Ready to proof -- Clare 6/4/21
KJ sent corrections to Clare on 6/8
CLJ Revised 6/9
KJ sent revised corrections on 6/10
CLJ Revised 6/10
Ready for author
KJ sent revised file to author on 6/14
Clean
FORMULATING WITH MIKE
Introduction to Additives
Part 2
Video: SoraPhotography, Creatas Video+ / Getty Images Plus, via Getty Images
Top Photo:Davizro, iStock / Getty Images Plus, via Getty Images
By Mike Praw, Senior Applications Scientist – Paints, Coatings and Inks,
Indorama Ventures: Integrated Oxides and Derivatives, The Woodlands, TX
This is the second in a series of four articles on additives. Rheology modifiers and suspension agents were covered in Part 1, which published in our May 2021 issue. Part 2 covers foam control agents.
Additives are used in small quantities and usually have the highest unit cost of coatings raw materials. They are used to facilitate production or to improve certain properties of the wet coating or the final film. They are absolutely necessary in paint; however, more is not better. In fact, with many additives higher levels can hurt performance.
Foam Control Agents
A pure liquid will not foam. However, we do not deal with pure liquids, so fighting foam is a reality in a coating’s formulation. Foam is a dispersion of a large volume of a gas (usually air) in a liquid. Foam control agents include defoamers, anti-foams and air release agents (deaerators). Each of these foam control agents is different, but the terms are often used interchangeably. A defoamer is designed to break foam at the liquid surface. An anti-foam prevents foam from forming. A deaerator is designed to get the foam (usually micro foam) out of the bulk liquid, and have it move to the surface so the defoamer can then take care of it. While there is this distinction, all foam control agents will normally defoam, deaerate and work as an anti-foam agent, but will have a greater effect on one of the three. Formulators usually use a combination of these for optimum performance across all types of foam. Often defoaming additives contain a combination of defoamers, deaerators and anti-foams, and will accomplish all three. In this article, the word defoamer will be used for all three phenomena.
So, what causes foam? The leading cause of foam stabilization is the presence of surfactants in the coating. Surfactants are added to aid in pigment dispersion, stabilize the resin emulsion or lower surface tension (to aid in flow and leveling or substrate wetting). Other raw materials such as rheology modifiers or resins with a high surface tension can also stabilize foam by trapping the air bubbles and preventing them from moving to the surface or allowing the bubbles to break. Air bubble and raw material interactions may also slow, or in extreme cases, stop air bubbles from leaving the bulk liquid.
Foam will rise to the surface based on the formula derived from Stokes law (covered in the last article), and is simplified to (assuming the same viscosity):
Velocity of the foam rising =
Size of the bubble x Density difference between the gas and liquid
Viscosity of the liquid
Since viscosity and density differences are difficult to adjust without significantly changing the coating, increasing the bubbles’ size increases the rate the bubbles leave the bulk liquid. This is where deaerators come into play. The deaerator is incompatible in the system (air bubble and bulk liquid) and reduces the surface tension of the air bubble. The bubbles interact, coalesce, and the larger bubbles rise to the surface. Figure 1 shows this process.

FIGURE 1 ǀ The deaeration process.
In most cases of foam stabilization, surfactants stabilize the lamella (thin layer of liquid around the gas bubble in the liquid or at the surface) by forming an electrical double charge layer. This layer is maintained by osmotic pressure; as the layer is formed or expanded, there is a concentration gradient between the coating system and the surfactants. If the layer starts getting thinner due to liquid draining away, the concentration gradient forces more liquid into the lamella, stabilizing it. The key to destabilizing foam is to destabilize the lamella. In the bulk liquid this gradient prevents small bubbles joining into larger ones, which would rise to the surface faster, while at the surface of the liquid it prevents the bubbles from bursting and releasing the gas. A lamella is stable if the cohesive forces of the lamella are stronger than the outward force on the lamella from the gas pressure inside the bubble. Figures 2 and 3 show a lamella and gas stabilization from surfactants. Figure 2 highlights foam stabilization in the bulk liquid, and Figure 3 illustrates the stabilization of foam at the surface (air/liquid interface).
FIGURE 3 ǀ Air bubble stabilization at the surface of a liquid.
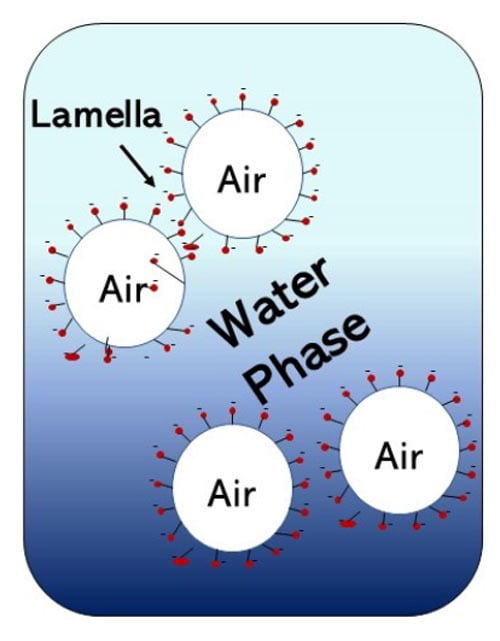
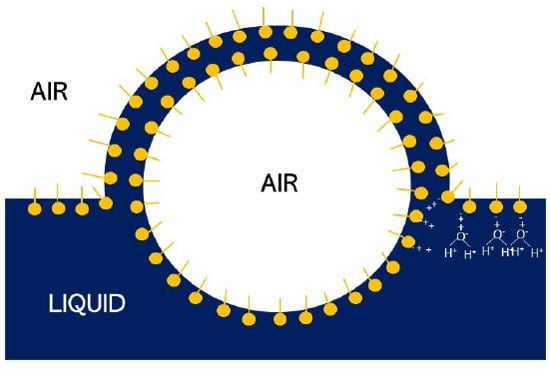
FIGURE 2 ǀ Lamella stabilization in a liquid.
So how does one destabilize the lamella? The standard way is to interfere with the surfactant double layer. A defoamer will do this by displacing the surfactant, lowering the surface tension or dewetting the liquid, so the lamella becomes too thin and the gas pressure ruptures the bubble.
A good defoamer will:
Be insoluble in the formulation/coating media;
Have a low surface tension;
Have a high penetration coefficient of the defoaming actives;
Have a high spreading coefficient of the carrier;
Have a dewetting mechanism.
The mechanism of defoaming has three steps:
Entering – the defoaming agent enters the lamella.
Spreading – The anti-foam agent spreads through the lamella and breaks the surfactant double layer.
Rupture of the lamella – Internal gas pressure ruptures the lamella and the bubble bursts (Figure 4).
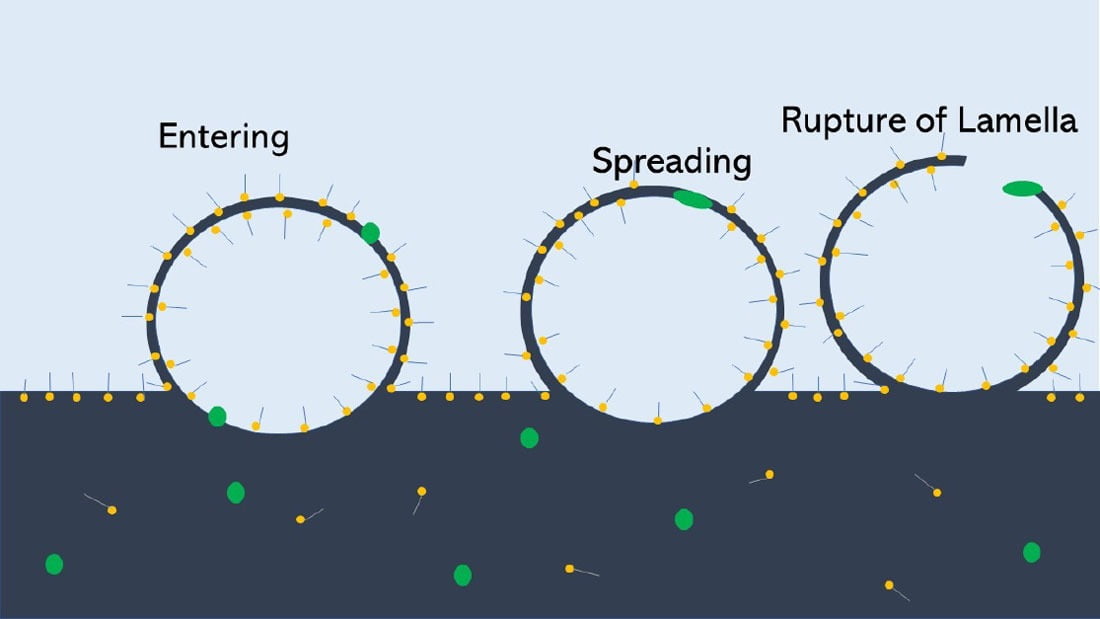
FIGURE 4 ǀ Stages of breaking the lamella.
Defoamer Composition
The composition of the defoamer is critical for the defoamer to be successful. Defoamers can have up to three different components. Defoamers have a primary liquid or carrier. They can have emulsifiers and wetting agents, as well as possibly having tertiary components.
The primary liquid serves as a defoamer and acts as a carrier for other active components such as hydrophobic particles. It must be insoluble in the coating solvent (including water) and components of the coating. If it is soluble, it will not act as discrete particles and break the lamella. It must have a lower surface tension than the coating system but have a higher interfacial tension to remain discrete particles. Examples for a water-based system include mineral oil, silicone oil, hydrophobic glycols and other organic hydrophobic liquids.
Emulsifiers and wetting agents control the degree of emulsification of the defoamer. The degree of emulsification affects the efficiency, persistence and compatibility of the defoamer. If it is too incompatible with the coating, it will lead to particles that are too large, making an inefficient defoamer, not allowing it to enter the lamella, and can also cause surface defects. If it makes the defoamer too compatible, defoaming efficiency will suffer. The rate of entering the lamella and spreading to weaken the lamella enough to break is dependent on the surface tension of the defoamer and the interfacial tension of the defoamer and the coating system.
Tertiary components include ingredients that can boost activity, increase product stability and alter compatibility of the defoamer. They include hydrophobic solids (such as waxes), fatty acids, coupling agents as well as many other chemistries.
Defoamer Compatibility
Compatibility is the crucial factor for a defoamer. Compatibility is a term used for a combination of properties of the defoamer that determine the final particle size of the defoamer in the coating and how efficient it is at breaking the bubbles. If it is too compatible, you will not get adequate spreading in the lamella, and the bubble will not break. If you are too incompatible, the defoamer particles may join, leading to few large particles that will not efficiently break bubbles. The shear you subject the defoamer to is critical when choosing your defoamer. The higher the shear, the greater the incompatibility needed since you will be emulsifying the defoamer more. Therefore, you need a very incompatible defoamer for the grind stage, while you need a much more compatible one for the letdown. Figure 5 shows the effect on foam by moving from a more compatible to incompatible defoamer.
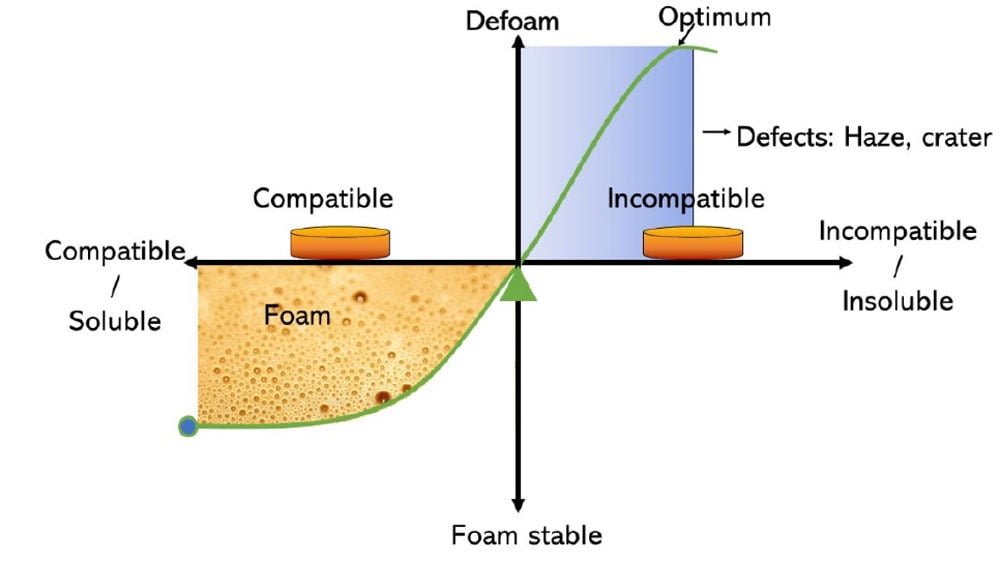
FIGURE 5 ǀ Compatible/incompatible balance.
Persistence and efficiency are two very different properties of the defoamer. The efficiency is based on how well it breaks bubbles (usually measured when you make the coating). The persistence is how the defoamer will hold up to time. If the defoamer has an interaction with the coating over time, it may lose its efficiency. One possible cause is polymer interactions that lead to partial coalescence and the larger polymer particles that do not need as much surfactant. This extra surfactant can cause the defoamer particles to become more compatible, and efficiency drops. There are too many possible interactions to mention here, but it is important to do stability studies on defoamer efficiency in your coating.
Mechanisms of Defoaming
One common mistake formulators make is to use one defoaming package for all systems. While purchasing and plant employees like the efficiency, simplicity and cost savings of this, every system is different in its nature, and your system may not be efficient or persistent enough.
There are several different mechanisms of defoaming, depending on the defoamer composition. The first is incompatible solids. In water-based systems, these solids would be hydrophobic. In this type of mechanism, small, incompatible solid particles enter the lamella, displace the surfactant and disrupt the double layer. The hydrophobic moiety of the surfactant is attracted to the hydrophobic nature of the solid particles. Figure 6 shows this.
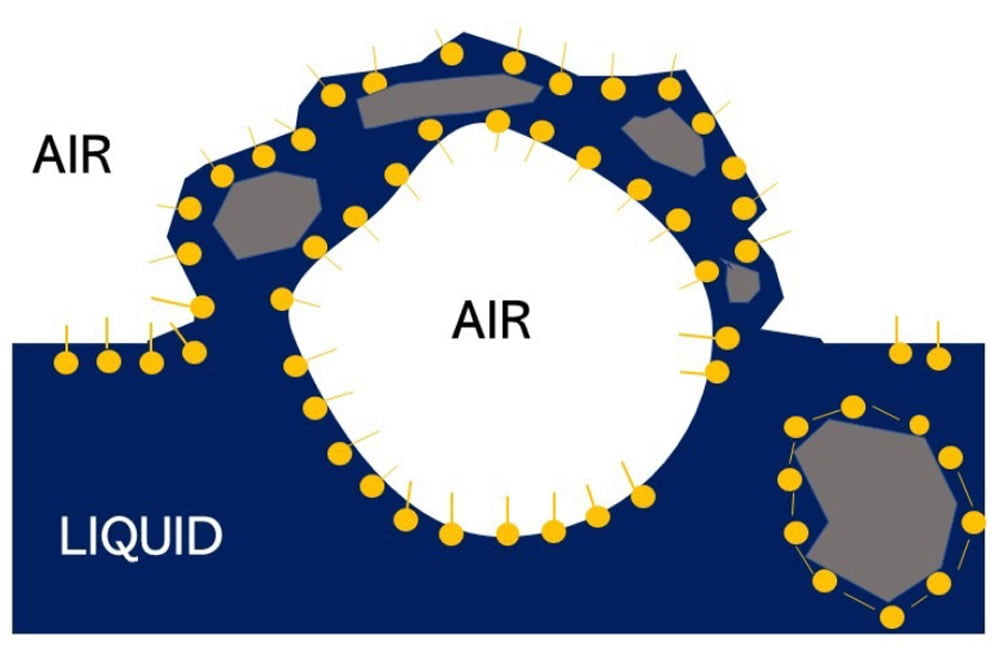
FIGURE 6 ǀ Incompatible solid mechanism.
Another mechanism of defoaming is the competition for surfactant. In this case, a surfactant-starved liquid species is added and it scavenges free surfactant. With less free surfactant, you do not get the double layer stabilization of the lamella. This tends to be more of an anti-foam and deaeration method of not stabilizing foam in the first place than an actual defoaming mechanism. Figure 7 depicts this mechanism. Also note that adding too much of this type of defoamer can strip surfactant off the resin emulsion and destabilize the resin.
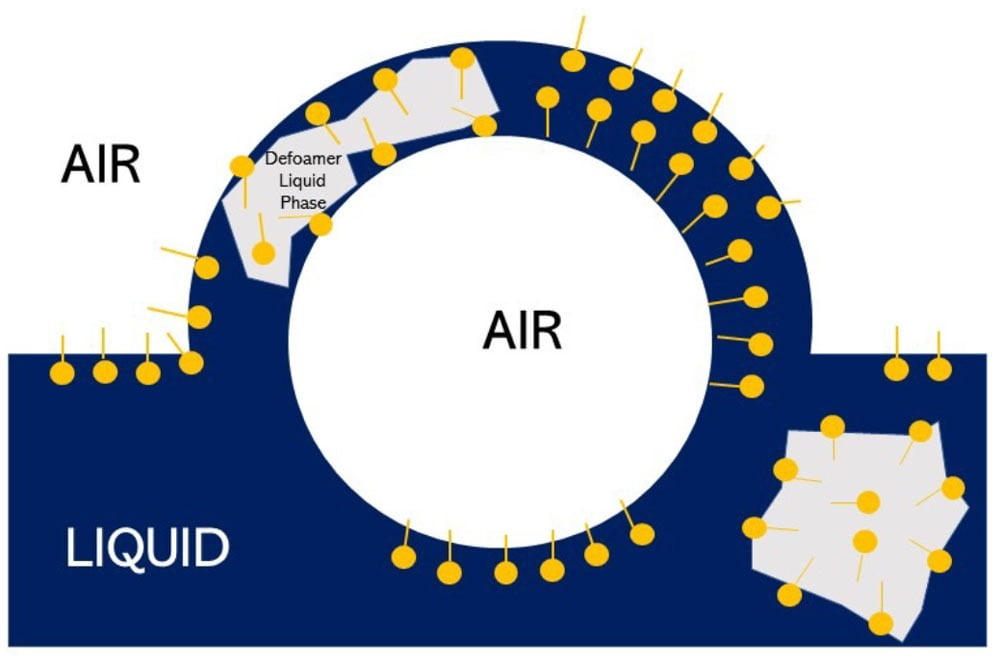
FIGURE 7 ǀ Competition for surfactant defoaming mechanism.
An alternative method is the use of an antagonistic surfactant. In this mechanism, a surfactant, which is significantly different than other surfactants in the system, is added to the coating. Due to the nature of this surfactant, a double layer may form but it is weak and does not stabilize foam. Figure 8 shows this.
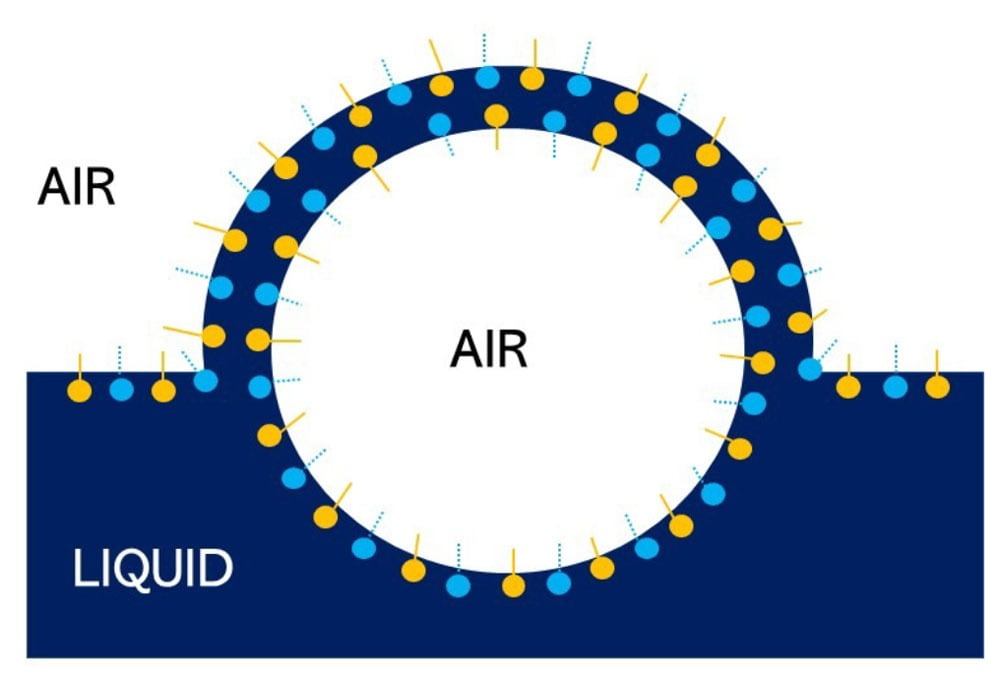
FIGURE 8 ǀ Antagonistic surfactant defoaming method.
The last main mechanism of defoaming is the incompatible, low-surface-tension mechanism. In this mechanism an incompatible, low-surface-tension liquid is added to the coating. It is dispersed into tiny hydrophobic droplets in a water-based system. The droplets are drawn into the lamella where they spread out, creating a weak spot and the bubble bursts. This is highlighted in Figure 4 as spreading.
Other Critical Factors
How dispersible the defoamer is can be a critical issue. Lower dispersible defoamers will have greater persistence and be better for high-shear applications. They will have a larger particle size and can lead to surface defects (craters and fisheyes). Dispersible defoamers are more compatible and better for high-gloss/high-distinctness-of-image coatings, and reduce film defects and increase colorant acceptance. They do have poorer persistence and should not be used in coatings with long shelf lives.
The order of addition is critical for defoamers. In the grind stage, they should be added before the pigments to minimize foaming. In the letdown, they should be added at the end to minimize any shear since they are much more compatible and less shear stable than the grind defoamers.
A lot of defoaming agents will contain secondary particles that are not dissolved. These defoamers tend to settle out or stratify, therefore agitation before use is critical. I have seen too many cases where a defoamer is taken from a drum and the coating has issues. In most cases the hydrophobic particles settle out, so the coatings made from the top part of the drum have foaming issues, while you see a lot of surface defects in coatings made from the bottom of the drum. Even clear defoamers can stratify if the liquids are not 100% compatible. To avoid these issues, always adequately agitate defoamers before use.
Questions to Ask Before Selecting a Defoamer
When will it be added — grind, letdown or post add?
Will it be exposed to high or low shear?
Will it be used in a tint base?
Are certain chemistries not allowed, for example silicon in automotive coatings?
What level of persistence is needed?
Are minor film defects an issue?
Do they increase volatile organic compounds or are they hazardous air pollutants?
Will they affect other properties (UV, chemical or corrosion resistance)?
Often a combination of defoamers will work better than just one. I have also seen synergistic effects of multiple defoamers. The performance of a defoamer system will vary from system to system due to the variety of other raw materials used. The key to efficient defoamer use is to properly incorporate it. You need a good distribution of active substances throughout the system for proper defoaming, without over dispersing them.
Formulating Considerations
One thing to consider for defoamer dosage is the variability of the raw materials. Resin emulsions may vary from batch to batch, moving the paint system from surfactant starved to a very high degree of free surfactant. Pigment dispersions are the same, but variabilities in dispersion efficiency and primary particle size will lead to different levels of free dispersant. Just formulating with extra defoamer is not an option, as surface defects can result. The best option is to have a foam test in quality control to test for initial defoamer level (persistence cannot be tested this way). Often a brush slap test or roller roll out is used as a quick verification, but other tests are also used.
The next thing to consider is the balance of grind defoamer to let down defoamer. If you use too little grind defoamer, air bubbles will form. Since air compresses significantly easier than liquid, the shear forces on the pigment will be reduced and grind efficiency will suffer. This leads to longer grind times and more heat generation, which can damage the components in the grind phase (defoamer, pigment dispersant, etc.). If you use too much grind defoamer, you can end up with surface defects or other issues, which can only be solved by using additional additives, which can lead to an additive death spiral.
Since defoamers are by their very nature incompatible with the system, they have a tendency to reform larger drops over time. This will lead to a decrease in both efficiency and persistence once the particle size of the defoamer moves out of the optimum defoamer particle size range. Too large a defoamer size may prevent it from being able to enter the lamella and burst the air bubble. The larger particle size may also cause surface defects such as fisheyes or craters. Too small a particle size and you may not disrupt the lamella enough to break the bubble.
Another issue is over shear of the defoamer. If too compatible a defoamer is used in high-shear conditions like grinding the pigment or high-shear application, the particle size of the defoamer may become too small to be effective. Therefore, choosing a defoamer that matches shear conditions is critical.
The higher the viscosity of the system, the more difficult it is to defoam. The higher viscosity will trap air and prevent it from moving to the liquid surface and will also slow liquid entering the lamella. Reduction of flow into the lamella will reduce the possibility of a defoamer particle entering the lamella and bursting the bubble in the desirable time frame.
Another major consideration is how long it takes to defoam the system. Do you need it to be foam free in 30 seconds, 30 minutes or 30 hours?
Purchasing often classifies different raw materials as offsets and can order either one. While being functional offsets in what they were designed to do (for example pigment dispersant), and chemically similar, they are not identical and can change other properties in the coating. Even if they are chemically identical, production variability at the plant level on how they are made can lead to differences in your coating. It is important to test all the different offsets in your formula when determining the defoamer package.
These are just some things to consider when trying to formulate your coating, and they will require a different balance of defoamers to be both efficient and persistent. The optimum balance of grind to letdown defoamer will not only increase the production efficiency of the product, but it will also decrease overall additive use, lowering the total cost.
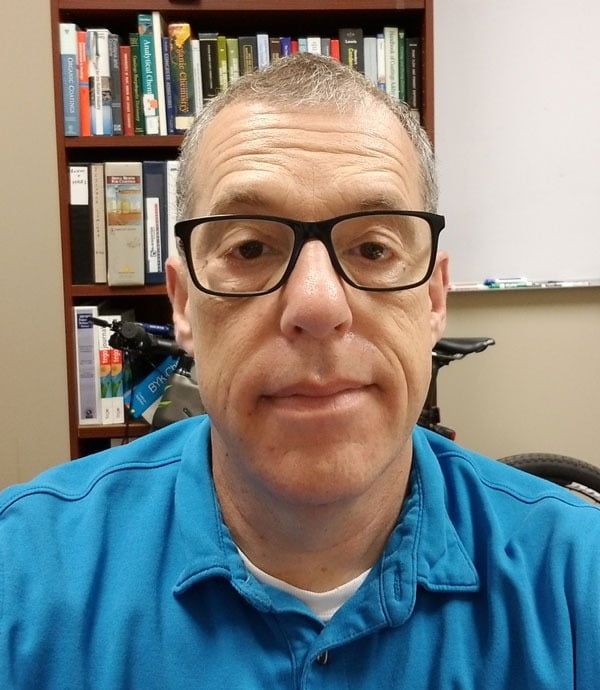
Mike Praw
Author’s Bio:
Born and raised in Montreal, Mike now lives in the Houston area. He has 34 years of coatings formulation experience, 18 years with coatings companies and 16 years with raw material suppliers. He is currently Senior Applications Scientist – Paints, Coatings and Inks, for Indorama Ventures: Integrated Oxides and Derivatives. He has degrees in Analytical Chemistry and Environmental Sciences, as well as a MBA. Mike is the Past President for The Detroit Society for Coatings Technology and The Piedmont Society for Coatings Technology, and served on the board of the Chicago Society for Coatings Technology. Mike is a Canadian Armed Forces veteran, having served 15 years in the Canadian Infantry.
All information contained herein is provided "as is" without any warranties, express or implied, and under no circumstances shall the author or Indorama be liable for any damages of any nature whatsoever resulting from the use or reliance upon such information. Nothing contained in this publication should be construed as a license under any intellectual property right of any entity, or as a suggestion, recommendation, or authorization to take any action that would infringe any patent. The term "Indorama" is used herein for convenience only, and refers to Indorama Ventures Oxides LLC, its direct and indirect affiliates, and their employees, officers and directors.