Ready to proof — CLJ 2/8/22
KJ proofed and sent Clare corrections on 2/10
Revised on 2/10
KJ sent one more correction on 2/11
Revised on 2/11
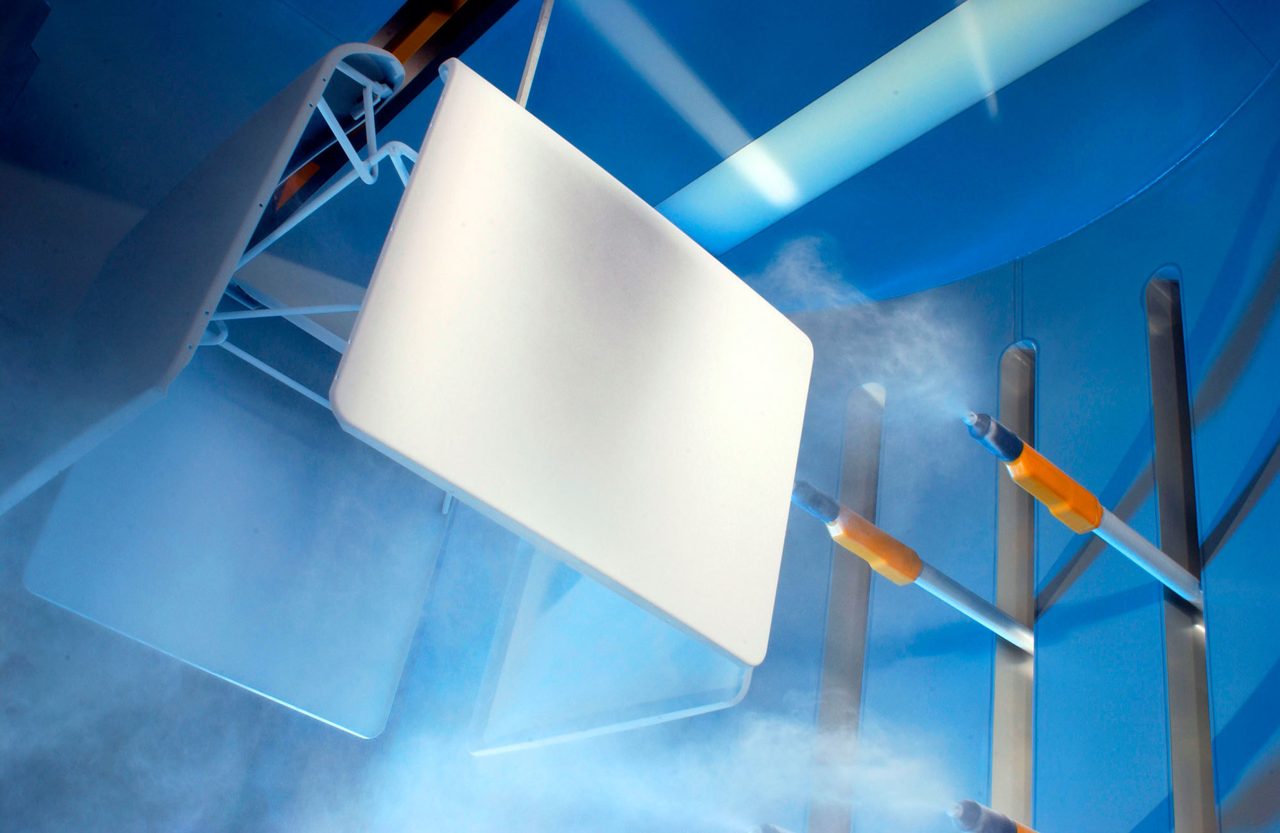
Hard Minerals Enhance Powder Coating Performance
Photo courtesy of Gema USA.
By Kevin Biller, President, ChemQuest Powder Coating Research, Columbus, OH
Powder coatings continue to expand their share of the industrial coatings market mainly because of their high performance combined with excellent economics. The application of powder coatings can be highly efficient, as the oversprayed material can be collected and recycled back into the finishing process. This minimizes waste streams, which allows powder’s environmental profile to align well with both corporate and regulatory sustainability goals.
Experts forecast robust growth of powder coatings. Global sales of powder coatings in 2021 are estimated to be around $12.5 billion (€10.6 billion) with a volume of approximately 5.5 billion lbs. (2.5 million tonnes). Growth is projected at 3.9% to 5.4% per annum for the next five years.
Abrasion resistance in powder coatings is an important property. Some powders are used to coat items that are subjected to extreme environments such as oil and gas transmission pipelines. Whereas other powder coatings are used in decorative applications where appearance is critical. These decorative finishes must maintain their appearance after the handling of parts during assembly, and everyday wear and tear.
Improving abrasion resistance is a sought-after goal of powder coating formulators, whether for functional or aesthetic purposes. The use of high-hardness mineral fillers is considered one avenue to increase abrasion resistance in powder coatings. This study examines the effect that white fused alumina, nepheline syenite and silicon carbide have on the abrasion resistance of a common powder coating system based on polyester-HAA (hydroxy-alkyl amide) chemistry.
Wester Mineralien
Wester Mineralien are experts in the refinement of mineral grains. The company offers intelligent solutions for abrasion-resistant, scratch-resistant and slip-resistant surface coatings, as well as blasting agents, abrasives and polishing agents. Wester has recently ventured into powder coating technology as a supplier of hard minerals to enhance powder coating performance.
Objective
Evaluate functional fillers in an industry-relevant powder coating formulation. Compare performance to a common industry filler and an unmodified control formulation. Evaluate for: processability, application performance, appearance (color, gloss and surface profile), mechanical properties, and abrasion resistance.
Materials
- Carboxyl polyester resin – Crylcoat 2689 – Acid value: 34, Tg 62° – allnex
- Hydroxy alkyl amide – Curing agent - Aal Chem
- Polyacrylate flow agent – Estron Chemical
- Benzoin – Degassing agent – Aal Chem
- Titanium dioxide pigment – TiPure R-960 – Venator
- Black manganese ferrite pigment – Lansco 8303 – DCL Corp.
- Nepheline syenite – Minex 4 – D50: 6.8 µm – Sibelco
- White fused alumina – F 500 – D50: 12.8 µm – Wester Mineralien
- White fused alumina – F 800 – D50: 6.5 µm – Wester Mineralien
- Silicon carbide – F 500 - D50: 12.8 µm – Wester Mineralien
Tables 1-3 show typical analysis of nepheline syenite, white fused alumina and silicon carbide. Table 4 shows general properties of mineral fillers.
TABLE 1 ǀ Nepheline syenite – typical analysis.
TABLE 2 ǀ White fused alumina – typical analysis.
TABLE 3 ǀ Silicon carbide – typical analysis.
TABLE 4 ǀ General properties – mineral fillers.
Formulation Platform
Materials were evaluated in a gray, standard, durable polyester-HAA powder coating. Fillers were incorporated at 5% and 10% by volume. Industry-standard additives were incorporated at conventional concentrations. Pigmentation consisted of titanium dioxide tinted with an inorganic black pigment (Table 5).
TABLE 5 ǀ Formulations.
Processing Conditions
The processing conditions were as follows:
- Premix: 8 seconds Vitamix @ low setting
- Extrusion: APV 19 mm twin screw extruder
Zone 1 : 100 °C
Zone 2 : 100 °C
Screw RPM : 500
Torque: 45 – 55%
Chill Rolls RPM: 18
- Grind: Strand mill
- Sieve: 140 mesh (106 µm)
- Application: Nordson Encore LT manual spray gun
- Substrate: 75 mm x 150 mm cold rolled steel test panels
- Film Thickness: 50 to 60 µm
- Cure: 10 minutes at 200 °C
Results
Processability
All samples processed well using the conventional conditions outlined above. No issues were experienced with extrusion, pulverization or electrostatic application.
Aesthetics
Gloss was measured at a 60° angle using a TQC Polygloss GL0030. Multiple measurements were taken in various locations across the surface of the finished coatings, and then averaged. Gloss was reduced with the addition of all fillers evaluated. Gloss reduction was very similar with the incorporation of nepheline syenite, white fused alumina F 500 and the silicon carbide F 500. The white fused alumina F 800 material reduced gloss slightly less.
Surface profile was graded using PCI Smoothness Standards, a subjective visual scale that ranges from 1 (the most texture) to 10 (the smoothest). The addition of 5% of all fillers had essentially no effect on smoothness, and the 10% addition of either white fused alumina F 500 or silicon carbide F 500 caused a slight increase in texture.
Rheology
Melt viscosity was ascertained using the pellet flow technique per ASTM D-4242. 1.0-gram pellets of each formulation were pressed, adhered to a test panel and baked at the standard curing condition (10 minutes at 200 °C metal temperature) at an incline of 65° from horizontal. Longer pellet flow correlates to a lower melt viscosity. Pellet flow was reduced incrementally with the addition of all fillers and correlated well with the surface profile observations.
Table 6 shows the gloss, smoothness and pellet flow results.
TABLE 6 ǀ Gloss, smoothness and pellet flow.
Color
Color was affected versus the control with the addition of all fillers. Nepheline syenite caused the least shift in color, whereas white fused alumina F 500 and white fused alumina F 800 caused a moderate shift. The silicon carbide F 500 material caused a significant shift in color. The color shift in all cases was mainly darker (lower “L” value) and was incrementally greater with higher concentrations of filler (Table 7).
TABLE 7 ǀ Color.
Mechanical Properties
Impact resistance is a rapid deformation test that was performed per ASTM D-2794 using a Gardner Impact Tester. Panels were struck with the tester both on the film surface (direct impact) and from the uncoated side of the panel behind the film (reverse impact). Impact resistance was measured in inch-pounds of force. The largest amount of force applied that did not result in the coating becoming cracked was recorded in Table 8. Impact resistance was generally unaffected by the addition of all of the fillers. A slight increase in impact resistance was observed with a 10% addition of silicon carbide F 500. This may fall within the precision of the test method.
TABLE 8 ǀ Impact resistance.
Abrasion Resistance
Abrasion resistance was evaluated using the Taber Abrasion test method per ASTM D-4060 using CS-17 abrasive wheels. Coating loss was measured after 500 and 1,000 cycles. The addition of all fillers provided a significant improvement in abrasion resistance versus the unmodified control. Best performance was observed with the addition of silicon carbide F 500, followed closely by white fused alumina F 500. Both white fused alumina F 800 and nepheline syenite provided improvements in abrasion resistance to a lesser degree. Abrasion resistance and coating loss results are shown in Table 9 and Figure 1.
TABLE 9 ǀ Abrasion resistance – ASTM D4060.
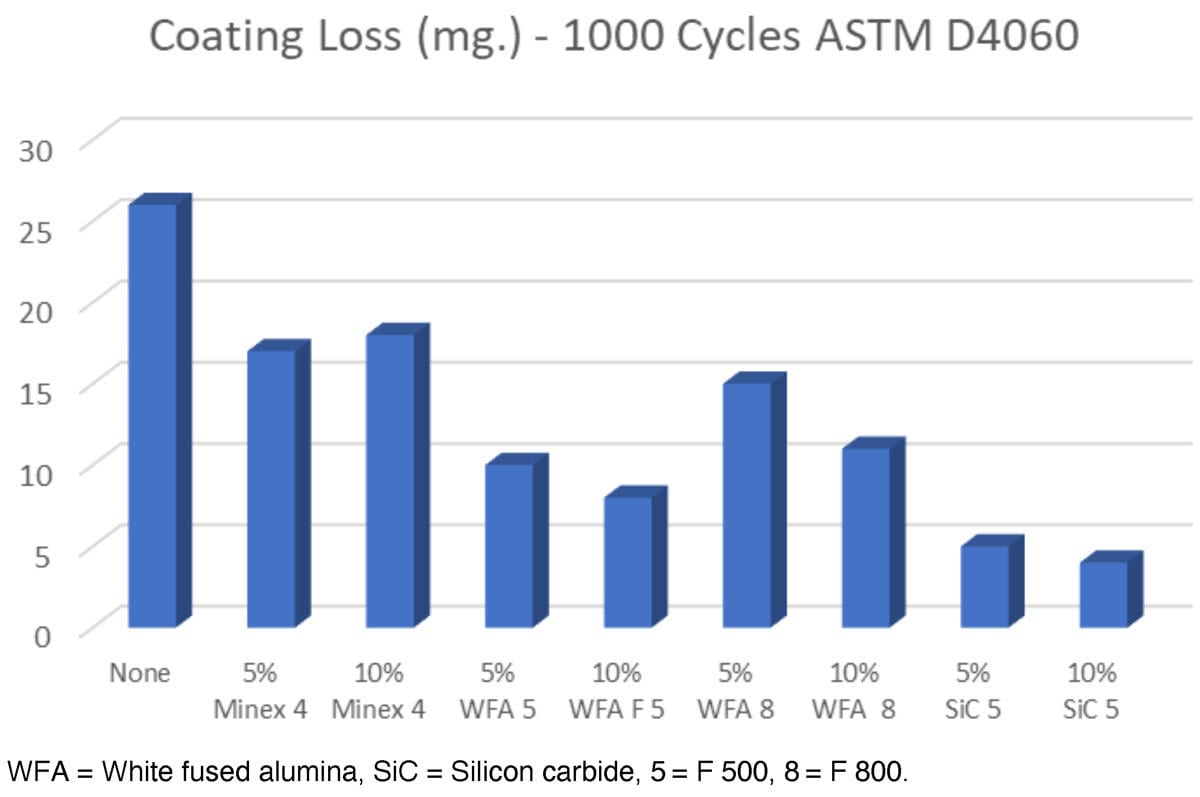
FIGURE 1 ǀ Coating loss.
Discussion and Conclusions
The primary goal of this study was to determine if the addition of “hard” mineral fillers such as white fused alumina, nepheline syenite or silicon carbide would increase the abrasion resistance of a powder coating. The addition of all fillers evaluated provided a significant improvement in abrasion resistance versus the unmodified control. Best performance was observed with the addition of silicon carbide followed closely by the large particle size white fused alumina (WFA F 500). After 1,000 cycles of Taber Abrasion per the ASTM D4060 Test Method, the control lost 26 mg, whereas 10% silicon carbide (SiC 5) lost 4 mg and white fused alumina (WFA F 500) lost 8 mg.
Adding 10% of the smaller particle size fillers, white fused alumina (WFA F 800) and nepheline syenite (Minex 4) provided improvements in abrasion resistance to a lesser degree. The WFA F 500 lost 11 mg, and the nepheline syenite provided the least improvement at 18 mg lost.
The addition of mineral fillers was expected to influence color, gloss and smoothness of powder coating samples.
Color was affected by the incorporation of all fillers. The 10% addition of nepheline syenite exhibited a modest effect on color of around 1.50 ΔE versus the unmodified control. The white fused alumina materials added somewhat more color with a ΔE of around 3.10 to 3.30. The silicon carbide material, black in color, introduced the most color versus the control with a 5.13 ΔE.
In general, the incorporation of larger particle size mineral fillers into powder coating formulations produces lower gloss. This trend was observed in this study as samples containing the larger particle size fillers exhibited measurably lower specular gloss. Specifically, the 10% by volume additions of both 12.8 µm WFA-5 and 12-13 µm SiC materials produced 60° gloss of around 48 gloss units, whereas the unmodified control exhibited a 95 GU and the smaller particle size fillers, nepheline syenite and WFA-8 produced gloss around 55 to 60 GU.
Surface profile was graded using PCI Smoothness Standards developed by the Powder Coating Institute. The addition of 5% of all fillers had essentially no effect on smoothness, and the 10% addition of either of the smaller particle size fillers, white fused alumina F 500 or silicon carbide F 500 caused a slight increase in texture.
Melt viscosity was ascertained using the pellet flow technique per ASTM D-4242. Longer pellet flow correlates to a lower melt viscosity. Pellet flow was reduced incrementally with the addition of all fillers, indicating an increase in melt viscosity. These results correlated well with the surface profile observations.
Only minimal effect on impact resistance was observed with the addition of the mineral fillers evaluated. A slight increase in impact resistance was observed with a 10% addition of SiC F 500. This may fall within the precision of the test method.
In conclusion, the incorporation of hard mineral fillers, specifically silicon carbide and white fused alumina, provides a significant enhancement of the abrasion resistance of a powder coating. Type and concentration of mineral filler should be carefully evaluated in formulations to determine optimal performance.
For further information and samples, contact Wester Mineralien GmbH through their website: https://www.wester-mineralien.de or by contacting their sales department at: +49 (228) 987 200. Wester Mineralien GmbH, Heerstraße 41, 53347 Alfter-Witterschlick, Germany.