Ready to proof — CLJ 2/15/22
KJ proofed on 2/15 and send correction
Revised on 2/15
Ready for author
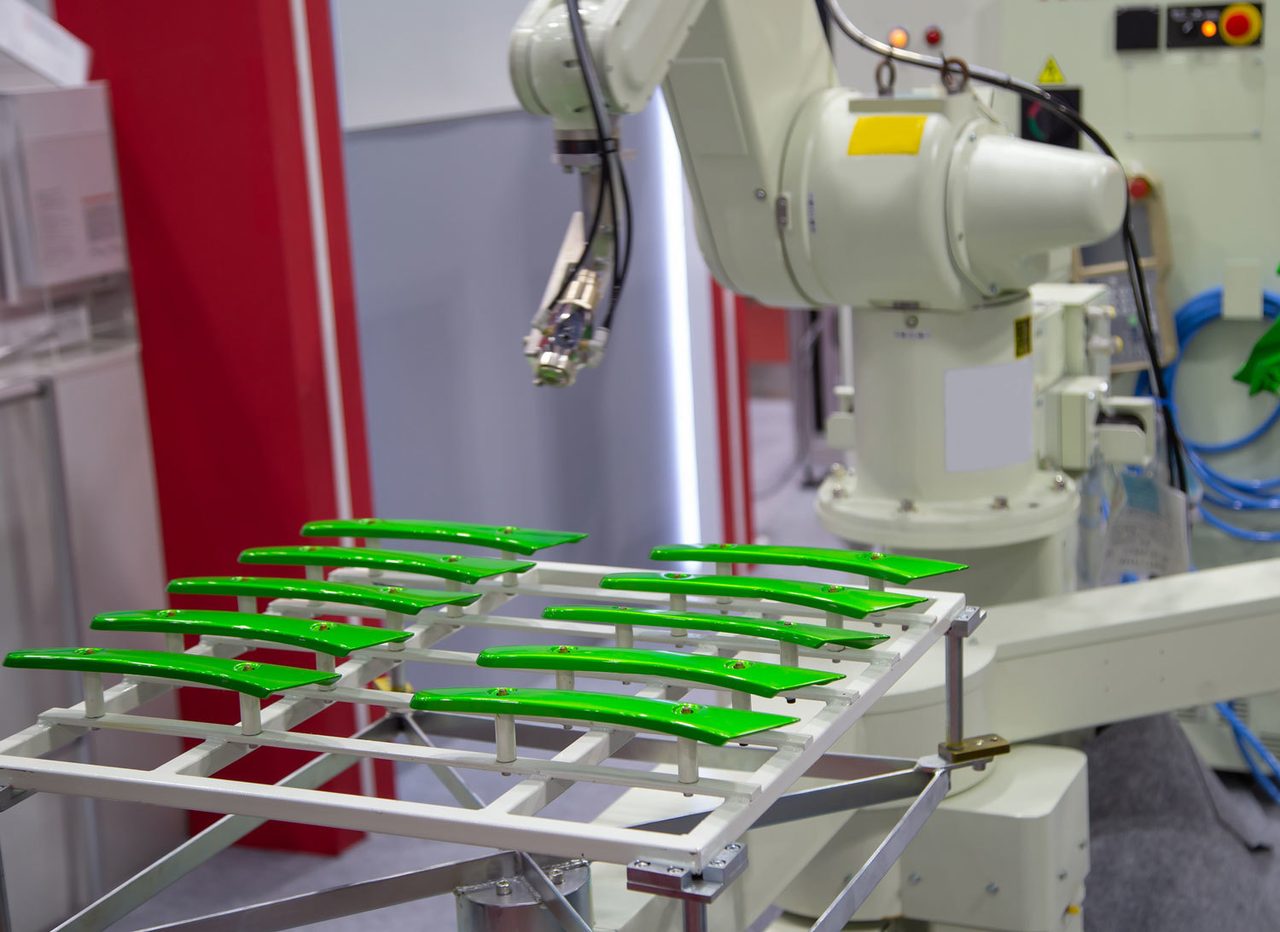
Photo: Itsanan Sampuntarat, iStock/Getty Images Plus, via Getty Images
Five Amazing Ways Robots Are Disrupting the Painting Industry
By Emily Newton, Editor-in-Chief, Revolutionized Magazine
Robots have brought dramatic benefits to industries ranging from health care to agriculture. Besides encouraging people to think differently about how these machines could improve operations, robots have brought new opportunities to tasks that once occurred solely or primarily through manual labor.
Innovations associated with painting robot technologies are great examples. Here are some of the eye-opening disruptions caused by robotic painting equipment.
1. Achieving High Efficiency with Less Waste
Two common manufacturing goals are to maintain high productivity levels and minimize waste. Meeting those aims makes it easier to stay profitable and keep budgets manageable. Painting robots can assist in both of those areas and others.
In one recent instance, robotic painting technology from ABB won the 2021 Innovation and Entrepreneurship in Robotics and Automation award sponsored by the IEEE Robotics and Automation Society and the International Federation of Robotics.
The PixelPaint includes a pair of 6-axle robots equipped with inkjet painting heads rather than conventional spray valves. It caters to customers interested in automotive painting automation. Besides eliminating the need to mask and de-mask each vehicle, the robot allows applying a two-tone or customized paint design with one pass rather than two.
Another advantage relates to how the robot eliminates overspray issues. Using other solutions typically meant losing 20%-30% of the paint due to those problems. However, this robot applies 100% of the coating to the intended surface. Then, manufacturers can make more accurate estimates about the supplies needed to cover all the cars made within a specific period.
2. Learning Powder Coating with Less Programming
There’s a good chance your home or yard includes at least a few powder-coated items now, or perhaps you’ve owned some previously. Statistics indicate that more than 15% of the world’s finishes are powder coated. It’s a popular option in steel fabrication, partly because of how a powder-coated surface offers durability that helps a product withstand severe weather and resist corrosion.
The team at South Dakota’s DeGeest Steel Works focuses on large steel production weldments for original equipment manufacturers (OEMs). As company processes experienced ongoing bottlenecks, decision-makers began exploring how automation could remedy them. Company president Derek DeGeest confirmed that his business handles the painting for hundreds of components between all the OEMs on the client list.
Automation appeared as the best way to maximize the painting department’s efficiency. After researching the options, it became clear that many of them required extensive programming before handing each part, and the process could take weeks. That was not a feasible solution for an organization working with so many component types.
However, people at the company eventually learned about Lesta, an Italian robotics brand offering self-learning machines that mimic human movements. That capability reduces the need for offline programming or using a teach pendant to train the bots.
Getting the robots ready for independent work requires activating a disengaged learning mode where the machines’ arms become weightless. A person then moves them in the desired way to paint. This process happens in a matter of seconds, making it a speedy option for preparing robots to work without ongoing intervention from people.
3. Eliminating the Hazards of Aviation Paint Stripping
Aircraft painting is an ongoing part of plane maintenance, especially for commercial jets that get regular use. It becomes an obvious necessity when the existing color becomes faded. It also occurs if an airline changes how a plane looks due to a rebranding effort.
Depainting must happen before a fresh coat of paint is applied to the surface, however. It involves stripping the existing layers with chemical or abrasive means. Those methods work well but pose environmental and human health hazards.
A Dutch company recently unveiled a robotics solution that could help. The business specializes in solutions for both stripping and painting planes. One of its newest technologies reportedly causes up to a 60% reduction in turnaround time for those jobs. Additionally, it reduces or eliminates the issues that can pollute the environment or put people at risk.
The robot, which measures more than 70 feet when fully extended, has a base with multidirectional wheels. Those allow it to move around inside a hangar or other parts of a plane maintenance facility. The machine’s color recognition and control systems give precise results when it removes paint from metal and composite surfaces.
Conventional methods of removing paint from a wide-body aircraft require 475 gallons of chemicals and 3,700 gallons of water. The robot uses neither and instead burns the existing coating from a surface with a laser. The machine then vacuums and filters the debris, resulting in only about 2 pounds of waste.
4. Creating Pleasing Visual Effects
Painting techniques and formulas can have a significant effect on how the associated surfaces look. The outcomes can give impressions of luxury, artistry, and other desirable attributes.
Representatives of global brand WB Coatings wanted to investigate new methods of using up to three layers of paint to achieve a chrome-like finish on interior car components, such as window lift switches. The company’s team realized that achieving these effects manually was prohibitively labor-intensive due to the uniformity needed to make the finish look realistic.
Andreas Ohletz, Head of Sales for Innovations at WB Coatings, clarified, “Without using a robot, we would not have been able to develop these new paint systems as a chrome-free alternative for shiny, silver-colored surfaces. The challenge is to apply the coating layers of the chrome-effect paint very evenly.”
He continued, “And the three-layer paint system in particular needs very thin, reproducible coating layers of 2 to 3 µm. This is something even highly experienced hand painters can’t achieve.”
Company leaders chose a six-axis robot that mixes and doses two-component paints before applying them with a spraying system. The dosing process requires working with tiny quantities of only a few milligrams each. Handling them manually raises the risk of inaccuracies due to human error during the challenging task. However, automating that step with the robot contributes to excellent reproducibility.
5. Giving Humans More Rewarding Responsibilities
Painting surfaces by hand is a painstaking process that often requires standing in the same position for prolonged periods and engaging in repetitive motions. However, a painting robot could give people more time to focus on tasks they find more enjoyable.
The industrial robotics sector officially started in 1954 when George Devol submitted the first mechanical arm patent paperwork. However, people liked the concept of robots helping them long before that time. One of the earliest known robots — from the third century B.C. — was a maid statue that could mix and pour water and wine.
Now that robots are much more widely available, some individuals worry that robots will take their jobs. That happens sometimes, but decision-makers also make conscious efforts to find ways for people and machines to work together. Then, the automated equipment could handle the most laborious tasks while employees get reskilled or assigned other duties they like more than their previous ones.
At a California company called Professional Finishing, leaders decided to supplement the workforce with painting robots. However, not all employees immediately took the news well. One employee said they would quit once the machines were installed. The owners assured worried workers the robots could help everyone keep their jobs.
The robotic painting equipment caused a four-factor increase compared to human productivity levels. It also eliminated processes that required people to bend, crouch and stay in other positions that often strain the body. The company’s employees that formerly held painting jobs now run the robots and ensure the machines have enough supplies.
Painting Robots Are Well Worth Consideration
Investing in a painting robot is not a guarantee of future success. Interested parties must first evaluate which processes or stages cause the most issues. They can then determine whether robotic technologies could address those challenges. However, the five use cases here highlight why people are increasingly interested in these purposeful machines.