Ready to proof -- Clare 5/4/22
KJ proofed on 5/16 and sent corrections to Clare
Revised on 5/16
Ready for author
ASK JOE POWDER
Sponsored by Gema
Our popular Ask Joe Powder blog has made its way to the pages of PCI magazine. What are your powder coating questions and challenges? Joe Powder, aka Kevin Biller of ChemQuest Powder Coating Research, shares his powder coating knowledge and expertise by answering questions sent in from around the world.
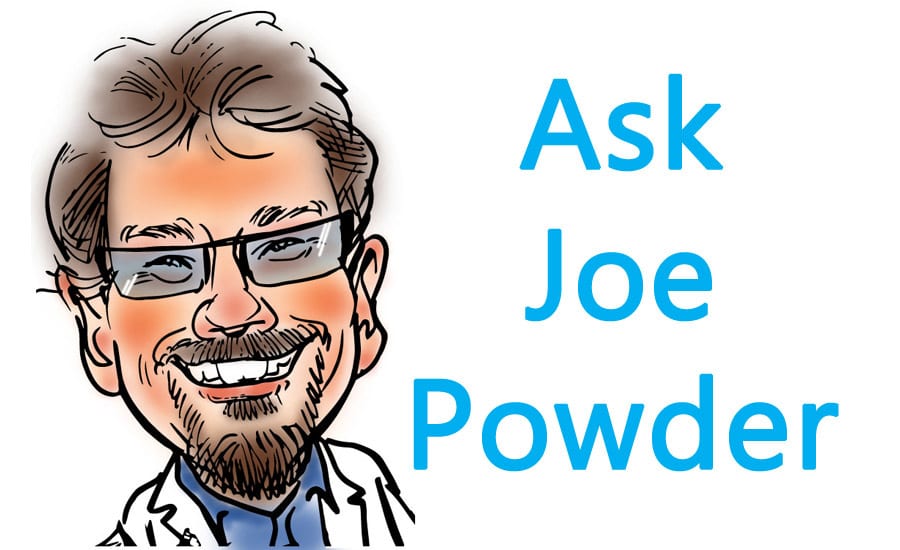
Dear Joe,
I'm a manufacturer of powder coatings in Vietnam. We have a problem with our product as follows:
The reclaimed powder is being sprayed on the object, but it has very poor transfer efficiency. (I know, the reclaimed powder should be added with fresh powder at a ratio 70/30 or 60/40, but my customer is spraying the reclaim alone). The particle size of fresh powder is 5 microns to 80 microns, D50=28 microns. Percentage of particle size 5-10 microns is about 10%. How would you suggest for us to enhance transfer efficiency with reclaimed powder?
I look forward to receiving a reply from you soon.
Thank you and best regards.
Tu Long Nguyen
Vietnam
Dear Tu Long,
Thank you for your question. Indeed, this is a challenge. As you know, the best solution is to correct the root cause, which can be delineated into two issues:
1. Improve first pass transfer efficiency to minimize the creation of overspray, which needs to be recycled. This can be accomplished by regular gun maintenance, always ensuring excellent earthing of the parts to be coated, keeping racks clean and using powders with good particle size distribution (minimal fines and coarse particles).
2. Only introduce a low level of reclaim to the virgin powder. Less is always better, but it is wise to never exceed a 30% reclaim to virgin powder ratio.
Obviously, you need help now because your customer insists on spraying high levels of reclaim. There is hope, however the solution is imperfect. It is possible to improve the fluidization and application performance of reclaim powder. The use of a dry-blend additive is worth attempting as a solution to your customer's application problem.
These materials are based on fumed silicas that have been surface treated to make them hydrophobic. The best material to try is based on a silane-treated hydrophobic fumed silica. They are supplied as agglomerates of very fine particles of silica, typically around 0.2 microns in diameter. Think of them as clusters of grapes. These agglomerates can be quite large and therefore will create defects in the finished powder if they have not been adequately de-agglomerated. Hence the mixing process used to disperse the dry-blend additive is important.
Here are a few guidelines for incorporating a dry-blend additive to the powder. A good starting point is a concentration of 0.2% by powder coating weight. Mix the modified powder coating thoroughly. I suggest a V-blender or something similar to accomplish this. After mixing, I recommend sifting the powder through a relatively coarse screen (80 mesh or 175 microns). This can further de-agglomerate the dry-blend additive to help minimize the possibility of "seeds" due to large agglomerates.
The modified powder will fluidize and transport through the application system much better than unmodified reclaim powder. I would pay close attention to the film thickness of the coated parts. Thicknesses less than 50 microns (2.0 mils) may exhibit "seeds" or defects caused by the protrusion of silica agglomerates.
Best of luck Tu Long. If possible, please provide an update of your progress.
Kind regards,
Joe Powder
Dear Joe,
I have a few questions for you regarding the powder coating process and defects. I hope you don’t mind taking the time to answer them for me. Here we go:
Is there any indication that static electricity could be causing defects such as fisheyes, cratering or "bits" in the powder coating process? Is any static electricity generated in any one of the powder coating systems? What products are commonly used when repairing the types of defects noted above? And last, but not least, how are powder coating companies ensuring that dust and lint are at a very minimum prior to coating their products?
Joe, thank you very much for your time. I really appreciate it.
Vicky DeRoven
Detroit
Hi Vicky,
Wow, you have a lot of questions. Let me break them down.
Static electricity — yes there is static electricity and from more than one source when dealing with powder coating application. As you probably already know, powder coatings are electrostatically charged, typically by a corona mechanism near the tip of the business side (outlet) of the spray gun. This works by very high voltage (80,000 to 100,000 volts) being delivered to the electrode. This high voltage ionizes the air, creating a field of electrons or negative charge. (Don't worry, the current is very small, typically micro-amps, so the process is relatively safe.) The powder is pneumatically conveyed into this electrostatic field, picks up a charge then heads to the nearest ground. The object of the game is to make your parts the closest ground and then the powder deposits on the surface of said part.
So, lots of static electricity is generated by the spray system. It's important to note that static electricity is generated elsewhere in the finishing system. The mere fact that powder particles are being conveyed into fluidizing hoppers, through powder pumps, hoses and spray guns creates static charges. This extraneous generation of charge affects powder deposition and can influence transfer efficiency.
Does static electricity cause fisheyes, cratering and "bits"? Probably not. Very characteristic defects are caused by electrostatics however. Excessive charge can build up in a powder coating layer if the powder is applied too thick, too quickly. This phenomenon is known as back ionization. The build-up of charge causes powder particles to microscopically burst away from the substrate. This causes micro defects that resemble volcanoes. These defects cause a rumpled appearance that looks more like localized macro-orange peel for lack of a better description.
Fisheyes are caused by a different mechanism and are more distinct in their appearance. Fisheyes are created by a significant differential in surface tension between a molten powder film and a contaminant. Common contaminants are lubricants and oils. Silicone lubes and penetrating oil (e.g. WD-40) are some of the worst actors. Fisheyes are gross defects characterized as deep circular voids in the coating film that reach the substrate. Craters are ambiguously defined as defects similar to fisheyes but smaller in diameter. Craters often do not reach the surface of the substrate and typically look like dimples.
As for "bits" I imagine you are referring to unmelted protrusions in the finish of the cured powder coating. These are not caused by static electricity. Common sources of "bits" are environmental dirt (oven, spray area, unclean application equipment, etc.), unclean substrate or dirty powder coating. They are typically more prominent at thin films (i.e. < 1.5 mils). If the preponderance of "bits" decreases with thicker coating films then you can suspect either the powder or a contaminated substrate surface. If film thickness is not a factor, then the contaminant is probably environmental and is deposited on the powder after it has been applied.
Regarding repair — fisheyes, craters and "bits" need to be buffed with an abrasive (Scotchbrite™ or 200 grit sandpaper), the surface wiped (e.g. acetone), dried and recoated. Alternately you can consider using a liquid paint-based touch-up if the repair is small and localized. Be careful however, as the touch-up may not meet the performance of the original powder coating finish.
Are powder coating companies doing everything to minimize dust and lint? Do you mean powder applicators or powder coating manufacturers? High-quality coating shops are very clean, with isolated application areas that use filtered make-up air. Their processes are carefully monitored and controlled. It's fairly easy to discern their quality level with a visit and tour of their finishing operations. As for powder coating manufacturers, there is a range of quality. Large producers have prominent quality programs, but this doesn't necessarily mean they clean their equipment well or that they produce perfectly clean products. If you can tour their facility, it will speak volumes on how they manage their manufacturing and quality programs. Word of mouth is also a good means to learn about a supplier.
I hope this helps you better understand the powder coating process and how defects occur. Please let me know if you have any more questions.
Best regards,
Joe Powder