Ready to proof -- Clare 5-5-21
KJ sent corrections to Clare - 5/10/21
CLJ Revised - 5/11/21
KJ sent new correction on 5/11
CLJ Revised - 5/11
Ready for author
Sent to author
KJ sent new Figure 1 to Clare on 6/14
CLJ Revised - 6/14
KJ sent revised proof to author on 6/14
Clean
Novel Path to Hydroxyl-Functional Emulsions
For High-Performance Waterborne Two-Component Polyurethane Coatings
Photo: onurdongel, iStock / Getty Images Plus, via Getty Images
By Marcelo Herszenhaut, Market Development Manager Americas, Versatics, Hexion Inc., USA; Steven Mao, Technical Manager, Versatics APAC, Hexion Management (Shanghai) Co. Ltd., China; Scott Wang, Senior
Technical Service Specialist, Versatics APAC, Hexion Management (Shanghai) Co. Ltd.; and David Vanaken, Global Technical and Marketing Director, Versatics, Hexion Research Belgium SA, Belgium
The global demand for waterborne (WB) industrial coatings continues to increase to meet more and more stringent VOC legislation and heightened awareness of environmental stewardship.1,2 Because of their lower environmental footprint, waterborne epoxy resins, acrylic polyol (APO) dispersions and hydroxyl-functional (OH-functional) emulsions are gaining market share in high-performance, two-component (2K) industrial coating applications. While waterborne epoxy resins are cured with a variety of amines, APOs and OH-functional emulsions are crosslinked with diverse WB isocyanates. Compared to APO dispersions, OH-functional acrylic emulsions offer lower cost and an easier production route, in addition to faster drying and property development. OH-functional acrylic emulsions can be designed with a wide range of hydroxyl values and performance characteristics to address the needs of many different applications in plastic, wood, automotive, and construction coatings.
Needs and Trends in the Coatings Industry
We highlight a few recurring needs in the coatings industry, each of them generating its specific set of trends:
Sustainability and Lower VOC Requirements, which lead to:
Higher solids in solventborne (SB) systems as a first step to increase environmental compliance. This trend has led to the development and adoption of various commercial solutions.1,2
Enhancement of the performance of waterborne coatings. Current WB systems already address many of the requirements of high-performance industrial applications, as reflected by their wider use.1,2
Productivity, as a measure of sustainability. While the production of SB systems has been streamlined by centuries of practice, the production of industrial WB systems may, sometimes, require additional or cumbrsome steps. This can lead to increased energy consumption per unit of protected substrate, longer process times or additional process steps. The solution presented in this article addresses those topics.
Excellent Performance
Although users are aware of environmental needs and demanding of action from their suppliers, they also require performance comparable to classic SB coatings. Some of the basic performance requirements are:
Appearance (gloss and flow, and the ability to control coating gloss);
Chemical resistance (to water, acids and alkalis, or solvents specific to the application in sight);
Hardness;
Weathering resistance.
Globalization of Technologies
Both global resin suppliers and global coatings producers seek solutions that can be easily used in various geographies. This relates to resins that are easily produced in more readily available equipment and that are less sensitive to coating formulation techniques and practices.
Controlled Cost
Much like in the case of performance, mentioned above, end users may not accept a premium for high-performance WB coatings. Thus, both the resin chemist and the coatings formulator must look for alternatives that deliver lower environmental impact and better performance at a reasonable cost.
Taking Advantage of a Highly Versatile Family of Building Blocks
In the 1950s, Dr. Herbert Koch from the Max Plank Institute in Mülheim, Germany, found that olefins react with carbon monoxide and water under the influence of strong acids to form tertiary, highly branched neocarboxylic acids (Figure 1).3,4

FIGURE 1 ǀ Koch reaction to produce neo-acids.
These neocarboxylic acids can be converted to their glycidyl esters by reaction with epichlorohydrin. Versatic™ Acid 10 (VA10), a neocarboxylic acid with 10 carbon atoms, is converted into Cardura™ E10P glycidyl ester (CE10P) via this route. In turn, the reaction of CE10P with acrylic acid generates Acrylated CE10P (ACE) (Figure 2).
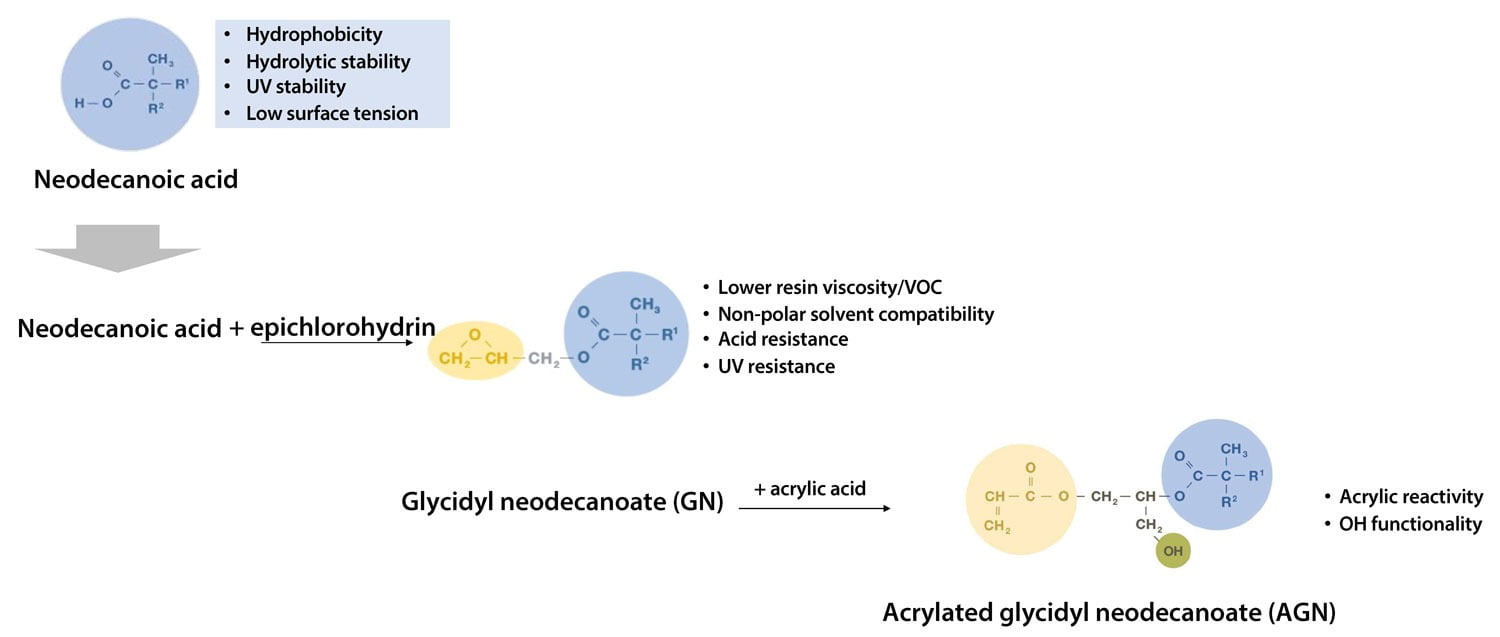
FIGURE 2 ǀ Structure of CE10P glycidyl ester and its adduct with acrylic acid.
ACE is a highly versatile molecule, containing an acrylic unsaturation, OH functionality (mostly primary), and a very hydrophobic and highly branched tertiary substituted structure. The acrylic functionality is used to incorporate ACE into polymers through reaction with other unsaturated monomers, the OH group can be used for crosslinking with isocyanates, and the branched alkyl chain from VA10 imparts outstanding performance characteristics.
Building WB 2K PU Systems
WB 2K PU systems are based on (A) an OH-functional resin (the clear majority with an acrylic backbone) or a mixture of such resins and (B) an isocyanate or a mixture of isocyanates. We will address here the (A) component.
Figure 3 shows the logical evolution in the technologies developed to produce OH-functional WB APO resins to be crosslinked with isocyanates.

FIGURE 3 ǀ Building resins for WB 2K PU systems
APO resin solutions are based on polymers with relatively short chains and high acid values. To deliver sufficiently low molecular weights, special equipment or larger quantities of chain-transfer agents may be required. After the polymerization step, the acid groups are neutralized with amines, and the resin is dissolved in water. However, this technology still requires the use of high quantities of co-solvent to ensure full solubility of the resin in water. Furthermore, the high concentration of acid groups may negatively affect performance of the cured coating. Figure 4 displays the relative acid value ranges for the technologies shown in Figure 3.
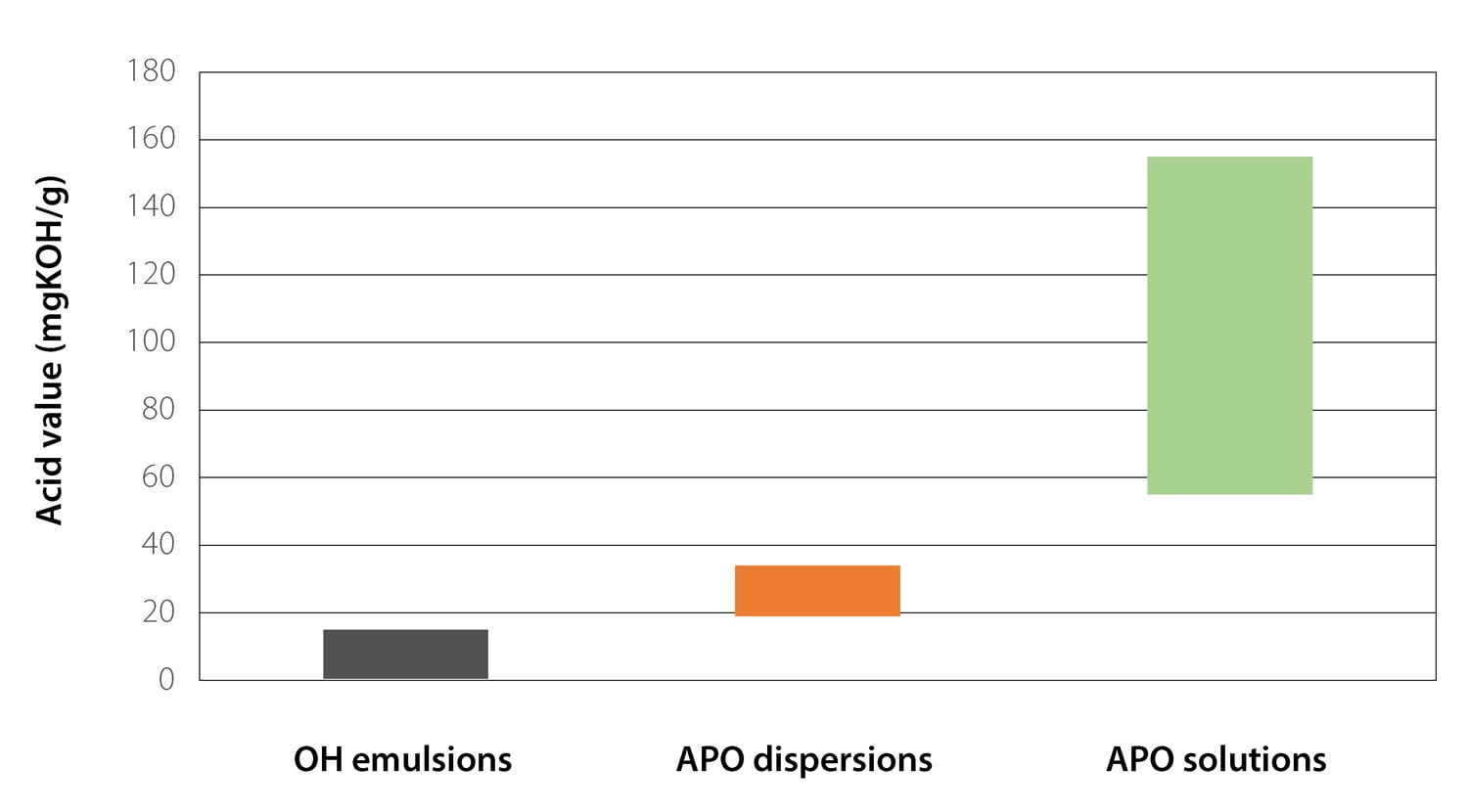
FIGURE 4 ǀ Relative ranges of acid values for various WB APO technologies
Waterborne APOs are typically prepared via conventional radical polymerization in solvent, much like their solventborne analogues (Figure 5). Waterborne APOs differ from solventborne APOs in that they contain a certain quantity of acid monomer, such as acrylic or methacrylic acid, to impart anionic character to the polymer. After the polymer is synthesized, these acid groups are neutralized with an amine to bring water dispersibility. One disadvantage of polyols prepared via the conventional process is their solvent content. A significant amount of solvent is required as a medium for the polymerization process, and without additional processing steps, this solvent remains in the polymer. To reduce the solvent content of the polymer to an acceptable level, an energy- and time-intensive distillation step is required.
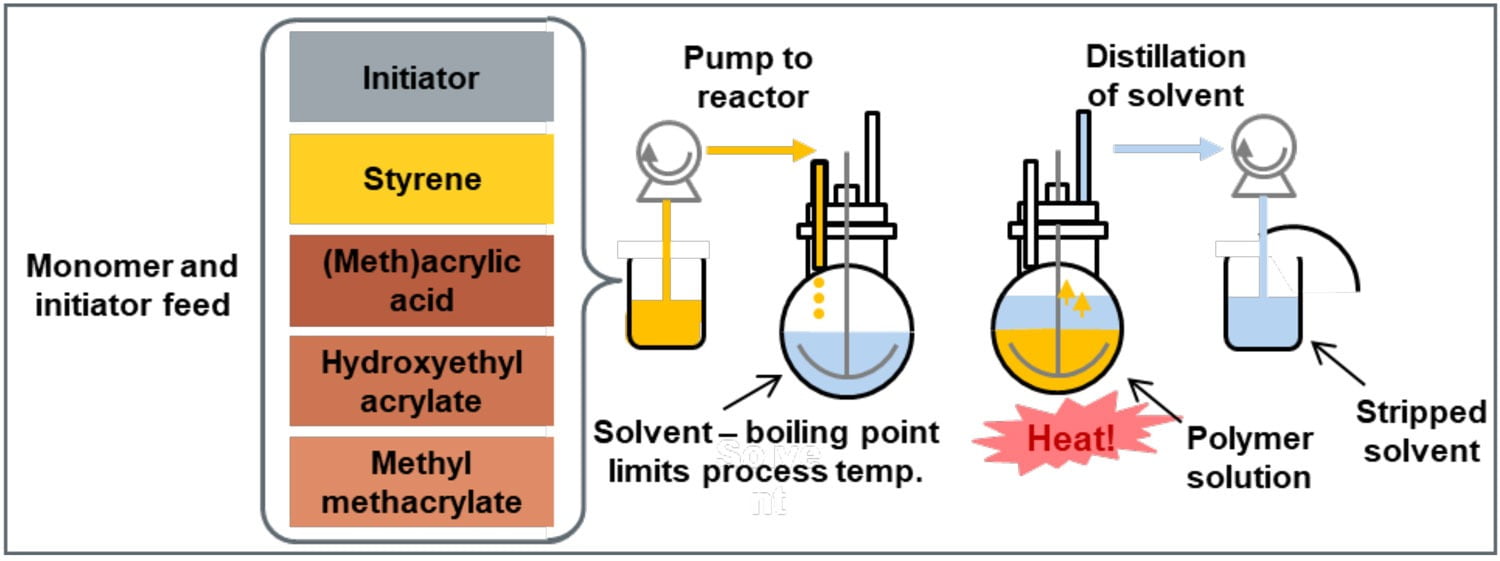
FIGURE 5 ǀ Synthesis of conventional WB APOs.
When used as a reactive medium for APO synthesis, CE10P replaces the solvent that would otherwise be used for polymerization. CE10P is gradually incorporated into the polymer backbone during the monomer feed step by the reaction of its epoxy functionality with acid groups contributed by acrylic or methacrylic acid present in the monomer feed. During this process, two reactions occur simultaneously: radical polymerization of the monomers and the epoxy-acid reaction, which incorporates the CE10P in the acrylic polyol.
The use of CE10P in the synthesis of acrylic polyol resins, both SB and WB, has been extensively discussed in the literature.5,6,7 This article will focus on the use of the acrylated adduct.
Primary vs. Secondary Dispersion
Figure 3 portrays OH-functional emulsions, a better form of WB APO technology. To address the question “why?” we will compare the two types of resins, evaluating the production process and chemical properties.
Process
As described above, secondary dispersions involve:
(1) polymerization (with or without solvent);
(2) neutralization of carboxylic acid groups;
(3) dispersion of the neutralized resin in water;
(4) An additional fourth step, solvent removal, may occur at different times, according to equipment and technology.
While steps (1) and (2) may be performed in the same vessel, step (3) will require high-shear mixing to ensure formation of a stable dispersion. This implies at least two vessels, in addition to the solvent removal train.
Emulsion polymerization is a simpler process, performed in a single vessel, itself with a rather simple design, does not require the use of solvents, rather using water as the polymerization medium, and can be performed at lower process temperatures than solventborne polymerization.
Chemistry
Secondary APO dispersions are stabilized via neutralized acid groups distributed along the molecular chains. This relatively high concentration of carboxylic acid groups may lead to issues during cure (interference with the isocyanate crosslinkers) and to moisture sensitivity of the cured films. Furthermore, to produce stable dispersions, such chains cannot be too long, and they usually have Mw values around 10,000 Da. Under similar cure conditions (catalyst and isocyanate concentration), these shorter chains exhibit slower cure response, because they fall short in properties from physical drying.
Emulsion polymerization can be equated to a multitude of parallel bulk reactions performed in nano-sized reactors (the polymer particles). Emulsions are stabilized with surfactants, and much higher Mw values are attained (upwards of 200,000 Da). Thus, once the emulsion-based coating has been applied and its film has coalesced, it will present physical properties before the onset of cure, solely because of the higher molecular weight. This will affect the apparent drying time and other characteristics, such as handling time.
Figure 6 summarizes these comparisons.
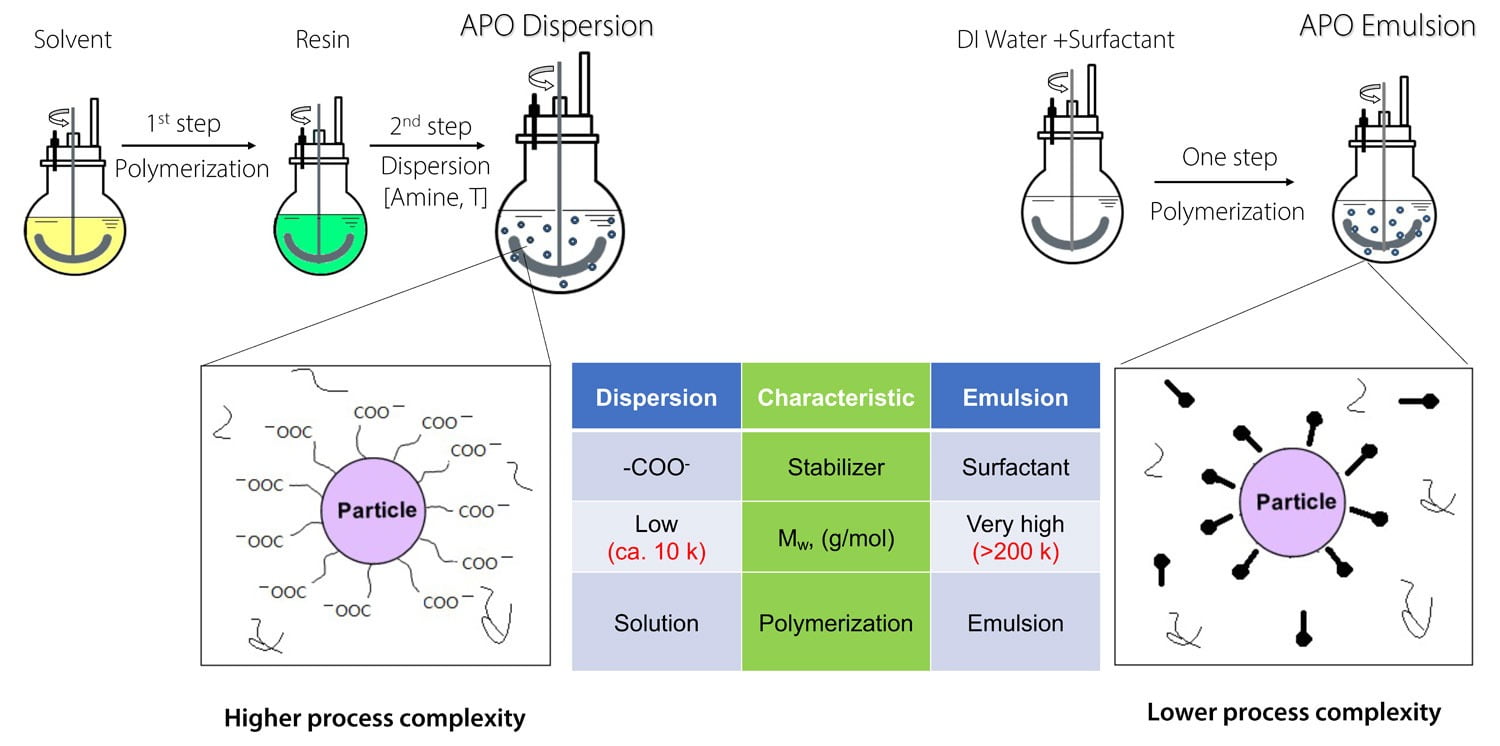
FIGURE 6 ǀ APO dispersions and APO emulsions – differences in synthesis and structure.
Novel OH-Functional Emulsions for High-Performance WB 2K PU Coatings
Having established the attractiveness of OH-functional emulsions for high-performance 2K PU coatings, we will now address some drawbacks of the current technology used to produce these emulsions and some unmet process and performance needs.
Most often, the source of OH functionality in these emulsions is HydroxyEthyl MethAcrylate monomer (HEMA). HEMA is a small, very polar molecule, and is readily miscible with water. HEMA’s solubility in water creates some process problems:
HEMA-rich monomer pre-emulsions tend to be less stable than those based on less soluble monomers;8,9
Once fed into the polymerization reactor, HEMA tends to more easily homopolymerize in the water phase (and not in the micelles). This leads to emulsions with higher grit formation and reduced HEMA concentration in the polymer micelles (HEMA does polymerize, albeit “in the wrong place”).
The use of ACE (Acrylated CE10P) as another source of OH functionality addresses both issues above. Since the solubility of ACE in water is negligible, it readily migrates to the organic micelles, carrying HEMA along. In doing that, ACE helps stabilize the polymer pre-emulsion and reduce grit formation. Figures 7 and 8 illustrate these benefits for an emulsion with 4.2 % OH on solids.
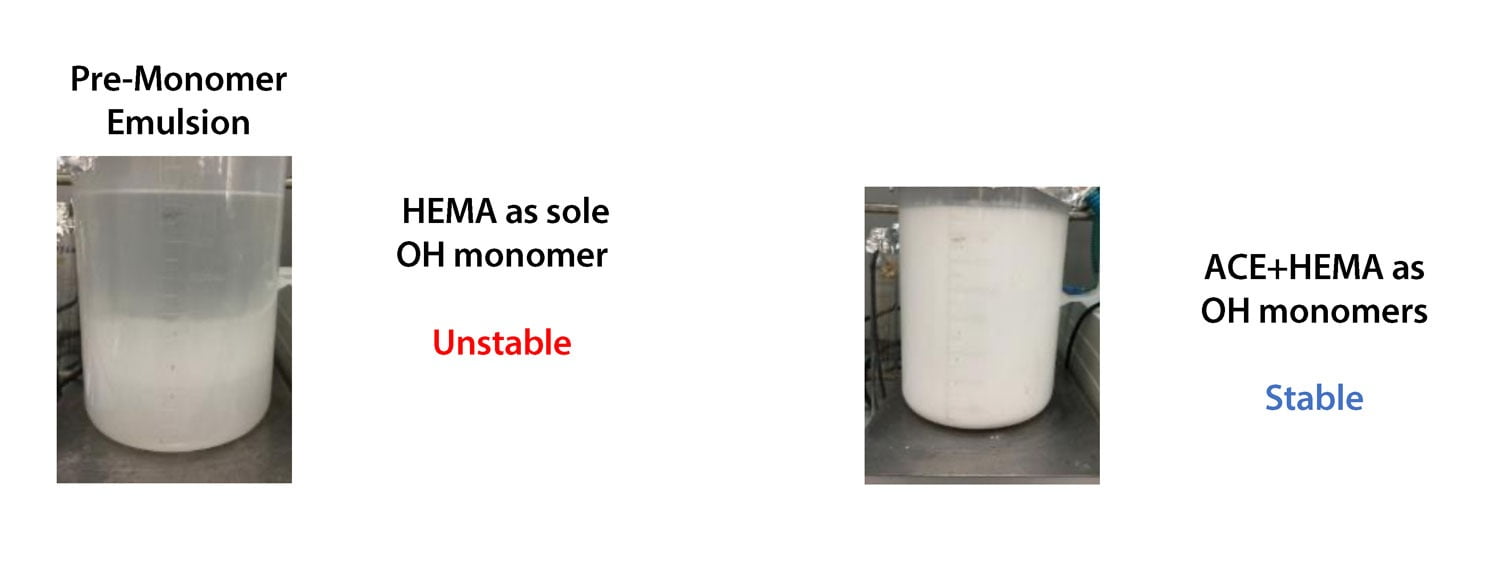
FIGURE 7 ǀ Increased monomer pre-emulsion stability with ACE.
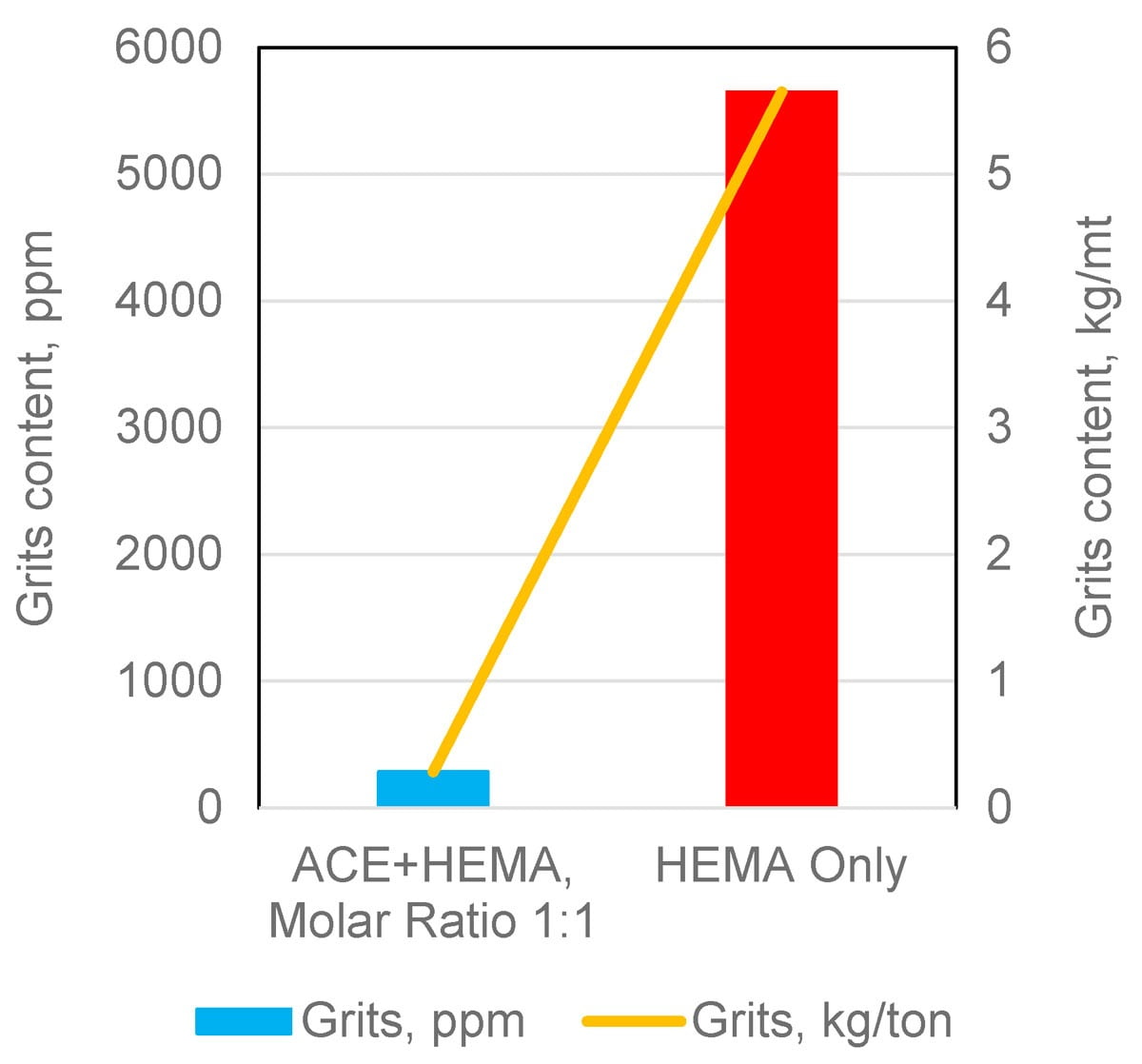
FIGURE 8 ǀ Reduced grit formation with ACE.
In addition to addressing process concerns, the use of ACE as a comonomer improves the emulsion polymer performance. As mentioned above, HEMA is extremely hydrophilic. Therefore, HEMA tends to stay on the surface of the polymer particles, either on the polymer backbone or in oligomer form. An emulsion that relies solely on HEMA as the source of OH functionality will thus have particles that will mostly crosslink on their surface. On the other hand, when ACE is used as a comonomer, it helps distribute OH groups inside the micelles, which leads to polymers with a more homogenous distribution of reactive OH groups. Thus, crosslinking occurs both inside and outside the polymer particles. This effect is shown in Figure 9.
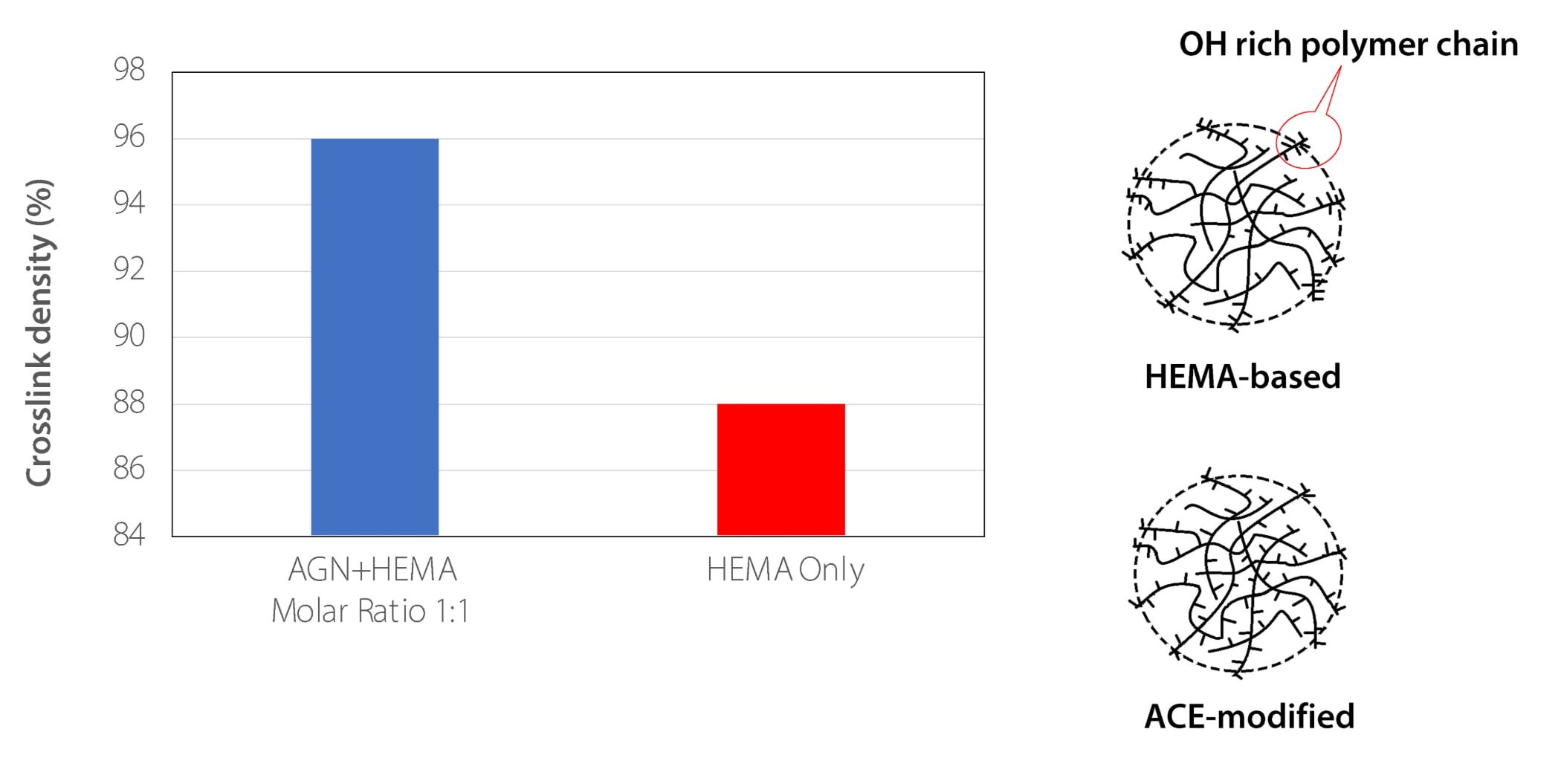
FIGURE 9 ǀ Improved crosslink density and functional group distribution when ACE is used.
Finally, one additional advantage of using ACE as a comonomer relates to compatibility with isocyanate crosslinkers. To properly cure, the emulsified resins must be compatible with the crosslinkers. Waterborne isocyanates are too viscous as supplied, so they are usually diluted with hydrophobic solvents (e.g. PMA). The very non-polar Versatate groups in ACE increase the compatibility of emulsified polymers with non-polar (hydrophobic) solvents. This results in better mixing of the crosslinkers and polymers, which, in turn, leads to improved properties of the cured films.
Figure 10 compares the properties of clear films, made one with a regular HEMA-only emulsion and one with a 50/50 mole HEMA/ACE monomer blend. In both cases, the OH content is 4% on solids. In addition to process benefits, the use of ACE as comonomer brings clear benefits to coating performance. Hexion has developed a toolbox to tailor polymer composition to the required performance, including drying speed.
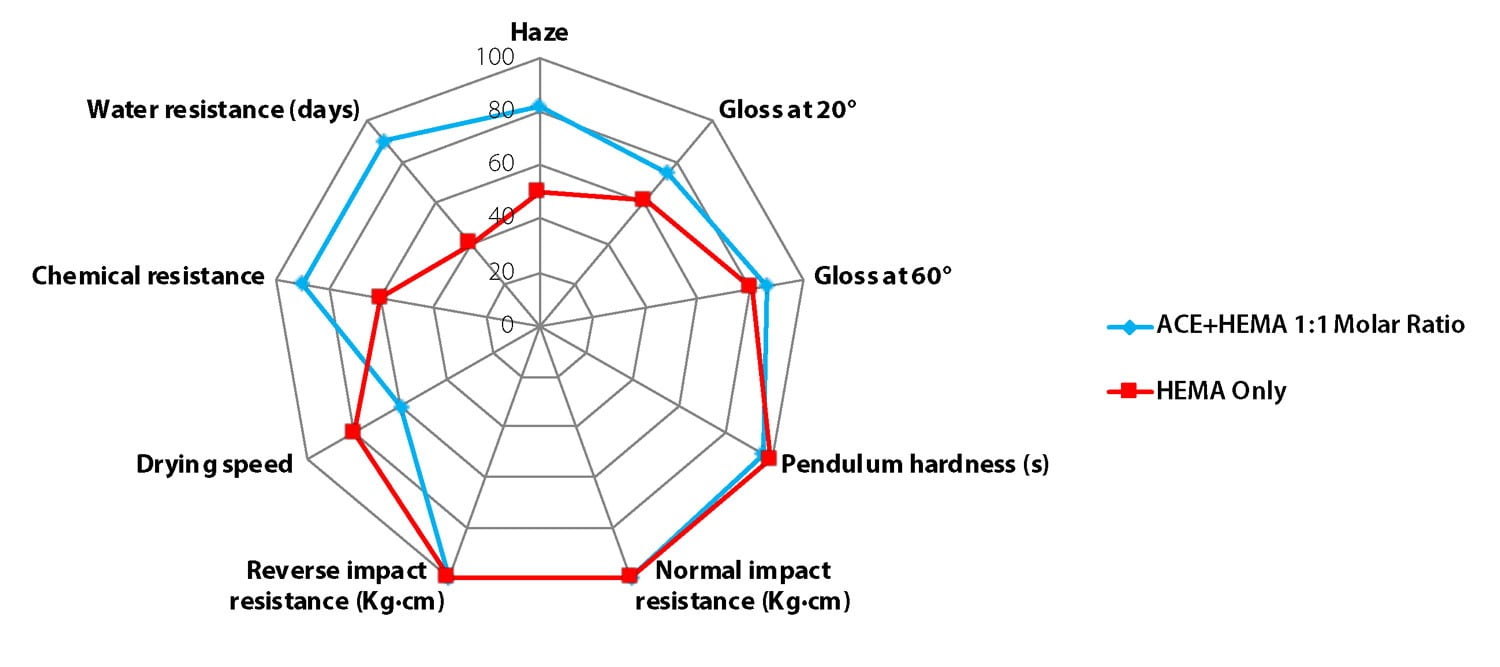
FIGURE 10 ǀ Comparison of cured film properties with and without ACE as comonomer (emulsion with 4% OH content).
Conclusion
The use of Acrylated Cardura E10P (ACE) as a comonomer with HEMA in the synthesis of OH-functional emulsions addresses issues observed when HEMA is used alone. Monomer pre-emulsions containing ACE will be more stable, and the process will generate less grit, reducing polymer losses. In addition, the hydrophobic nature of ACE ensures that the OH groups in the final polymer are evenly distributed within the polymer particles, not only on their surface, leading to better crosslinking. Furthermore, the hydrophobic nature of ACE improves miscibility of the isocyanates used for 2K WB PU coatings, resulting in better coating performance. Finally, performance properties of the emulsions based on ACE are improved over those without this monomer.
References
1 Kumar, V.; Bhattacharya, A. Demand for Low-VOC Coatings Continues to Rise, Paint & Coatings Industry, May 5, 2020.
2 Challener, C. Waterborne Industrial Coatings: Regulatory Changes Slowly Driving Shift to Waterborne, CoatingsTech, Vol. 14, n° 10, October 2017.
3 Koch, H. Production of Carboxylic Acids from Olefins, US patent 2,831,877, filed 17 March 1952.
4 Koch, H. Über Neuere Bei der Synthese Verzweigter Carbonsäuren Erzielte Ergebnisse, Fette, Seifen, Anstrichmittel, Vol 59, n°7, 493-498, 1957.
5 Steinbrecher, C.; Le Fevere, C.; Heymans, D. Hybridized Acrylic and Polyester Chemistries: High-Performance Polyols for Solventborne and Waterborne Polyurethane Topcoats, conference “Automotive Coatings”, 2011, Berlin, Germany.
6 Cavallin, C.; Yan, Z.; Vanaken, D.; Heymans, D. High Solids Acrylic and Polyester Polyols Made Easy: The Glycidyl Ester of Neodecanoic Acid Provides Performance and Competitiveness, ABRAFATI conference, 2015, São Paulo, Brazil.
7 Cavallin, C.; Herszenhaut, M. The Production of High-Performance Waterborne Acrylic Polyols Made Easy By the Use of Glycidyl Neodecanoate Technology, Coatings Trends and Technologies, 2016, Chicago, USA.
8 Zhang, C-Y; Zhu, Z-W; Gong, S-L. Synthesis of Stable High Hydroxyl Content Self-Emulsifying Waterborne Polyacrylate Emulsion, Journal of Applied Polymer Science, 2017, DOI: 10.1002/APP44844.
9 Zhang, F.; Wang, Y.; Yuan, L.; Chai, C. Synthesis of Acrylic Emulsion Containing High Hydroxyl Content, Journal of Macromolecular Science, Part A, Volume 41, 2001, issue 1, 15-27.