Ready to proof -- Clare 04/5/22
KJ proofed on 4/13 and sent corrections to Clare
CLJ revised on 4/13
Ready for author - clean
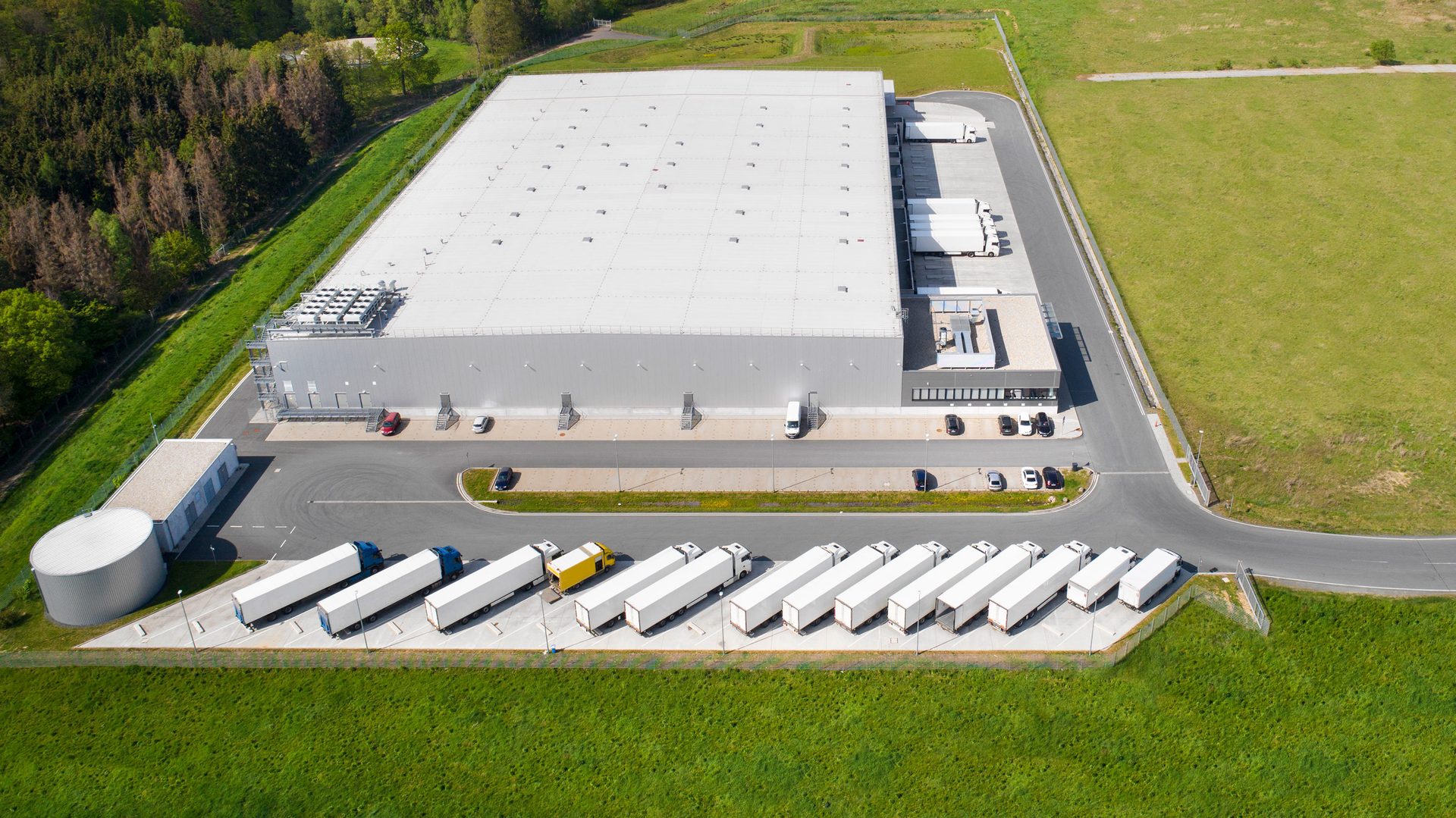
Photo: ollo, E+, via Getty Images
Dirt-Pickup Resistance in
Low-Tg Elastomeric Coatings
By Alejandra Hernandez and Robert Sandoval, Ph.D., EPS — Engineered Polymer Solutions
Maximizing dirt-pickup resistance (DPUR) is a key requirement for many exterior coatings. For example, in roof coatings, in addition to aesthetic considerations, maintaining a dirt-free coating can result in significant savings on energy costs, since a white coating will not absorb as much solar energy versus a coating that is soiled.
While it is generally known that higher glass transition temperature (Tg) resins impart improved DPUR due to a harder film that is formed, stricter VOC regulations have resulted in the use of lower Tg resins in traditional exterior architectural coatings. This has limited the extent to which high-Tg resins can be used, as formulators generally desire a single national formula that conforms to the widest range of regulations from various jurisdictions.
For elastomeric coatings (e.g., acrylics and silicones) that require the use of soft, low-Tg polymers, achieving acceptable DPUR is even more challenging, since higher Tg resins cannot be utilized. For acrylic coatings, this commonly results in reformulation by including special additives or adjusting other aspects of the coating formulation, such as the pigment volume concentration (PVC), which may not be acceptable depending on the application or required performance. Another method known in the art to improve DPUR is the incorporation of benzophenone into the resin or coating formulation. Benzophenone is activated by UV light and abstracts a hydrogen from the acrylic resin. Crosslinking can then occur between radicals at the surface of the coating, resulting in a hard film at the surface, thus improving DPUR. There are several concerns with the use of benzophenone. Among other things, it may trigger certain labeling requirements or additional disclosures in a safety data sheet. Benzophenone is also considered a VOC according to the ASTM D-6886 testing protocol.
In this study, formulation techniques are compared to resin technology that incorporates DPUR without requiring coating reformulation, particularly in systems with a measured Tg (via differential scanning calorimetry) of less than -10 °C. Additives such as fluorosurfactant and wax are examined, along with modification of the coating PVC. Finally, coating formulations developed with an acrylic resin that has a measured Tg as low as -28 °C and incorporates this DPUR technology is shown to have excellent DPUR in accelerated laboratory testing and natural exterior exposure testing, compared to similar Tg resins without this technology, and compared to resins that utilize benzophenone.
Experimental
A generic elastomeric coating formulation was used for the formulations in this study, according to Table 1. For PVC modification, the ingredient levels were modified to achieve the desired PVC.
TABLE 1 ǀ Elastomeric coating formulations.
For accelerated DPUR testing, an iron oxide slurry was prepared according to Table 2 using a high-speed mixer to disperse the ingredients until smooth. Coating samples were drawn down at 30 mils wet film thickness on white mylar and allowed to cure at room temperature for 3 days, followed by QUVA cycling for 7 days. The iron oxide slurry was added to half of the panel and allowed to dry for 3-4 hours. The panel was then gently washed by running under water and using a small piece of cheesecloth, rubbing lightly. The panel was blotted dry and allowed to completely dry before measuring the color change, ΔE, using a spectrometer, and comparing to the pristine section of the drawdown.
TABLE 2 ǀ Iron oxide slurry.
A dry dirt particulate was also used as an additional accelerated DPUR test. Panel preparation and cure conditions were the same as the above described iron oxide method. However, instead of a slurry, a dry dirt particulate was used. Each cured panel was then placed in a 50 °C oven for 1 hour prior to the dirt particulate being applied to the panel. The panel was allowed to cure in the oven for an additional hour, before being removed and allowed to cool to room temperature. The panel was then tapped to remove the excess dirt, with no washing or scrubbing of the panel. The ΔE value was then measured, comparing to the pristine section of the drawdown.
Natural exterior exposure testing was performed in Los Angeles, California. New southern yellow pine was used, with the board being divided into six sections. Two coats of a coating were applied at a coat weight of approximately 400 square feet per gallon, applied 4 hours apart. The board was dried for approximately 24 hours in the ambient lab environment prior to being placed outside horizontally.
Results and Discussion
The first comparison made was using a resin with a Tg of +9 °C and modifying the PVC of the formulation. Accelerated iron oxide DPUR testing resulted in large ΔE values between 44 and 52 units, with the lowest PVC formula showing the lowest value (with a lower ΔE value indicating better DPUR performance). Although the 30 PVC sample has the lowest ΔE value, overall, all samples have very poor performance.
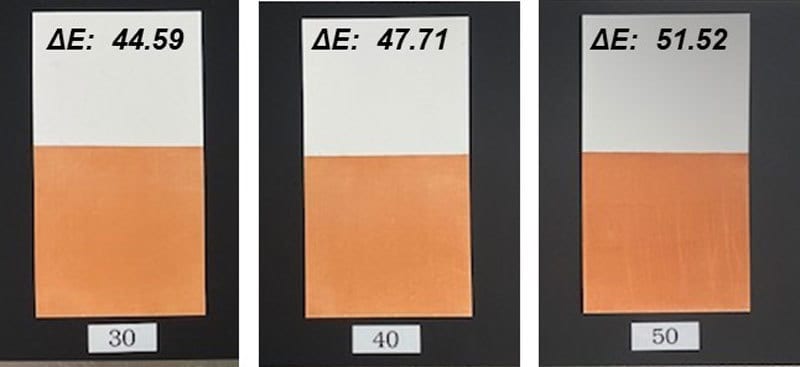
FIGURE 1 ǀ Formula modification by PVC adjustment.
The same formula was used with the addition of several post-additions. Here, a wax emulsion was added at 2.5% wax based on wet coating. In the second sample, a fluorosurfactant at 0.15 wt% based on resin solids was added. In these samples, little to no change was observed versus the control coating. The fluorosurfactant showed approximately a 3 unit change in ΔE. However, the performance of these samples remained poor overall (Figure 2).
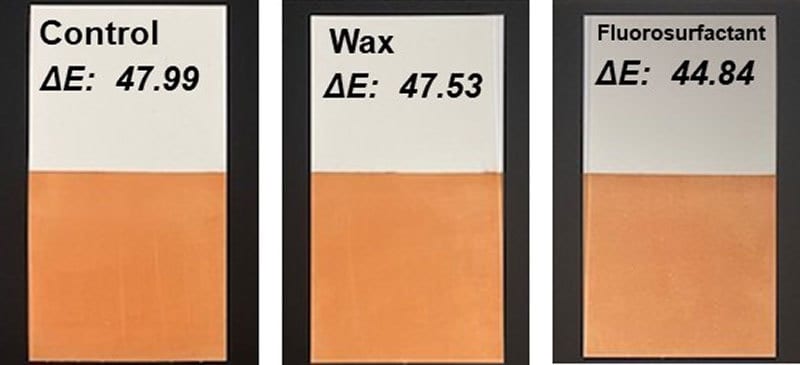
FIGURE 2 ǀ Formula modification by post-addition of additives.
The third series replaced the polymer with resins of varying Tg values, as shown in Figure 3. In this series, as expected, the higher Tg resin resulted in the greatest improvement in DPUR, with a ΔE value of about 10 units. The softest resin, with a Tg of -32 °C resulted in the poorest performance at 52 units. In systems that require a low-Tg resin, such as elastomeric coatings, utilizing the higher Tg resin is not possible. Further, additional coalescent was added to the coating system with the high Tg to achieve acceptable film formation, resulting in a high-VOC coating system, which is not desirable and may limit use in particular jurisdictions.
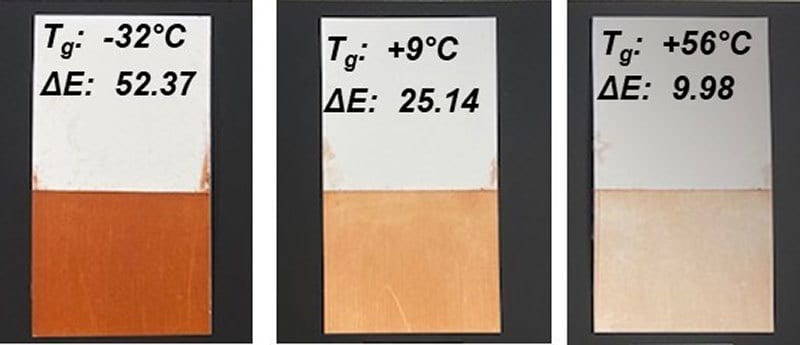
FIGURE 3 ǀ Resin Tg impact on dirt pickup resistance.
In the next series of coatings, the Tg of the resin, in addition to the DPUR technology type was examined, as shown in Figure 4. Panels 1-3 contained resins with a Tg of -26 °C that had no DPUR technology, EPS DPUR technology and benzophenone technology. Panels 4-5 contained resins with a Tg of -10 °C with benzophenone and EPS DPUR technology, respectively, and panel 6 was a fail control. Comparing the first three panels, it is observed that including benzophenone in the system only improves the DPUR marginally, from a ΔE value of about 45 to 37. The resin with the EPS technology further reduces the ΔE to less than 4 units, a dramatic improvement. Similarly, in panels 4-5, the DPUR is improved to less than 5 units in the -10 °C Tg system.
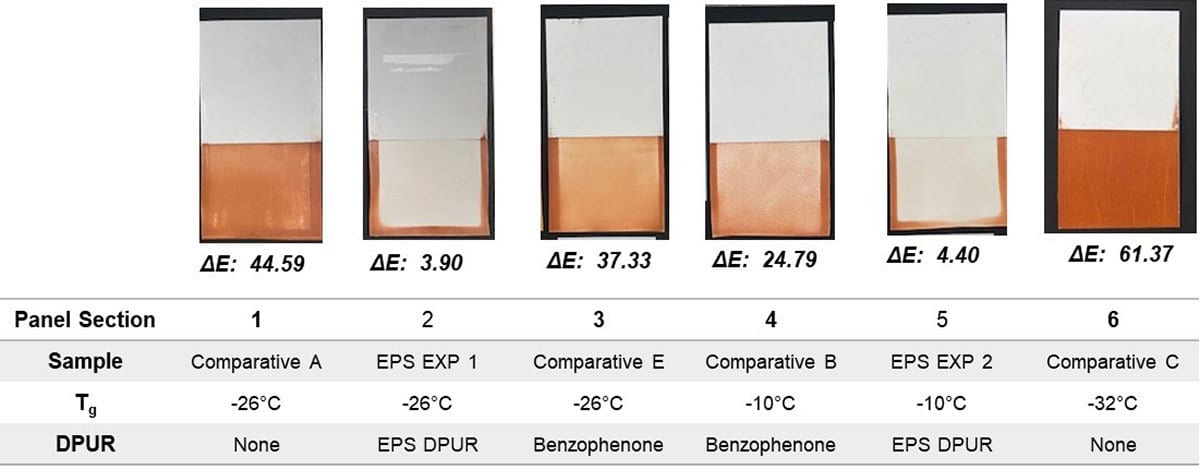
FIGURE 4 ǀ Accelerated dirt pickup comparison with various Tg and resin technology.
Since there is always some level of uncertainty in how accelerated testing compares to natural exposures, a board was painted out and exposed in Los Angeles, California, to compare testing methods. Results are summarized in Figure 5. Here, images of the board prior to exposure and the board after 6 months are shown. Panels 1 and 6, with no DPUR technology, have very poor DPUR results, as evidenced by the darkened panel after 6 months. Panels 3 and 4, which utilize benzophenone, show moderate improvements vs. the controls (panels 1 and 6), but still show a significant difference in DPUR compared to panels 2 and 5. Thus, coatings made with resins containing EPS DPUR technology have the ability to remain whiter for a longer period of time.
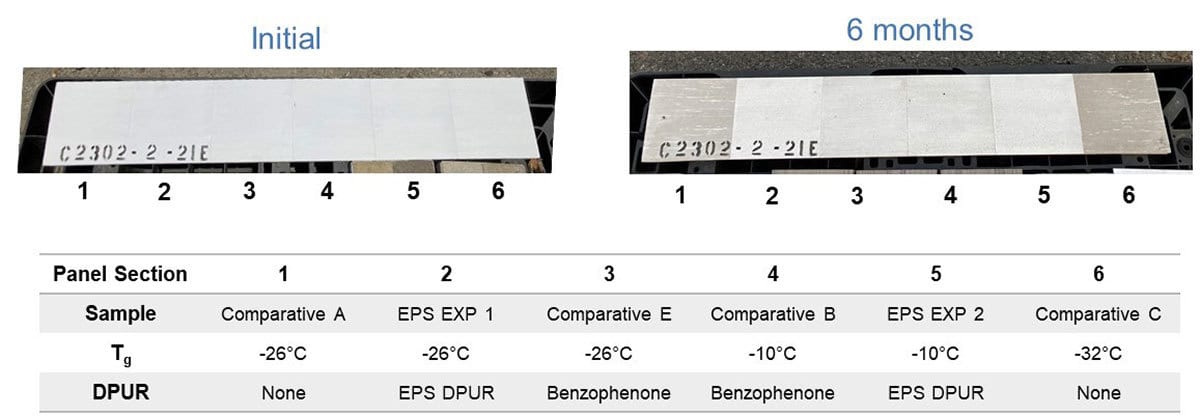
FIGURE 5 ǀ Los Angeles dirt pickup resistance exposure series.
The final series compares a commercial silicone coating system bought off the shelf and the EPS DPUR technology in a low-Tg resin. This is shown in Figure 6. In this evaluation, the iron oxide method showed good DPUR for both coating systems. This appears to contradict anecdotal knowledge that silicone coatings tend to be poor for DPUR. However, it was hypothesized that the testing method, which uses an iron oxide dispersed in water, may unrealistically show better performance. Since water is the carrier liquid for this test, and silicones are extremely water resistant, the testing method may not correlate with real-world testing. To demonstrate this, an additional accelerated test was performed, this time using a dry particulate. In this testing, the tapped panels showed a large amount of residual dirt remaining with the silicone coating, whereas the EPS resin with DPUR technology still had good performance and a low ΔE value.
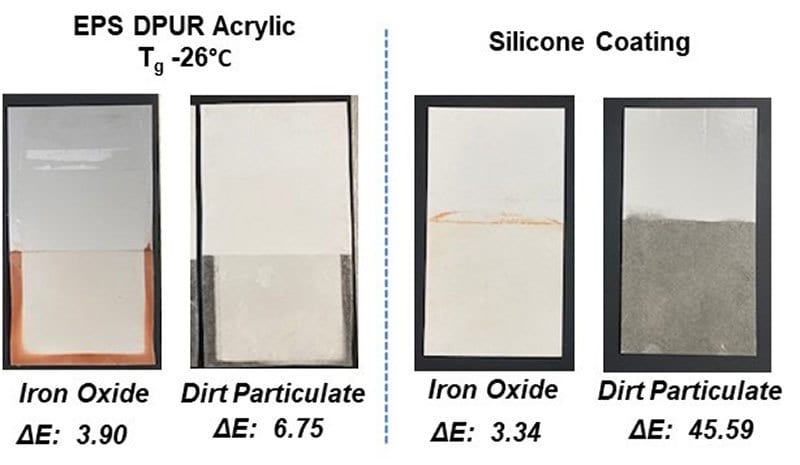
FIGURE 6 ǀ Dirt pickup resistance of acrylic and silicone coating system.
Conclusions
Overall, methods that formulators commonly use to improve dirt pickup resistance in coatings show a range of benefits but can introduce negative attributes as well (Table 3). The use of higher Tg resins shows improved DPUR, but may require a higher VOC level, which may not be allowed in some regulatory jurisdictions. Additionally, some coatings require a low-Tg material for certain performance attributes, and these would not be achieved with higher Tg resins. The incorporation of unique additives such as wax or fluorosurfactant may improve DPUR, although the particular ones examined in this study did not show improvement. Additionally, there is increasing regulatory scrutiny on certain small-molecule additives such as fluorosurfactants. Adjusting the PVC of the resin provided no significant improvements in DPUR and may require substantial formulation changes that may not be appropriate for the application. Benzophenone, a legacy technology, did show modest improvement in DPUR. However, the use of benzophenone could trigger labeling requirements and could be considered a VOC according to certain testing methods. An alternate chemistry, such as silicone, while performing well in iron oxide testing, did not perform well in a non-aqueous DPUR testing method. The EPS technology showed a large effect on the DPUR, even at Tgs as low as -26 °C. This required no formulation modification compared to an unmodified formula, and DPUR effectiveness was confirmed with exterior exposure testing.
TABLE 3 ǀ Benefits and negative attributes of commonly used methods to improve dirt pickup resistance in coatings.
Acknowledgements
Dr. Jonathan Wang and Ashley Rodgers are gratefully acknowledged for synthesis of the resins used in this study, and Dr. Patrick Lutz is acknowledged for performing the exterior exposure testing.