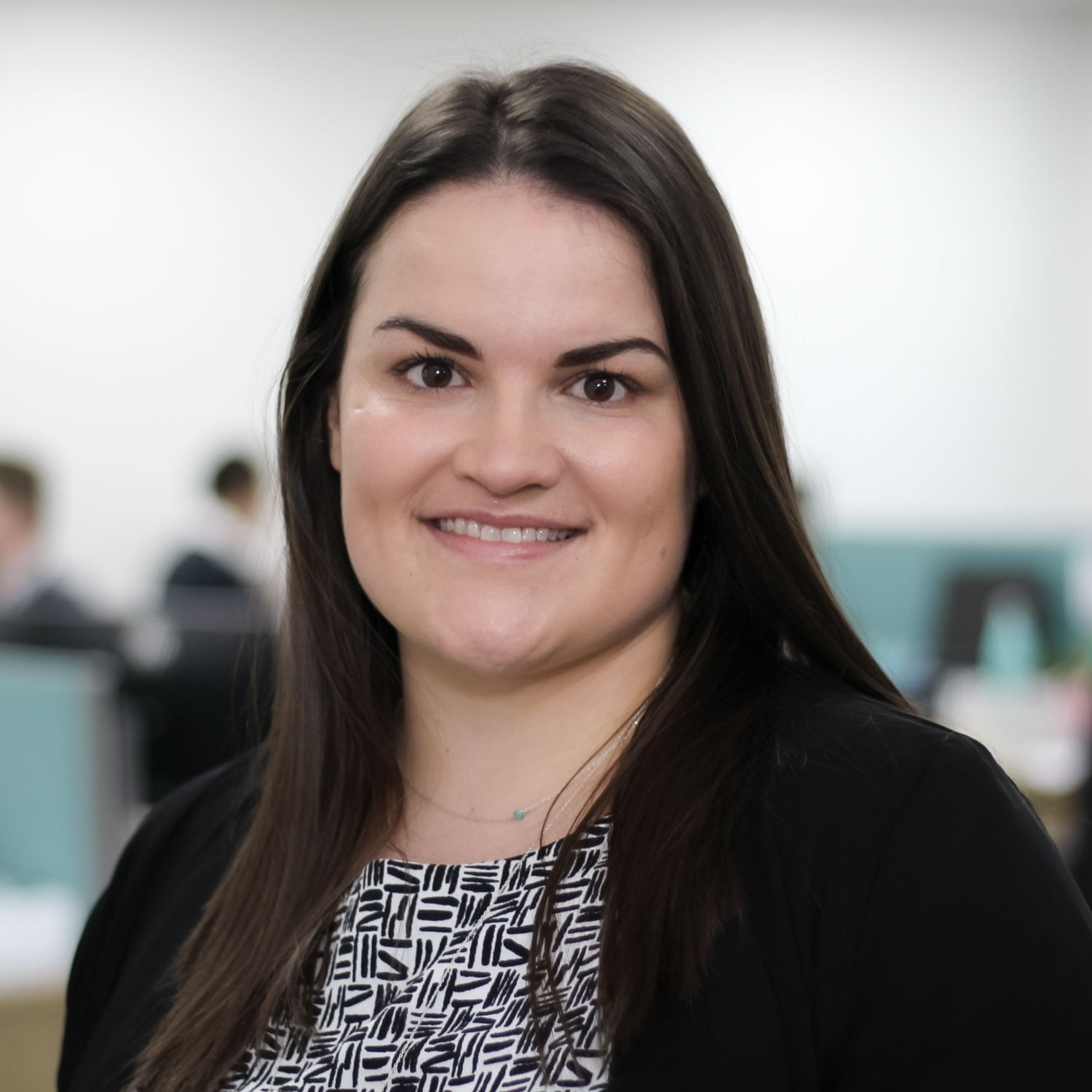
Jennifer Collier
*BioCote technology does not protect users or others against disease-causing bacteria, germs, viruses or other harmful organisms. This technology is not a substitute for good hygiene and/or cleaning practices.