Ready to proof -- Clare 04/5/22
KJ proofed on 4/11 and sent corrections to Clare
CLJ revised on 4/11
KJ sent new correction on 4/13
Revised on 4/13 - Ready for author
KJ sent author corrections to Clare on 4/20
CLJ revised on 4/20 - clean
Amino Alcohol Dispersants for Waterborne Metal Coatings
Video: janiecbros, Creatas Video, via Getty Images
By Dr. Mark Langille, Customer Application Specialist, ANGUS Chemical Company, Buffalo Grove, IL
Waterborne metal coatings face challenging performance requirements, but as water-based technologies improve they are replacing an increasing number of solventborne coating systems. A growing sub-segment of the metal coatings market is direct-to-metal (DTM) coatings, which aim to meet the same performance criteria of a multi-coat system while reducing the application time, complexity and cost with a single coating. All waterborne metal coatings need to use the highest performing raw materials in their most effective manner to achieve their performance goals. In the case of a DTM coating, properties such as corrosion resistance and outdoor durability are critically important but must also be balanced with aesthetic requirements for high gloss and opacity. Here we demonstrate how to maximize the performance of waterborne acrylic metal coatings using amino alcohols as highly efficient dispersants for pigments.
The unique properties of ANGUS amino alcohols offer a multitude of benefits to waterborne formulations, including efficient pH control and enhanced formulation stability.1 The amino alcohol studied in this work, 2-amino-2-methyl-1-propanol (AMP), has a relatively low molecular weight and high pKa, making it a highly efficient pH control additive (Table 1). AMP is also VOC exempt by the U.S. EPA and by the Governments of Canada and South Korea, and can therefore be used to make waterborne industrial coatings that meet low- and zero-VOC regulations.2 However, one of the critical chemical interactions that these materials have with ingredients in waterborne coatings is their strong interaction with pigment surfaces, which makes them highly efficient and effective dispersants for pigments. The amino functional group of AMP can have strong interactions with negative surface charges on pigment surfaces, such as titanium dioxide, clays and talcs, among other extenders and colored pigments.3
TABLE 1 ǀ Physical properties of 2-amino-2-methyl-1-propanol.
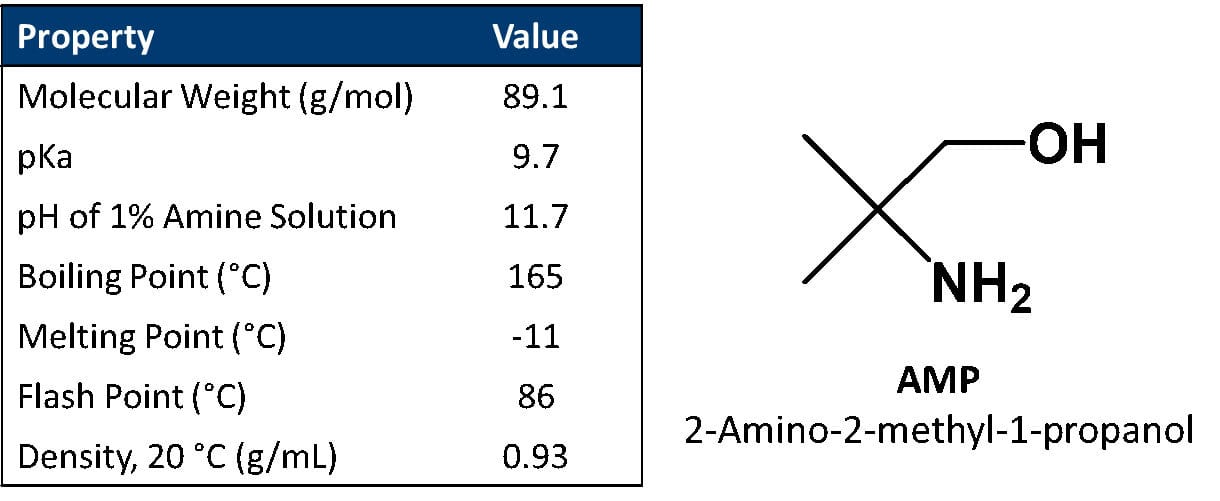
In this article we demonstrate how the dispersancy properties of AMP can be used to improve a multitude of performance attributes of waterborne acrylic DTM coatings, including viscosity stability, opacity, gloss, weatherability and corrosion resistance. These performance improvements are demonstrated to be extremly robust across different formulations, as demonstrated by results in waterborne metal coatings prepared from three different acrylic resins. Overall, these results speak to the generality of this formulating strategy for improving performance of waterborne industrial coatings with amino alcohol dispersants.
Experimental Design
In the following experiments two primary variables were evaluated: (1) the use level of AMP as a dispersant and (2) the resin chemistry. Three use levels of AMP were evaluated, each in three different resin systems for a total of nine paints. Amino alcohols are highly efficient dispersants and can partially replace the primary polymeric dispersant, with higher levels of amino alcohol enabling greater reductions in the primary dispersant level. While a polymeric dispersant can have a significant impact on the gloss, opacity and corrosion resistance of metal coatings, so too can an amino alcohol dispersant. The following three dispersant packages were evaluated, with the specific grind formulations shown in Table 2.
- A control formulation using a supplier-recommended dosage of primary dispersant (1.5% active primary dispersant on pigment solids) and no AMP.
- A formulation containing 0.1% of AMP on total formulation weight as a replacement for 30% of the primary dispersant (1.0% active primary dispersant on pigment solids and ~ 0.5% of AMP on pigment solids).
- A formulation containing 0.15% of AMP on total formulation weight as a replacement for 50% of the primary dispersant (0.75% active primary dispersant on pigment solids and ~ 0.75% AMP on pigment solids).
TABLE 2 ǀ Grind formulations containing 0.00%, 0.10% and 0.15% of AMP on total formulation weight as a replacement for 0%, 30% and 50% of the primary dispersant, respectively.
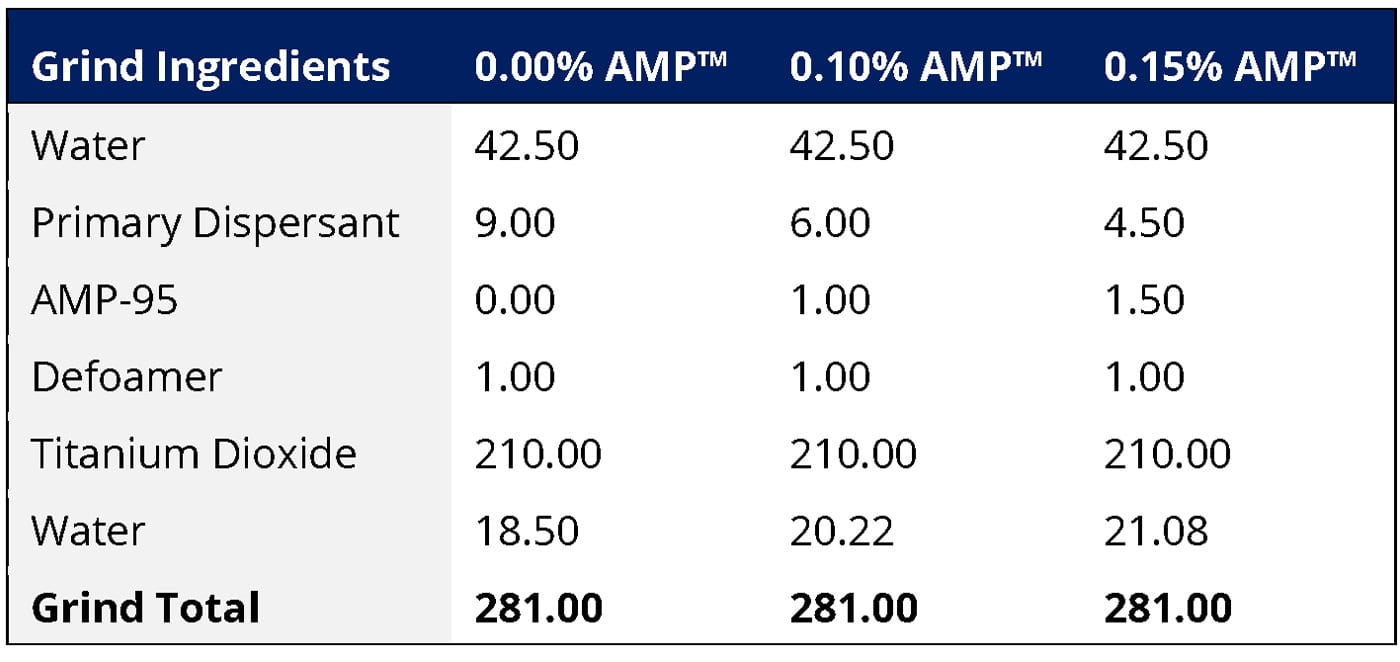
For the second experimental variable, three acrylic resins designed for waterborne metal coating applications were selected from three different suppliers, referred to as Resin A, Resin B and Resin C. Descriptions and physical properties of the resins are shown in Table 3. All three resins are based on styrene-acrylic chemistry, but Resin A can interact with pigment surfaces, which can improve the pigment particle distribution in the film. Resin B and C are non-pigment interacting but designed for 150 g/L and 50 g/L VOC formulations, respectively.
TABLE 3 ǀ Description and physical properties of acrylic resin chemistries.
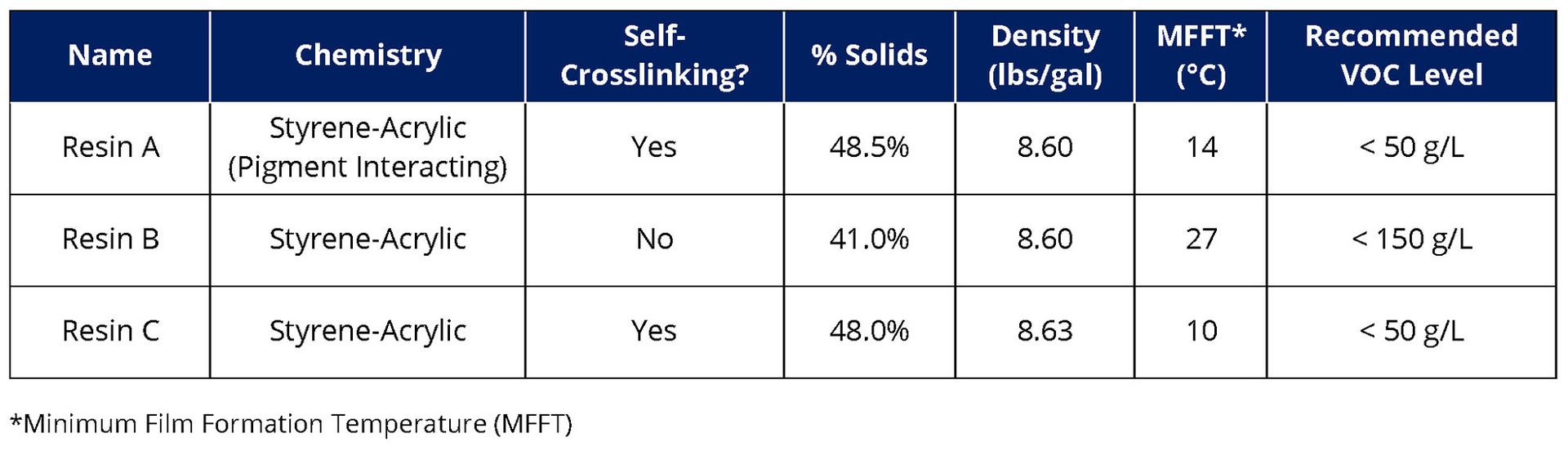
The three different resins were evaluated on an equal solids basis in a waterborne semi-gloss DTM formulation at 17.5% PVC and 36% volume solids. The same slow-evaporating coalescent was used in each formulation, although the coalescent level was adjusted for the target VOC level of each resin. The rheology modifier levels were adjusted for each resin system to target similar viscosity profiles. The formulations were otherwise not further optimized. The let-down ingredients are shown in Table 4. It is important to note that although AMP is often used as a pH control additive in the let-down, all the formulations studied in this work were neutralized in the let-down with ammonia to their target pH. The differences in coating performance are therefore due to the use of AMP as a dispersant in these formulations.
TABLE 4 ǀ Let-down formulations used for each of the three resins.
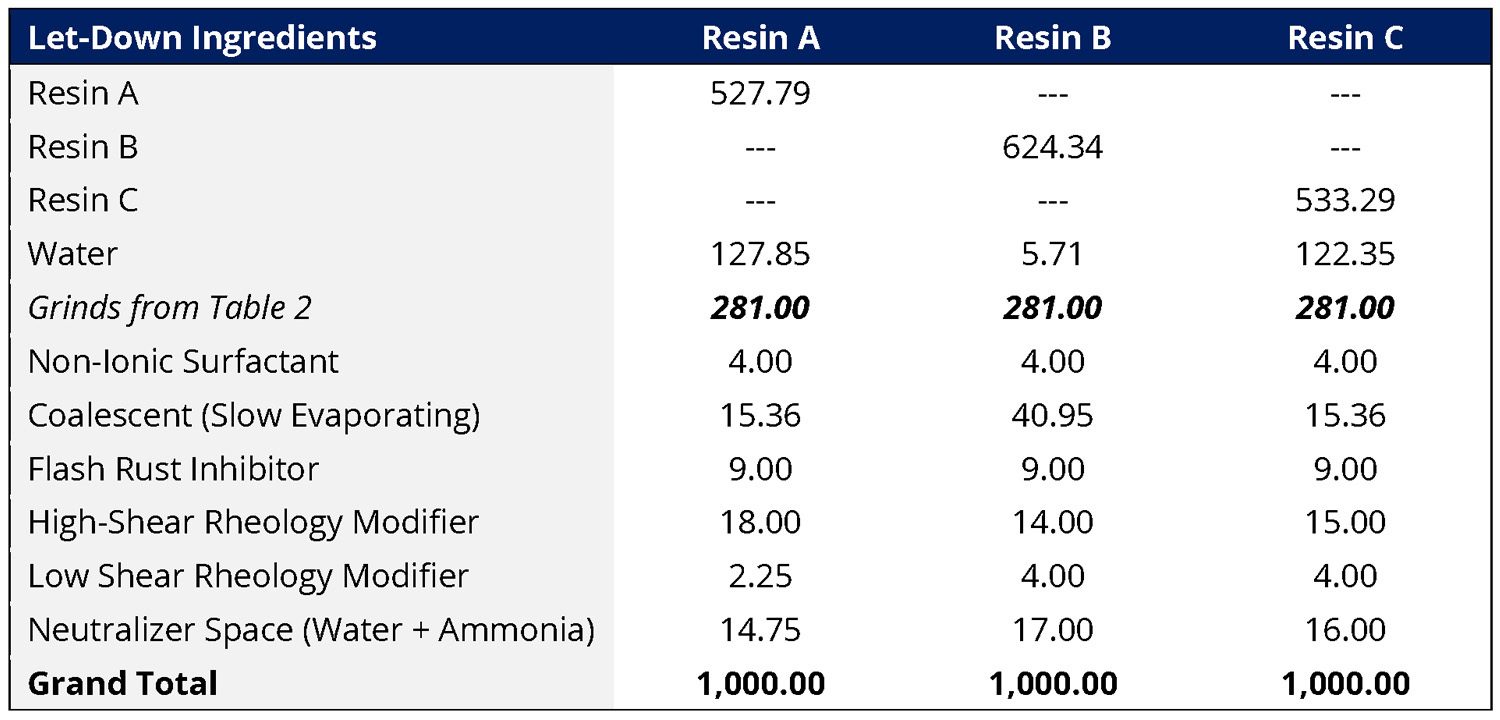
Results and Discussion
The viscosity of the paints, stored at room temperature, were monitored over time, including an initial measurement the same day that the paints were made followed by subsequent measurements overnight, after one week and after four weeks. ΔKU values versus the initial off-mill measurements are plotted in Figure 1.
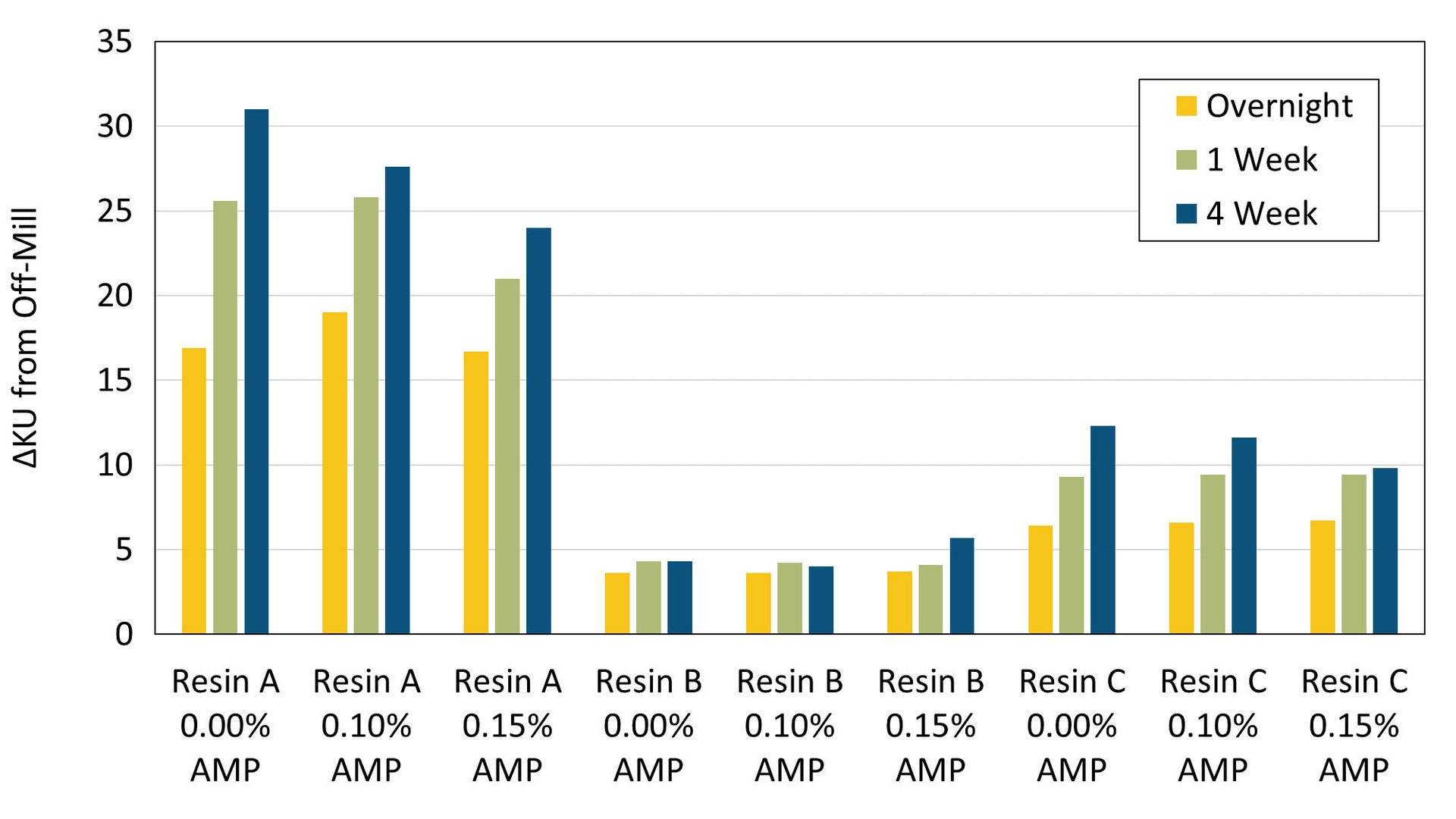
FIGURE 1 ǀ Viscosity stability after an overnight, one-week and four-week equilibration time.
Viscosity rise over time was most significant for Resin A, and much less so for Resin B and Resin C. The large viscosity rise seen with Resin A is likely due to potential ongoing interactions between the resin and the titanium dioxide pigments. In general, paints formulated with AMP show more stable viscosity over time, with formulations containing Resin A and Resin C showing the best viscosity stability at the highest use levels of AMP.
Contrast ratio and gloss values were measured for each paint on Leneta opacity charts. Regardless of resin system, AMP shows clear advantages for improving both hiding and gloss, with the highest values of each measured for samples prepared with 0.15% AMP in the grind. Resin A had the highest initial contrast ratio (Figure 2) and gloss values (Figure 3), which were expected from the resin-pigment interactions that can take place, yet the use of AMP improves these performance properties even further. In non-reactive resin systems, the improvements to hiding and gloss are even more significant, with the highest use levels of AMP enabling the greatest improvements for Resin B and Resin C. Gloss values on steel or aluminum substrates also show the same trend as on the Leneta opacity chart results reported here, with higher levels of AMP yielding higher gloss values, although this data is not shown.
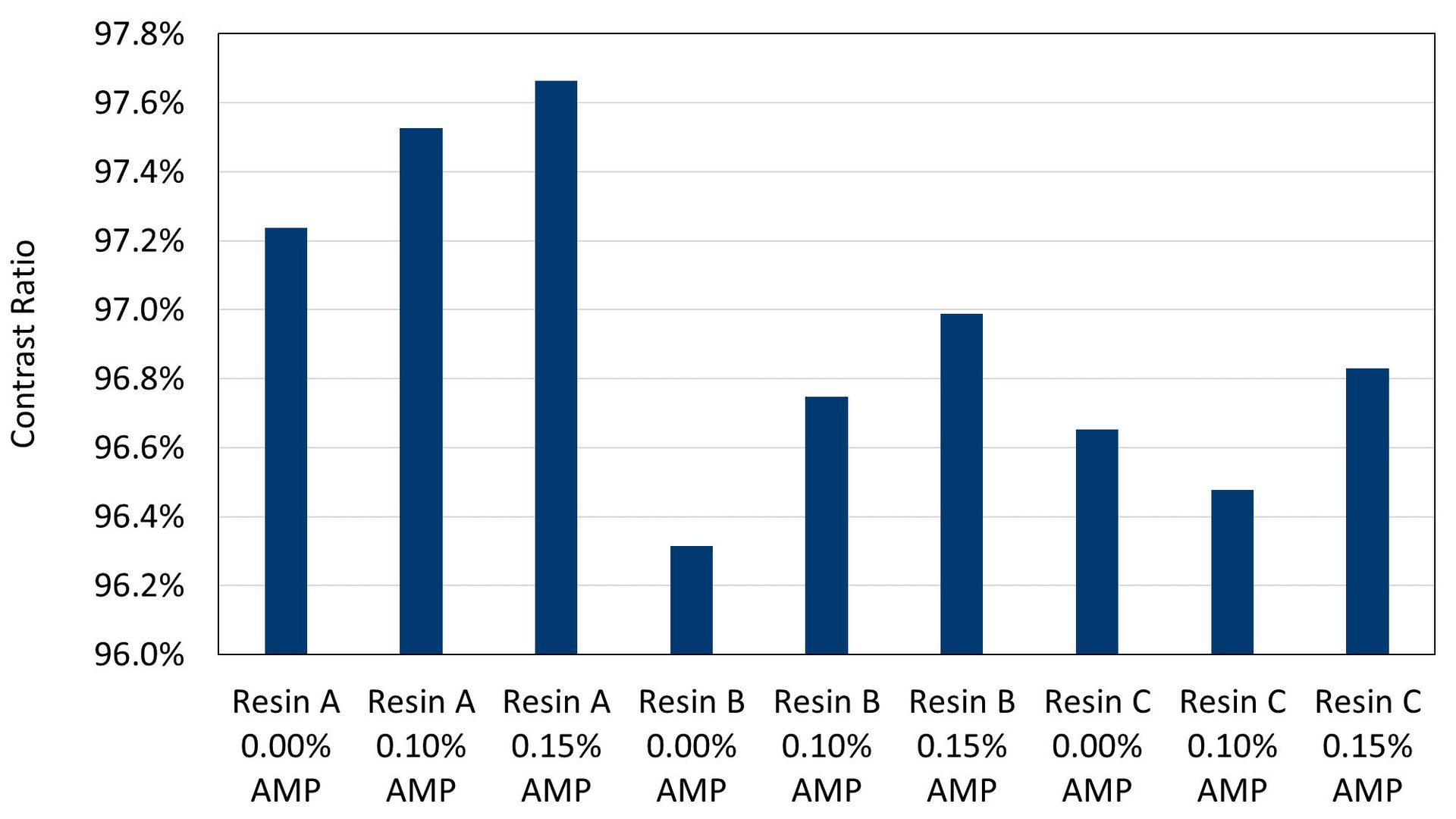
FIGURE 2 ǀ Contrast ratios measured on opacity charts.
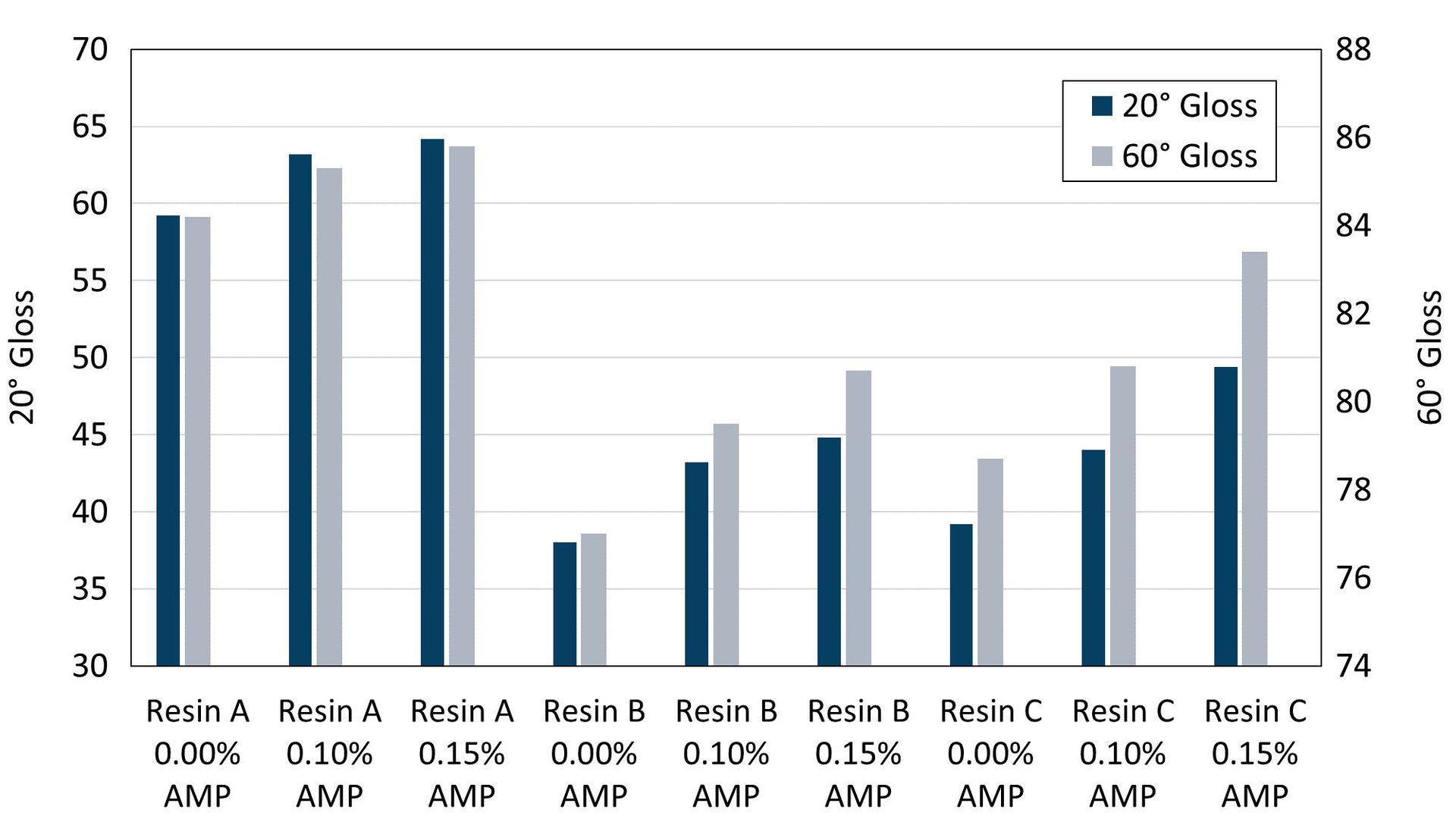
FIGURE 3 ǀ Gloss on opacity charts.
König hardness values were measured over a four-week period (Figure 4). The formulation containing Resin B had higher hardness values than the others, which would be expected based off its higher minimum film formation temperature and higher coalescent demand. Fluctuations in hardness over time can be attributed to varying ambient temperature and humidity levels in the lab. The resin had a much more significant impact on hardness values than AMP, but generally, formulations containing AMP are found to have similar or very slightly lower König hardness values than those formulated without AMP.
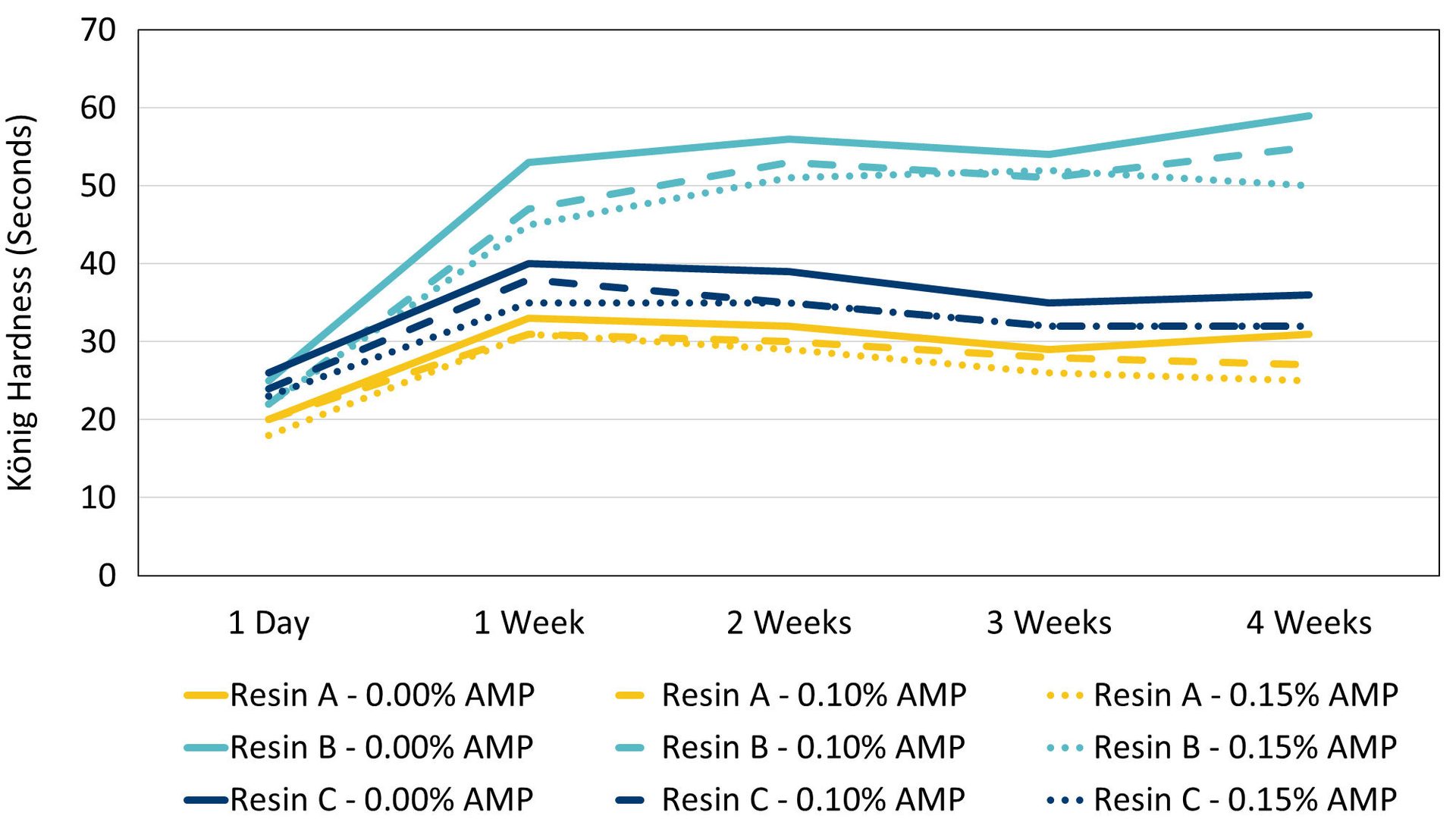
FIGURE 4 ǀ König hardness values over four weeks.
Gloss retention was measured for six weeks under accelerated weathering conditions. Immediately apparent in the data is the large difference in performance between resin systems, with Resin A maintaining much higher gloss values over the six weeks (Figure 5). The initial gloss of samples containing AMP are higher than those that do not contain AMP. For Resin A and Resin B this higher initial gloss is simply maintained throughout the experiment, although Resin A holds its initial gloss value better than Resin B. For Resin C, the gloss difference between samples with and without AMP increases during the experiment, with AMP enabling better gloss retention of that formulation. Although these formulations may not be fully optimized for gloss retention, the overall trend observed is that AMP can both increase the initial gloss of a formulation and help to better maintain gloss in some systems during an accelerated weathering test.
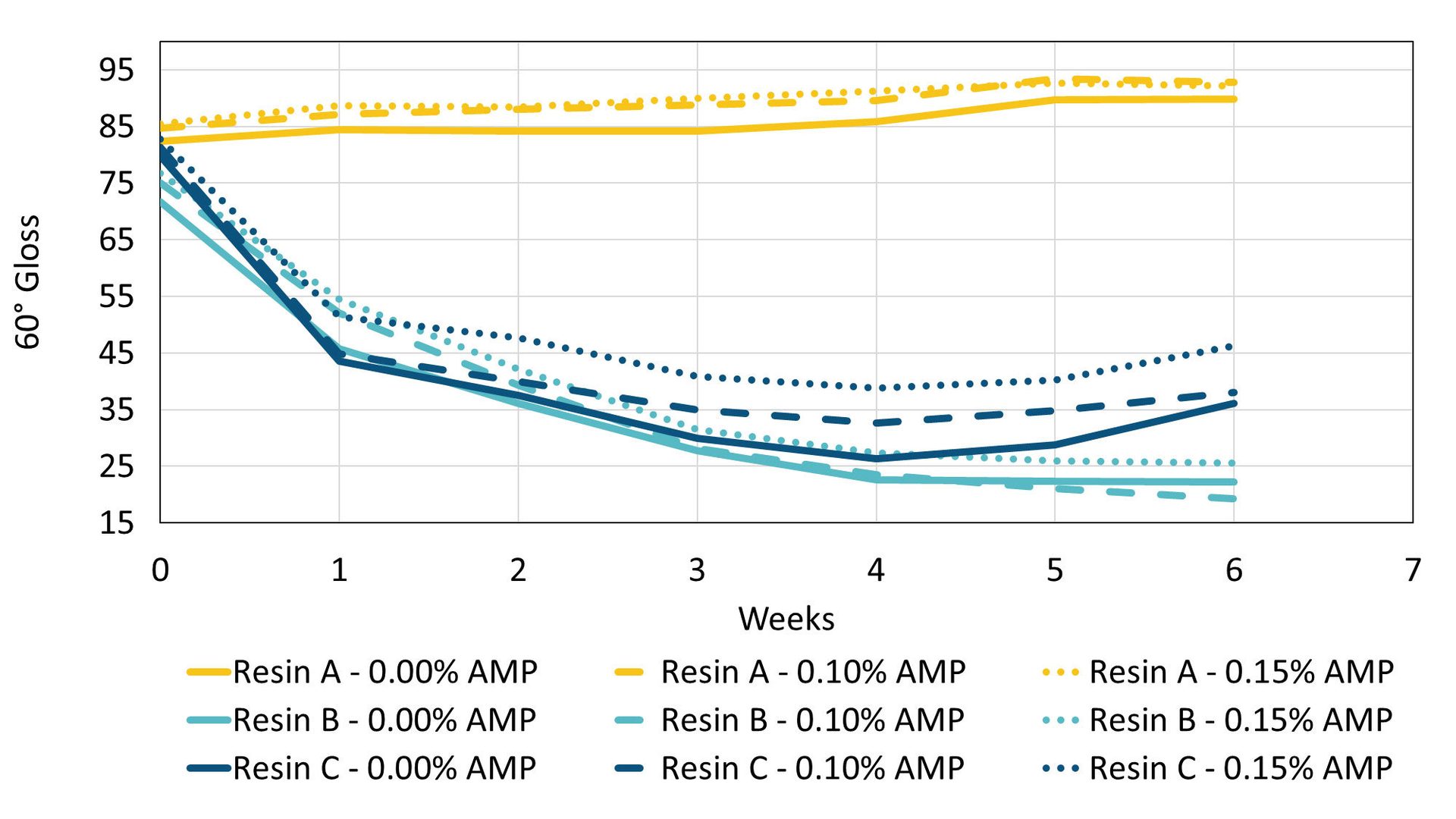
FIGURE 5 ǀ Gloss retention during accelerated weathering testing.
Early water resistance was also measured for these coatings by drying wet films for 2 hours prior to submersion in tap water for 24 hours. Early water resistance values, reported as a weight percent of water absorbed on dry film weight, were found to be highly formulation dependent (Figure 6). Resin B had the lowest performance for early water resistance, but this would be expected from the much higher level of slow-evaporating coalescent in the formulation compared to the others. However, the use of AMP can enable a significant reduction in water uptake, as seen for formulations based on Resin B and Resin C. This improvement to early water resistance could be the result of a better distribution of pigment in the film and can also be partially driven by a reduction in the primary dispersant level enabled by AMP. The carboxylic acid functionality of polymeric dispersants can make them highly water sensitive, and reductions in the level of water-sensitive materials in a coating formulation are known to improve certain properties including early water resistance.
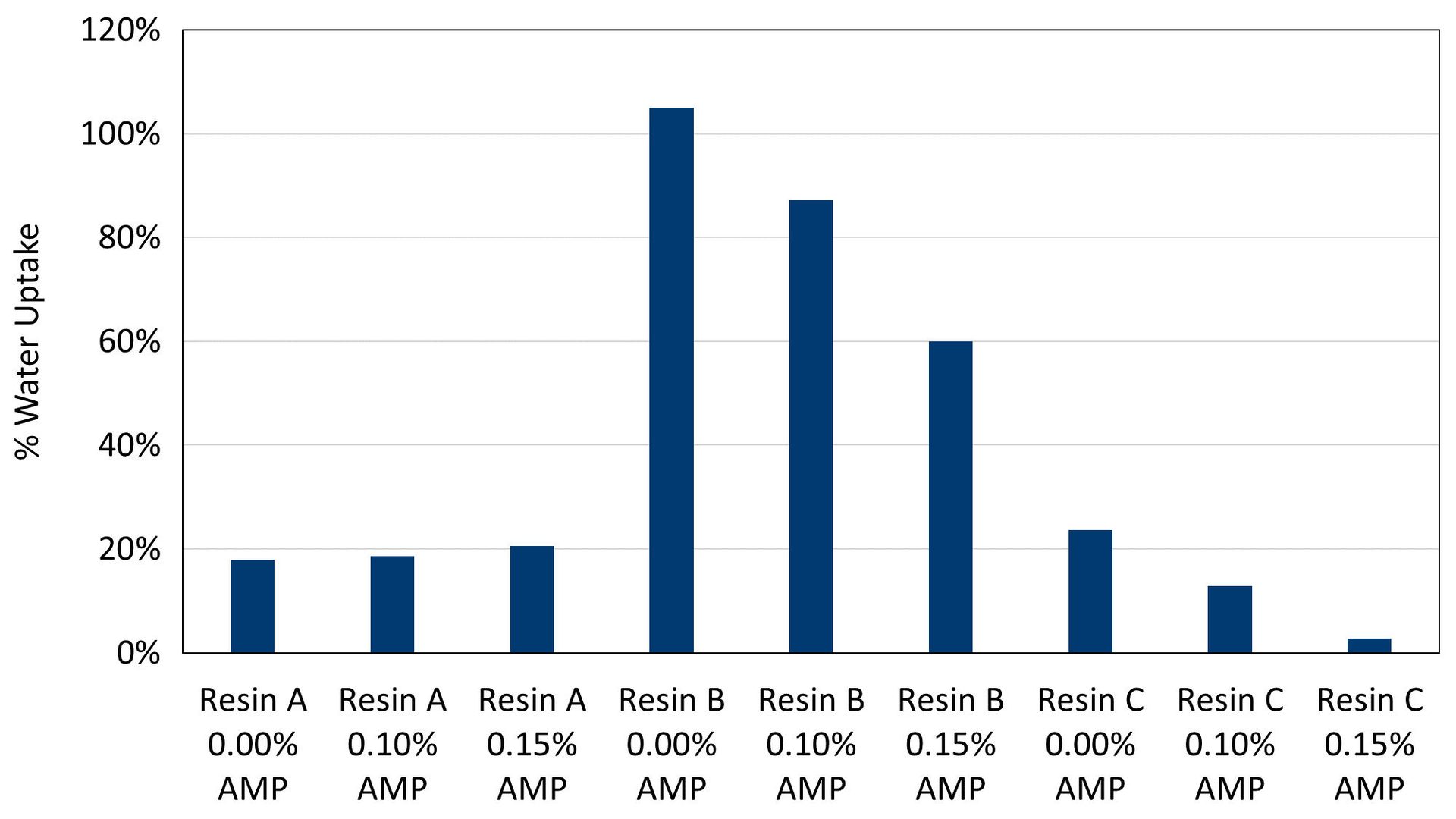
FIGURE 6 ǀ Two-hour early water resistance water update values.
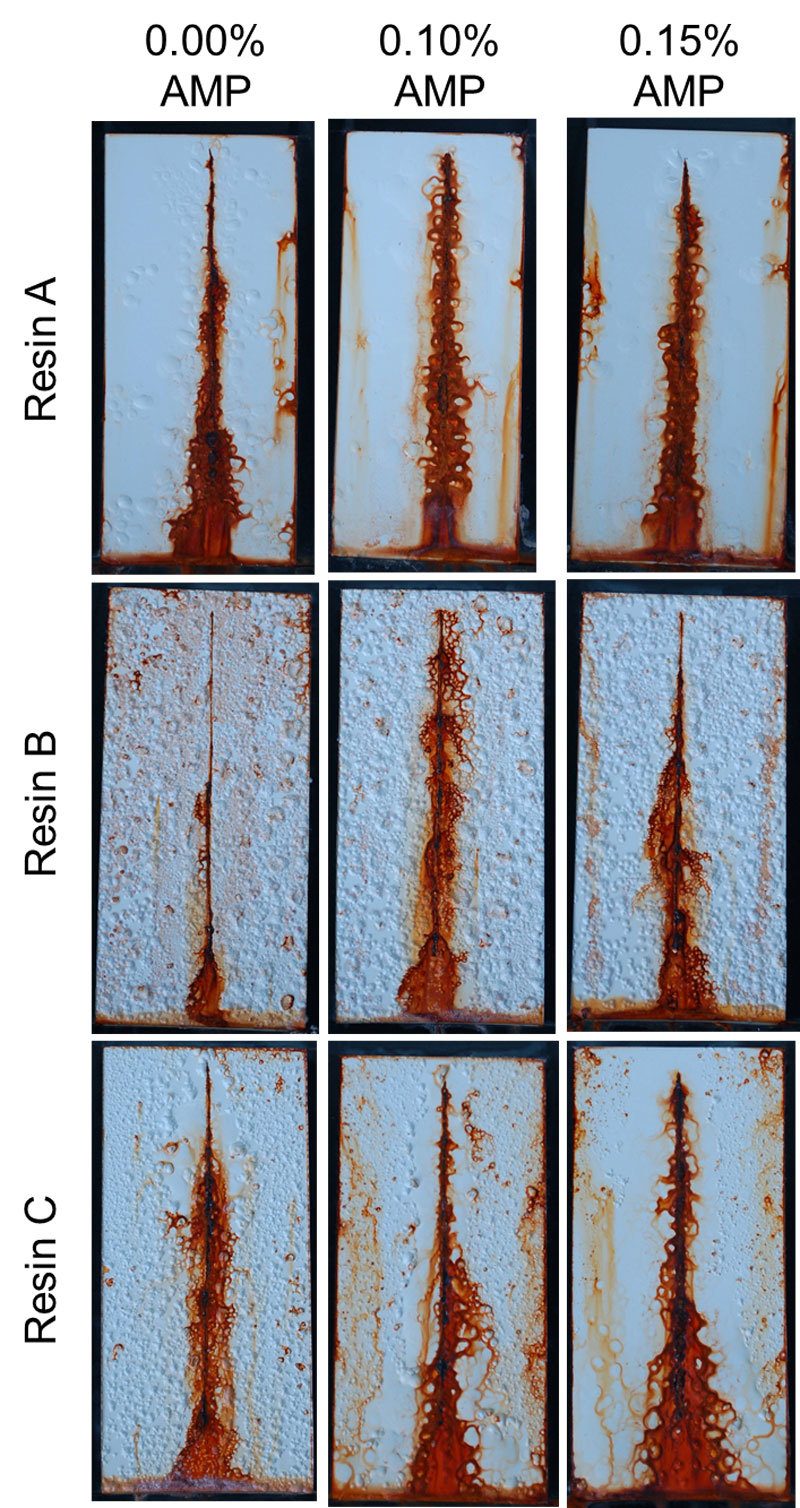
FIGURE 7 ǀ Corrosion resistance testing after one week of exposure to salt fog.
Coatings were also evaluated for corrosion resistance by the ASTM B117 test method. Dry film thicknesses of approximately two mils were applied to cleaned cold-rolled steel panels and exposed to a salt fog for 1 week (Figure 7). The resin chemistry has a definite influence on corrosion resistance results, but so does the use of AMP. Differences are relatively small, but there is a trend towards better corrosion resistance with higher use levels of AMP in Resin A and Resin C formulations. Overall, most improvements to corrosion resistance with AMP are found around reductions to the number of blisters and in some cases reductions to the amount of rust staining observed.
Conclusions
Many of the performance challenges faced by waterborne industrial coatings are related to barrier and optical properties, which are both critically dependent on achieving an optimized pigment dispersion. Amino alcohols such as AMP are powerful formulating tools for achieving high-quality pigment dispersions through their strong interaction with pigment surfaces. The potential benefits of an optimized pigment dispersion with AMP are two-fold. AMP can help to better disperse pigments through the dry film, which can directly improve optical and barrier properties of the coating, as illustrated in Figure 8. Additionally, the high dispersing efficiency of AMP allows for significant reductions in the level of primary dispersant (by 30-50%), which can further improve water sensitivity properties of the film, such as shown here by improvements to early water resistance.
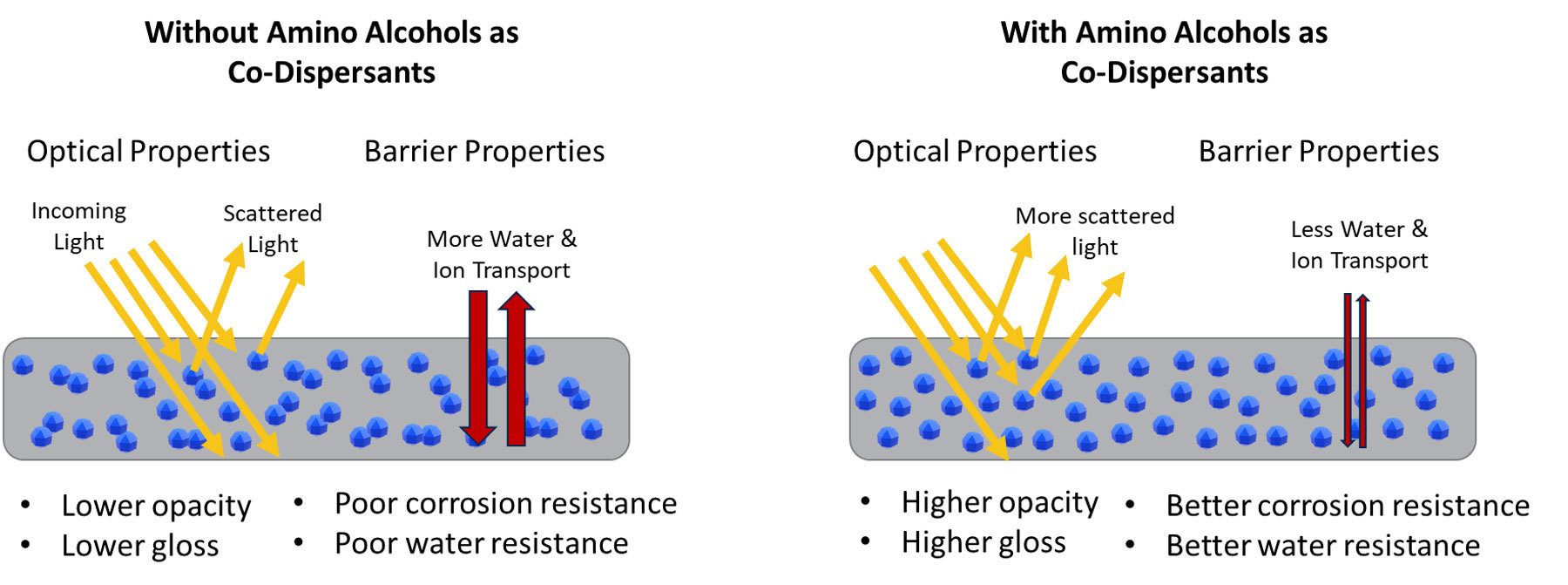
FIGURE 8 ǀ Scheme depicting performance improvements made possible by amino alcohol dispersants.
The use of AMP as a dispersant in the grind of waterborne metal coatings can improve a range of performance properties, including enhancements to paint stability, opacity, gloss, weatherability, early water resistance and corrosion resistance. Importantly, it was also demonstrated that these improvements are robust across different resin chemistries and formulations. While each of these resins exhibits a different overall balance of properties, the ability of AMP to improve properties such as paint stability, opacity and gloss are quite consistent across all the formulations.
The use of 0.10-0.15% of AMP on total formulation weight in the pigment grind can enable the removal of 30-50% of the primary dispersant. Although not demonstrated in this article, other possible formulation optimizations enabled by AMP can include reductions in surfactant levels by 25% and reductions in flash rust inhibitor levels by 25%-50% due to the wetting and anti-corrosive properties of amino alcohols, respectively. Taken together, these formulation optimizations can help reduce the total amount of water-sensitive material in the formulation, thereby further enhancing coating performance. Amino alcohols such as AMP are effective multifunctional formulating tools that can help formulators design and optimize waterborne industrial maintenance coatings that meet today’s demanding performance expectations.
Experimental Methods
Standard laboratory practices were followed for paint preparation and testing. Paint viscosity stability was monitored for four weeks at room temperature. Contrast ratios and gloss values are reported for 3-mil wet film thickness drawdowns on Leneta opacity charts. König hardness measurements followed ASTM D4366-16 for 3-mil wet film thickness drawdowns on aluminum panels. Gloss retention during QUV accelerated weathering followed ASTM D4587-11. 6-mil wet film thickness drawdowns on aluminum panels were dried for 7 days prior to exposure to cycles of 8 hours UV exposure followed by 4 hours of condensation and monitored weekly for changes to gloss. Corrosion resistance was measured following ASTM B117 for 2-mil dry film thickness samples on cold rolled steel panels. Early water resistance was measured by performing 3-mil wet film thickness drawdowns on aluminum panels. The panels were dried for 2 hours at ambient conditions before submerging completely in tap water for 24 hours. Water uptake is reported as a weight percent of water absorbed on total dry coating weight. The author can be contacted at mlangille@angus.com for additional experimental details or for supporting data mentioned but not published here.
References
1 Severac, R.; Fernandes, Y. Painting a More Stable Picture. European Coatings Journal. 2018, 6, 2018, 18-21.
2 Troester, L.; Brutto, P.; Peera, A. The Journey to VOC Exemption. Paint & Coatings Industry. Jan. 2015.
3 Severac, R.; Fernandes, Y. Improving Pigment Dispersion and Paint Stability with Versatile Amino Alcohols. Coatings World. Sept. 2019, 132-135.