Ready to proof — CLJ 6/16/22
KJ proofed on 6/16
Ready for author
75 Years in Coatings: A Historic Look at the Coating Industry’s Evolution
By Melissa Molitor, Vice President, Marketing, Carboline (a subsidiary of RPM International Inc.)
For hundreds of years, the global paint and coatings industry has played a key role in driving new product innovations that are used to beautify, protect and extend the useful life of the world around us — from infrastructure and the built environment, to everyday consumer goods.
Not only do coatings add aesthetic appeal to a finish, but they have long served as a highly durable, protective barrier against degradation from corrosion, abrasion, extreme temperatures, chemicals and other harsh conditions. In addition, many coatings support sustainability by maximizing energy efficiency, reducing landfill waste and curbing CO2 emissions.
As Carboline marks a major milestone of 75 years in business, let’s take this opportunity to reflect on the longstanding history of the paint and coatings industry — and how it has evolved since its early days into the nearly $165-billion global industry we see today.
Historic Influences on the Paint and Coatings Industry
For more than 30,000 years, humankind has been using paint as a decorative or protective coating. In the earliest times, cave dwellers and hunters used crude paints to depict graphic representations of their daily lives — some of which still remain on display even to this day.
Flash forward to the early 19th century, when the very first paint and varnish factories were established in industrialized nations around the world. After paint formulations had been produced in only small batches for hundreds of years at a relatively steep expense, the increasing demand among consumers for ready-mixed paints and coatings made it a highly profitable venture to manufacture paint for wider consumption.
Two major influences for this evolution were the Industrial Revolution and the mass production of the automobile industry — both of which opened the door to vast new markets for paints and coatings. As the need for anti-corrosive and other special-purpose coatings continued to grow, advancements in paint formulations quickly followed suit to meet consumer demand. Coatings were used on virtually every consumer good that was manufactured on an assembly line — from the Model T Ford, to children’s toys and the latest-model radio.
In the years leading up to World War II, consumers began to recognize the inherent health and environmental risks associated with certain paint ingredients. In response to these growing concerns, paint manufacturers began to use titanium dioxide — an inorganic white pigment introduced to the market in 1918 — as a safer alternative to lead and other toxins.
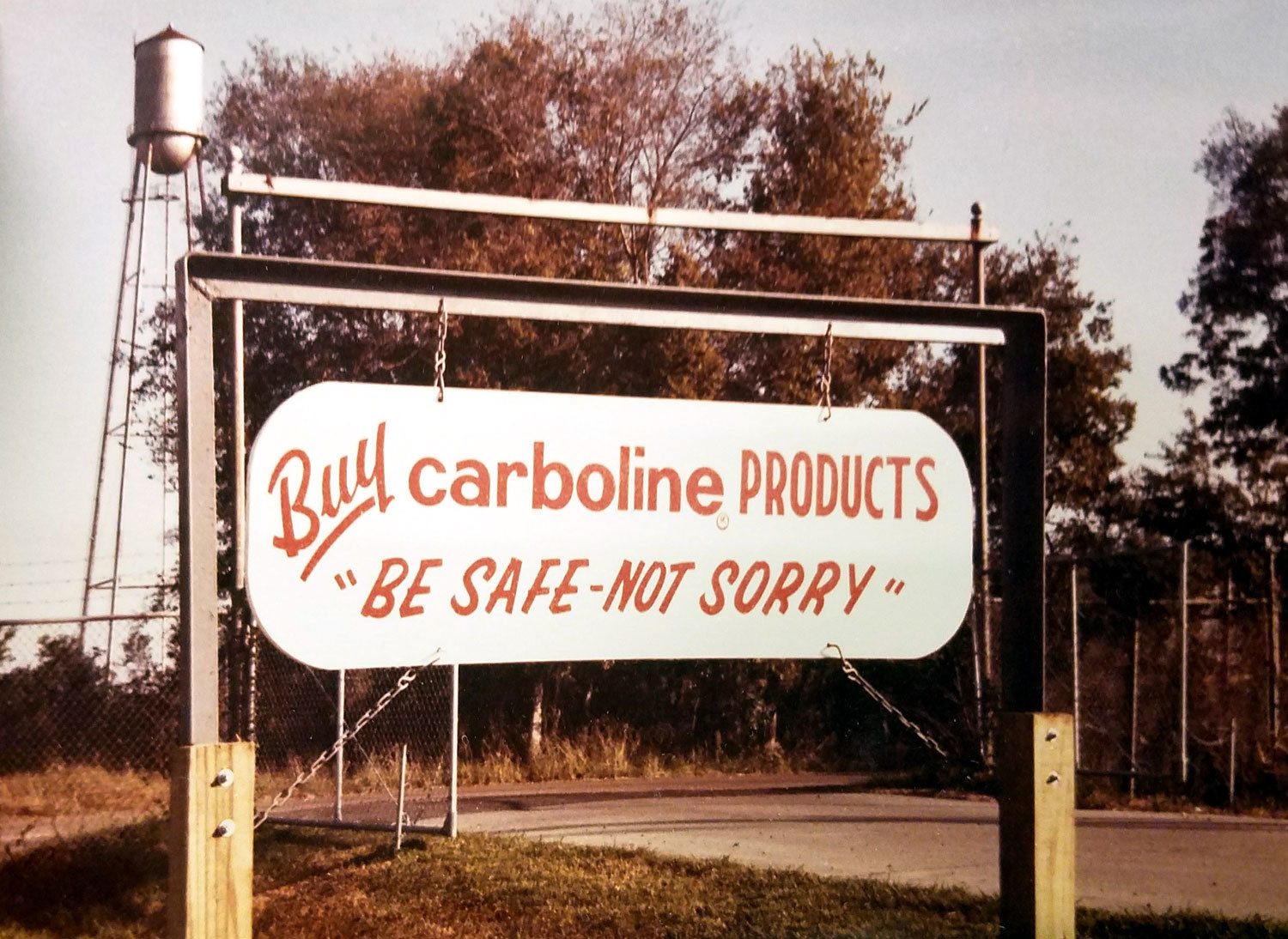
By the middle of the 20th century, the natural oils that had been traditionally used in paint and coating formulations were being replaced by synthetic resins. Around this time, Stanley Lopata, a chemist by training, was working as a manufacturer’s representative selling corrosion-resistant equipment to the chemical industry. While visiting a customer, he noticed damage to certain “glass-lined” tanks, which were critical to the manufacturing process. Motivated to find a solution to this problem, Lopata developed a carbon-based liquid repair product known as Furan C4H40 — the catalyst for St. Louis-based Carboline’s founding in 1947.
In 1950, Carboline introduced Carbozinc 11, a self-curing, inorganic zinc primer that revolutionized painting for steel fabrication. Prior to its development, zinc primers had to be cured using a post-cure solution sprayed onto painted steel members. It wasn’t long before Carbozinc 11 started to replace lead-based paints on our nation’s steel bridges. This innovation was key during the industrial construction boom of the 1960s through the early 1980s, when interstate highway construction was expanding and the use of deicing salt exploded.
As this period brought major changes to the industry, Carboline continued to expand its coatings and linings business internationally — starting in the 1950s with Canada, Italy and France. By the early 1960s, Carboline had grown to become a $2-million, publicly traded company.
In 1958, President Eisenhower convinced Congress to pass the National Aeronautics and Space Act and, just a decade later, Neil Armstrong became the first person to walk on the moon. By the early 1970s, NASA’s space program ignited the development of Cape Kennedy Space Center’s Vertical Assembly Building in Cape Canaveral, Florida. The largest building ever built at that time, it was located in one of North America’s most corrosive coastal areas, where conventional paint systems failed within six months. Now considered a historic landmark, this launch site has been protected by Carbozinc 11 all these years later.
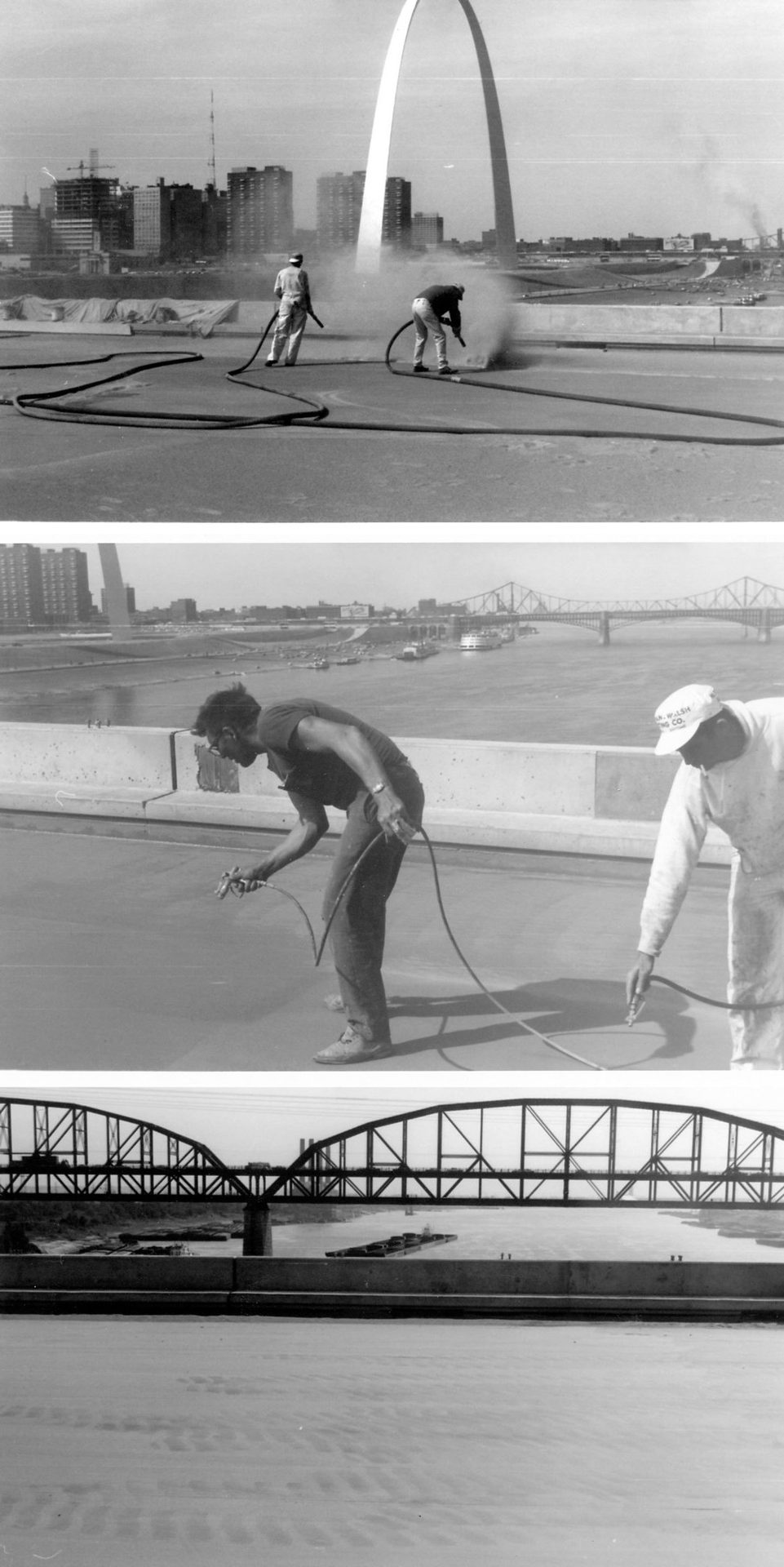
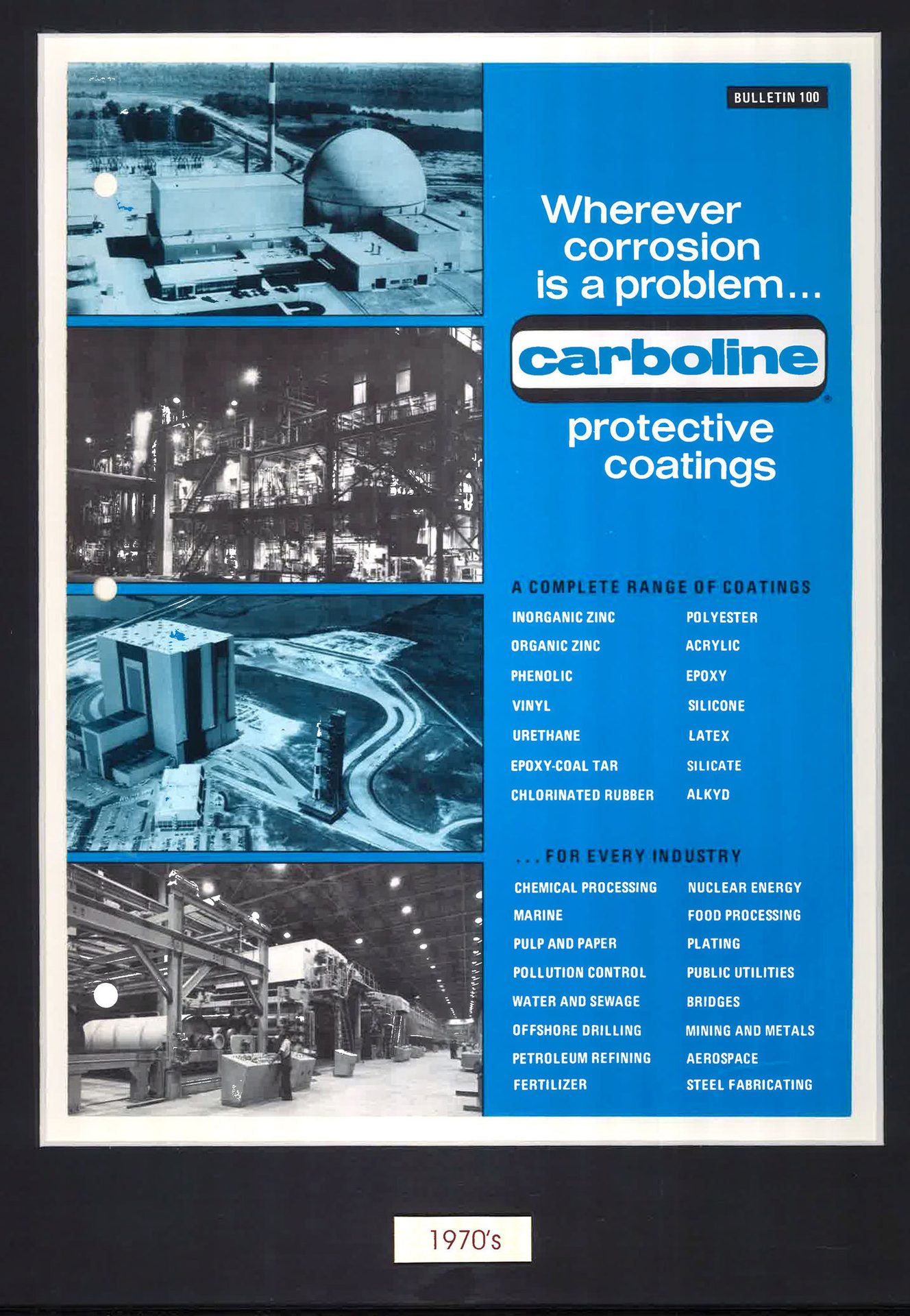
Around this time, the nuclear power market had also emerged as a key influence on the coatings industry, and the U.S. began building commercial nuclear reactors across the nation. In response to this booming market, Carboline developed safety-related nuclear coatings for containment applications. Then, in 1979, Three Mile Island’s Unit 2 Nuclear Generating Station was the scene of the nation’s worst commercial nuclear accident as a result of technical malfunctions and human error. However, the damage was minimized as a result of Carboline’s coatings, which prevented radioactive contamination of steel and concrete surfaces inside containment.
Peaking in the early 1970s, the oil and gas market saw booming growth as oil demand rose rapidly in the decades following World War II. This presented a huge opportunity for the paint and coatings industry. In fact, Carboline’s corrosion-resistant coatings were utilized on the Gullfaks Platform, one of the most profitable developments in the North Sea.
Leading up to this period, the innovations of its Phenoline, Pyrocrete and Carbomastic product lines allowed Carboline to penetrate the marine, bridge and commercial architectural markets. The introduction of Carbomastic 15 in 1970 revolutionized maintenance painting as a one-two punch for both new construction and maintenance applications.
In 1981, Carboline’s acquisition of the Plasite line allowed the company to penetrate the railcar and transportation markets. This eventually progressed to the production of protective linings for various storage tanks, including frac and water tanks, across multiple industries. A few years later, in 1985, Carboline was acquired by RPM International Inc., now a $6.1-billion global leader in specialty coatings, sealants and building materials.
As new regulations of the 1990s mandated that the environment be protected from contamination that could occur from tank leakage, the need for secondary containment was born. To address this need, Carboline acquired its Semstone line of secondary containment linings.
When the 1996 Summer Olympic Games were awarded to Atlanta, the city scrambled to prepare its stadium — fast-tracking it for completion. For this project, Carboline developed the first high-friction organic zinc primer that accelerated the application and shipping of steel fabrication.
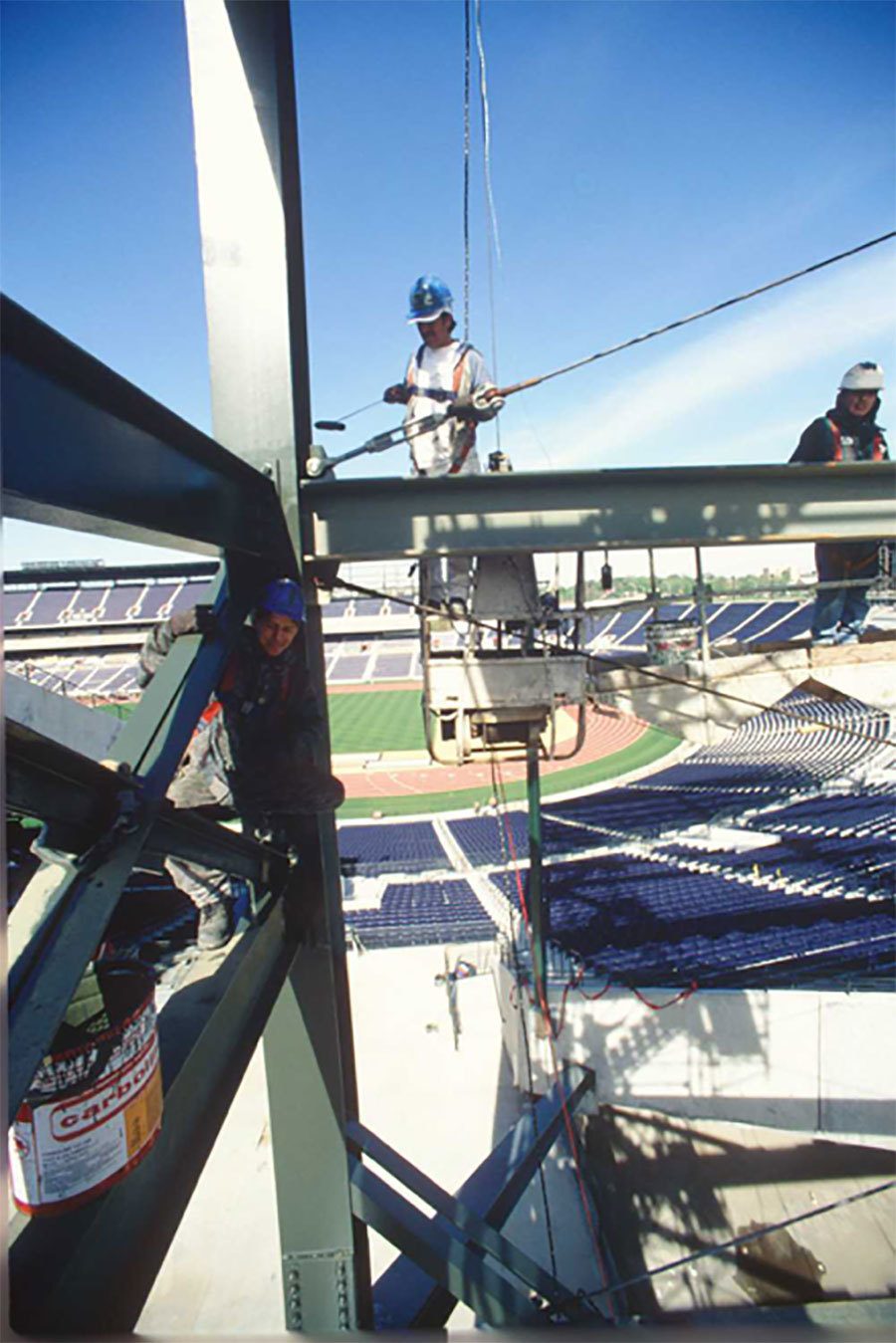
As this decade set the stage for a new millennia, the early 21st century presented new challenges as awareness of coatings’ environmental impact continued to rise. This led to widespread demand for eco-friendly solutions that would meet the needs of consumers and manufacturers alike, while complying with environmental regulations put forth by various government agencies. As a result of this movement, coating manufacturers began to phase out volatile organic compounds (VOCs) for water-based and solvent-free coating formulations.
A Push for Sustainability Promotes Greener Chemistry
Over the past two decades, the paint and coatings industry has risen to meet constantly evolving market demand, regulatory developments and industry trends by taking proactive measures to reduce its environmental footprint. This has involved investing more heavily in R&D and sustainable manufacturing practices in order to develop new coatings in a more environmentally conscious way — without compromising product performance.
This movement for environmental stewardship led to the emergence of innovative technologies with greener chemistries, such as water-based, powder, ultraviolet (UV) cure and lower-emitting coatings — ultimately contributing to a drastic reduction in both hazardous air pollutants (HAPs) and volatile organic compound (VOC) emissions from production in recent years.
In fact, the U.S. Environmental Protection Agency’s (EPA) Toxics Release Inventory revealed that emissions by the paint and coatings sector decreased by 81% between 1990 and 2014. Even more significant was the 94% decline from toxicity-weighted air toxic emissions during this time.
Among some of these eco-friendly solutions was Carboguard 890, the first high-solids, VOC-compliant epoxy to hit the market. Developed on what was an innovative curing technology at the time, Carboguard 890 is highly resistant to chemicals and abrasion.
A recent example of this epoxy at work is the Paso Robles wastewater treatment plant in California’s Central Coast region. In June 2017, the city began constructing a large-scale Tertiary Treatment Facilities project to support its long-term plan of building a sustainable, recycled water system. This included flow equalization basins, cloth media filtration, UV light disinfection, a recycled water pond and pump station, and a nutrient-harvesting reactor.
Given its frequent exposure to chemicals and cleanings, the facility’s exterior piping, EOM equipment, structural steel and interior linings were primed with Carboguard 890 and top-coated with Carbothane 134 series. Carboguard 510 SG, Plasite 4500 S and Bitumastic 300 M were also used to coat the water basin, treated water tanks and existing clarifier. In 2020, the Paso Robles plant won the Wastewater Project of the Year Award at the Global Water Awards.
In addition, the industry continues to embrace sustainability and social responsibility through its heightened focus on maximizing resource recovery to curb production waste, formulating products that meet specific safety requirements, and supporting life-cycle analyses that evaluate the environmental benefits of preserving the global infrastructures.
According to the EPA’s Hazardous Waste Report, the paint and coatings industry nearly cut its total production waste in half — a 48% reduction — between 1995 and 2013. It also increased total recycled waste by more than 81%. On top of that, 97% of all waste solvents from paint and coating manufacturing facilities are now reclaimed for future use.
As a result of these environmental advancements, coatings are now engineered to not only be more sustainable, but to provide superior performance and protection under a wide variety of conditions — from harsh, corrosive chemicals, to extreme temperatures and UV exposure.
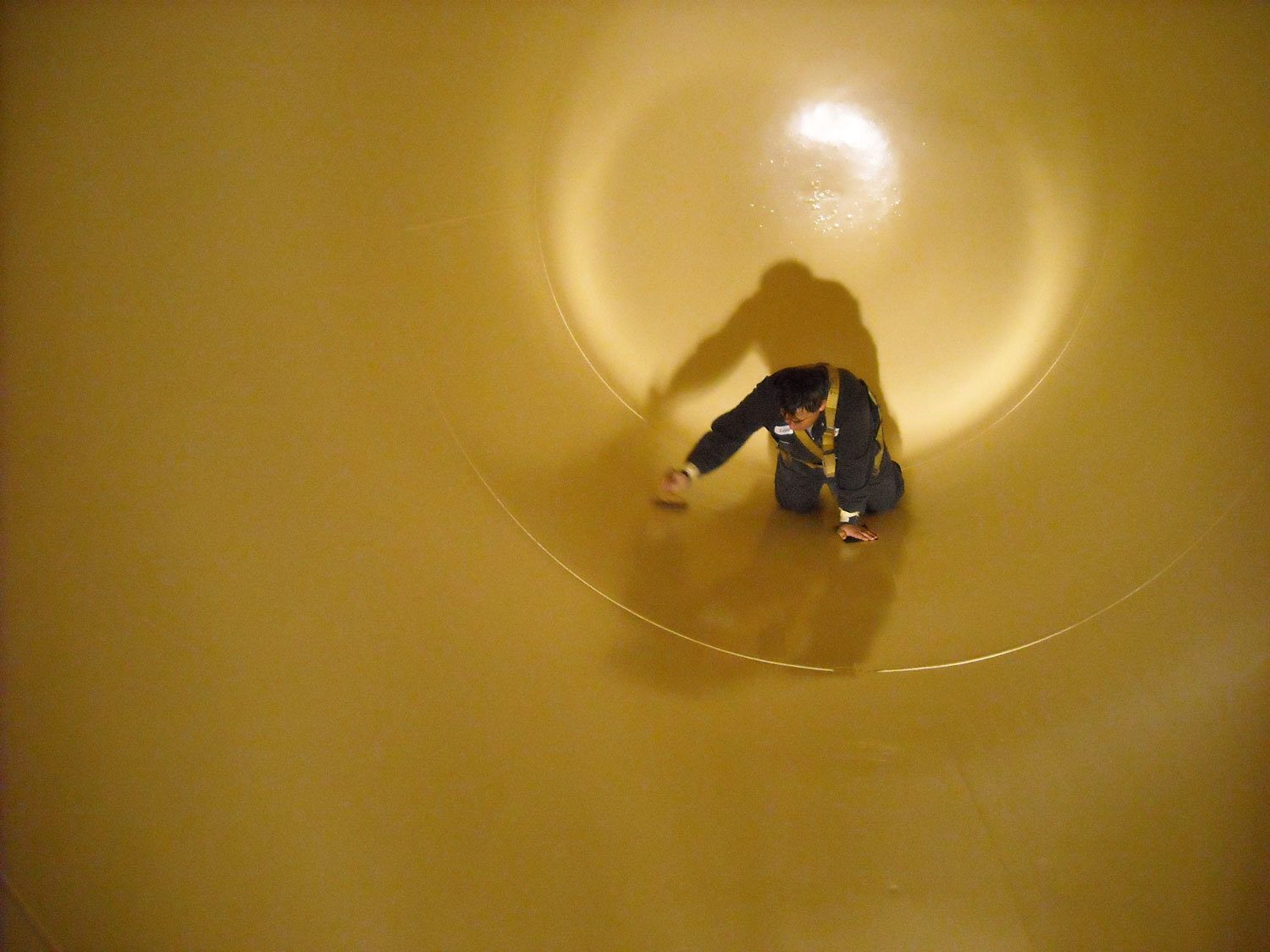
Specialty Coating Formulations Open the Door to New Markets
Over the course of nearly a century, the paint and coatings industry has evolved from small-batch production for general, multi-purpose needs to high-performance coatings that are specifically formulated to fulfill the varied requirements of countless applications.
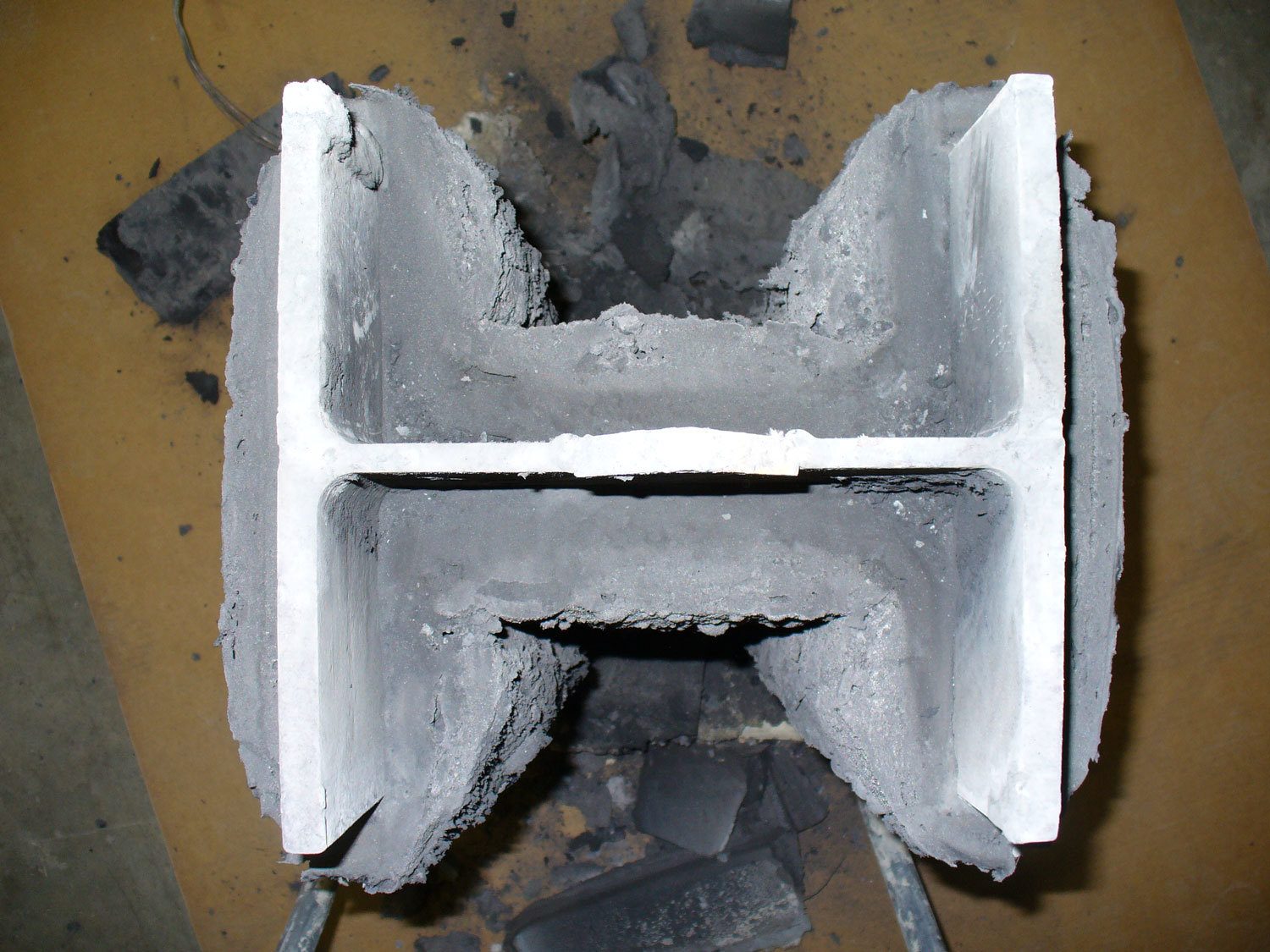
This ranges from transparent barrier coatings that line the interior of food packaging and conductive coatings used on cellphones and tablets to reflective, cool roof coatings and multi-component finishes applied by automobile manufacturers on the assembly line.
Two popular markets within the world of industrial coatings are anti-corrosion coatings and passive fire protection — both of which anticipate continued growth. In fact, the anti-corrosion coatings market is projected to reach $32.5 billion by 2024 — a compound annual growth rate (CAGR) of 4% — while the passive fire protection market is slated to exceed $9 billion by 2027.
Across both the commercial and industrial markets, passive fire protection has historically been a key driver of growth for Carboline — a position that was bolstered by the company’s acquisitions of Nullifire, AD Fire and NuChem in the late 1990s and early 2000s. Just a decade later, Carboline set the new standard in offshore fireproofing with its launch of Pyroclad X1 in 2013 — earning it the most comprehensive fireproofing line on the market.
However, the heart of Carboline’s business remains in corrosion-control coating systems, which have made it a key player in markets such as power, food and beverage, pharmaceutical, mining, brown water marine, OEM and commercial construction.
Most recently, Carboline acquired the Ohio-based Dudick Inc. business in June 2021. A world leader in corrosion resistance and chemical containment systems, Dudick has further diversified Carboline’s product portfolio in secondary containment, flooring and water/wastewater.
Evolving Customer Needs Drive a Focus on R&D and Innovation
As customer demands rapidly evolve, paint and coating manufacturers are investing more heavily in research and development (R&D), testing and product innovation in order to meet their needs and maintain a competitive edge.
To date, Carboline has introduced more than 500 innovative coatings, including well-known product lines like Carboguard, Bitumastic and Thermaline. In 2021, Carboline opened the doors to its state-of-the-art, full-scale Fire Protective Lab — the first and only manufacturer-owned lab in North America. This allowed Carboline to triple its speed to market, avoid costly third-party testing and promptly address customer needs.
Some of its more recent products include Pyrocrete 341, which offers cementitious passive fire protection for hydrocarbon fire, jet fire and cryogenic spill exposures, and Plasite XHT 400, designed for the long-term protection of fire tubes in oil processing vessels. This lining utilizes Carboline’s patent-pending Supoxy system, which delivers extreme heat and chemical resistance from the highly cross-linked resin.
It's also no secret that workers in the coatings industry are routinely exposed to a wide variety of risks — from working with hazardous chemicals and using dangerous machinery, to performing their jobs under extreme conditions such as working at height. Over the past decade, there has been a heightened focus among coatings manufacturers on establishing health and safety programs that protect not only their workforce, but the surrounding communities at large.
Cultivating the Next Generation of Coatings Professionals
As an entire generation of seasoned coatings and corrosion professionals looks ahead to retirement, new leaders are beginning to emerge in the industry by taking on more decision-making roles. Yet, despite this changeover, the industry continues to face widespread shortages in skilled labor — making it extremely challenging to find good talent. In an effort to drive the industry forward, many coating manufacturers have sought to overcome this challenge by creating talent development programs aimed at molding young professionals.
For example, Carboline established its CarboNext program to educate, connect and support the next generation of corrosion professionals. It offers technical training, networking opportunities and other resources focused on corrosion control and protective coatings.
The Future of Coatings is Colorful Despite Challenges
Despite pandemic-driven raw material shortages and construction delays, the coatings industry is likely to see continued growth. According to a study by Fortune Business Insights, the global protective coatings market is projected to reach $21.2 billion by 2028 — a CAGR of 7.3%.
This growth will largely be driven by consumer demand — particularly for smarter, more sustainable solutions. Looking ahead toward this bright future, coatings manufacturers worldwide will be investing more dollars than ever in R&D and innovation.
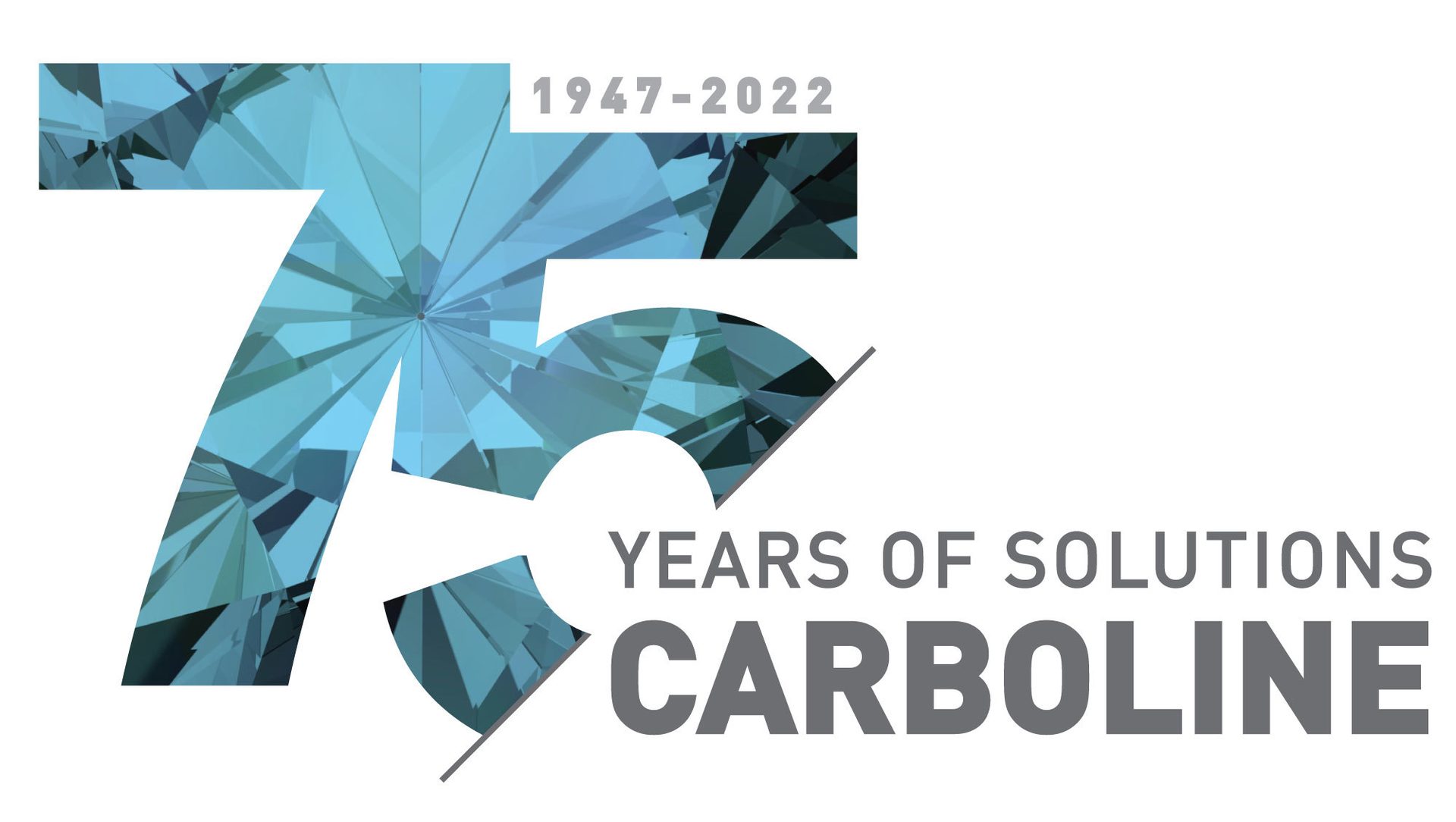
To build upon this growth, Carboline is embarking on the most extensive strategic initiative in its 75-year history, with the single-largest investment of SG&A expenses and capital. Carboline will expand its operations across Canada and Europe, widely diversify business in the U.S., and significantly grow its sales and EBIT over the next five years. In addition, this expansion will increase the company’s focus on the renewable energy sector.