Ready to proof -- Clare 10/13/22
KJ proofed on 10/13. Three notes below for Clare on placing the photos right above the "Results" section of each case history.
CB proofed on 10/14
CLJ revised on 10/14
Methods to Increase Paint and Coating Application Process Efficiencies
By Tasha Jamaluddin, Managing Director, Epcon Industrial Systems
The industrial painting and coating of surfaces typically involves stages of heat treatment along with significant VOC emissions, which make the process well suited for an integrated “oven/oxidizer combination” design with multi-stage heat recovery. By utilizing heat exchangers to transfer heat, it is possible to recover and recycle most of the thermal energy that would otherwise be wasted in the process, and potentially save millions in annual operating costs.
A primary heat exchanger is used to pre-heat the process gas as it enters the air pollution control unit. These are typically in the form of regenerative and recuperative thermal oxidizers. From there, a secondary and even tertiary heat exchange system can be utilized to further recycle thermal energy. Within industrial paint and coating applications, the inclusion of multi-stage heat recovery between the ovens and oxidation process not only ensures emission compliance, but enhances thermal efficiency and overall system performance, equating to a more sustainable, even, net-zero operation.
The following three project case studies demonstrate how a custom-engineered system that manages airflow and thermal recycling throughout the process has a multitude of benefits, regardless of production details or material specifications.
Case Study 1: Coating System for Metal Processing
The Challenge
A metal processing plant needed to replace several old coating line ovens and a stand-alone air pollution control system. Not only did the facility want to increase throughput capacity while remaining code compliant on emissions, but also increasing operating efficiency was top priority.
After extensive evaluation and consideration of the existing system operation, it was determined that the optimal solution for this application was a combination system layout, consisting of a 3-zone prime oven and 4-zone finish oven with a single thermal oxidizer, along with primary and secondary heat recovery systems. This comprehensive system capitalized on every part of the process, ensuring no heat nor material go to waste.
The Solution
With coating ovens, it is common to design the oven with multiple zones, depending on the process. The different zones within the oven allow for a gradual heating process, which can be a vital component when dealing with certain materials, such as paint or metal. In this particular system, the 3-zone prime oven cured the primer onto the metal, reaching temperatures between 500-600 °F. The 4-zone finish oven continued to cure the paint as the metal passed through each zone, gradually achieving the desired, peak metal temperature.
As the painted metal strips were cured in both the prime and finish ovens, the paint solvents evaporate. This air laden with VOCs is then extracted from the oven’s work chamber and routed through the primary heat exchanger of the thermal oxidizer. This primary heat exchanger pre-heats the process stream from the ovens above 1,100 °F to minimize the oxidizer’s burner fuel consumption. The VOC's exothermic reaction during the oxidation process further contributes to making the oxidizer’s retention chamber act as a self-sustaining agent without any additional burner heat input. Once the contaminated air from the prime and finish coater rooms is effectively cleaned by the thermal oxidizer, it is routed through the secondary heat exchanger. The use of a secondary heat exchanger further establishes an efficient, economic, closed-loop solution, as it continuously supplies pre-heated air back to both the prime and finish ovens.
Beyond the integrated oven/oxidizer system outlined, an additional tertiary heat recovery method was engineered into the process to further recycle the thermal energy and increase energy savings. A waste heat hot water heater was installed to capture available waste heat from flue gases to generate hot water needed for cleaning the metal strips, without having to use a burner and additional fuel.
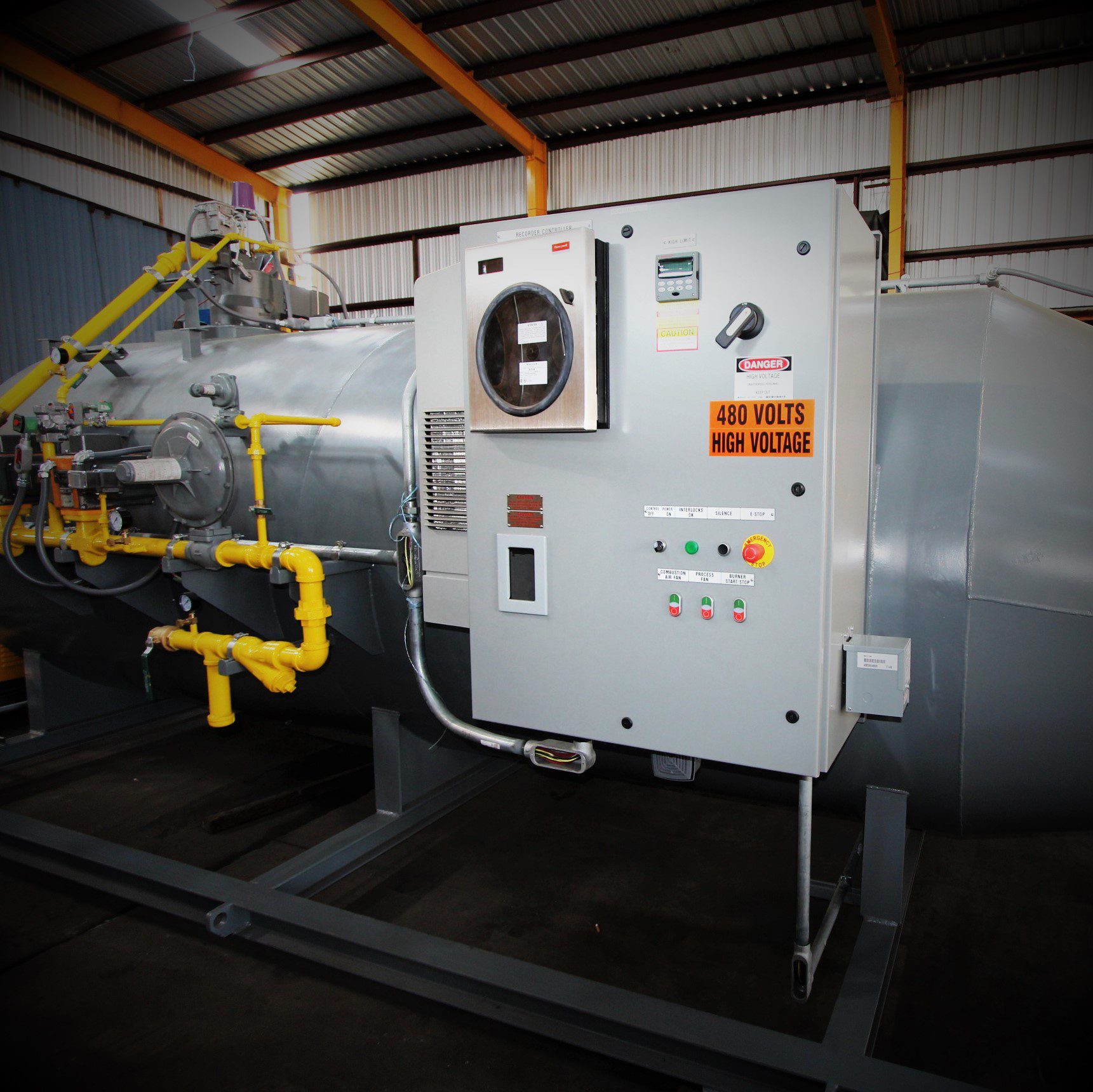
FIGURE 1 ǀ Waste-heat hot water heater installed as tertiary heat recovery to utilize excess thermal energy from flue gases to generate hot water needed for cleaning metal strips.
The Results
In the primary heat exchanger, when the solvent vapors oxidize and the exothermic reactions take place, the solvent acts as fuel to the oxidizer, reducing the fuel cost of operating the oxidizer to an absolute minimum. The primary heat exchanger ultimately resulted in savings of approximately 8.0 MMBTU per hour for the facility. The secondary heat exchanger recovers the waste heat from the thermal oxidizer, re-circulating the clean hot air back to the oven supply, which resulted in reducing the oven burner’s fuel consumption by approximately 6.0 MMBTU per hour. Furthermore, the addition of the waste heat hot water boiler, to heat the water up to the desired temperature, saved the facility an additional 3.0 MMBTU per hour.
In total, the new optimized system layout for this metal coating application resulted in a fuel savings of over 17.0 MMBTU per hour. That equaled an annual savings of $420,000 per year on fuel cost alone. This patented method of coupling the heat processing and air pollution control system, paired with seeking additional opportunities to capture and recycle heat, is a prime example of how thermal engineering can create value through efficiency during metal coating.
Case Study 2: Resin Application for Continuous Cord Manufacturing
The Challenge
A major engineering company was seeking a large 25,000 – 35,000 SCFM afterburner, or direct fired thermal oxidizer (DFTO), for a continuous cord resin-impregnating manufacturing plant. This facility was in violation of EPA rules and was about to be shut down. Their goal was to contain the total VOC capture from several sources: the mixing area, the storage area, the coating area and the curing ovens, and direct all of the contaminated exhaust throughout the operations to a single air pollution control unit. The fuel consumption for this undertaking would have been approximately $485 per hour.
The engineering company had no idea about the operating costs that would have been associated with a stand-alone afterburner of this size. They were working through a lawyer that was representing this company with the state agency, and their singular concern was VOC mitigation, and ensuring the facility would meet regulatory compliance to stay operational.
The Solution
Epcon’s application engineers studied the overall problem and came up with a solution that utilized a much smaller regenerative thermal oxidizer instead of the large 30,000 SCFM afterburner they were seeking. The regenerative thermal oxidizer would only need to be approximately 6,000 CFM as it was a comprehensive system that was integrated with the process heating ovens and utilized primary and secondary heat exchangers.
The primary heat exchanger was installed to preheat the incoming polluted exhaust from the various sources. By capturing all the affected areas’ fugitive-emissions and utilizing this latent process heat, the primary heat exchanger allowed for significant operational efficiency increases, as less fuel was needed to heat the oxidizer to the proper temperature for VOC destruction. Furthermore, instead of releasing the clean, hot air into the atmosphere, it was sent from the oxidizer to the secondary heat exchanger. The thermal energy was not wasted but recycled and supplied back to the three process ovens. This closed system was a double-whammy in fuel savings.
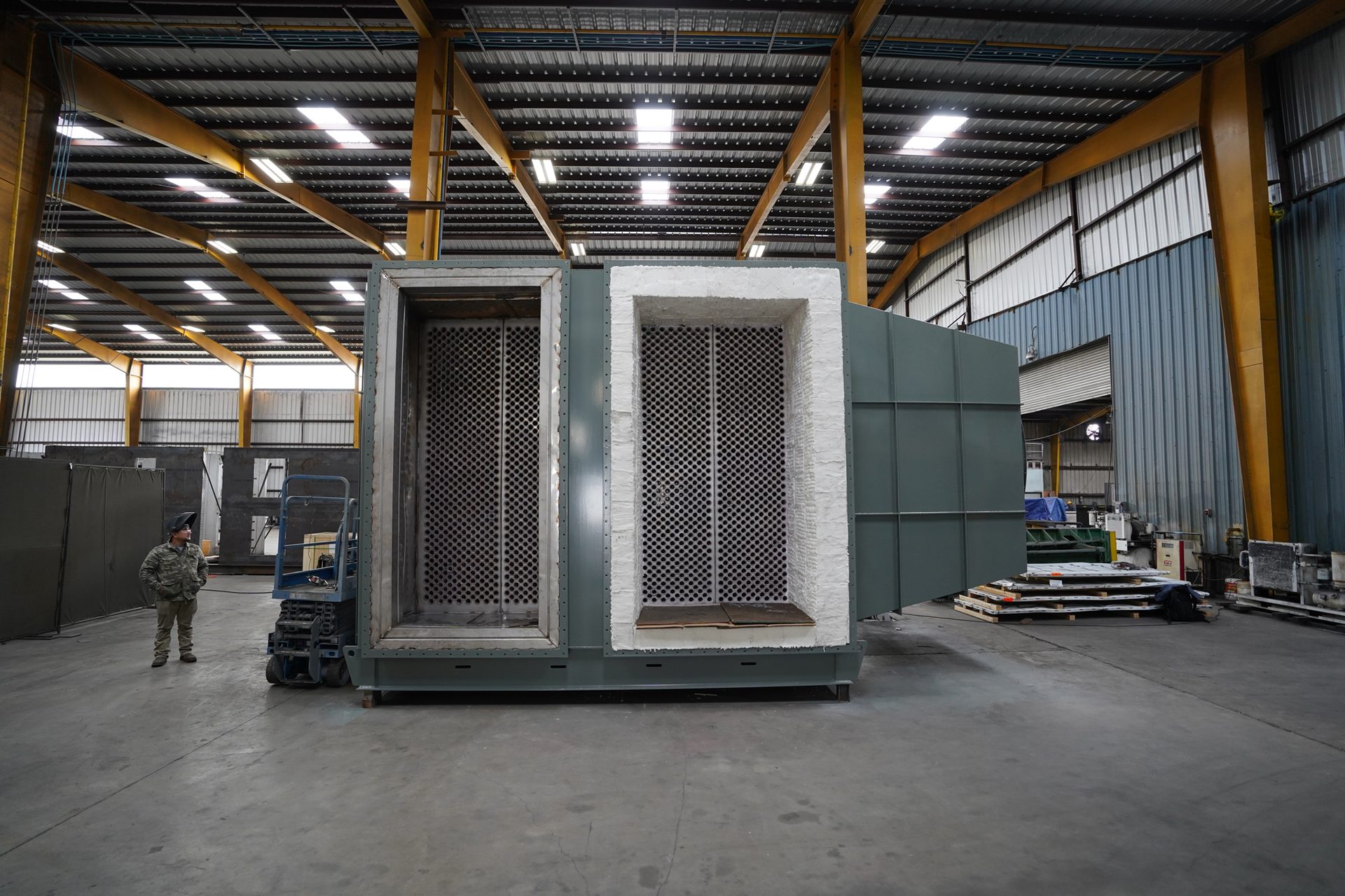
FIGURE 2 ǀ Cross section of the heat exchanger showing the shell and tube configuration that allows heat to be recycled between the thermal oxidizer and ovens.
The Results
Beyond meeting EPA compliance and being able to stay in business, the system had several additional benefits. First, it was a much smaller system than anticipated, with significantly lower upfront capital equipment footprint and cost. Additionally, the heat recovery from both the primary and secondary heat exchangers resulted in next to nothing fuel cost to operate the oxidizer and the ovens. And most importantly, the system’s overall safety was greatly enhanced. Due the thermal recovery of the secondary heat exchanger, the ovens, which have very high LFL (lower flammable limit), were able to operate without a burner or an ignition source.
Case Study 3: Metal Coil Coating Application
The Challenge
A coil coating operation, with line speeds up to 700 ft/min, utilized an old afterburner, and a 100-foot-long curing oven. Evaluating the appropriate oxidation system requires in depth analysis of the specific process gas and operating parameters, as there are many configurations to choose from. An afterburner, or direct fired thermal oxidizer (DFTO), is the most elementary system, as it contains no internal heat recovery system and is ideal for high VOC levels and fluctuating operating conditions.
The Solution
After much analysis, a more sophisticated system, comprised of a 45,000 SCFM regenerative thermal oxidizer along with multistage heat recovery methods was agreed upon. Typically utilized for larger process air flows, regenerative systems absorb and transfer heat between at least two fixed ceramic media lined beds, with a common combustion/retention chamber connecting the two. The hot air from the combustion chamber flows through one of the beds, heating it up, while the other discharges, alternating in continuous cycle of retention and purging. Regenerative systems can handle a range of process flow rates and typically yield a thermal energy recovery efficiency between 80% and 95%+.
For this design, both primary and secondary heat exchangers were incorporated into the overall system. The regenerative oxidizer’s cyclical airflow mechanics acts as the primary heat exchanger. The clean air leaving the regenerative oxidizer then continues onto the secondary heat exchange system, which utilizes the waste heat from the combustion process of the thermal oxidizer to run other parallel production processes throughout the manufacturing facility and pre-heat the various ovens.
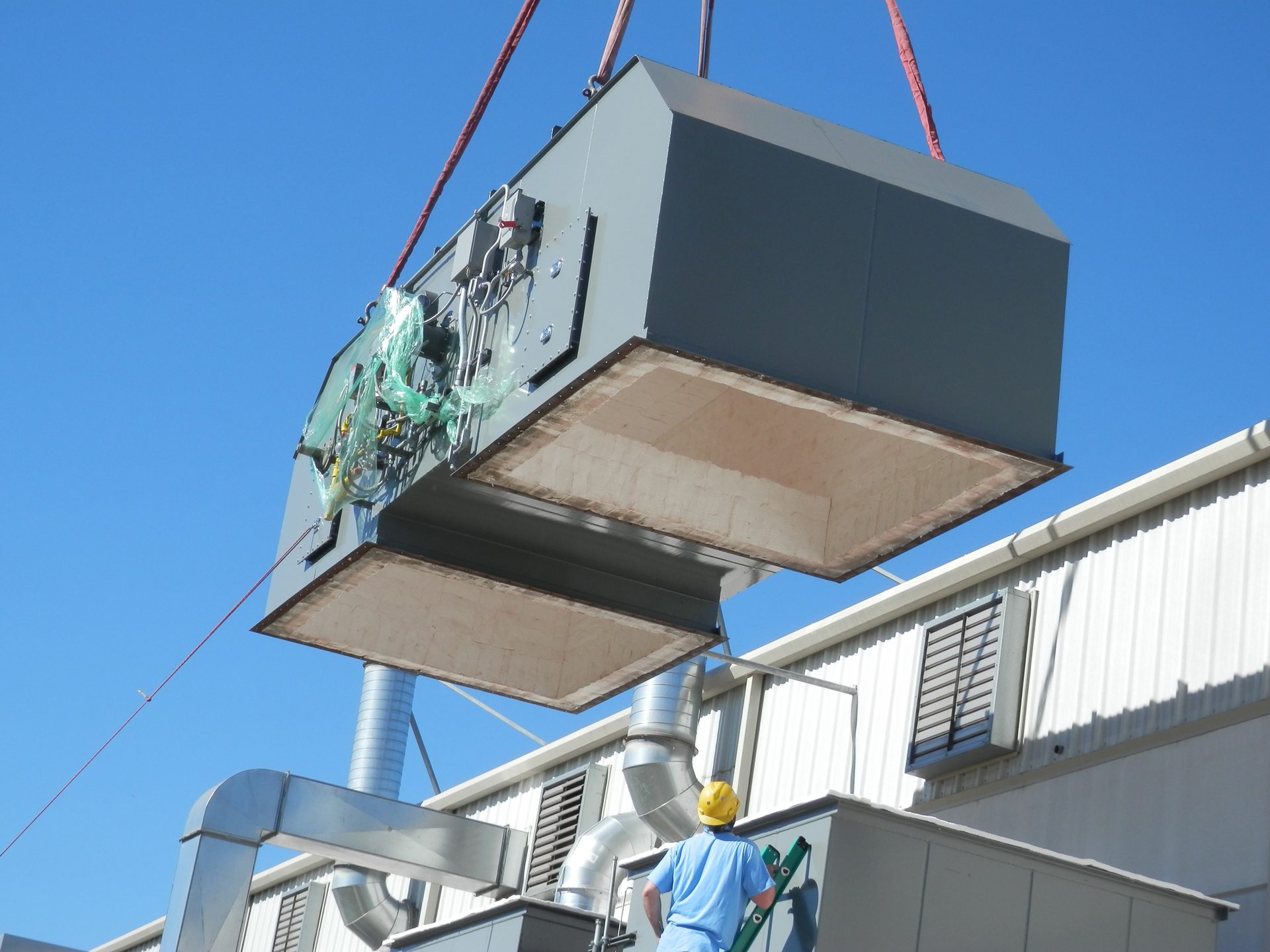
FIGURE 3 ǀ Installation of a regenerative thermal oxidizer showing the two ceramic media lined beds used in the alternating heat recovery cycling.
The Results
The old system with the inefficient afterburner system used 40 million BTU/hr. The new regenerative thermal oxidizer with primary and secondary heat exchangers reduced the fuel consumption down to 16 million BTU/hr, a savings of 24 million BTU/hr, which translated into 210 billion BTU saved annually.
Conclusion
An “oven/oxidizer” combination system can be implemented in almost any manufacturing facility that requires both process heating equipment and an air pollution control system. Based on the unique application requirements, different types of heat exchangers can be strategically integrated into the overall system. As demonstrated by these three different paint and coating applications, by continuously recycling the heat between the oxidizer and ovens via heat exchangers, a combination system can create optimal operational efficiency and allow a facility to capitalize on the thermal energy across the entire process.
When building a new facility or replacing old paint and coating lines, its critical to have a heat recovery expert asses the overall process, and potentially re-engineer the stand-alone equipment into an integrated system. By extracting and recycling heat at various stages in the process, multi-stage heat recovery can create a closed-loop system and is the best way to maximize your process efficiencies and reduce operating cost and fuel consumption.
*All images courtesy of Epcon Industrial Systems.