Ready to proof — CLJ 4/25/22
Proofed by KP on 4-25-2022
KJ proofed on 4/25
CLJ revised on 4/25
Clean
COMPANY NEWS
AkzoNobel Names Winners of Paint the Future Challenge
AMSTERDAM – The three winners of AkzoNobel’s Paint the Future global startup challenge are ready to accelerate their innovative solutions for the paints and coatings industry. Following an intense three-day bootcamp, three startups were selected by an international jury to continue working with AkzoNobel on sustainable business opportunities. Within 24 hours of the selection, the three startups had signed letters of intent to continue working together on sustainable business opportunities.
The winners of the Paint the Future global startup challenge are:
SolCold: The Israeli startup SolCold is working on a sustainable, self-cooling coating based on anti-Stokes. It uses the sun’s energy to keep the inside temperature much cooler without having to use any electricity. “As a group of engineers and scientists, we know how to do R&D very well,” said Yaron Shenhav, CEO of SolCold. “But what we lack is the ability to mass-produce and scale our very innovative product. So collaborating with AkzoNobel is the perfect fit.”
Aerones: Latvian startup Aerones brings a robotic solution to wind turbine maintenance. Their crawling robot allows technicians to safely and efficiently perform inspections, cleaning and repairs in high places. “We had a great experience, and as we made new friends this week it started to feel like a real family,” said Janis Putrams, CTO and co-founder of Aerones. “We’re excited to work together with AkzoNobel to improve the generation of renewable energy — we would like to surprise our clients with a solution that combines our technology and AkzoNobel’s unique expertise in protective coatings.”
SprayVision: From the Czech Republic, SprayVision brings a data-driven approach to optimizing spray application of paint, offering customers full control over the process. The solution helps to reduce environmental impact by saving material and improving quality. “What a great week, it exceeded our expectations,” said Petr Jahn, CEO of SprayVision. “We learned a lot from connecting with the other startups and getting such challenging questions from the AkzoNobel team. They’ll introduce us to completely new fields we’re not currently active in, which represent big opportunities for collaboration.”
“Collaborative innovation is truly transforming the paints and coatings industry,” said Klaas Kruithof, AkzoNobel’s Chief Technology Officer and Chair of the Paint the Future jury. “I’m looking forward to mixing the skills of these passionate entrepreneurs with our knowledge of paints and coatings. Together, we’ll bring our customers new solutions that go beyond imagination.”
This is AkzoNobel’s second global startup challenge, following its industry-first predecessor in 2019. Regional startup challenges have since been held in Brazil (2020), China (2021) and most recently in India (2022).
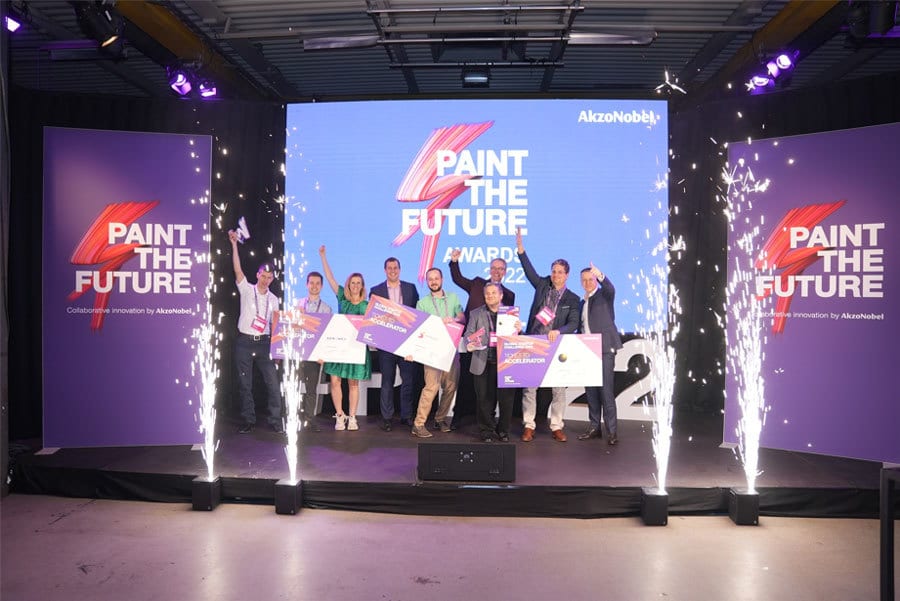
Winners of the Paint the Future global startup challenge. Photo courtesy of AkzoNobel.
BASF Confirms Climate Targets, Initiates Steps to Reduce Product-Related Emissions
LUDWIGSHAFEN, Germany – In an update for investors and financial analysts, BASF confirmed that by 2030 it aims to reduce its greenhouse gas emissions by 25% compared with 2018, and is maintaining its goal of net zero emissions globally by 2050. On its path to reducing global emissions to 16.4 million metric tons by 2030, BASF is publishing an annual CO2 emissions forecast for BASF Group as part of its outlook, with a corridor of plus or minus 0.5 million metric tons.
In 2021, BASF reduced CO2 emissions by around 3% compared with 2020 despite significantly higher production volumes. To a large extent this was due to the increased use of renewable energy. Switching power to renewable energy will be the main driver of emission reduction until 2025. In 2021, renewables accounted for 16% of BASF Group’s global power demand. By 2030, the company projects that 100% of its 2021 global power demand will be obtained from renewable sources.
To cover its demand for renewable energy, BASF is pursuing a make-and-buy strategy. This includes investing in its own renewable power assets and purchasing green power from third parties. In 2021, BASF purchased a stake in Vattenfall’s wind farm Hollandse Kust Zuid (HKZ). Once fully operational, it will reportedly be the world’s largest offshore wind farm, with a total installed capacity of 1.5 gigawatts. The project is expected to become fully operational in 2023. BASF has also signed 25-year power purchase agreements (PPAs) with ENGIE and Ørsted for the supply of significant amounts of renewable electricity from wind and solar power in Europe. In the United States, BASF has concluded long-term supply contracts for wind and solar power for its Freeport and Pasadena sites. In China, BASF has signed agreements with suppliers for the purchase of renewable power for its new Verbund site in Zhanjiang.
At BASF’s site in Ludwigshafen, Germany, the company is developing new technologies and implementing a new steam supply concept. Currently, about 50% of the steam demand at the Ludwigshafen site is based on steam generation processes that produce CO2 emissions. A new approach is to generate steam with electricity. BASF is working with Siemens Energy on a project in the acetylene plant that uses heat pumps and vapor recompression to upgrade waste heat such that it can be used as steam for the steam grid of the site. The integration of this heat pump project will enable not only the production of around 60 metric tons of steam per hour but will also avoid around 160,000 metric tons of CO2 emissions per year and reduce the annual consumption of cooling water by more than 20 million cubic meters. The planned start-up for the use of this technology is in the second quarter of 2024. The project also serves to collect day-to-day operational experience and to simplify the rollout to other sites in the future.
Another project pursued at the Ludwigshafen site is the development of an electrically heated steam cracker furnace. Currently, cracker furnaces are heated with gas and produce about 1 metric ton of CO2 per metric ton of olefin. BASF has signed an agreement with SABIC and Linde to develop and pilot electrically heated steam cracker furnaces. The project for a multi-megawatt pilot plant in Ludwigshafen is progressing as planned and is on track to start up in 2023, subject to a positive public funding decision. For the CO2-free production of hydrogen, BASF is developing new processes such as methane pyrolysis.
BASF’s Verbund site in Antwerp is the largest chemical production site in Belgium and BASF’s second-largest Verbund site after Ludwigshafen. BASF aspires to reduce emissions at the site from 3.8 million metric tons in 2021 to close to net zero by 2030. This could become possible by importing green power from offshore wind parks in combination with the deployment of new, low-emission technologies and a planned large-scale CCS project in the port of Antwerp. If this goal is realized, the Antwerp site could become the first petrochemical site to approach net zero in 2030. Given the short time period involved, these efforts constitute a challenge, and BASF reports that support is needed from politicians in setting the right framework conditions.
BASF’s site in Zhanjiang, China, will become the company’s third-largest Verbund site. An advanced Verbund concept and the use of renewable energy will play the key role in significantly lowering the site’s CO2 emissions compared to a gas-powered petrochemical site. Replacing fossil-fuel energy by electricity from renewable sources is a main lever. BASF recently signed a second framework agreement over 25 years with the State Power Investment Corporation Limited (SPIC) under the new renewable energy trading rules in Guangdong province, China, to purchase the renewable electricity supply for the next phases of the Zhanjiang Verbund site in Guangdong province.
Serving as a prototype for the transformation of its mid-sized sites, BASF Schwarzheide GmbH and enviaM established a joint venture for a solar park that has an expected electricity production of 25 gigawatt hours per year, about 10% of the site’s current annual electricity demand. It will be the first major solar power plant in which BASF is directly involved.
BASF believes that end consumers will drive the transformation towards net-zero and low-PCF consumer products since they are increasingly requesting alternatives to conventional consumer products and want to make a personal contribution to reducing emissions. Many of BASF’s customers are eager to reduce the carbon footprint of their products to reach their own emission goals, which requires a new level of transparency. BASF has developed an in-house digital solution to calculate the PCFs for approximately 45,000 sales products. In this tool, BASF currently has to use industrial averages and values from commercial databases as the basis to include upstream Scope 3 emissions. In order to create more transparency on Scope 3 emissions, BASF is working with suppliers to improve the data for the raw materials it purchases from them. BASF is also sharing knowledge of evaluation and calculation methods, contributing to the standardization of PCF calculations.
“There is a brutal war raging in Europe with far-reaching consequences for both people and the economy. Nevertheless, we must not lose sight of the greatest global challenge of our time — climate change,” said Dr. Martin Brudermüller, Chairman of the Board of Executive Directors of BASF SE. “Across BASF, we are working intensively to implement a large number of projects to further reduce our CO2 emissions significantly and achieve our ambitious climate targets. By cooperating with suppliers of raw materials we are also taking steps to reduce our product-related emissions. In this way, we are driving forward our transformation and supporting customers in their efforts to reduce emissions in their product portfolios.”
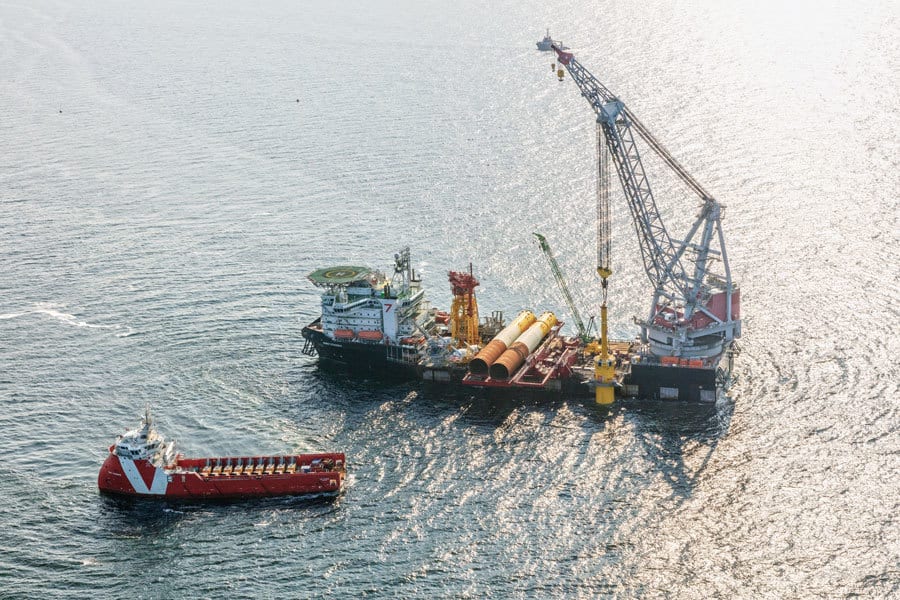
Construction work for the Hollandse Kust Zuid offshore wind farm in the North Sea is progressing. Credits: Flying Focus BV.
PPG Marks 300 Years of Operations in The Netherlands
AMSTERDAM – PPG is marking 300 years of operations in the Netherlands and the anniversary of the SIGMA COATINGS™ brand by PPG, one of the leading architectural coatings brands in Europe. The anniversary celebrations began April 6, which is Dutch National Painters’ Day, with PPG staff visiting thousands of painters across the country to personally thank them for their work.
Image courtesy of PPG.
Today, PPG has six sites and 61 stores in the Netherlands, and employs 1,200 people. The company offers a portfolio of leading architectural coatings brands in the country, including Sigma Coatings products by PPG, HISTOR™ coatings by PPG and RAMBO™ coatings by PPG. The Sigma Coatings brand by PPG is available in 13 countries across Europe and the Middle East.
“We are pleased to celebrate such a proud history of paints and coatings innovation in the Netherlands,” said Justus Tichelman, PPG General Manager, Benelux Trade, Architectural Coatings. “What started with grinding pigments in a windmill is now a core part of PPG and a key contributor to our purpose of protecting and beautifying the world.”
In 1722, Jan Pieterszoon Schoen set up a windmill in Westzaan, the Netherlands, to grind pigments for local painters. The company he founded, Pieter Schoen & Sons, later moved into paint manufacturing. It was one of three companies that merged in 1972 to form Sigma Coatings, marking the start of the Sigma Coatings brand. The company further expanded to become SigmaKalon, which PPG acquired in 2008.
“Schoen laid the foundation for a company that has truly stood the test of time,” said Tichelman. “His company was one of the first to offer pigments and dyes commercially for paint makers and evolved to become one of the first international paint companies. It thrived with a focus on continuously responding to customers’ needs and changing market conditions — something that remains a core value for PPG.”
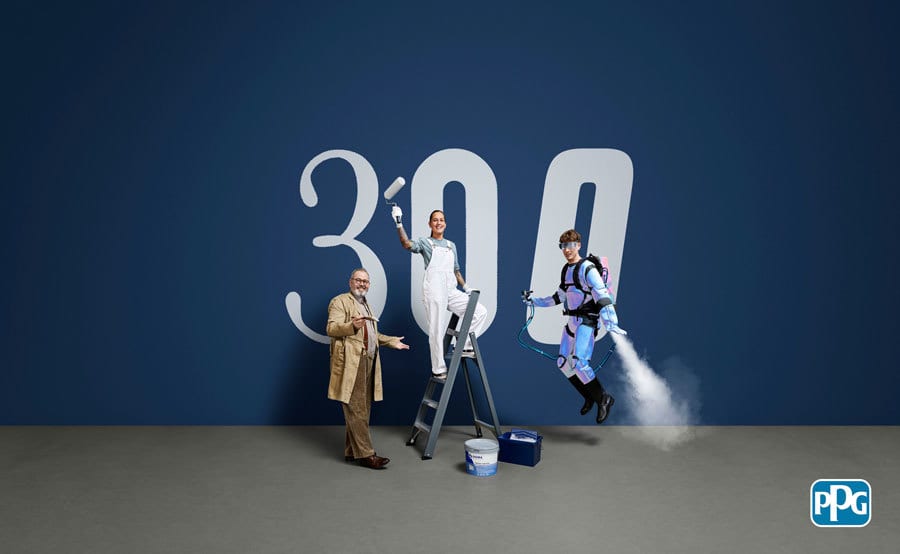
Nikkei Asia Recognizes FUSE Automotive Coloring System
COLUMBUS, OH – AERO Sustainable Material Technology announced that the FUSE Automotive Coloring System, known as the Ultra-Wide TOM Machine, won a grand prize at the 2021 Nikkei Superior Products and Services Awards from the Asian news magazine Nikkei Asia. Reported to be an environmentally sound alternative to the assembly-line process of traditional paint, the Ultra-Wide TOM Machine is an efficient system for coating automotive body panels and other exterior components by applying AERO’s film-based coatings.
The Ultra-Wide TOM Machine incorporates new Neo-TOM Thermoforming technology, which was developed by Fu-se Vacuum Forming Co. Ltd. (FVF) in Osaka, Japan. This recently developed process addresses the difficulties of traditional compressed air thermoforming where hollow parts (such as an automotive hood) cannot withstand the air pressure, resulting in deformation. With Neo-TOM, the film is heated and softened in a vacuum and placed close to the component to allow air to be introduced to the front side of the film, and then the air pressure difference between the inside and outside of the film causes the film to be attached to the component without deformation. Although this process has been previously utilized for automotive interior components, it had been difficult to apply films uniformly on large automotive parts until the advent of the FVF Neo-TOM process.
“This world’s largest Ultra-Wide TOM Machine using AERO’s environmentally sustainable film-based coating technology has the ability to uniformly coat large parts and therefore entire automotive vehicle bodies,” said Jim McGuire, CEO of AERO Sustainable Material Technology Inc. “The amount of electricity used can be reduced to one-third or less compared to the conventional method of painting and drying repeatedly.”
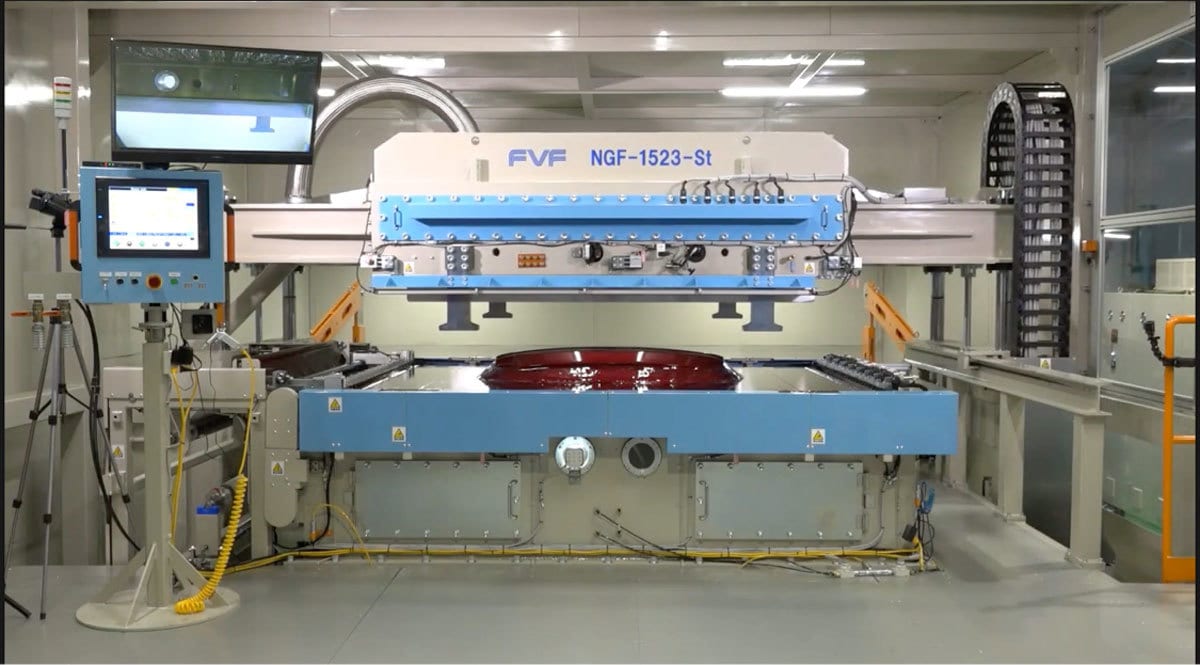
Photo courtesy of AERO Sustainable Material Technology Inc.
Sherwin-Williams Acquires Sika’s European Industrial Coatings Business
CLEVELAND – The Sherwin-Williams Co. announced it has completed its acquisition of the European industrial coatings business of Sika AG. The acquired business will become part of the company's Performance Coatings Group operating segment. Approximately 115 Sika employees will join Sherwin-Williams.
Sika's European industrial coating business manufactures and sells corrosion protection coating systems for high-value interior and exterior steel infrastructure, bridges, airport and rail, wind and energy, chemicals, power transmission, interior linings for oil and gas tanks, vessels, and pipework, and water and wastewater applications, along with fire protection coating systems to protect and preserve steel, wood and concrete building components. Sika's industrial coatings business is based in Germany with additional sales and technical support in Poland, Austria and Switzerland. Sales of the business were approximately $82 million for the year ended Dec. 31, 2020.
“This business brings us unique technology and additional manufacturing and services capabilities in line with our strategy of acquiring complementary, high-quality, differentiated businesses that support our growth and profitability targets,” said Sherwin-Williams Chairman and Chief Executive Officer, John G. Morikis. “The combination of customer focus, talented employees and similar cultures creates exciting prospects for continued growth and success throughout Europe and other regions across the world.”
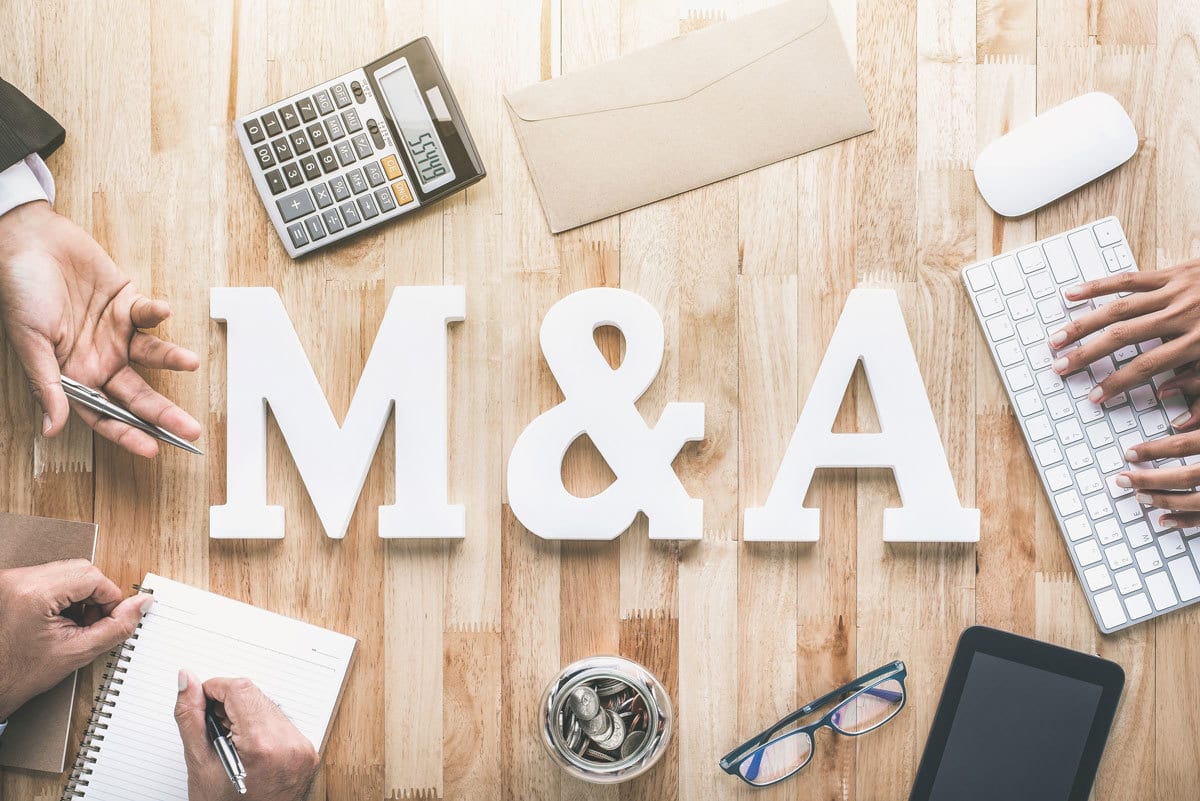
Atstock Productions, iStock/Getty Images Plus, via Getty Images
Advanced Polymer Coatings Announces Multi-Ship Deal with Shandong Shipping
AVON, OH – Coating manufacturer Advanced Polymer Coatings (APC) is gearing up production after signing a new deal with Chinese ship owner Shandong Shipping to supply a fleet of 50,000 DWT medium-range tankers with its MarineLINE protective cargo tank coating.
APC President David Keehan explained that the new agreement will begin in July 2022 and will again supply the New Times Shipyard. The latest vessels will also be chartered by Shell as part of Shell Project Solar. “To win repeat business from Shandong and Shell on this high-profile project is testament to the hard work and effort of all involved,” said Keehan. “Each ship has 20 cargo tanks, including two slop tanks, which require MarineLINE coating, along with application inspection, and full heat curing services. So, this will be an extensive job for our team working with the specialists at New Times Shipbuilding with whom we have developed a close working relationship.”
The new deal follows the successful completion of an earlier contract with Shandong in which APC applied MarineLINE to eight new 50,000 DWT MR product/chemical tankers, which will be chartered to Shell for its Shell Project Solar program. That deal saw APC supply MarineLINE to the New Times Shipbuilding Co. Ltd., at the Xingang Port in Jingjiang City. The project was completed in November 2021.
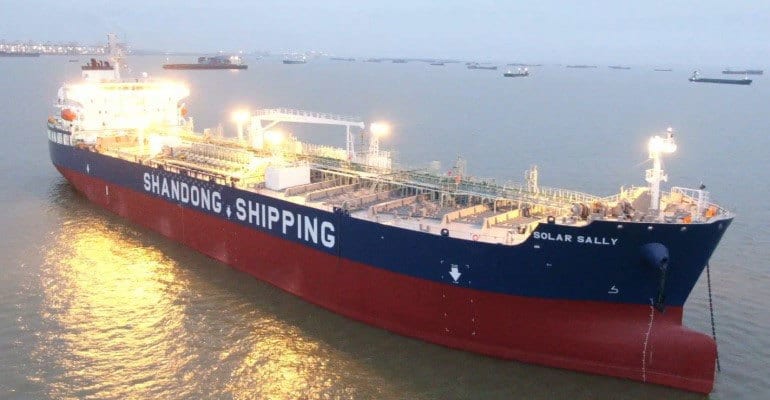
Photo courtesy of Advanced Polymer Coatings.