Ready to proof -- CLJ 08/04/21
Ready for author
FORMULATING WITH MIKE
Introduction to Additives
Part 3
Surface Tension Modifiers
Video: SoraPhotography, Creatas Video+ / Getty Images Plus, via Getty Images
Top Photo:Davizro, iStock / Getty Images Plus, via Getty Images
By Mike Praw, Senior Applications Scientist – Paints, Coatings and Inks,
Indorama Ventures: Integrated Oxides and Derivatives, The Woodlands, TX
This is the third in a series of four articles on coatings additives. Previous articles have covered rheology modifiers and defoaming. The fourth article will cover pigment dispersants and the pigment dispersion process. This article discusses surface tension modifiers. In particular, I will only be covering the surface tension of liquid coatings on solid substrates in this article.
Surface tension is the macroscopic effect of the cohesive forces between molecules to minimize the surface area. Surface tension is defined as the force per unit length exerted by a stretched liquid membrane. Wetting out a substrate is the interaction of the surfaces of the liquid and the substrate, or the surface tensions of both. This is often reported as Dynes/cm and are the units I will be using.
Contact angle (θ) is the angle between the line tangent to the surface of the liquid and the surface of the substrate. This is used to determine how well a liquid will wet out the surface. If the cohesive forces (forces between molecules of a liquid) are stronger than the adhesive forces (forces between the liquid and the substrate), the liquid will bead and not wet out the substrate. In this case the contact angle will be between 90° and 180°. If the adhesive forces are stronger than the cohesive forces, the liquid will wet out the substrate and the contact angle will be between 0° and 90°. If the adhesive forces are significantly stronger than the cohesive forces, you will observe complete wetting with a contact angle around 0°. These three wetting scenarios are shown in Figure 1.
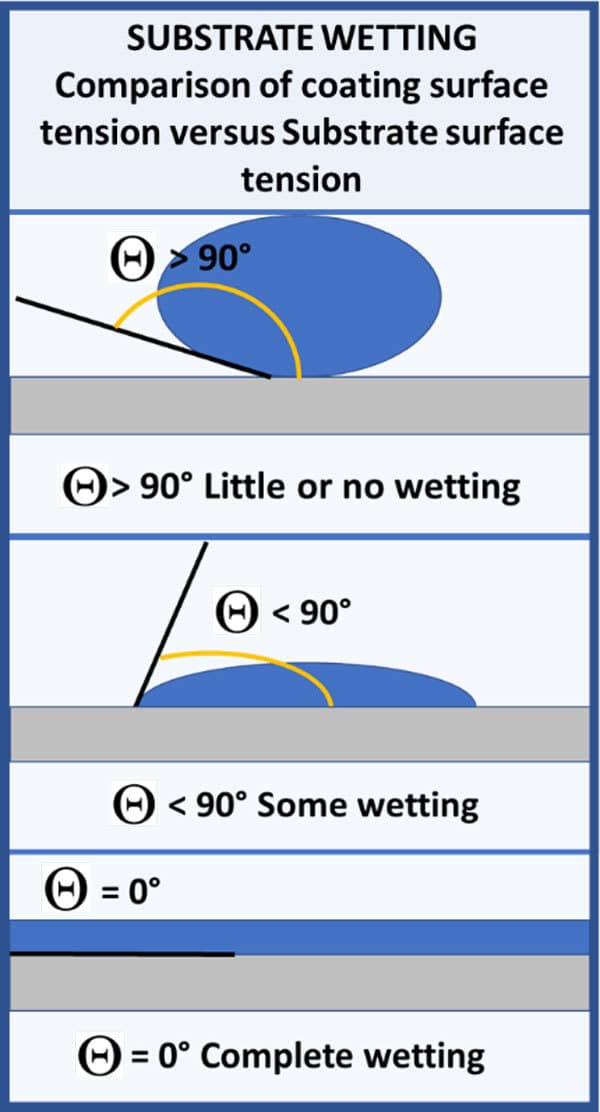
FIGURE 1 ǀ Basic properties of surface tension modifiers – substrate wetting.
If the surface tension of the liquid is higher than the surface tension of the substrate, then the cohesive forces are stronger than the attractive forces between the liquid and substrate, and you do not wet out the substrate. If the surface tension of the liquid is lower than the surface tension of the substrate, then the attractive forces are stronger than the cohesive forces and you will wet out the substrate.
It is normally more difficult to change the surface tension of the substrate than change the surface tension of the liquid. Examples of modifying the surface tension of the substrate include corona treating plastics and mechanically profiling the surface of the substrate, such as shotblasting steel or concrete. It should be noted that mechanically profiling is more directed to removing low-surface-tension contaminants than actually changing the substrate’s surface tension. Therefore, it is more often preferred to lower the surface tension of the coating to aid in wetting out the surface, using additives called surface tension modifiers.
We may also want to modify the surface tension of the coating for other reasons than wetting out the substrate. Examples are: aiding in the application and flow of the coating, modifying the dried coatings’ final surface tension or surface slip, or making the surface tension low enough so contaminants such as dust are incorporated into the coating rather than resting on the surface as defects.
Coatings can contain resins and other raw materials that have a higher surface tension than what is ideal. This can lead to poor atomization during spraying, poor flow during application, poor wetting out of the substrate or poor leveling after application. All these issues can lead to inadequate final coating performance.
There are many additives than can fall into the surface tension modifier category, but for this article we will be concentrating on:
Substrate wetting agents,
Flow and atomization agents,
Leveling agents, and
Slip and mar agents.
Wetting, flow, leveling and slip phenomena all require some amount of time to accomplish. This is complicated by a constantly changing system caused by pseudoplastic behavior of the rheology modifiers, solvent evaporation (water is a solvent) and film formation.
Spreading is the near-spontaneous distribution of the liquid coating on the solid substrate to maximize contact at the solid/liquid interface to minimize the system energy. Spreading or the flow of the coating over the substrate is desirable to get a uniform dried film on the surface of the substrate. As the contact angle goes below 90°, spreading will start occurring, but you need to approach a contact angle of 0° before complete spreading occurs. Spreading is highlighted in Figure 2.
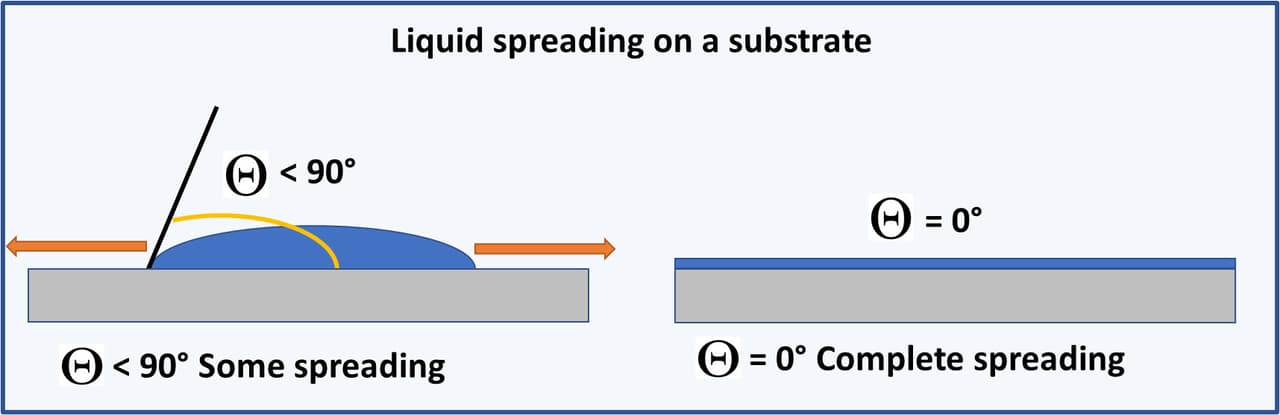
FIGURE 2 ǀ Basic properties of surface tension modifiers – spreading.
Leveling is when the irregular coating thickness, caused by application, flows to give a uniform coating thickness. Leveling is based on the surface tension of the liquid and is independent of the surface tension as the substrate since the substrate is already wetted out. Leveling is different than wetting or spreading because the cohesive forces want to minimize the surface area of the coating, and a flat surface has less surface area than an irregular surface, giving the system lower energy. Leveling is illustrated in Figure 3.
Spreading and leveling are further complicated because a coating’s viscosity often plays a more significant role than its surface tension. The viscosity, or resistance to flow, is a further force to complicate the wetting, spreading and leveling process. To wet and spread over a substrate, the adhesive forces must be greater than both the combined cohesive forces and the resistance to flow. If cohesive forces are greater than viscosity, the coating will level.
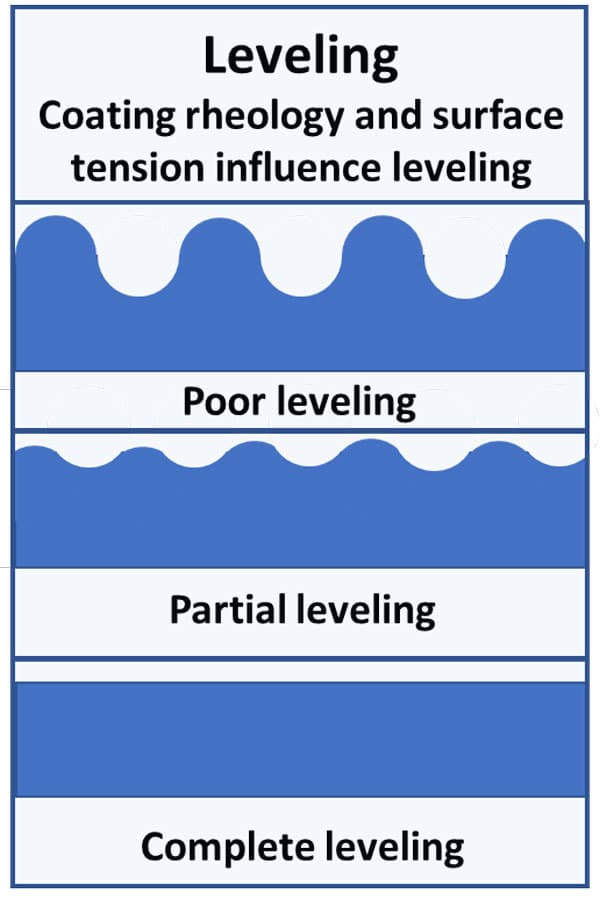
FIGURE 3 ǀ Basic properties of surface tension modifiers – leveling.
Wetting, spreading and leveling are time-dependent processes. The added complexity here is that viscosity is also a time-related process, unless you are using a Newtonian liquid, which is extremely rare. Over time, the coating coalesces, or cures, and the water and solvent evaporate. Balancing these time-dependent processes increases formulation complexity by an order of magnitude. The ideal situation is a system where you have low viscosity during application and immediately after application. Then viscosity increases, preventing sags and drips. You need very quick wetting, spreading and leveling so they can occur while the coating is in the low-viscosity phase of pseudoplastic behavior. The good news is modern surface tension modifiers can do this.
For a coating to wet out a substrate, the surface tension of the liquid must be below the surface tension of the substrate since liquids flow from low to high surface tension. If the surface tension of the liquid is around that of the substrate, you will get partial wetting, leading to poor flow, leveling and adhesion. Since both the substrate and the coating are made up of mixtures of different components, the substrate’s and the liquid’s surface tension vary slightly on a molecular level, and you will get areas where the surface tension of the substrate is slightly below or above that of the liquid. To avoid this phenomenon, try to have the coating’s surface tension well below that of the substrate.
Surface Tension Modifiers
Substrate wetting agents work by reducing the surface tension of the coating to below that of the substrate. They operate at the coating substrate interface. In order to get complete wetting of the substrate, the coating must have a lower surface tension than the substrate. This can be problematic on low-surface-tension plastic substrates for most coatings, but is further complicated when using water-based systems due to the very high surface tension of water. The surface tension of water is ~72 dynes/cm at 25 °C compared to most solvents with values between 20 and 30 dynes/cm at 25 °C. Substrate surface tensions, which range from ~400-1,100 dynes/cm for metals to ~18-45 dynes/cm for polymers/coatings, highlight the variation inherent in substrates. This illustrates what we have seen in coatings where solvent-based systems wetted out most substrates without issues while water-based systems have trouble doing the same. This has led to a huge assortment of wetting agents for water-based systems. Often when using water-based systems without wetting agents, the dried coating has a lower surface energy than the identical wet one, leading to crawling of the second or subsequent coats.
Flow agents are similar to substrate wetting agents but are designed to reduce flow at the higher shear rates observed during application of the coating. Since this is taking place during application, they work on the air/coating interface.
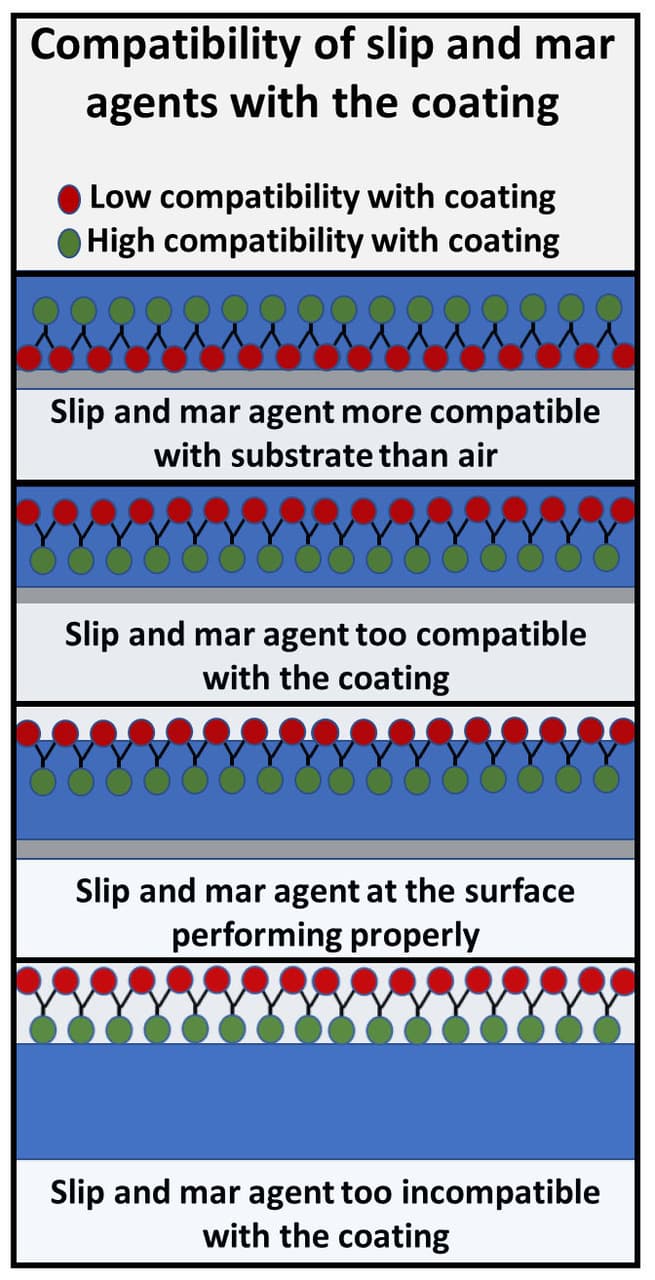
FIGURE 4 ǀ Basic properties of surface tension modifiers – slip and mar agents.
Leveling agents are also like wetting and flow agents, and operate at the air/coating interface. They are designed for low shear conditions where they help the coating level out, giving a smooth surface and even out surface defects. In leveling, the time it takes to level out is directly proportional to viscosity, and inversely proportional to surface tension and film thickness. If you want to increase the leveling of a coating, increasing the dry time through slower-evaporating solvents or applying a thicker coat helps.
The last group is slip and mar agents. These additives are designed to move to the air/coating interface and concentrate there. Their function is to lower the surface tension of the cured coating.
Figure 4 highlights some of the processes influenced by the difference in compatibility of the coating and additive. The function of slip and mar agents is to increase the slip and lubricity, and lower the surface tension of the dry film. This increases the abrasion resistance, mar resistance, blocking resistance, dirt pickup resistance and cleanability of the coating. They are often based on polysiloxane or wax chemistry. In all cases they migrate to the air/substrate interface, and in many cases protrude out of the coating into the air.
Measuring surface tension is further complicated by the need for static and dynamic testing. Static testing is good for longer-term processes like leveling, and is measured at low shear. Static testing is best suited to systems in which equilibrium is reached faster than the time needed for the test. Dynamic testing is measured at high shear and is best suited to systems in which the measurement is faster than the time needed for equilibrium. This is a better method for fast processes like flow and substrate wetting during a fast application process.
Surface tension modifiers also help reduce or eliminate surface defects such as orange peel, crawling, roller/brush marks, fish eyes, craters, etc. Fish eyes and craters happen when a contaminant (dust, defoamer, etc.) that is incompatible with the coating, and of lower surface tension, is in the coating. Since it is incompatible, it will rise to one of the coating’s interfaces. Liquids flow from low to high surface tension, therefore, these contaminants cause coatings to move away from the contaminant, creating a defect. The main difference between fisheyes and craters is that fisheyes have a solid particle in the middle (resembling a fish eye), while craters are liquid. Lowering the surface tension at the air/liquid interface will allow the coating to flow over the defect, yielding a more uniform film.
While surface tension modifiers are specifically designed for one function, they also affect other functions. A leveling agent may also act as a substrate wetting agent. While solvents also will modify surface tension, they are often added for other reasons and are not considered true additives. The main categories of these additives are pure and modified polydimethylsiloxanes (siloxanes), polyacrylates (acrylates) and perfluoroalkyl (fluoro) chemistries.
Siloxanes are either pure or modified by polyether, alkyl, polyester or others groups, and have strong surface tension reduction. Figure 5 shows the structure of siloxanes. The pure compound has methyl groups at R1 and R2, while modified siloxanes have some other groups at R1 and/or R2. The molecular weight can also be modified by changing the number of repeating groups (n and m in Figure 5). The nature of the groups at R1 and/or R2 and the molecular weight of the molecule will determine how the additive works. Low molecular weights are used for leveling agents, mid molecular weights work better for slip, and higher molecular weights are used for defoamers due to their incompatibility with the coating system. Polyether modification increases compatibility, but also increases the tendency to stabilize foam. Ethylene oxide-based polyethers will be much more hydrophilic than propylene oxide-based ones. Alkyl, phenyl or polyester modified siloxanes have increased thermal stability (240 °C versus 180 °C), decreased compatibility and decreased foam stabilization when compared to polyether-modified siloxanes. Fluoroalkyl-modified siloxanes reduce surface tension to a significantly greater extent than all others, but also stabilize foam more. Polyester-modified siloxanes tend to have worse hydrolytic stability than polyether-modified siloxanes.
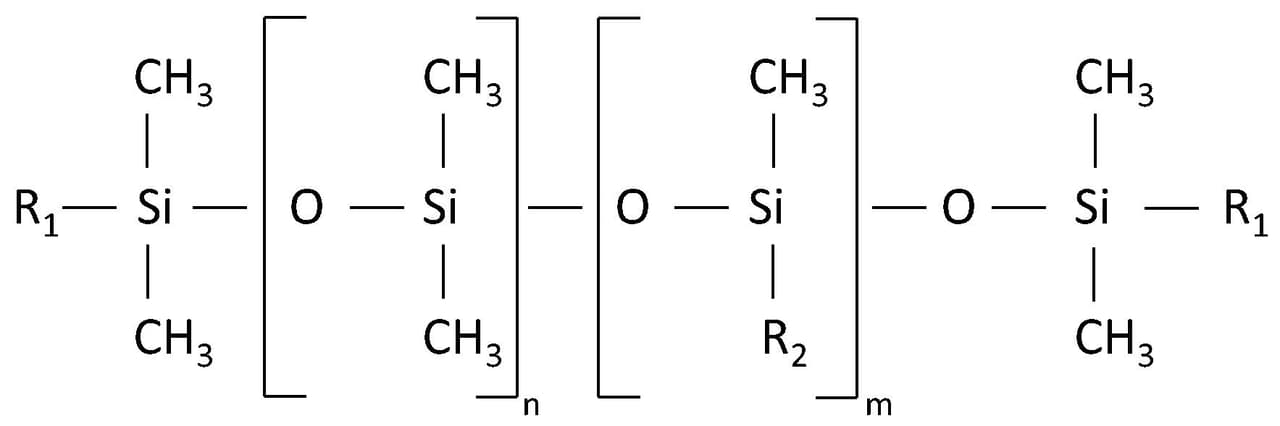
FIGURE 5 ǀ Polydimethylsiloxane structure.
Polyacrylates afford moderate surface tension reduction, but do not have recoatability issues like siloxanes or fluoro surfactants can have. Fluorinated acrylates afford significantly greater surface tension reduction but also stabilize foam more. Acrylates are generally used instead of siloxanes when silicone content is limited in the application, such as automotive coatings.
Perfluoroalkyl surfactants allow for the greatest surface tension reduction. They are, however, fairly expensive and readily stabilize foam.
Other chemistries include waxes (amide, polyethylene and paraffin) for slip and mar resistance. They can influence recoatability, and over time will change the gloss of the coating. Initially they lower gloss, but as they flow out due to wear and deformation, gloss can change.
Very slow-evaporating solvents and plasticizers can be used to help improve leveling in water-based paints. Hydrophilic solvents lower the surface tension of the bulk liquid, making flow easier and can slow down water evaporation, increasing open time. Hydrophobic solvents aid in coalescence and result in a more uniform surface. The negative impact of solvents when compared to plasticizers is increased VOC due to solvent evaporation, while non-evaporating plasticizers will soften the film, leading to block and dirt pickup issues. They really do not affect other coating properties like surface tension modifiers so they can be a viable option.
Figures 6 and 7 highlight some of the differences between the main chemistries (polysiloxane, polyacrylates and perfluorosurfactants).
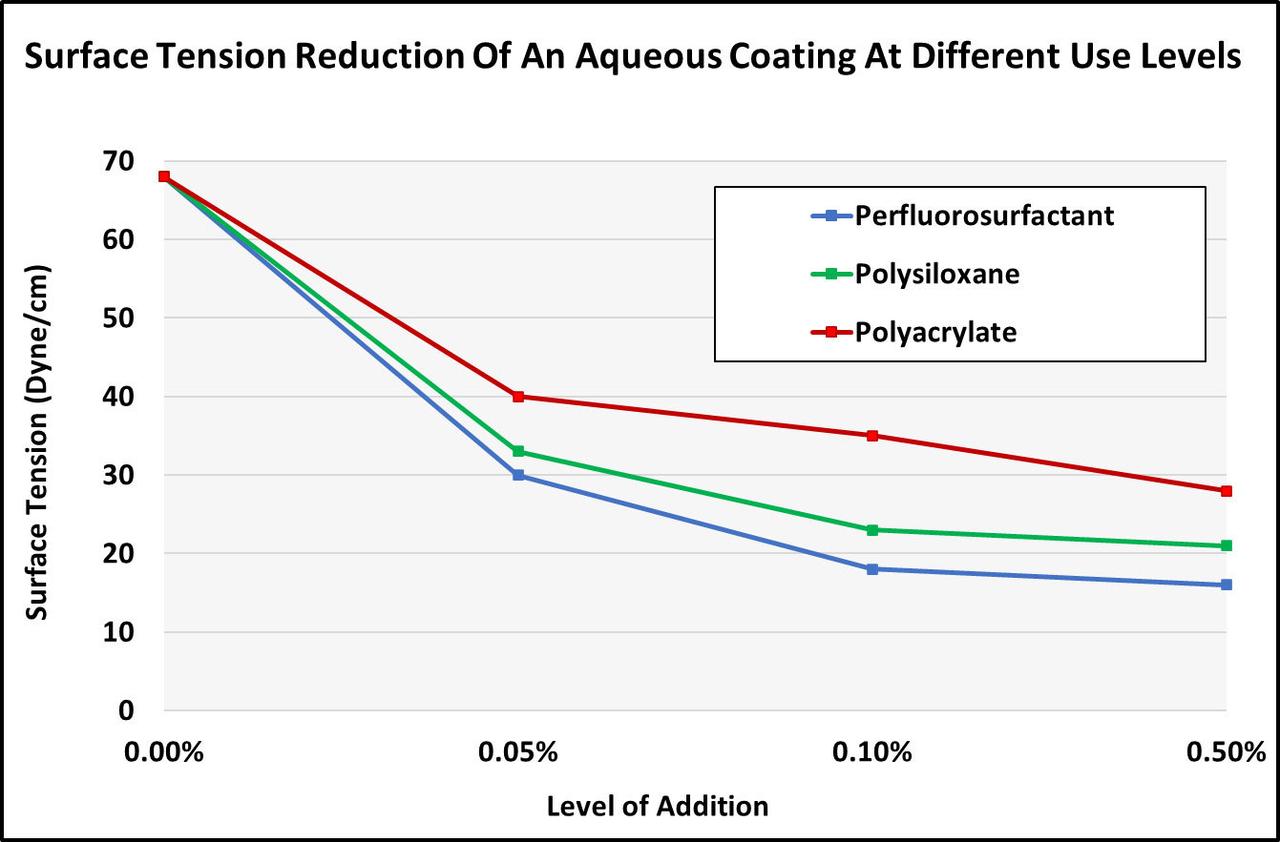
FIGURE 6 ǀ Surface tension reduction of an aqueous system.
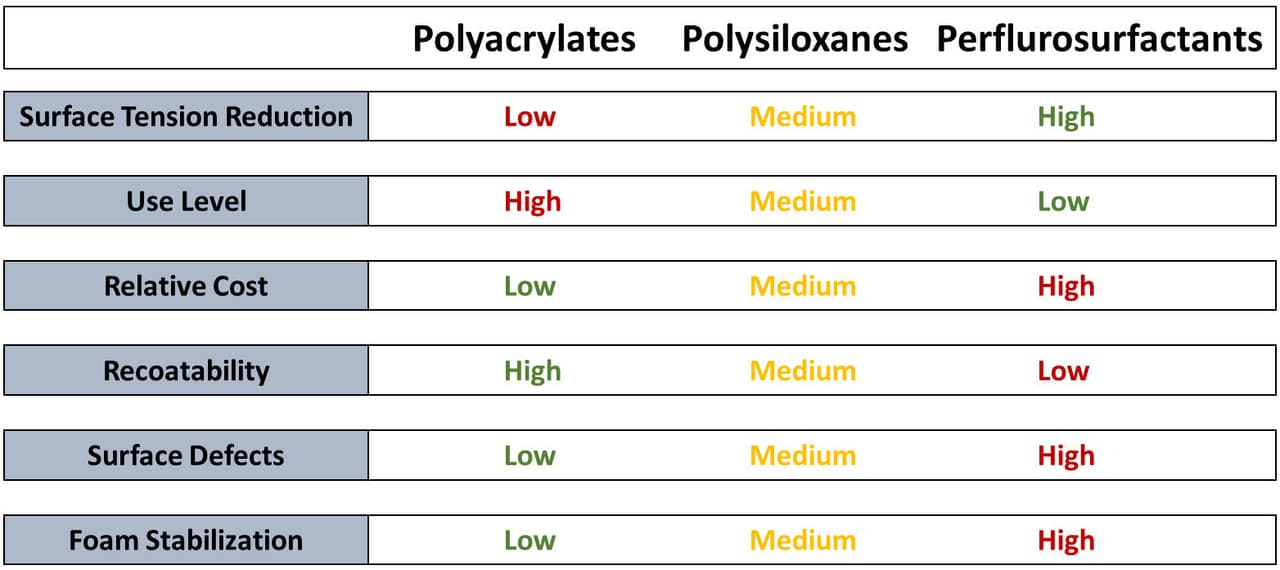
FIGURE 7 ǀ Comparison of polysiloxanes, polyacrylates and perfluorosurfactants.
Surface Agent Issues
The biggest problem with surface modifying agents is constructive interference. Surface agents must be mobile to work by migrating to either the coating/substrate interface or the coating/air interface. The issue we run into is that we often want to recoat previously painted substrates without having to remove the old paint, or we have a multicoat application process. If we use a flow and leveling agent with too low a surface tension, the new coating will have a higher surface tension and not spread or adhere, and we can formulate around that. But what if we are putting on a third, fourth or fifth layer of coating? This is not that uncommon on substrates that require a bonding primer, sanding primer basecoat and topcoat often used on plastics in automotive coatings or multiple coats of paint applied over years in architectural coatings. We may not know what the formulation of the previous layers are, so it is much harder or even impossible to formulate around it.
Since the surface tension modification agents want to move to the air/surface interface, they can migrate out of one coating layer and into the new coating layer. This effect is multiplied with every coating layer until we have such a high concentration of additives at the surface and the surface tension is so low that recoat is impossible. Mar and slip agents and defoamers further complicate this process, as you have significantly higher concentrations of mobile, low-surface-tension molecules at the air/coating interface. This can often lead to too low a surface tension in floor coatings and pose a slip or fall hazard, especially when wet.
A similar phenomenon can happen for substrate wetting agents where the agents in each layer of paint work their way to the substrate upon which a layer of additive forms and adhesion is compromised, or in extreme cases, there is no adhesion. The small size of the molecules allows them to move through some cured coatings over time, leading to adhesion failure sometime in the future.
The worst case situation is when the additives are partially mobile and substrate wetting agents move to the coating/coating interface concentrating there, while the leveling and slip/mar agents remain there, preventing polymer resin/polymer resin intercoat adhesion of the two layers of paint.
Conclusion
While the surface phenomena of coatings cause coating issues, understanding surface tension modifiers and their limitations will allow coatings formulators to create more robust coatings systems.
In the next article, I will discuss pigment dispersants and the pigment dispersion process.
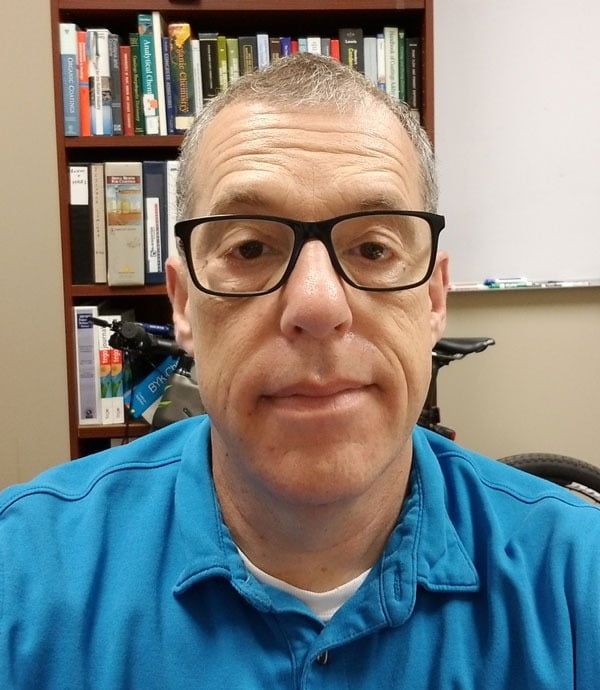
Mike Praw
Author’s Bio:
Born and raised in Montreal, Mike now lives in the Houston area. He has 34 years of coatings formulation experience, 18 years with coatings companies and 16 years with raw material suppliers. He is currently Senior Applications Scientist – Paints, Coatings and Inks, for Indorama Ventures: Integrated Oxides and Derivatives. He has degrees in Analytical Chemistry and Environmental Sciences, as well as a MBA. Mike is the Past President for The Detroit Society for Coatings Technology and The Piedmont Society for Coatings Technology, and served on the board of the Chicago Society for Coatings Technology. Mike is a Canadian Armed Forces veteran, having served 15 years in the Canadian Infantry.
All information contained herein is provided "as is" without any warranties, express or implied, and under no circumstances shall the author or Indorama be liable for any damages of any nature whatsoever resulting from the use or reliance upon such information. Nothing contained in this publication should be construed as a license under any intellectual property right of any entity, or as a suggestion, recommendation, or authorization to take any action that would infringe any patent. The term "Indorama" is used herein for convenience only, and refers to Indorama Ventures Oxides LLC, its direct and indirect affiliates, and their employees, officers and directors.