Ready to proof -- Clare 4/11/23
CB proofed 4/12/23
KJ proofed on 4/12 - clean from my end
ASK JOE POWDER
Sponsored by Gema
Our popular Ask Joe Powder blog has made its way to the pages of PCI magazine. What are your powder coating questions and challenges? Joe Powder, aka Kevin Biller of ChemQuest Powder Coating Research, shares his powder coating knowledge and expertise by answering questions sent in from around the world.
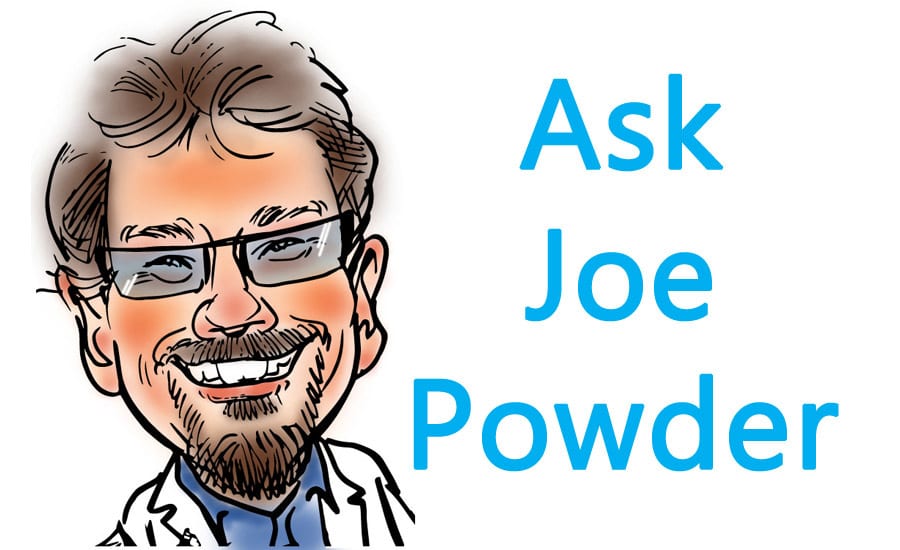
Hi Joe,
Hope you are doing well. Have you come across hydrophobic additives for powder coating? Or a wet paint that could easily be applied over powder coating for added protection?
Chris McKinnon
Vancouver, BC
Hi Chris
Regarding a topcoat for powder coatings, you may want to consider a scratch-resistant UV clearcoat. This technology is what is applied to polycarbonate eyeglass lenses. I realize that you seek a hydrophobic surface, and these are touted to be scratch resistant, however the scratch resistance is developed with silicone and silane chemistry, which are also quite hydrophobic. You can get more of an idea if you do an internet search on: optically-clear-hard-coatings.
Alternately you can ask a powder supplier for a highly water-resistant powder coating. We formulators can develop hydrophobicity through high crosslink density and with the incorporation of silicone additives. In particular, polyurethane-based powder coatings typically exhibit far better hydrophobicity than standard polyester types.
Kind regards,
Joe
Hey Joe,
I’m looking for a degassing agent for low-temperature-cure powder coating. Can you assist with this?
Ahmet Özcan
Turkey
Dear Ahmet,
Thanks for the question. Degassing agents can be used for a variety of phenomena. Some "gassing" is related to the expulsion of interstitial air between powder particles as they fuse and form a film. In addition, some cure chemistries emit volatiles — for example, e-cap-blocked polyurethanes, glycoluril-crosslinked polyesters, and hydroxyl-alkyl amide-cured (e.g. Primid®) polyesters. Also a small amount of moisture (< 0.5%) is normally present in powders. Degassing agents are essential in all these scenarios.
Another gassing phenomenon involves the expulsion of gases (air, water vapor, and even hydrogen) that are associated with substrates — cast metals, galvanizing, etc. This is commonly referred to as "off-gassing" or "outgassing". A different set of degassing agents work for these phenomena.
Formulating for degassing is tricky business. Benzoin works very well for gas release in standard bake powder coatings. This pertains to the air, moisture, and cure-chemistry volatiles degasification phenomena. It doesn’t work so well in low-bake (<130 °C) powders because the melt point is around 132 °C and is rendered ineffective below that temperature. Hence, you need to consider more specialized proprietary products from additives suppliers (check out Estron, Troy Corp. and BYK Additives).
As for “off-gassing” or “outgassing,” the secret sauce is based on a wax. These waxes allow the coating to stay soft and “open” during the melt and cure cycle. This open phase allows the volatiles from the substrate to evolve through the coating. After volatiles have exited the coating, the wax reflows to fill the void created by the evolution. Specific product suggestions are available from Micro Powders, Estron, and BYK Additives.
I hope that this explains some the magic of powder formulating.
Kind regards,
Joe
Dear Joe,
I’m working on a marketing research project and have a question regarding powder coatings used on medium density fiberboard (MDF). Do they always have to be UV cured?
Regards,
Pamela
Cleveland
Dear Pamela,
No, they do not. There are essentially two options: UV-curable and low-temperature-thermosetting powder coatings. The UV curables require an additional process step but cure in a shorter process footprint. They also provide better coating durability (mainly hardness and chemical resistance). UV cure requires line-of-sight curing that is also critical to the distance of the lamps to the coating surface. In addition, film thickness must be carefully controlled. If the coating is too thick (or too opaque) it will not cure completely. And as you can guess the material cost is higher than more conventional products
Thermosetting powders can be used as well. They require longer curing times (typically 20-30 minutes), although infrared heat can mitigate some of this. They are highly catalyzed and therefore must be stored in a controlled environment and can advance chemically, which affects coating smoothness. The thermosets are generally less smooth than the UV-curable types and typically less durable.
As for specifics regarding cure requirements, this mainly depends upon the chemistry. Polyester TGIC systems work with cure cycles of about 25 minutes at 265 °F. Acrylics can cure as low as 25 minutes at 275 °F. Epoxies have been formulated to cure at 25 minutes at 230 °F. Epoxy-polyesters (hybrids) can be processed at 25 minutes at 250 °F. Polyurethanes and polyester-HAA require cure temperatures over 300 °F. More conventional powders cure with less dwell time at much higher temperatures and therefore cannot be used for MDF.
UV-curable powder technology requires a melt stage, typically around 60 to 90 seconds at a peak temperature of 200 to 240 °F. The additional UV-cure process usually takes only a few seconds depending upon the complexity of the part.
Lots of film performance and process issues are very specific to the formulation so you need to be careful with generalizations. Several powder manufacturers make and sell both types of chemistries as one shoe doesn't fit all.
Best regards,
Joe