Ready to proof -- Clare 9-12-22
CB proofed 9/14 - clean on my end
KJ proofed on 9/14 - clean on my end
FORMULATING WITH MIKE
High-Speed Dispersion
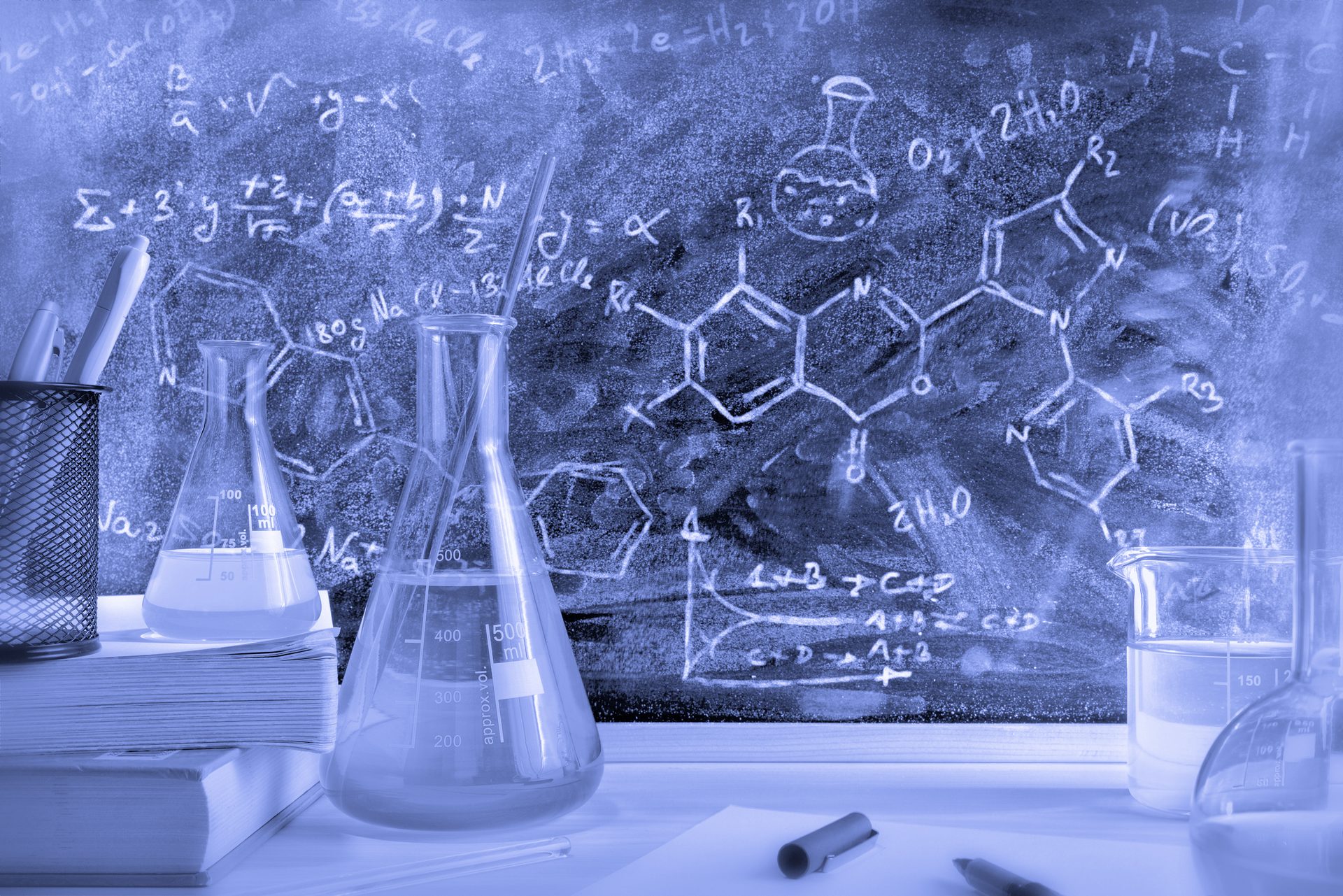
Davizro / iStock / Getty Images Plus, via Getty Images.
By Mike Praw, Technical Service and Development Manager — Coatings and Performance Products, Indorama Ventures: Integrated Oxides and Derivatives, The Woodlands, TX
Continuing August’s article on pigment dispersion, this article will cover high-speed dispersion. As a younger formulator 20-plus years ago, I attended a presentation on “Practical Paint Making” by George Goodwin. I learned a lot that day and wish to thank him for taking the time to pass on his knowledge. This article will cover some of that material, so while I write this, it would not be as good without his training and material.
Dispersion is the process by which non-soluble substances are uniformly incorporated into a liquid phase and stabilized against settling or separation once mechanical energy is no longer applied to the system.
A good dispersion:
- Breaks up clumps (aggregates and agglomerates) but does not reduce primary particle size.
- Ensures uniform pigment in the paint.
- Maximizes hiding power, tint strength, gloss, and eliminates grit.
- Saves time and money (quicker and more efficient dispersions and less in-process adjustments).
- Maximizes properties and minimizes raw material costs.
The three steps of dispersion (covered in depth in the August 2022 “Formulating with Mike” article) are:
- “Wetting” of the pigment.
- “Dispersing” the particles, deagglomeration, and deaggregation.
- “Stabilization” of the pigment against settling by the dispersant.
Figure 1 shows the setup for optimizing high-speed dispersion.
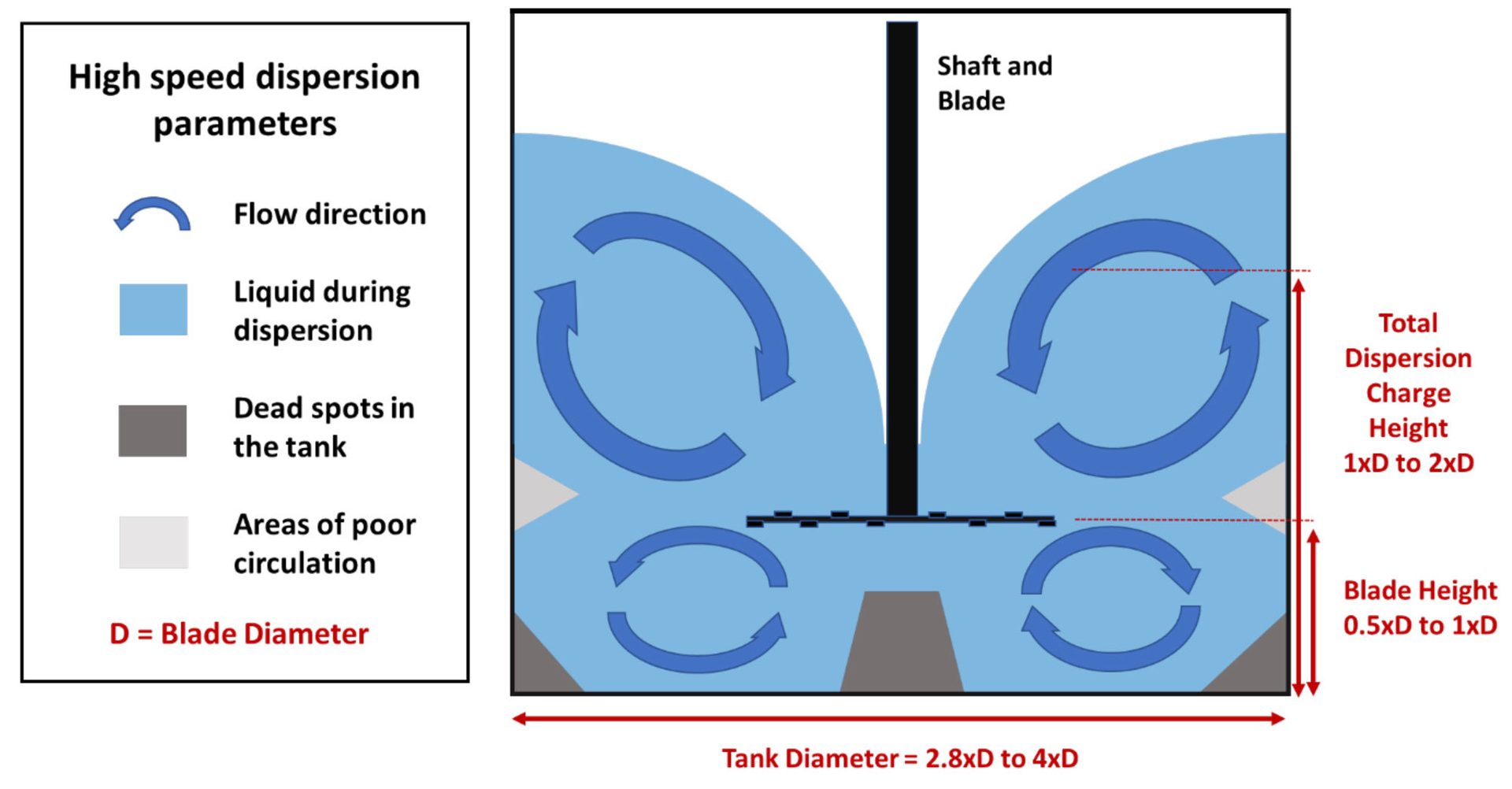
FIGURE 1 ǀ High-speed dispersion optimization.
The size of the high-speed dispersion blade in relation to tank size and liquid volume for efficient high-speed dispersion is fixed. The blade to tank size ratio for the most favorable dispersion is that the tank is 2.8 to 4 times the blade diameter, with an optimum around 3 times the blade diameter. During charging of the dispersion, the minimum blade height from the bottom of the tank should be 0.5 of the blade diameter and closer to blade diameter during dispersion. The optimum liquid height should be close to 2 times blade diameter. While you can successfully disperse pigment outside of these parameters, experience has shown these conditions to give the best balance of minimizing dispersion time and maximizing pigment dispersion.
The liquid in the tank during dispersion moves due to the pumping action of the teeth of the blade. There are, however, some locations in the tank with less than optimal circulation. In Figure 1, you can see there is a zone in the middle of the tank that can have poor liquid flow. It is possible to determine if the flow in this zone is appropriate using temperature variation. As the dispersion is proceeding, the batch will warm up. Before the advent of low-cost thermal sensors, it was common for the dispersion operator to touch this area to determine if there was a temperature difference between it and the rest of the tank. If a difference was noticed, the blade speed or height was adjusted to improve circulation. With current temperature-sensing instrumentation and computerized batch production, it is very easy to avoid areas of poor circulation.
The tank also has some dead spots of very poor circulation. These areas are maximized during pigment addition preceding the dispersion. A combination of lower blade height, lower blade speed and too fast pigment addition will lead to areas of pigment accumulation. Once the pigment accumulates in these dead spots it will be difficult to reincorporate the pigment into the dispersion. To avoid this, a slow, constant pigment addition is key. Figure 1 depicts these areas.
During high-speed dispersion, most of the dispersion takes place on or adjacent to the blade.
- 25% of the dispersion takes place on the blade by shear.
- 70% of the dispersion occurs in laminar flow as each layer of mill paste accelerates at a different rate.
- The remaining 5% occurs as the mill paste circulates in the tank.
These percentages are from “Practical Paint Making” by George Goodwin.
As the liquid is moved onto the blade due to flow, it enters near the shaft. At this point the liquid has almost no rotational velocity. The liquid is rapidly accelerated as it spirals from the center of the blade to the edge. This rapid acceleration results in shear forces on the liquid, which helps break up pigment particles (the 25% of dispersion that takes place on the blade). Since high-speed dispersion is optimized for laminar flow, as you move away from the blade parallel to the blade, the velocity of the liquid is reduced. These layers of different velocity create shear forces that also disperse the pigment (the 70% of shear due to laminar flow). The remaining 5% of dispersion takes place from pigment particles colliding, and other forces in the tank. Contrary to popular belief, the teeth are designed to provide pumping action and do not chop up the pigment. It is important that both the top and bottom of the blade be covered during dispersion to maximize liquid contact with the blade.
While there are potential pitfalls in the dispersion process, the following steps will help avoid them:
- Position the shaft in the center of the tank and adjust height to form a deep vortex.
- Do not choke the blade by adding too much pigment at once. Pigment should not float on top of the mill base, or it will erupt in mushroom clouds over the tank.
- As pigment is added, adjust speed and blade height as necessary to maintain the vortex.
- Excessive speed while adding the pigment will overheat the batch and cause splashing.
- Too little speed will cause pigment to float and not wet the pigment.
- Once all the pigment is in, the blade should be about one blade diameter from the tank bottom (mark the shaft or hydraulic cylinder to identify this point).
- Once all the pigment is added, and none is floating, scrape the side of the tank and shaft (if possible), and then rinse them to ensure all the pigment is in the mill base. Undispersed pigment on the side of the tank will just ruin a good dispersion.
- Offset the blade to the side of the tank, halfway between the center and the side of the tank. The blade edge should never be closer to the side of the tank than half the blade diameter.
- Offsetting the blade will increase flow, minimize the vortex, and allow higher speed without splashing or excessive air entrapment.
- At normal dispersion speeds (4,500-5,500 ft/min tip speed) the off-center blade creates one or more vortices.
- To properly disperse pigment, you need good circulation. As the batch warms up, check circulation by measuring the temperature of the tank at various places. If circulation is sufficient, the tank should warm up uniformly. If circulation is not sufficient, adjust dispersion parameters.
- After about 15-20 minutes, check the grind using a Hegman gauge. If the mill base is optimized and the blade position and speed are correct, the grind should be done and the letdown started. Do not let mill pastes sit overnight.
- If the blade is visible and the liquid is high up the tank walls, the blade may be on upside down.
- During the letdown process, check pH before adding raw materials. Add the letdown ingredients slowly under agitation to avoid “shocking” the mill base. For water-based systems, letdown with water first and avoid adding resin emulsions if the grind is over 120 °F.
While there are multiple different blade designs, it is critical the blade have teeth. The teeth provide pumping action in the tank to maximize circulation and bring new material to the blade and prevent the mill base from sliding across the blade too fast for efficient dispersion. The pumping action of the blade must match millbase viscosity. Too much pumping will result in the top of the blade being uncovered, a large vortex incorporating too much air, and in extreme cases, the liquid splashing out of the tank. Too little pumping results in new material not getting to the blade, and overheating material near the blade that damages raw materials.
While high-speed dispersion requires planning and proper setup, it can be done, resulting in excellent pigment dispersion.
All information contained herein is provided "as is" without any warranties, express or implied, and under no circumstances shall the author or Indorama be liable for any damages of any nature whatsoever resulting from the use or reliance upon such information. Nothing contained in this publication should be construed as a license under any intellectual property right of any entity, or as a suggestion, recommendation, or authorization to take any action that would infringe any patent. The term "Indorama" is used herein for convenience only, and refers to Indorama Ventures Oxides LLC, its direct and indirect affiliates, and their employees, officers, and directors.