Ready to proof -- CLJ 08/04/21
Ready for author
Making Solvents Green
Reducing the Environmental Impact of Solvents in Your Operation
Photo: KTStock, iStock/Getty Images Plus, via Getty Images
By Josh Huffman, Director, Sustainable Solutions, CleanPlanet Chemical; and Jim Kuzara, Sales Manager, Ship & Shore Environmental
With changing consumer and investor demands, new regulations and the realities of environmental impact, one thing is clear: businesses need to find ways to increase sustainability or risk falling behind. The coatings industry knows this well, and has taken major steps to incorporate energy-saving technology. But what happens when the low-hanging fruit has been picked? It’s time to open a drum and take a look at your solvent.
Is Your Solvent Green?
Solvent-based paints make up a meaningful portion of the paint and coatings market globally. Manufacturing these solvent-based coatings requires additional use of wash solvents to clean equipment, resulting in a further consumption of solvents. This solvent use has a major impact on manufacturing sustainability. Whether from the metric of hazardous waste generation, VOC emissions or increased carbon footprint, your solvent waste negatively impacts the sustainability of your operation. But there is good news! There are new technologies and business approaches that have come to market in the last several years that effectively neutralize this impact. Solvent doesn’t have to be a dirty word when it comes to the environment. In fact, with proper management, solvent can actually be more environmentally friendly than water-based solutions.
The True Environmental Cost of Your Solvent
If your facility utilizes solvents, you are already familiar with the effects of waste generation from spent solvent, but there is an additional environmental cost you have probably not considered — the energy cost of the solvent life cycle. Every step in the solvent life cycle from raw material acquisition to disposal requires energy and contributes to the overall carbon footprint. The majority of solvents used in the coatings industry are hydrocarbon based, so to really understand the true environmental cost of your solvent we need to examine oil production.
In a simplified example of the solvent life cycle, the process begins with the extraction of oil. After constructing an oil well, iron horses are used to pump oil into containers, which are stockpiled at storage facilities until they are later transported to a refinery. The refinery takes the oil and produces a number of petrochemicals, including your solvent. Next, the refined petrochemicals are transported to distributors. Distributors then stock the barrels and fill orders, which are then shipped to end users. End users, such as the coatings industry, consume the petrochemicals in various processes and products. The solvents that remain after the production process, which are typically hazardous waste streams, are transported to authorized disposal sites where they are incinerated. Each step in this life cycle requires additional energy to progress it to the next step, be it transportation, pumping or refining (a step that requires large amounts of energy).
When solvent is ultimately incinerated, its carbon footprint isn’t just the greenhouse gases released in the process, but all the upstream greenhouse gases released while progressing the chain from start to finish. In fact, according to a study by Carleton University, a typical pound of solvent will have produced 9.8 pounds of greenhouse gas once incinerated from all the cumulative upstream effects. This is the hidden cost of your solvent. The good news is that this process is reversible.
Solving the Solvent Problem
The real problem with the solvent life cycle is that it ends. All that resource, effort and energy is ultimately gone forever when the solvent is incinerated. This may be a bigger problem than you ever thought. According to the EPA, over 90% of solvents are disposed of in this manner, creating a significant carbon footprint.
In an industry that uses millions of gallons of solvent a year, this is a real problem, but also an opportunity for facilities to improve sustainability. The question is how best to answer the problem.
Option 1: On-Site Energy Recovery
It may not always be cost effective or practical to recover certain waste solvent. At this point, solvent end of life via thermal oxidation is a consideration. Although obviously not ideal for recovery and re-use models (the process converts solvent emissions to primarily carbon dioxide and water), it does mitigate the more harmful release of hazardous smog-forming fugitive VOC emissions, which may vent to the atmosphere when other options prove not optimal (capital or operational costs). Extremely efficient regenerative thermal oxidizer (RTO) technology uses solvent emissions as fuel to use little or no natural gas in the combustion process. To further take advantage of the combustion process, excess heat from the RTO exhaust can be used to heat process air, water or oil to reduce any other process operational energy needs.
Option 2: Giving your Solvent a Second Life
This is the ‘Reuse’ part of ‘Reduce, Reuse, Recycle and can dramatically impact the environmental impact of your solvents. In a study titled “Wash Solvent Reuse in Paint Production” conducted by the Pollution Prevention Research Branch of the EPA, it was found that wash solvents, those previously used to clean paint manufacturing equipment, could be used in the manufacturing of certain solvent-based paints. Not only does this reduce the production of new solvent, it also extends the life cycle of the existing solvent. In this EPA study, the waste stream generated by spent wash solvent was reduced by 80%. More importantly, the paint that was manufactured with wash solvents was found to be comparable in quality to that which contained only virgin solvent. This option not only offers manufacturers an environmental savings, but also an economic one.
A more common option to provide your solvents a second life is fuel blending. This method blends your solvent waste as a fuel source for kilns used in the cement manufacturing process. While this ultimately results in the burning of solvent and the subsequent release of greenhouse gases, it extends the solvent life cycle and provides an energy source for a process that would otherwise use coal or natural gas.
While giving your solvent a “second life” extends the life cycle, it doesn’t prevent the end. Ultimately, the solvent is disposed of and the greenhouse gases are released. To truly be sustainable, you need to extend the solvent life cycle as far as possible.
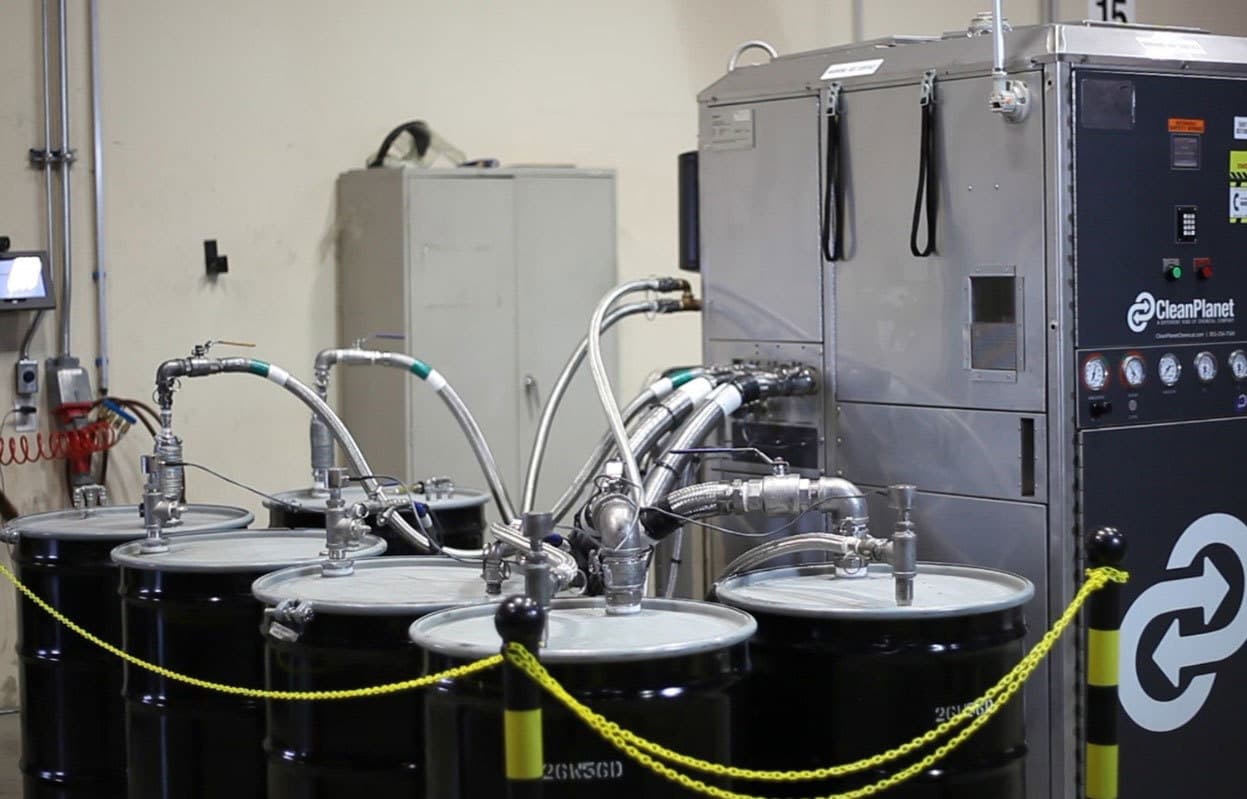
Closed loop recycling extends the life of your solvent and minimizes emissions. Photo courtesy of Ship & Shore Environmental.
Option 3: Extending the Cycle
If your operation uses wash solvents, the only way to truly maximize sustainability is by recycling your waste. This reduces both the amount of waste a facility generates as well as its overall greenhouse gas emissions.
The two common methods for solvent recycling are 1) recycling solvent off-site and 2) recycling solvent on-site. Off-site recycling allows a facility to divert their waste from incineration or disposal to recycling with very little disruption. Off-site recyclers will collect the waste from multiple facilities, aggregate it, recycle it, then ship back the recycled product. This is an effective and low-burden means to reduce both waste and greenhouse gas emissions for facilities that don’t have the capital, space or expertise to recycle on-site. While this is an obvious step in the right direction, issues with quality mean that additional solvent purchases are often required, resulting in more emissions and waste. Additionally, this method doesn’t eliminate hazardous waste shipments and the associated liability, and typically costs significantly more in the long-run versus recycling on-site.
The other recycling option, recycling on-site, allows facilities to process their solvent waste stream internally. The two main benefits of this approach are 1) the solvent can be reclaimed over and over again for reuse, saving the coatings manufacturer a considerable amount of money on solvent purchases, and 2) a greatly reduced volume of waste for disposal. There are many solutions for recycling your waste on-site. These include small-scale bag-style recyclers, larger batch recyclers and continuous-feed automatic recyclers. Depending on the technology, facilities that recycle on-site see waste reductions anywhere from 80% to 95%. This is an effective means for facilities to achieve small quantity generator (SQG) status. Additionally, by diverting such a large amount of waste away from incineration, these facilities are able to dramatically reduce their greenhouse gas emissions. In the Carleton University study, it was found that on-site solvent recyclers can reduce the greenhouse gas emissions from the entire solvent life cycle by 48%. Traditional on-site recycling technology clearly represents a step in the right direction, but it has some limitations and is still a VOC emitter. This is problematic from an environmental and safety point of view, but also means that key constituents from the solvent blend are lost. This ultimately means purchasing more solvent, a reduction in cleaning productivity, and once again increased emissions and waste.
Option 4: Handling “Lost” Fugitive Solvent Emissions
Reduce, Reuse and Recycle is the golden rule to maximize sustainable operation. Accountability of fugitive emissions (especially in large-scale production operations) must be addressed in a solvent material life cycle. In poor air quality regions around the country typically referred to as non-attainment areas, greater focus is placed on the control or recovery of these emissions to mitigate release.
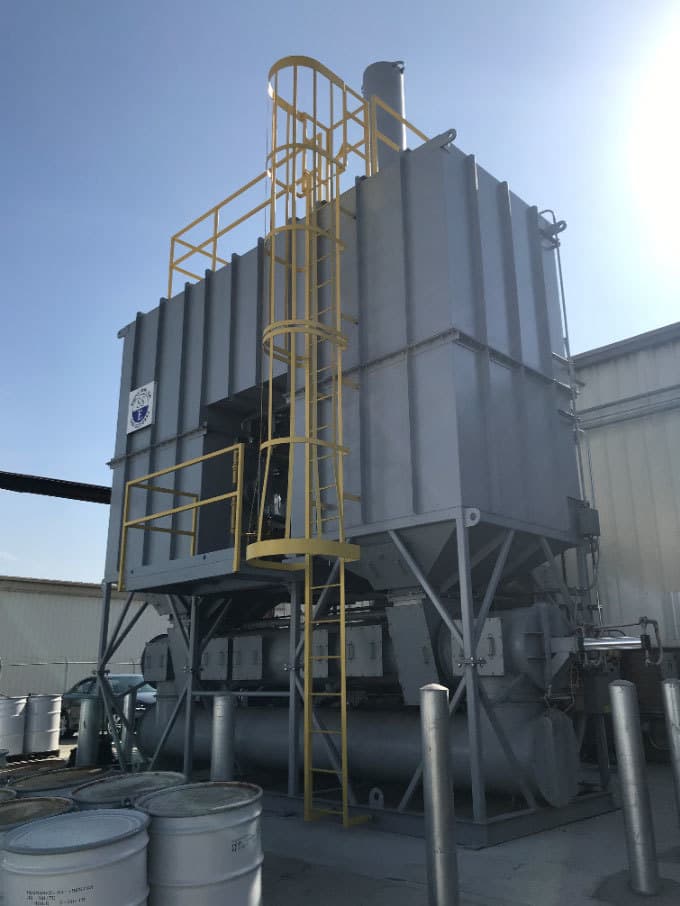
Fugitive solvent emissions are not easily controlled, and processes must be put in place to minimize the environmental impact. Fugitive emissions are often released into the plant environment or atmosphere via transitional production activities. Good examples of this are tank vent sequences during emptying and filling of storage tanks, the transition of coated goods from spray booth, and dip spin coating operations (freshly coated parts are transitioned via conveyor to open air flash-off/cure or bake oven cure zones.) Segregation and collection of these emissions are difficult and normally result in very large, low-solvent-content air streams. These conditions are not optimal for cost-effective recovery.
Partners in abatement equipment technology, such as Ship & Shore Environmental, offer helpful insights with sustainability in these situations. Various approaches can be taken to improve handling of fugitive emissions. Concentrator technology (typically carbon or zeolite materials) can be used to adsorb solvent materials, converting high-volume, low-solvent conditions to low-volume, high-solvent concentrated conditions, which greatly improves recovery.
An RTO is used to capture and abate VOC and fugitive emissions from solvents. Photo courtesy of Ship & Shore Environmental.
Ending the Cycle with Innovation
Advancements in solvent recycling technology over the last five years, such as the equipment from CleanPlanet Chemical, have, for the first time, resulted in the creation of an effective closed-loop recycling system. This technology answers many of the failures of traditional on-site solvent recycling. Improved sensor and automation technology has drastically improved the uptime of solvent recyclers (the amount of time a recycler is processing solvent per day), meaning that greater amounts of waste can be processed each day. Built-in quality control systems are able to ensure a higher-quality product, leading to a reduction in make-up solvent purchases. The closed-loop nature of these modern recyclers result in de minimis VOC emissions. Virtually no emissions means that the solvent produced by this technology is practically identical in composition to the virgin solvent. The result is a breakthrough in recycling, an indefinite solvent life cycle.
However, for innovative green technologies such as this to actually make a difference, they need to be easily adopted by industry and used consistently. Recent innovations in the solvent recycling business model are lowering short-term and long-term barriers to success by providing “recycling as a service”. Under the service model, facilities don’t have to make a capital purchase or provide maintenance and repair for a solvent recycler. Additional tasks like training, monitoring, reporting and optimization are all taken care of at no charge as a part of the complete solution. From an economic perspective, facilities pay for only the recycled solvent, at a rate much cheaper than alternatives, further incentivizing the adoption of this sustainable technology. Due to this rethinking of the recycling business model, this technology is already seeing successful adoption at many facilities in the coatings industry.
Conclusion
The demand for solvent-based paints means that the environmental burden of the solvent life cycle will always weigh on coatings manufacturers. Hundreds of millions of gallons of solvent are used each year, with the vast majority ultimately converted into greenhouse gases. This is a problem, but one with clear solutions. By implementing reuse strategies, traditional recycling, or most effectively, modern solvent recycling, coatings manufacturers can drastically improve the sustainability of their operations. Solvent is and will continue to be an important part of the coatings industry, but it doesn’t have to carry the negative stigma that it does today. The coatings industry can use solvent AND do the right thing by the environment. Good news indeed!