Ready to proof -- Clare 10/11/22
CB proofed 10/12 - left comment for CJ below.
KJ - Do you like the video at the end? Do we need to add a subhead/description?
CLJ revised on 10/12
KJ proofed on 10/13. There are notes for both Courtney (for Table 1) and Clare (moving a few figures and the video). Courtney, I think we should also re-number the references so that they appear in numerical order (they start with 4 and then go to 1, etc. So just renumber then 1-4 in the copy, and then re-arrange them at the bottom so that they match up. Thanks.
CLJ revised on 10/13
KJ: Just need to renumber the references still. Everything else clean for me.
CB revised table and references 10/14 - clean on my end
Highly Branched Vinyl Ester-Based Binders for Elastomeric Roof Coatings
Credit info / Collection info, via Getty Images.
By Vanaken David, Nguyen Lan and Yan Zegui, Hexion Inc.
Elastomeric roof coatings have been used for many years to extend the useful life of several types of roofing substrates. The roof coatings market has seen significant growth, driven by the “cool roof” movement. By using a white roof coating, the underlying building and surroundings can be protected from excessive heat buildup. A proper white reflective elastomeric coating offers reduction in temperature and hence, a reduction in cooling costs.
Elastomeric roof coatings need to have very good water barrier properties. High water resistance is required so that the elastomeric coating can withstand ponding water, which can occur on low-slope roofs. Good adhesion to the substrate and good weatherability are some of the other factors that contribute to a long service life of the roof coating.
Traditionally, acrylates and styrene have been used as main monomers in the emulsion polymerization process to make latex binders for elastomeric coatings. This article describes the use of the very hydrophobic, highly branched VeoVa™ vinyl esters1 (VV10) for high-performance binders for elastomeric coatings.
Climate and Binder Type
Hot summers, cold winters, high daytime heat from the sun, and significant nighttime cooling mean that, depending on the regional weather conditions, an elastomeric roof coating needs to be able to perform even in the most challenging situations.
Figure 1 shows the differences in monthly 24-hour average temperatures for Phoenix, Arizona, and Chicago, Illinois. Both in Phoenix and Chicago, temperatures vary by as much as 25 °C between summer and winter, with 24-hour average temperatures going well below freezing for Chicago in winter. Furthermore, in desert climates such as Phoenix, intraday temperatures can vary by as much as 30 °C going below 0 °C at night.

FIGURE 1 ǀ Regional temperature differences.
Since the properties of elastomeric materials are affected by the temperature of the roof and of the surface air, the polymeric binders used in the roof coatings need to exhibit flexibility and good elongation even at the lowest possible temperatures for the local climate. Therefore, an elastomeric roof coating used in climates with minimum temperature fluctuations and year-round high, average temperatures can be formulated with a much harder binder than a roof coating used in climates with pronounced temperature differences between summer and winter, or climates with high intraday differences.
Norms and Standards for Elastomeric Roof Coatings
Some of the most important tests for elastomeric roof coatings are tensile strength, elongation, and water absorption. Other tests often performed are peel adhesion, low-temperature flexibility, accelerated weathering, water vapor permeability, and recovery after elongation. Norms and standards as well as test methods differ per region and country. In the United States there are several standards classifying the performance of elastomeric roof coatings, including ASTM D6083, the Energy Star program, California Energy Commission Title 24, and several regional ones. ASTM D6083, “Standard Specification for Liquid Applied Acrylic Coating Used in Roofing,” is one of the most well-known standards.2
Monomers for Elastomeric Binders
Latex polymers for elastomeric roof coatings are prepared by emulsion polymerization. In this process, different monomers are polymerized in water through free-radical polymerization. A polymer needs to have a low Tg to be flexible at low temperatures. Therefore, latex polymers for elastomeric roof coatings typically consist of a combination of low-Tg and high-Tg monomers to obtain the desired balance between elongation and tensile strength.
Besides flexibility, water resistance is one of the most important properties of a roof coating. The water resistance of a coating is mainly governed by the composition of the polymeric binder and therefore by the monomer used. If one takes water solubility of the monomers as an indication of hydrophobicity, it becomes clear that the vinyl ester of neodecanoic acid (VeoVa 10 vinyl ester) has a much higher hydrophobicity than other monomers commonly used in emulsion polymerization (Table 1).3 In addition, the homopolymer Tg of the VeoVa 10 monomer (VV10) of -3 °C is rather low, between those of hard monomers such as styrene and methyl methacrylate (MMA) and those of softer monomers such as butyl acrylate (BA) and 2-ethylhexyl acrylate (2-EHA).
TABLE 1 ǀ Water solubility and Tg of some commonly used monomers.
The very high hydrophobicity of the VV10 monomer combined with a Tg suitable for the preparation of low-Tg polymers makes it a very interesting candidate to develop novel, high-performance binders for elastomeric coatings.
Highly Branched VeoVa Vinyl Esters
VV10 is an ideal vinyl monomer for the production of latices for high-quality water-based elastomeric coatings. It finds its principal use as a hydrophobic co-monomer in vinyl and acrylic polymerization. This vinyl ester molecule has a unique, highly branched tertiary substituted α-carbon structure. Therefore, this alkyl neodecanoate group is resistant to degradation in alkaline conditions as there is no hydrogen on the α-carbon and in addition the bulky alkyl structure protects the ester function of the molecule. The branched tertiary structure with bulky and hydrophobic hydrocarbon groups provides the VV10 vinyl ester (Figure 2) with a highly hydrophobic nature and a low surface tension. Furthermore, VV10 vinyl ester exhibits strong resistance to hydrolysis and does not degrade under the influence of UV light.
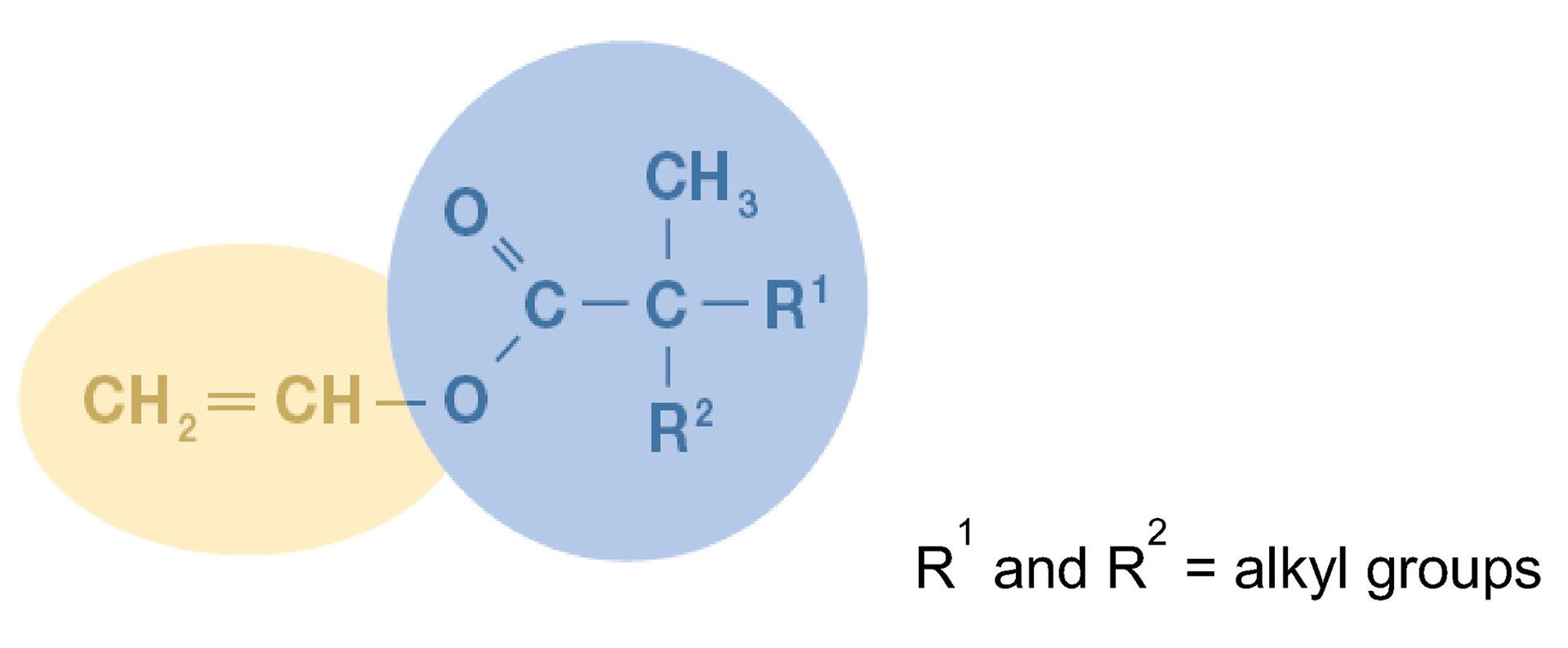
FIGURE 2 ǀ Chemical structure of VV10 monomer.
VV10 monomer polymerizes with various other monomers through its vinyl ester functional group. In this way the specific properties of the monomer can be imparted to its copolymers.
VV10 can be used in combination with a variety of other monomers to produce various polymers. The ease of polymerization depends on the reactivity ratios of the monomers used (Table 2).
TABLE 2 ǀ Reactivity ratios of vinyl esters with other monomers.
The data in Table 2 show that VV10 exhibits reactivity similar to that of vinyl acetate. There is a difference of reactivity between vinyl esters and (meth)acrylate monomers, yet this difference is such that they can still co-react in emulsion polymerization.
VV10 Vinyl Ester-Modified Acrylics
VV10 monomer readily copolymerizes in emulsions with acrylate and methacrylate monomers. The bulky and hydrophobic hydrocarbon structure of the VV10 monomer enhances the polymer and provides a high degree of water repellence, hydrolysis resistance and improved adhesion to low-surface-energy substrates such as TPO and EPDM. VV10/acrylic latices represent a family of polymers with a wide range of possible polymer compositions and performance properties. Any incorporation of VV10 monomer leads to significant improvements in water resistance and adhesion to plastics, and the effect increases with increasing VV10 content.
The water repellence effect can be demonstrated visually in a water beading test shown in the video below, and also by measuring contact angles. Figure 3 shows the spreading of equally sized droplets of water over various acrylic paints. Acrylic systems modified with 30% VV10 had a high water contact angle of 79 degrees. On the VV10-modified acrylic paint the water beads to a small droplet, while on pure acrylic systems containing either BA or 2-EHA the water readily spreads out over a large area of the paint surface.
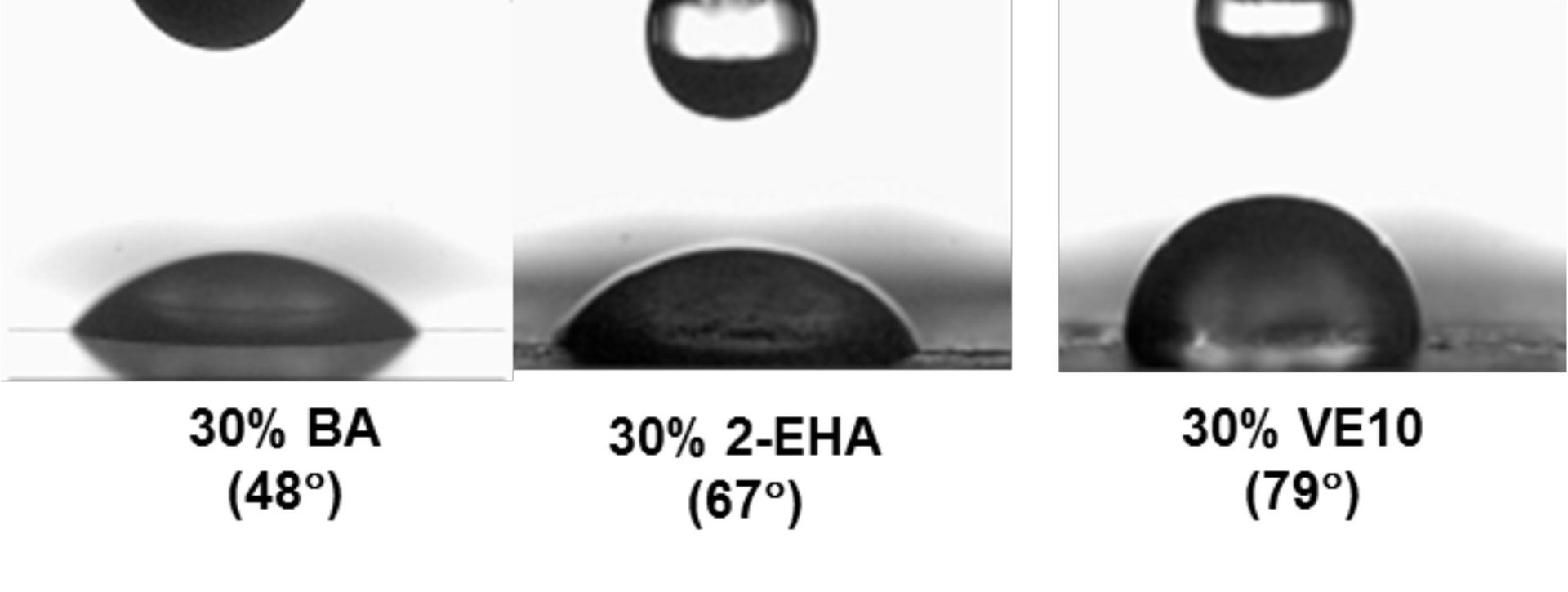
FIGURE 3 ǀ Beading effect and contact angle of VV10/acrylic-based paint.
Water Absorption
According to the ASTM 6083 standard, the water absorption test must be performed following ASTM D471. In this study, elastomeric coating samples based on all-acrylic binders and on VV10-modified acrylic binders were immersed in water for 14 days.
It becomes clear from Figure 4 that the incorporation of the hydrophobic VV10 monomer into the acrylic backbone also reduces the water swelling of acrylic polymers. The more VV10 monomer incorporated, the lower the amount of water absorbed into the elastomeric membrane. At 30% VV10 monomer (on total monomers), the amount of water absorbed into the coating drops to below 10%, well below the maximum of 20% specified by ASTM 6083.
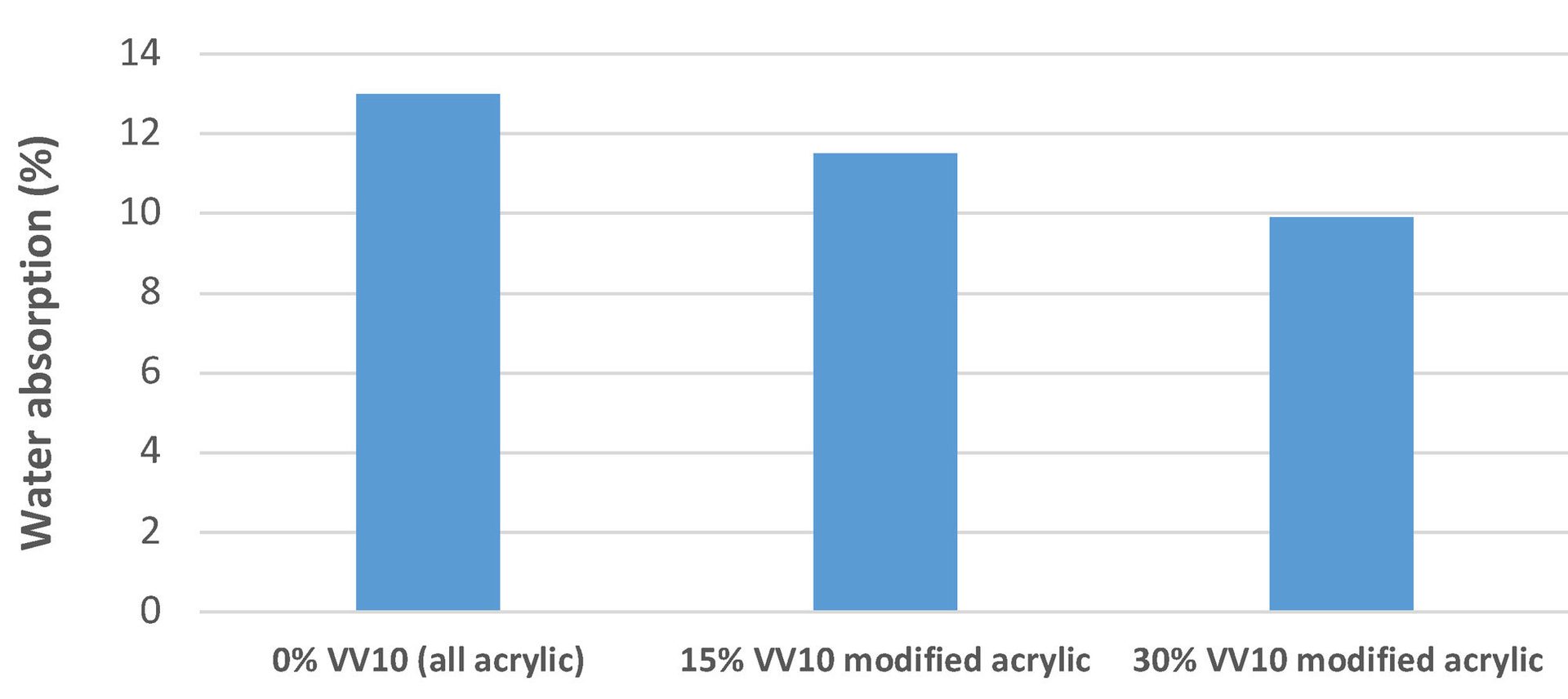
FIGURE 4 ǀ Water absorption all-acrylic vs. VV10-modified acrylics.
Elongation at Break
Elongation is measured as percentage of the maximum deformation when the sample breaks. At iso-Tg an increase in VV10 content leads to a significant increase in elongation (Figure 5).
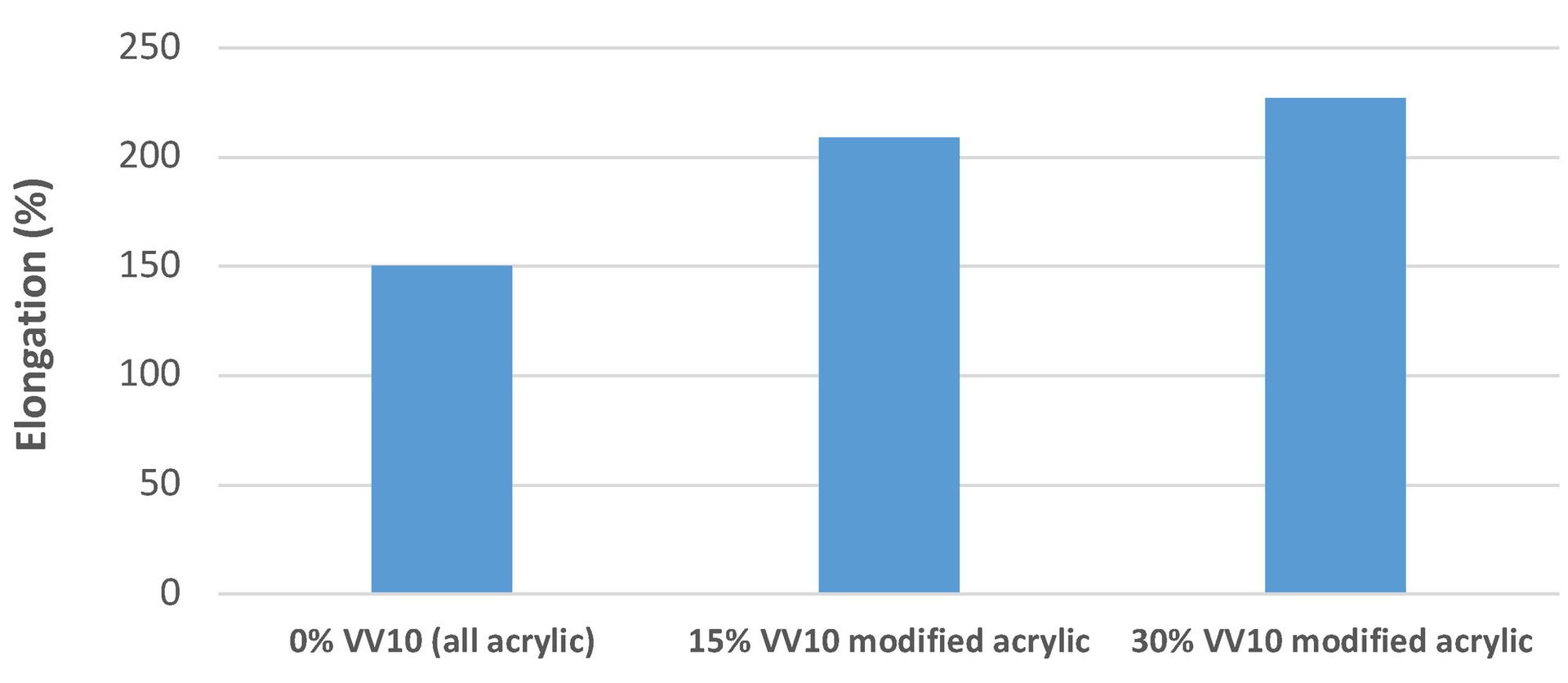
FIGURE 5 ǀ Elongation of elastomeric coatings. All-acrylic vs. VV10-modified acrylics.
Adhesion to TPO
TPO and EPDM roofing membranes are popular roofing systems in the United States. The development of waterborne elastomeric roof coatings with sufficient adhesion to the surface of weathered TPO roofing membranes has been challenging. Since polymers made with VV10 monomer have lower surface tension and increased hydrophobicity, VV10-modified acrylics make good candidates for water-resistant elastomeric roof coatings with good adhesion to polyolefinic substrates.
A series of elastomeric roof coatings based on VV10-modified acrylics was applied onTPO. Both wet and dry adhesion was tested (ASTM C794) at a peel rate of 2 inch/min. Wet adhesion was measured after the samples were immersed in water for 7 days.
As can be seen from Figure 6, the incorporation of VV10 in the acrylic backbone has a very positive effect on both the dry and wet adhesion of the roof coating to TPO, with higher levels of VV10 leading to further improvements in adhesion. The low surface tension of the VV10-based polymers leads to an improved wetting of the TPO surface while the increased hydrophobicity allows maintaining good adhesion under wet conditions.
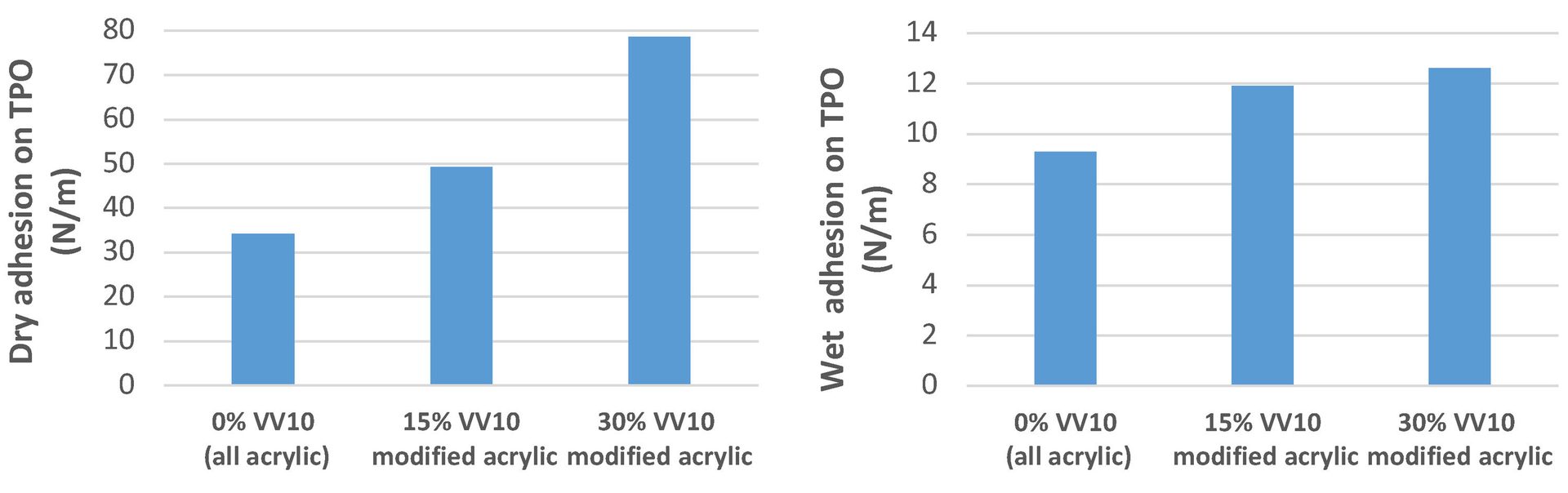
FIGURE 6 ǀ Dry adhesion (left) and wet adhesion (right) on TPO.
VeoVa/Vinyl Acetate/Acrylate Emulsions
VV10 monomer and vinyl acetate exhibit very similar reactivities in free-radical emulsion polymerization, which yields polymers with monomer units randomly distributed along the chains. This is important because it allows the key performance characteristics of VV10 monomer to be fully utilized. The unique, highly branched, carbon-rich structure of VV10 monomer sterically protects its ester group from hydrolysis. More importantly, it also protects neighboring acetate groups (Figure 7), thus improving the hydrolytic stability of the polymer. This protection is called the “umbrella effect,” 4 and enables such polymers to be successfully used as paint binders even on very alkaline substrates.
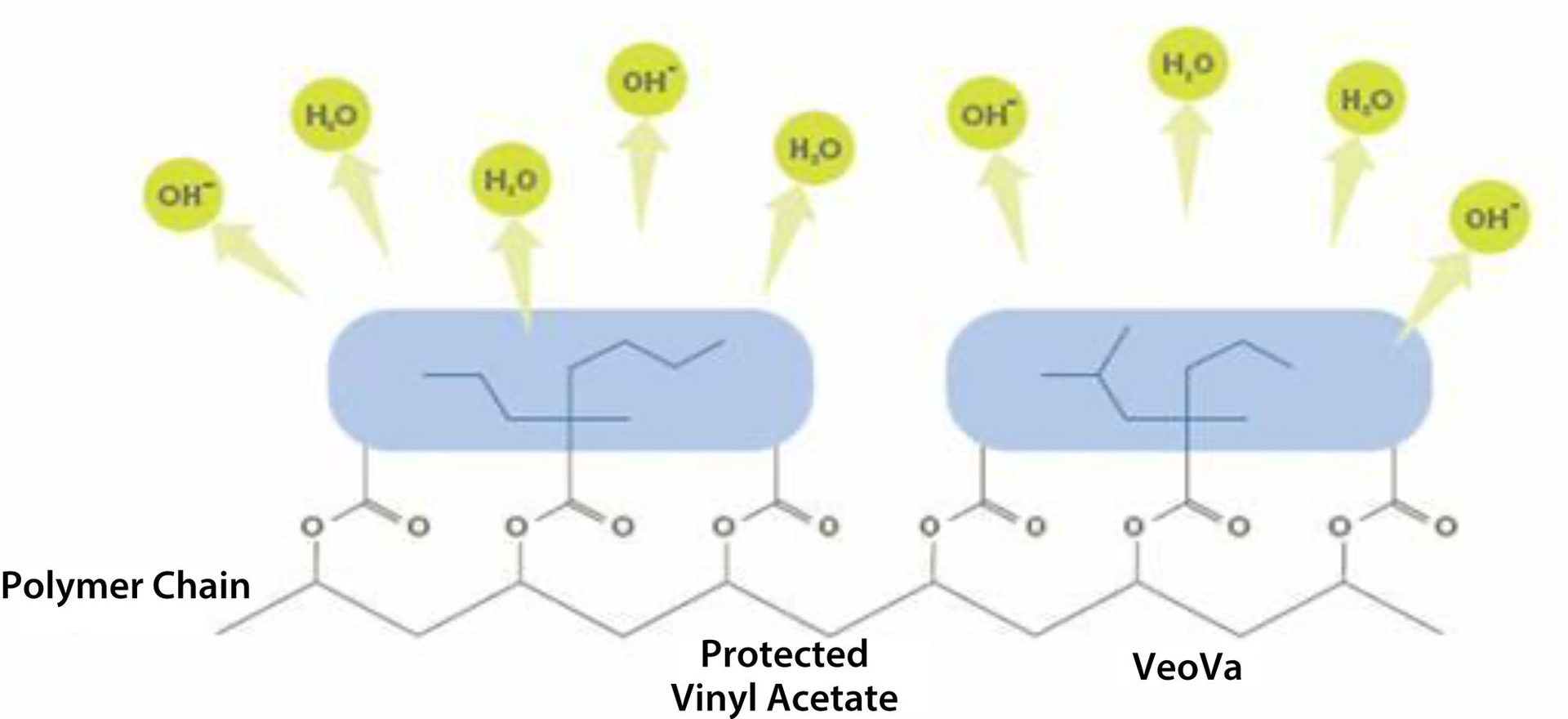
FIGURE 7 ǀ Protection of the acetate groups by adjacent VV10 groups.
Soft, plasticizing, acrylate monomers such as BA (Tg -40 °C) and 2-EHA (Tg -65 °C) can be used to improve the flexibility of vinyl acetate-based polymers. Unlike VV10, these acrylates do not protect the adjacent acetate groups from chemical attack and therefore such systems have the major disadvantage of low hydrolytic stability, leading to poor outdoor durability. The addition of VV10 monomer to such polymers to form terpolymers with vinyl acetate and acrylates substantially upgrades the hydrolytic stability, while allowing to retain a good flexibility. In addition, outstanding water resistance and outdoor durability, good elongation, and tensile strength can be achieved for elastomeric roof coatings.
As an example a vinyl-modified acrylic resin based on vinyl acetate, VV10, and butyl acrylate was synthesized. This resin was tested in a formulated elastomeric roof coating against a leading all-acrylic emulsion. The performance of these systems against the reference is summarized in Figure 8.
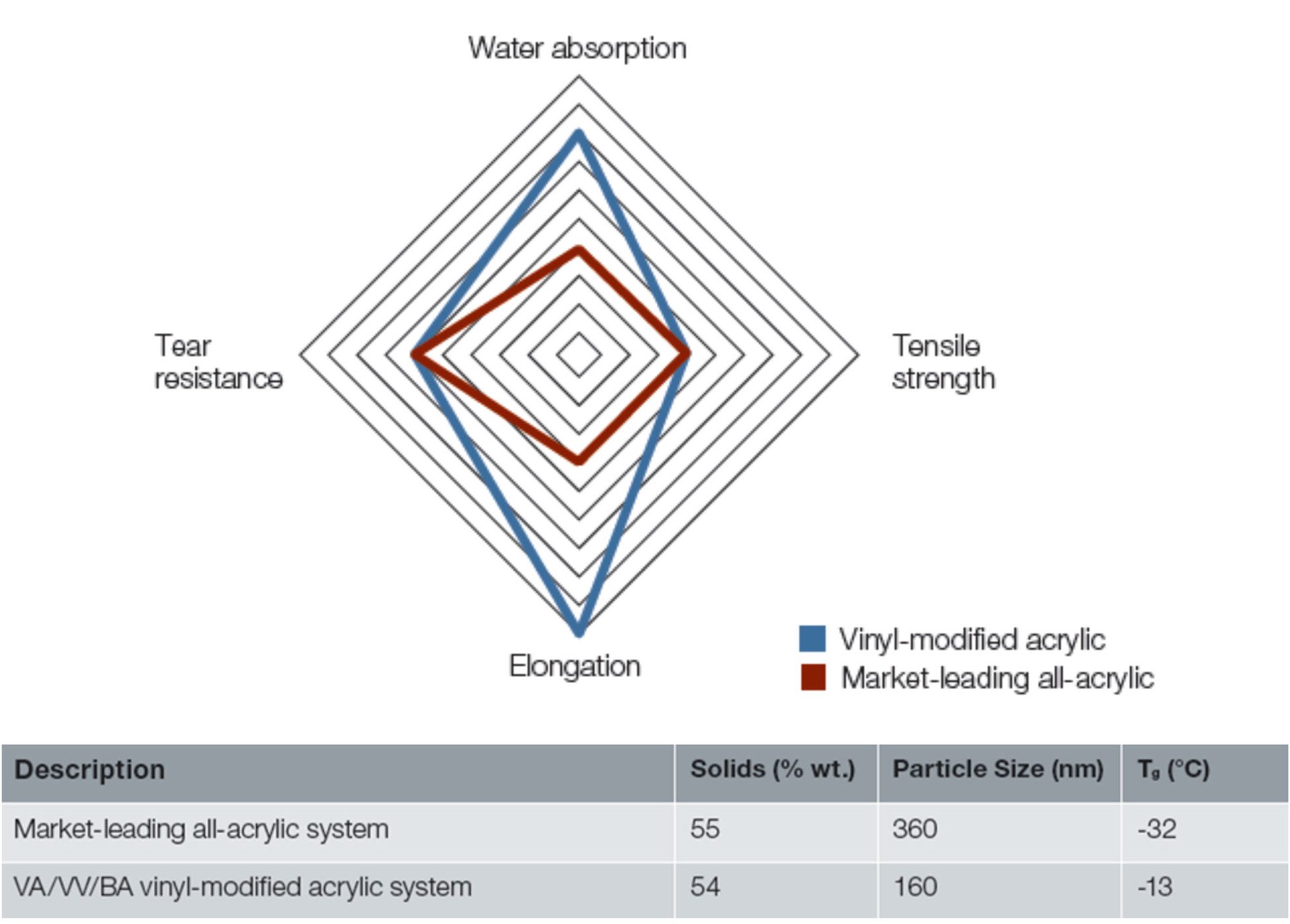
FIGURE 8 ǀ Overall performance in elastomeric roof coatings. Vinyl-modified acrylic vs all-acrylic.
Roof coatings based on VV10 terpolymers (vinyl-modified acrylic) combine very high elongation with high tensile strength. The VV10 terpolymer-based system has a much higher elongation than the lower Tg commercial all-acrylic system. The very hydrophobic VV10 monomer also imparts very low water absorption, often superior to commonly used acrylic polymers. Since these terpolymers are based on a relatively low-cost vinyl acetate-based monomer, high-quality vinyl ester-based polymers offer the formulator a cost-efficient option to design coatings that match and even outperform the current products for elastomeric roof coatings.
Blending Resins
Latex blending is mixing two or more type of emulsion. It is also a technique used to reduce the overall cost. The selection of blend resins are often based on their hydrophobicity, particle size or Tg.
Two VV10-based systems to be used as blending resins for all-acrylic resins were tested:
- A vinyl-modified acrylic resin based on vinyl acetate, VV10 and butyl acrylate;
- A vinyl system rich in VV10 containing 80%VV10 and 20% VAM monomer (Veopol).
These resins were blended at 30% on polymer solids with a market-leading, all-acrylic resin and tested in formulated elastomeric roof coatings against the base all-acrylic emulsion.
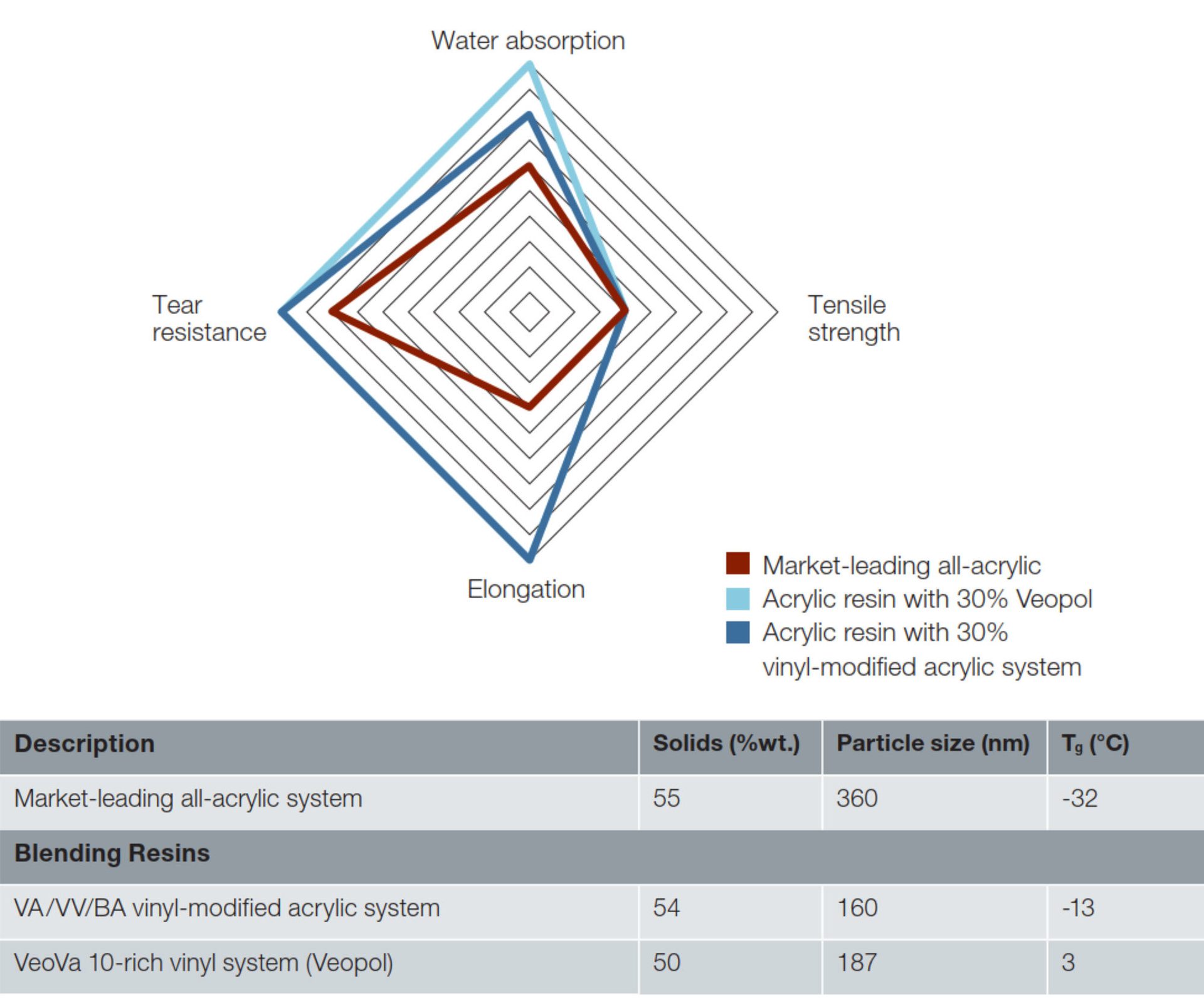
FIGURE 9 ǀ Overall performance of VV blending resins in elastomeric roof coatings.
The blending resins allow easy upgrade of a wide variety of different elastomeric roof coating formulations, leading to a reduced water absorption and substantially increased elongation (Figure 9).
Conclusions
VV10 monomer significantly upgrades the overall performance of the binders used in roof coatings.
Combining VV10 monomer with acrylate monomers offers a versatile tool to formulate various high-performance emulsion polymers for use in elastomeric coatings with an increased water resistance, high elongation, and improved dry and wet adhesion to TPO.
Production of vinyl acetate / VV10 polymers is easy due to the favorable reactivity characteristics of the VV10 monomer and vinyl acetate. Roof coatings based on VV10 vinyl ester terpolymers combine very high elongation with high tensile strength and excellent water resistance. Since these terpolymers are based on a relatively low-cost vinyl acetate monomer, high-quality vinyl ester-based polymers offer the formulator a cost-efficient option to design coatings that match and even outperform the current products for elastomeric roof coatings. Highly hydrophobic, pre-polymerized, VV10-rich resins offer an innovative route to easily modify existing elastomeric roof coating formulations through simple blending.
Contact: David Vanaken, david.vanaken@hexion.com, https://veovahouse.hexion.com
References
- ® and ™ denote trademarks owned by or licensed to Hexion Specialty Chemicals Inc.
- ASTM D6083 “Standard specification for liquid applied acrylic coating used in roofing".
- Basett, D. Hydrophobic coatings from emulsion polymers, Journal of Coatings Technology, 2001, pp. 43.
- Vanaken, D.; Arriaga, V. “Branched vinyl ester monomers for hydrophobic emulsion polymers”, Proceedings of the 40th Annual International Waterborne, High Solids, and Powder Coatings Symposium, February 2013, pp. 117-131.