Ready to proof -- Clare 10/13/22
KJ proofed on 10/13: Courtney, fyi, I updated the lead image credit to match this photo. ALso, there is one note down below for you just as an fyi - no change needed. Clean from my end.
CLJ revised on 10/14
Highly Weatherable PVDF-Based Aqueous Dispersions for Low-VOC Applications
Photo: Lari Bat, iStock, via Getty Images
By Kelly E. Lutz, Research Scientist, Arkema Inc., King of Prussia, PA
Polyvinylidene fluoride (PVDF)-based topcoats have long been the choice of architects and specifiers who are seeking superior weatherability.1,2,3 Traditionally, these solventborne coatings have typically been used as factory-applied topcoats for metal (coil-coatings) and can pass AAMA 2605 specifications, the highest standard available for organic coatings on architectural aluminum.4 The PVDF resin is dispersed in a latent solvent (VOCs ranging from 500-700 g/L) along with an acrylic copolymer, selected for miscibility, that ultimately leads to an excellent film upon baking above the PVDF melting point (170 °C).5 Panels prepared in this way have exhibited excellent color retention for over 50 years in South Florida.
Outdoor weathering provides exposure to ultraviolet (UV) radiation, which prompts photooxidative degradation, breaking the chemical bonds in a polymer resin backbone. The polymer resin, which initially encapsulates the pigment, will deteriorate, creating a rough surface, manifesting in chalking and gloss loss. With the pigment now exposed and no longer protected, it can undergo deterioration, resulting in color fade. There are multiple tools to photostabilize the polymers such as UV absorbers or HALS. However, these small molecules can lose effectiveness or leach out of the coating over time. An alternate method is to select polymers that are less sensitive to photo-degradation, such as those that contain stronger atomic bonds, like the C–F bond. The innate structure of PVDF, repeating CH2–CF2 units, produces a photochemically inert resin.6 Because of this, the typical oxidative photodegradation pathway for other organic coatings are not entirely applicable to PVDF-based coatings. Typical degradation of coatings begin on the surface and then penetrate as the initial surface erodes away.7 The PVDF-based coatings are a homogenous blend of PVDF and miscible acrylic. Degradation of these coatings will occur almost exclusively on the acrylic portion. Over time, the acrylic will erode (by evidence of physical chalking), leading to an enriched PVDF surface (Figure 1).
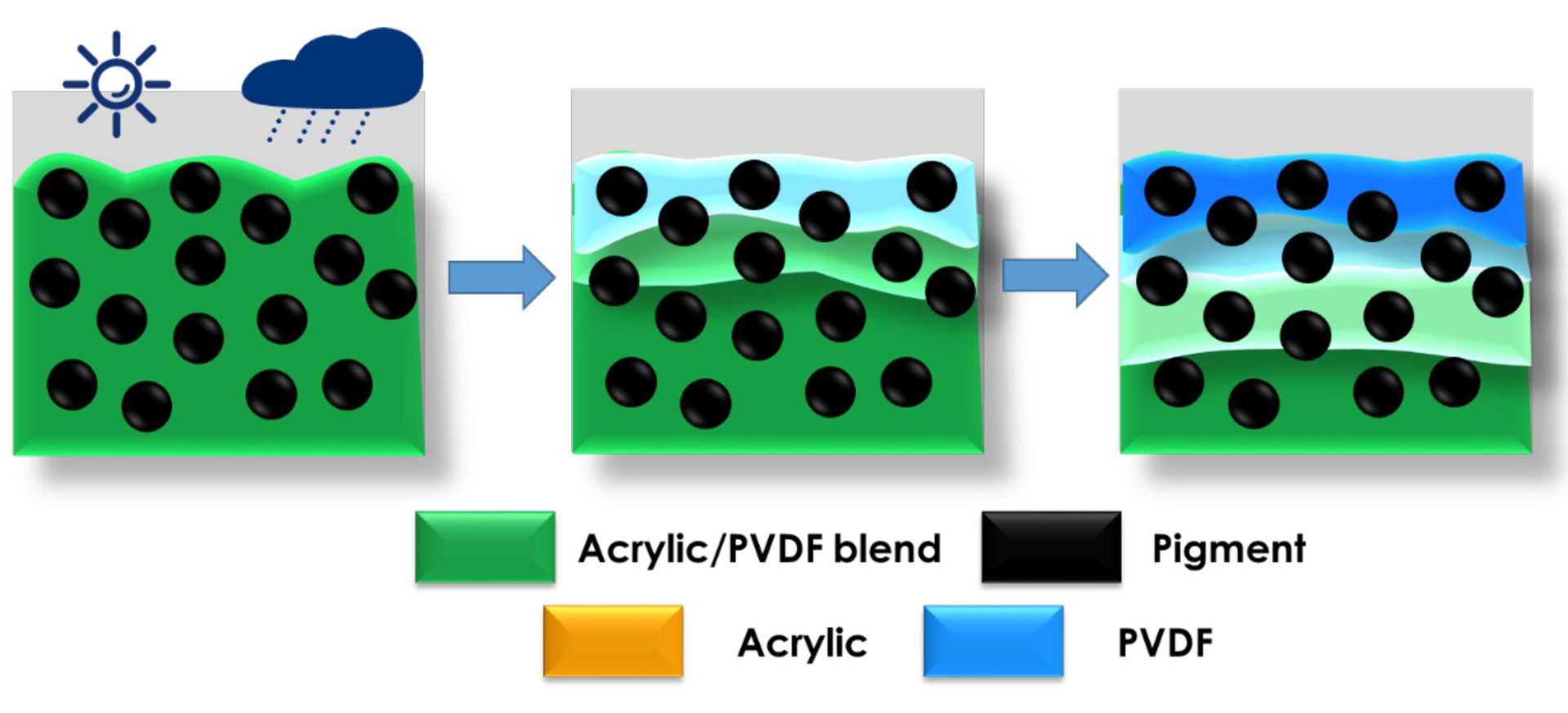
FIGURE 1 ǀ Weathering of homogenous PVDF-acrylic blend leads to erosion of acrylic and enrichment of PVDF on surface, while maintaining pigment encapsulation.
Arkema, Inc. developed water-based PVDF-acrylic hybrid dispersions to meet the need of resins applied in the field or over temperature-sensitive substrates. The first version of these PVDF-acrylic hybrid latex materials, Kynar Aquatec® ARC, mimics its solventborne analogs. The aqueous dispersion contains 70% PVDF content by weight with 30 wt% interpenetrated acrylic polymerized within.8 Exposed to over 20 years of South Florida weathering, this preliminary waterborne resin shows comparable performance to its solventborne counterpart, Kynar 500® FSF® PVDF (Figure 2).1
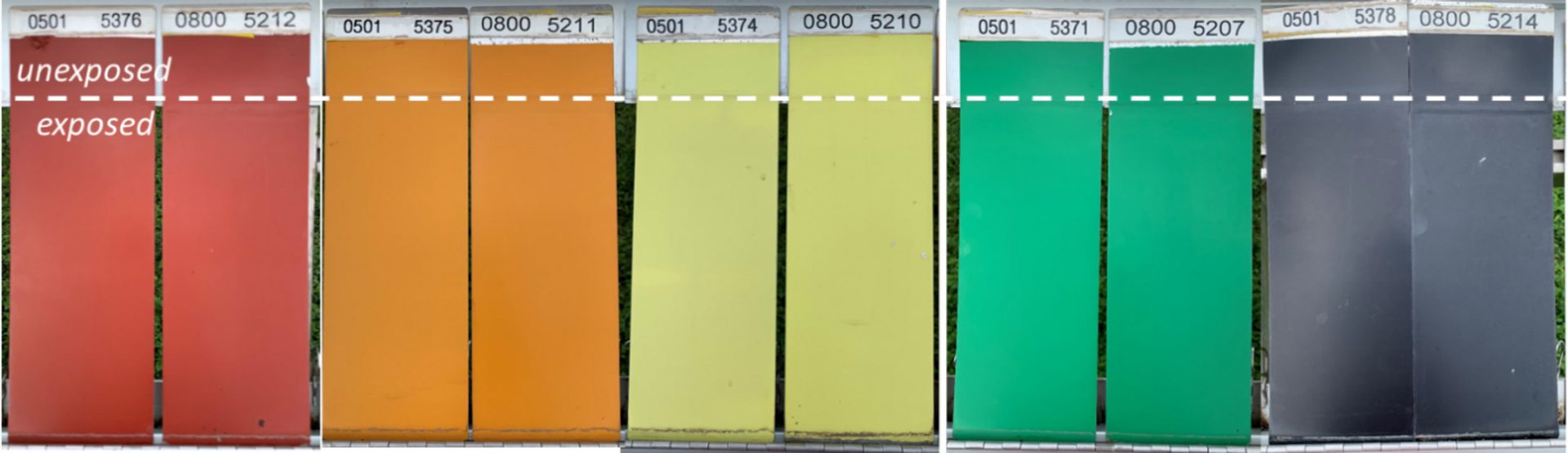
FIGURE 2 ǀ Waterborne 70% PVDF-acrylic hybrid dispersion coatings (right of color pairs) were prepared in 2000-2001 to compare to solventborne 70% PVDF baked coatings (left of color pairs). (Picture taken November 2021.)
Despite having excellent weatherability, the VOC demand of this latex still exceeded the target set for typical field-applied architectural coatings. VOC demand of any latex is decided by how much co-solvent is required for the latex to undergo the three basic steps of film formation: evaporative drying/packing, particle deformation, and eventually polymer interdiffusion/coalescence.9 The higher the Tg of the latex, the more co-solvent it will need to effectively “soften” so that it can undergo appropriate deformation and lead to a well-coalesced film. Different co-solvents and plasticizers will have a varying effect on the minimum film formation temperature (MFFT) of a latex. In Figure 3, we see that addition of 5-10% coalescent based on the polymer solids of the 70% PVDF latex can significantly lower the MFFT from its original 26–28 °C. In a full coatings formulation, an addition of around 3-5% coalescent is the maximum limit to meet the VOC targets of < 50 g/L, thus the 70% PVDF latex is not a good candidate for a low-VOC formulation if curing takes place below 20 °C.
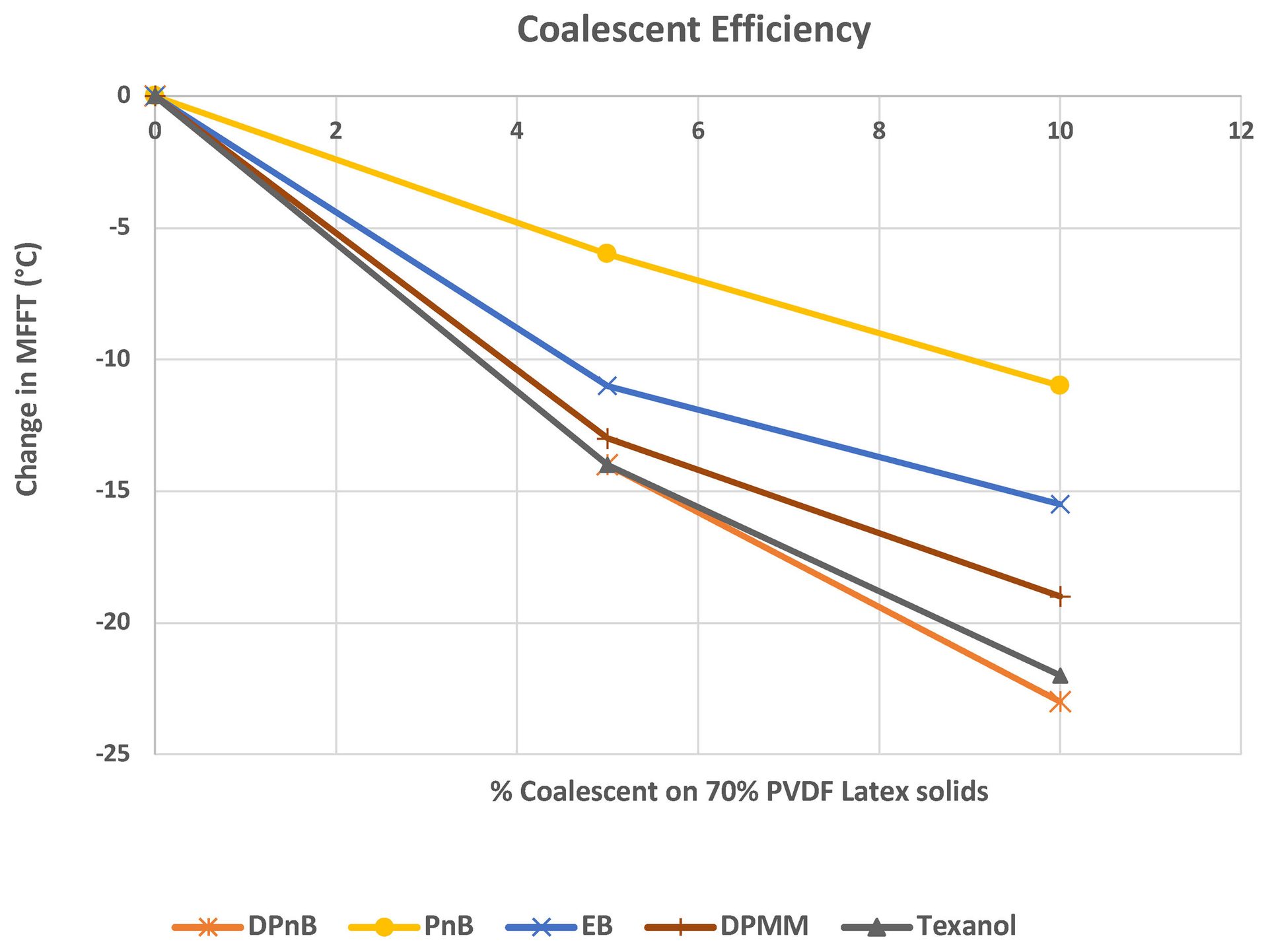
FIGURE 3 ǀ Coalescent efficiency of multiple co-solvents with 70% PVDF Latex A.
To meet the low VOC target, several variables could be altered. In addition to lowering the acrylic Tg of the PVDF-latex hybrid dispersion, the amount of PVDF content in the latex could be decreased. Data from 20 years shows that 70% PVDF content is sufficient to provide excellent weatherability, but it was unclear to what degree the PVDF content could be lowered without sacrificing performance. A next-generation product was developed that would meet VOC regulations based on its MFFT and PVDF content, and 10 year data shows that it still provides excellent weathering performance with numerous inorganic and organic pigments.
Results and Discussion
To determine how increasing the acrylic content as a means to reducing MFFT (and therefore VOC) affects weatherability, a range of commercially available water-based coatings, with varying amounts of PVDF content and color-matched to either Blue RAL 5015 or Gray RAL 7039, were exposed to QUV-B accelerated weathering for 4,000 hours (Figure 4). The blue pigmented coatings without any PVDF have ΔE* values ranging from 14 to 23. An inclusion of only 20% PVDF in the polymer matrix drops the ΔE* value closer to 10, whereas as a coating with up to 70% PVDF can maintain a ΔE* less than 5 after 4,000 hours. A less extreme, but similar trend is seen in the gray coatings.
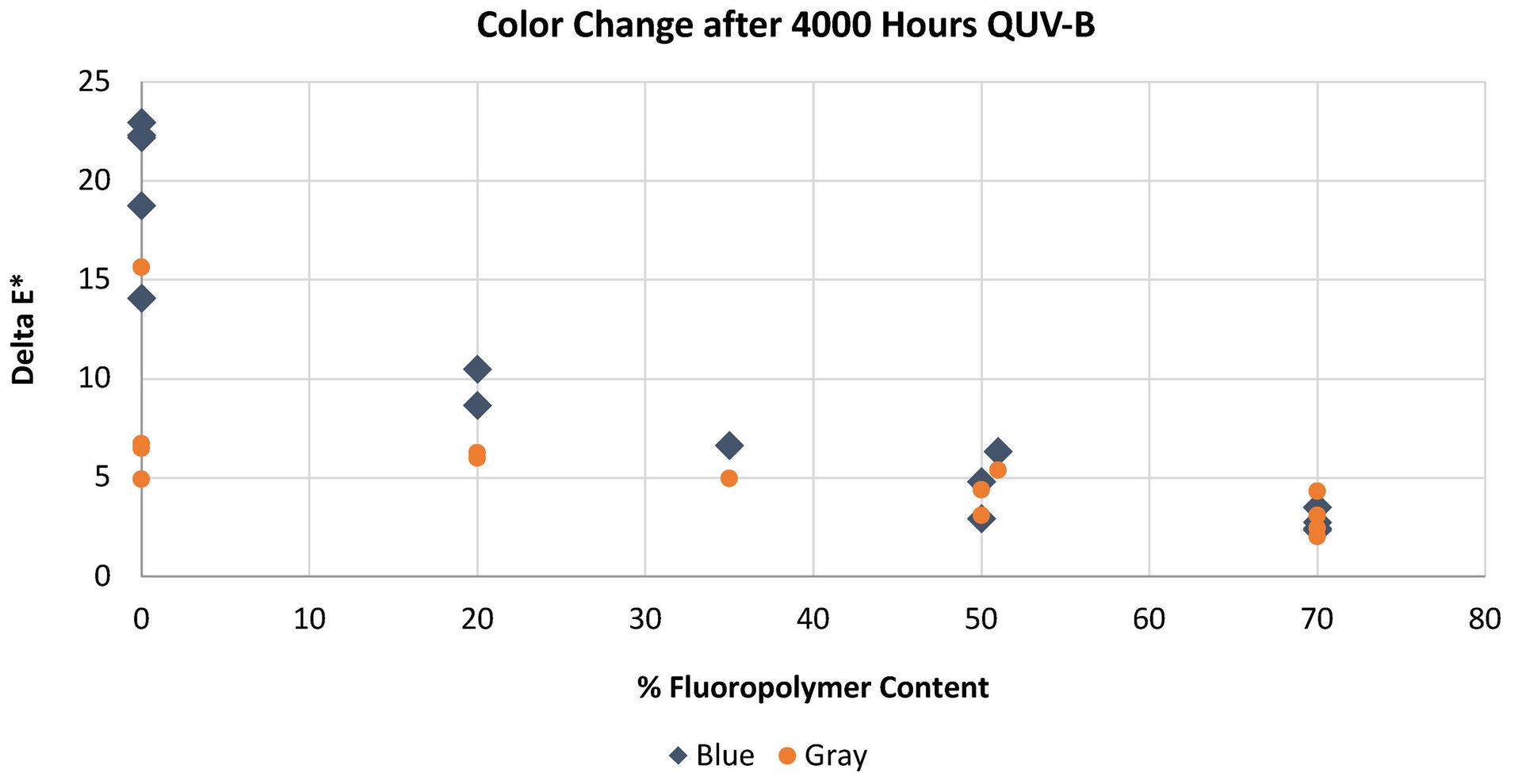
FIGURE 4 ǀ Color retention after 4,000 hours of QUV-B (313 nm) of commercially available coatings containing 0-70% PVDF in resin.
The study in Figure 4 examined commercial coatings where numerous unknown variables could account for differences in the performance of the final coating. The range of ΔE* differences in the coatings without any PVDF-acrylic latex could be explained by different grades of pigment or other additives used in the formulation of the base coating. In order to have a firmer grasp on the performance of different levels of PVDF in the final coating performance, a ladder study of coatings were formulated ranging from 70% PVDF (neat 70% PVDF latex) to 0% PVDF (100% acrylic). The coatings were formulated with color-stable inorganic pigments (mostly pigment blue 36) and blended with an elastomeric acrylic. After 135 months of South Florida exposure, a clear correlation between color and gloss retention with amount of PVDF in the coating can be seen (Figure 5). In this case, the color retention appears to be linearly correlated, whereas the gloss retention shows an almost exponential improvement as the amount of PVDF increases.

FIGURE 5 ǀ Color and gloss retention of 70% PVDF latex and acrylic blended to have 0-70% PVDF content in polymer matrix, formulated into navy blue coatings.
The PVDF/elastomeric acrylic blend study shows that it is possible to dilute 70% PVDF latex with a traditional latex and still have better color and gloss performance than a 100% acrylic formulation. However, blending of acrylic and PVDF-based latexes provides a series of hurdles to overcome: semi-crystalline PVDF, considered a hard particle, must be compatible with the soft, acrylic latex particles, all while achieving homogenous distribution and proper particle packing. Incompatibility in latex choice or coalescent selection could easily disrupt proper film formation.
Blending of the PVDF-acrylic hybrid with the lower MFFT-acrylic allowed for lowering of coalescent levels from 150 g/L to as low as 100 g/L. This amount still is not low enough to meet current architectural application regulations. We have shown through weight loss studies that the unique morphology of the PVDF-acrylic interpenetrated network (IPN) gives enhanced weatherability over PVDF-acrylic core-shell latex as well as pure acrylic latex.10 In order to circumnavigate these obstacles of latex blending, yet still produce a highly weatherable PVDF-based coating that can meet VOC guidelines, a new PVDF-acrylic dispersion was designed.
Excellent weathering can still be achieved with less than 70% PVDF in the polymer matrix. A dispersion comprised of 50% PVDF and 50% lower Tg acrylic was designed that would balance weathering performance properties, while allowing the coalescent demand to be lowered to under 50 g/L. Kynar Aquatec® FMA-12, a 50% PVDF latex, with an MFFT of 12-14 °C, can achieve excellent film formation at room temperature with less coalescent, thereby leading to overall lower VOC content (Table 1).
TABLE 1 ǀ Physical properties of PVDF-acrylic hybrid dispersions.
With a single PVDF-acrylic hybrid latex in hand, a study was designed to directly compare the two grades of PVDF-acrylic dispersions. A series of panels were produced using the same weatherable pigments in masstones and tints, and placed for weathering in South Florida. As expected, the 70% PVDF latex panels had lower ΔE* results after 113 months for most of the pigments tested (Figures 6 and 7). However, the 50% PVDF latex-based masstone panels maintained a ΔE* <10 after 113 months, and the tints held a ΔE* <5 after 106 months.
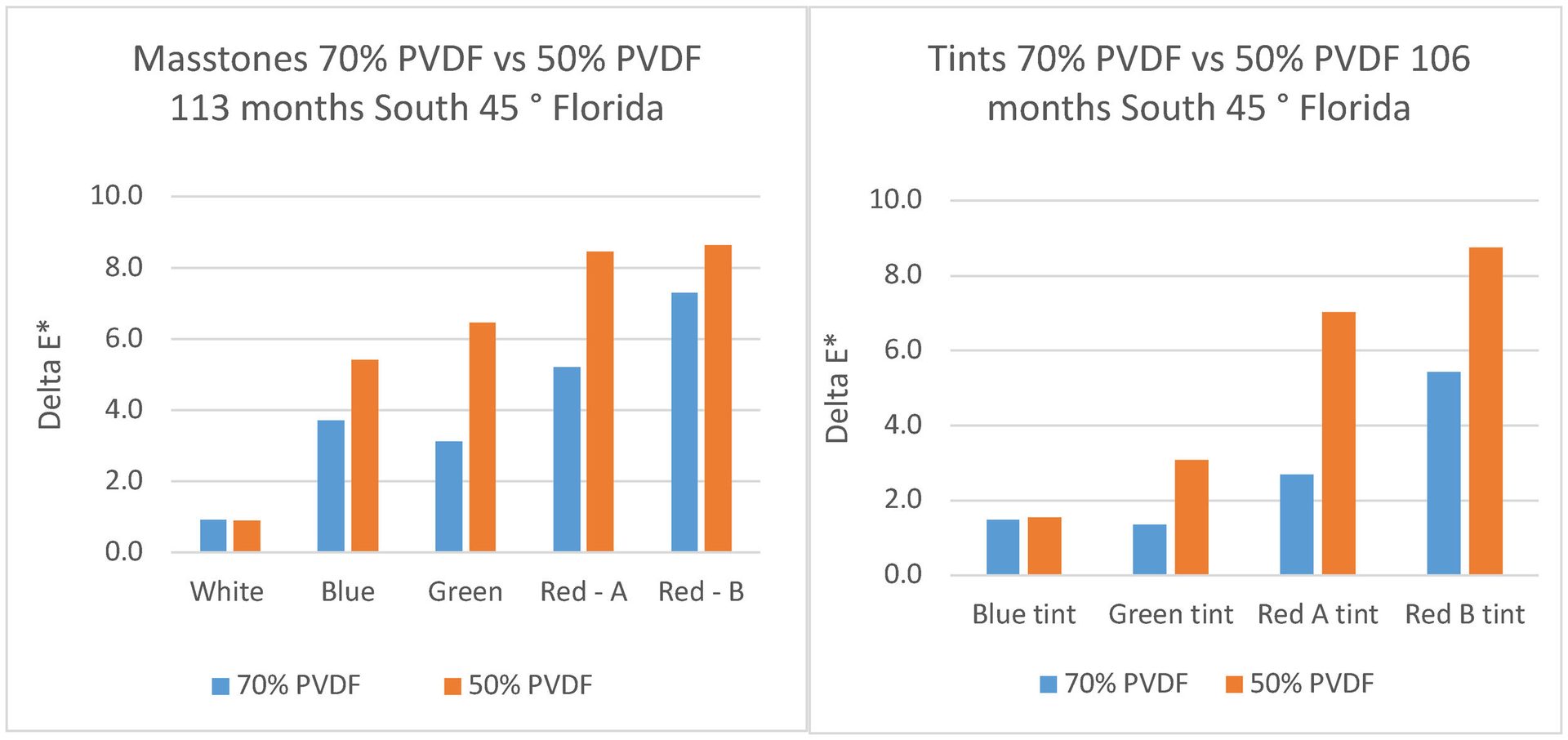
FIGURE 6 ǀ South 45 ° Florida color retention for inorganic masstones and tints in 70% PVDF latex vs 50% PVDF latex resins.
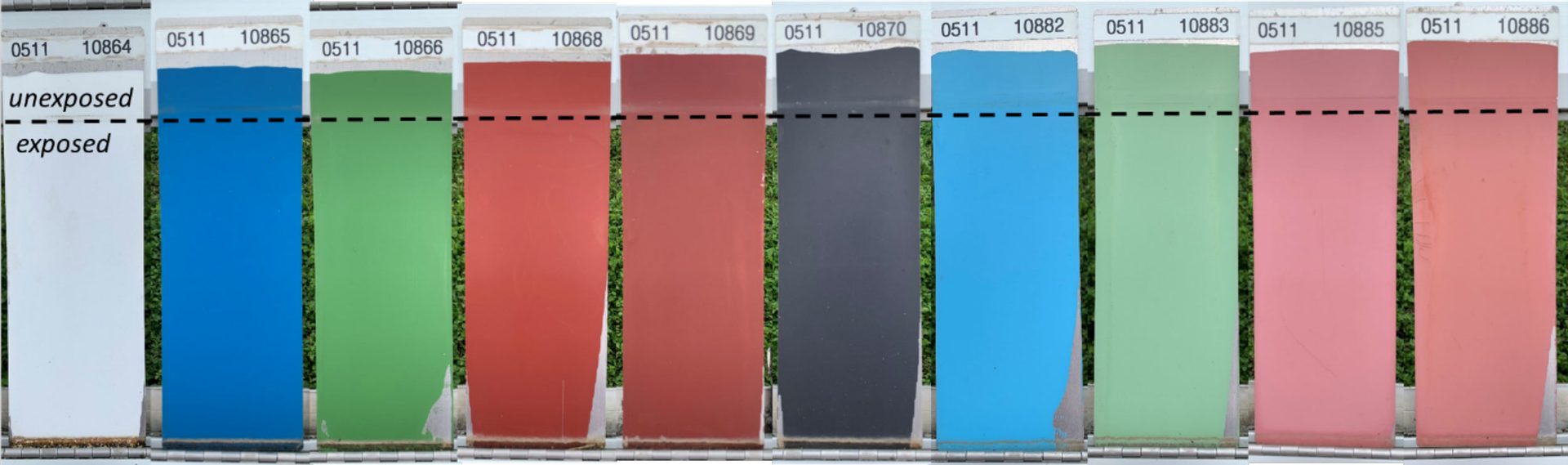
FIGURE 7 ǀ 50% PVDF Latex B panels in masstones (first five panels on left) and tints (four panels on right) after 113 months in South Florida. (Picture taken November 2021.)
One of the most impressive weathering achievements of the 50% PVDF latex is the weathering performance with diketopyrrolopyrrole (DPP) red pigments. The gloss retention for all three panels is above 80% and the color retention is less than 10 ΔE* units even after 10 years of exposure (Figure 8). We can tell that the PVDF-based binder has not degraded due to its high gloss retention, but because the PVDF resin is UV transparent, photodegradation can still occur on the pigment molecule resulting in color change.
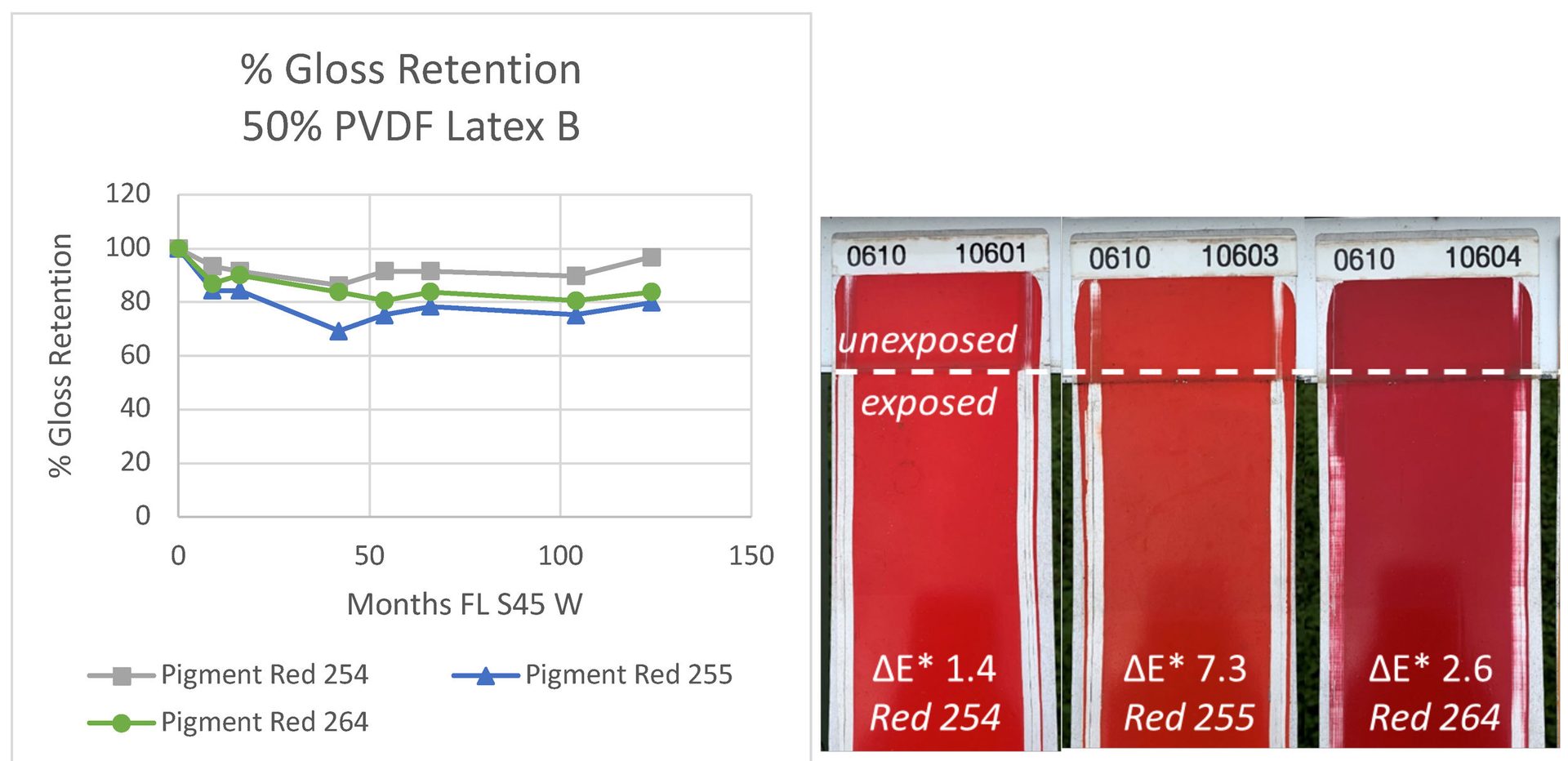
FIGURE 8 ǀ Color and gloss retention of DPP red pigments in 50% PVDF latex after 124 months in South Florida.
We can compare the performance of the 50% PVDF latex with a previous study examining pigment red 254 formulated with two other resins: a 70% PVDF solventborne dispersion coating and a 2K acrylic polyurethane (PU) system. In Figure 9, there is a sharp drop in gloss with the PU panels after the first two to three years, indicating that the resin is degrading, exposing the pigment to the elements, creating surface roughness that equates to gloss loss. With the pigment now exposed to the elements, a host of degradation pathways can occur, leading to color loss in these panels.
Alternatively, the gloss retention on the baked 70% PVDF panel is excellent, indicating the color loss is solely from pigment degradation underneath the intact UV-transparent PVDF resin. After three years in Florida, the color retention of the 70% PVDF dispersion coating begins to diverge from the 50% PVDF latex. Studies have shown that intentionally disrupting the crystallinity of DPP red pigments by exposure to high temperatures or by substituting the N-position to help increase solubility of the pigment will dramatically decrease the stabilization as shown by TGA and DSC, potentially allowing for long-term instability.11 This thermosensitivity is most obvious when comparing the 70% PVDF coating baked at >230 °C versus the 50% PVDF latex cured at ambient conditions. The difference in color retention over time may be pinpointed back to the difference in the thermohistory of the panels.
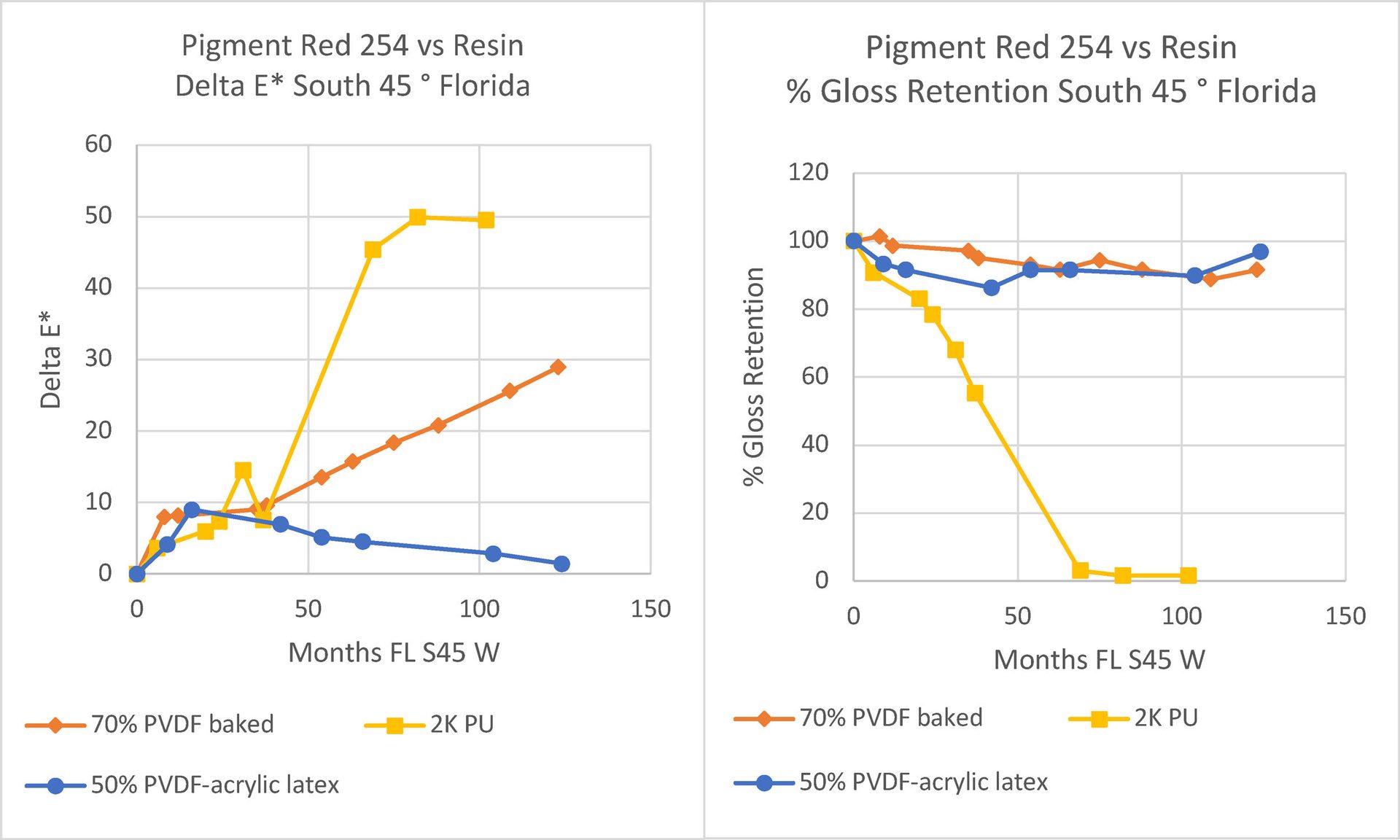
FIGURE 9 ǀ Pigment red 254 formulated in different resin technologies: 70% PVDF solvent dispersion, 50% PVDF latex, and 2K polyurethane.
We have shown that we can achieve excellent 10+ year weathering performance with as low as 50% PVDF content in the coating binder. We were then interested to see how the 50% PVDF latex performed compared to other low-VOC architectural coatings. The importance of developing a resin that can be formulated at low VOCs is made increasingly important by agencies such as South Coast Air Quality Management District (SCAQMD). SCAQMD is a regulatory agency responsible for controlling emissions in the South Coast Air District, an area encompassing large swaths of Los Angeles, Orange County, Riverside, and San Bernardino counties. About 25% of these emissions include stationary sources, or consumer products like house paint. Through their work, air quality has improved despite a tripling of population in the area.12 Rule 1113, adopted in September 1977, states that “any person who supplies, sells, offers for sale or manufactures any architectural coating for use in the SCAQMD must comply with the current VOC standard,” which as of today, is 50 g/L. Commercially available acrylic resins that meet the SCAQMD limits of 50 g/L in dark brown and dark blue were compared to formulations of the 50% PVDF latex, also formulated with < 50 g/L VOC. After one year exposure in South Florida, the 50% PVDF latex was already performing significantly better than the three commercial acrylic coatings in the blue series. After three years, the acrylics experienced significant fading while the 50% PVDF coating is consistently unchanged. The brown series showed a similar, but less exaggerated trend, most likely due to a more weatherable pigment choice. Both 50% PVDF latex samples show a ΔE* of less than 5 after eight years (Figures 10 and 11).
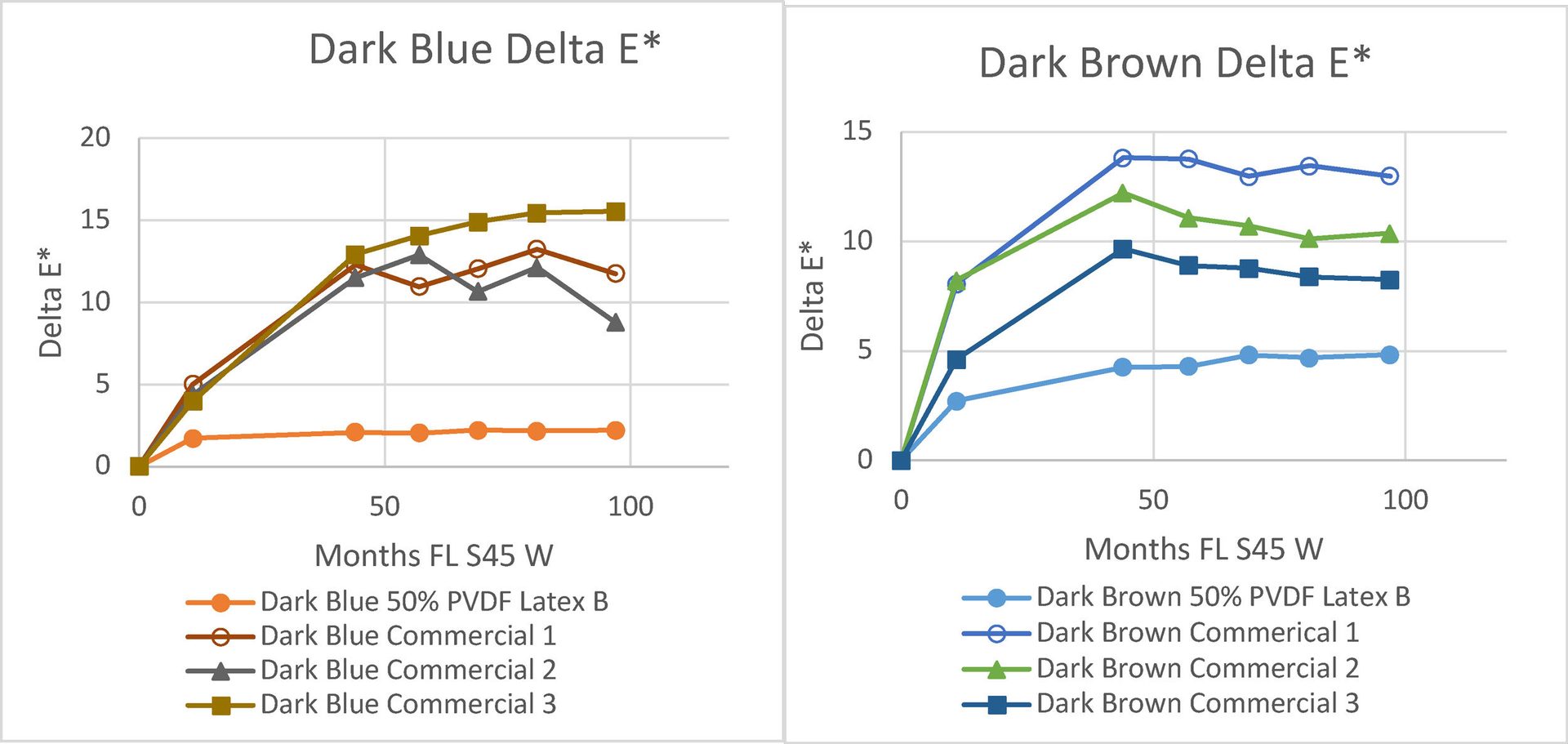
FIGURE 10 ǀ Color retention of low-VOC coatings in South Florida after 10+ years of exposure. (Photo taken in November 2021.)
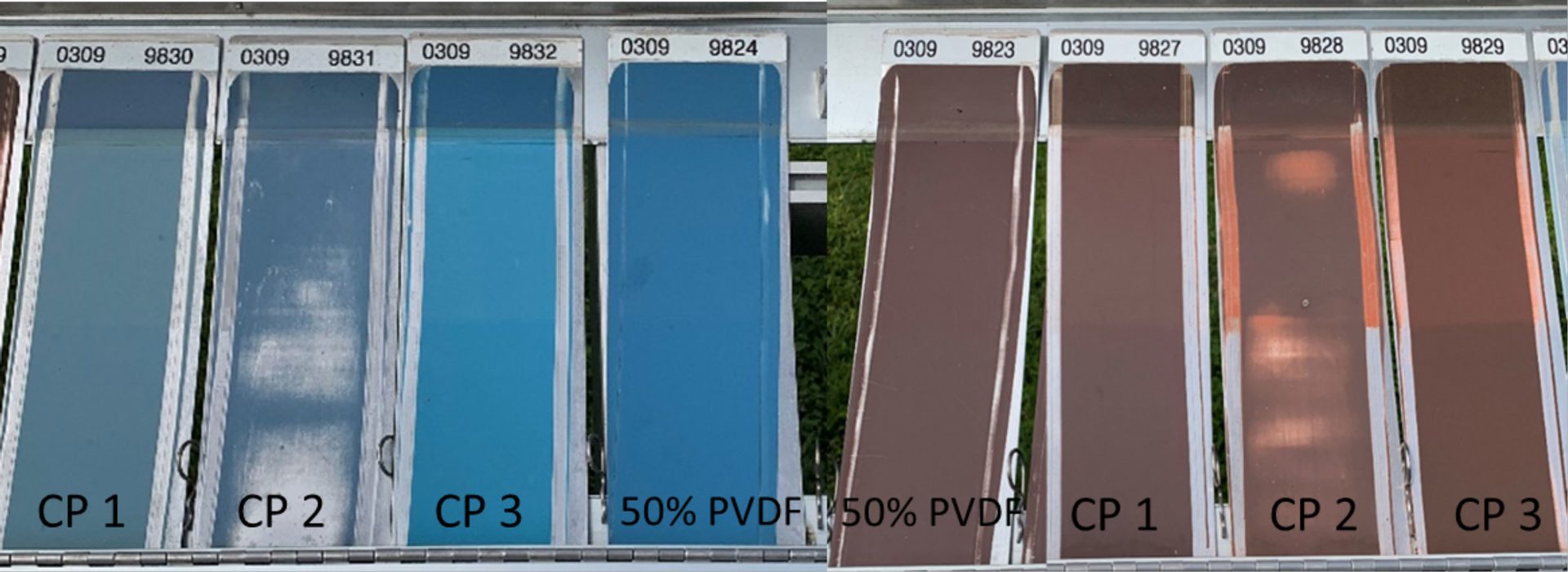
FIGURE 11 ǀ Low-VOC commercial paints and 50% PVDF latex panels after 10+ years of South Florida exposure. (Picture taken November 2021.)
The lower MFFT of the 50% PVDF latex allows it to have a wider window of application temperatures and substrates than the first generation 70% PVDF latex. Unlike the first iteration of these hybrid dispersions, which was designed for rigid, metal substrates, Kynar Aquatec® FMA-12 can be applied to substrates that are more flexible (e.g. wood, EPDM, etc.). To this end, the same SCAQMD commercial acrylic coatings were compared against the 50% PVDF latex on Hardie Board (Figure 12). Here, degradation of the polymer is exacerbated by the natural expansion and contraction of the substrate versus that of an aluminum panel. In Service Life Prediction (SLP) theory,13,14 failure is determined as a visible end point, resulting from a cascade of events that are often more catastrophic rather than gradual.15 For the fiberboard panels in Figure 12, a small microscopic chemical change in the acrylic binder-based panels led to a change in physical properties that ultimately led to loss of binder and poor color retention of the pigment. However, this microscopic chemical change did not occur in the panels containing PVDF, which still maintain good adhesion and color retention even after 10+ years.
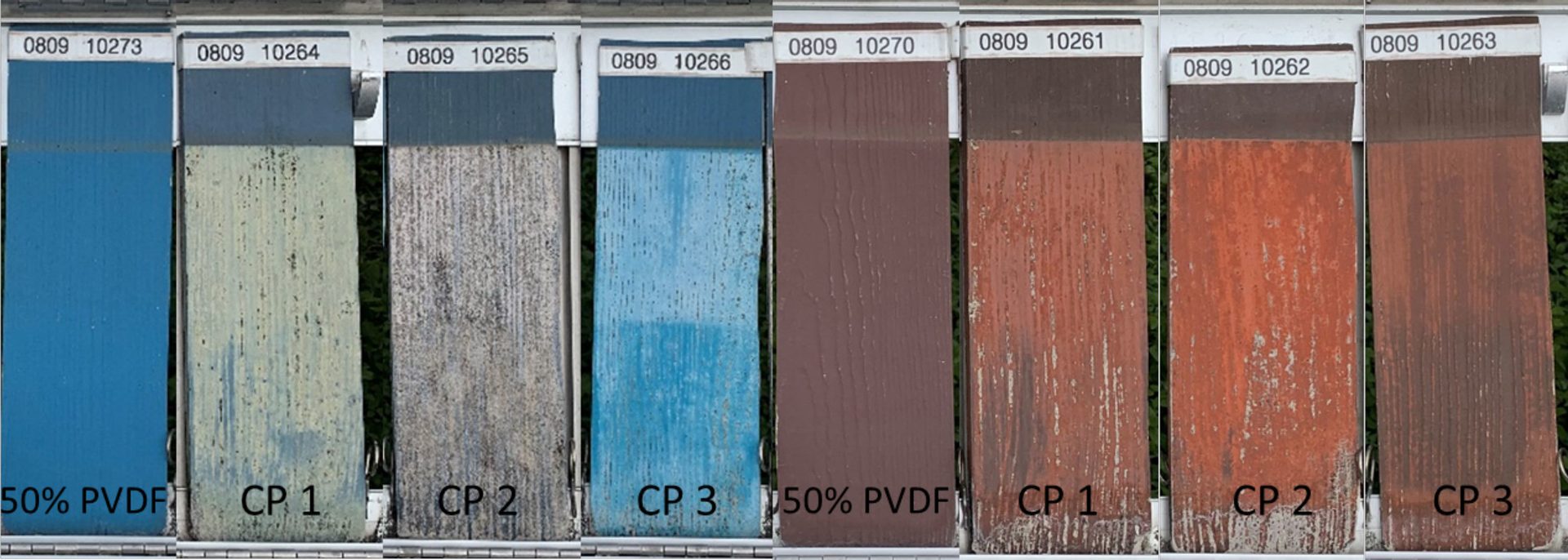
FIGURE 12 ǀ Low-VOC commercial paints (CP) and 50% PVDF latex on Hardie Board after 10+ years of South Florida exposure. (Photo taken November 2021.)
Conclusions
Baked, solventborne, 70% PVDF-based coatings have shown excellent weatherability for over 50 years, but there existed a need for a water-based alternative that could be applied at ambient conditions and be formulated under 50 g/L VOC. Many decades of research have unfortunately shown that accelerated weathering is no match for real-time weathering when it comes to accurately predicting performance over a range of different pigments, raw materials, and substrates. Here, we are able to show that after a decade of South Florida weathering, Kynar Aquatec FMA-12, a 50% PVDF-acrylic dispersion, is able to provide excellent color and gloss retention in a variety of colors in formulations that can meet the strictest low-VOC requirements.
References
1 Humphrey, S.; Drujon, X. Polymeric Materials Encyclopedia; CRC Press, Inc., 1996; Vol. 11, p 8591.
2 Iezzi, R. A. Fluoropolymer Coatings for Architectural Applications, Modern Fluoropolymers; Wiley, 1997. p. 14.
3 Hatcher, H.; Tocher, A. The Role of High Performance Inorganic Pigments in Surface Coatings. Paint. Coat. Ind. 2002, March.
4 Fenestration & Glazing Industry Alliance. 2021. AAMA 2605-21: Voluntary Specification Performance Requirements and Test Procedures for Superior Performing Organic Coatings on Aluminum Extrusions and Panels. Schaumburg, IL.
5 Gupta, R.; Wood, K. Novel Fluoropolymer-based Emulsion Technology: Striving for “Green” Coatings. Paint. Coat. Ind., 2007, 70-80.
6 Phillippart, J.-L.; Siampiringue, N.; Strassel, A.; Lemaire, J Inertie Photochimique du Poly(fluorure de vinyldene) a Courte et a Grandes Longueurs D’onde. Makromol. Chem., 1989, 190, 413-418.
7 Blaga, A. Deterioration Mechanisms in Weathering of Plastic Materials. In ASTM STP-691: Durability of Building Materials and Compounds; Sereda, P.J; Litvin, G.G. Eds.; ASTM, 1980 Philadelphia, pp 827-837.
8 Wood, K. The Advantages of Networking: Poly(vinylidene fluoride)-acrylic IPN Structures for Solvent and Waterborne Coatings. European Coatings Journal, 2005, 48–53.
9 Keddie, J.L. Film Formation of Latex. Materials Science and Engineering, 1997, 21, 101-170.
10 Wood, K.A.; Hedhli, L.; Hanrahan, K. Effects of Latex Particle Morphology on the Film Formation and Properties of Fluoropolymer-based Latex Paints. Paint. Coat. Ind. 2005, July.
11 David, J.; Weiter, M.; Vala, M.; Vynuchal, J.; Kucerik, J. Stability and Structural Aspects of Diketopyrrolopyrrole Pigment and its N-Alkyl Derivatives. Dyes and Pigments, 2011, 89, 137-143.
12 South Coast Air Quality Management District, 2021, http.//www.aqmd.gov
13 Bauer, D.R. Predicting In-Service Weatherability of Automotive Coatings: A New Approach. J. Coat. Technol. 1997, 69 (864), 85–96.
14 Floyd, F.L. Reducing Product Development Cycle Times Without Increasing Risk. J. Coat. Technol. 1998, 70 (876), 71–81.
15 Martin, J.W. A Systems Approach to the Service Life Prediction Problem for Coating Systems. In Service Life Prediction of Organic Coatings, ACS Symposium Series 722, American Chemical Society, Washington, DC, 1999, pp. 1–20.