Ready to proof -- Clare 8-16-22
KJ proofed on 8/16 and made comments for CB. Clare, there is one correction for you in Table 3. Also, is there any way to slow down the lead video? No big deal if not.
Courtney, once you have made my corrections and your own, let me know and I'll turn off the notes if you don't have permission yet so that you can send this to Evonik.
CLJ revised figure 3 on 8/17. I can’t change the speed of the video.
Credit: flavioc77 / Creatas Video, via Getty Images
New Tools for Improving the Durability and Maintaining the Appearance of
Architectural Coatings
By Ingrid K. Meier and Tony Hazim, Evonik Corporation
Introduction
The Quest for Cost-Effective Durable Interior Architectural Paints
Many of us may not have appreciated the value of durable interior house paints until forced to spend significant time at home due to the COVID-19 pandemic; however, architectural paint manufacturers have long sought interior architectural coatings with improved durability because they know that consumers want their painted walls to look like new for as long as possible. Minimizing the burnishing that occurs in spots that see repeated rubbing and making the paint more resilient to frequent cleaning are ways that paint manufacturers can reduce the cost-of-ownership of a paint. A recent study highlighted that ultra-low-VOC waterborne paints that are durable enough to not need repainting for seven to 15 years have excellent life-cycle analyses because they reduce raw material consumption, paint production, and waste paint1. The additional scarcity and high cost of hiring contract painters in North America makes the value proposition of a high-quality, durable paint quite clear.
Historically, consumers who wanted more durable interior paints would need to avoid flat paints entirely and, instead, use higher-sheen wall paints — sacrificing the ability to hide imperfections in the underlying walls. However, paint manufacturers have now begun to develop premium, 100%-acrylic flat paints with improved physical properties, but the cost of 100%-acrylic resins is significantly higher than that of vinyl-acrylic or vinyl acetate-ethylene (VAE) copolymers. A technology that could enable a lower-cost resin-based paint to match the performance of a premium 100%-acrylic paint would be a valuable tool in a formulator’s toolbox.
In many regions, the mineral nepheline syenite is now used to improve the wet scrub resistance of interior wall paints. Nepheline syenite is a silica-deficient, sodium-potassium aluminosilicate with a Mohs hardness of 6. When ground and classified, grades that are suitable for flat and higher-sheen paints are available. These nepheline syenite particles are angular in morphology, and a single grade of material has a broad particle size distribution (Figure 1).
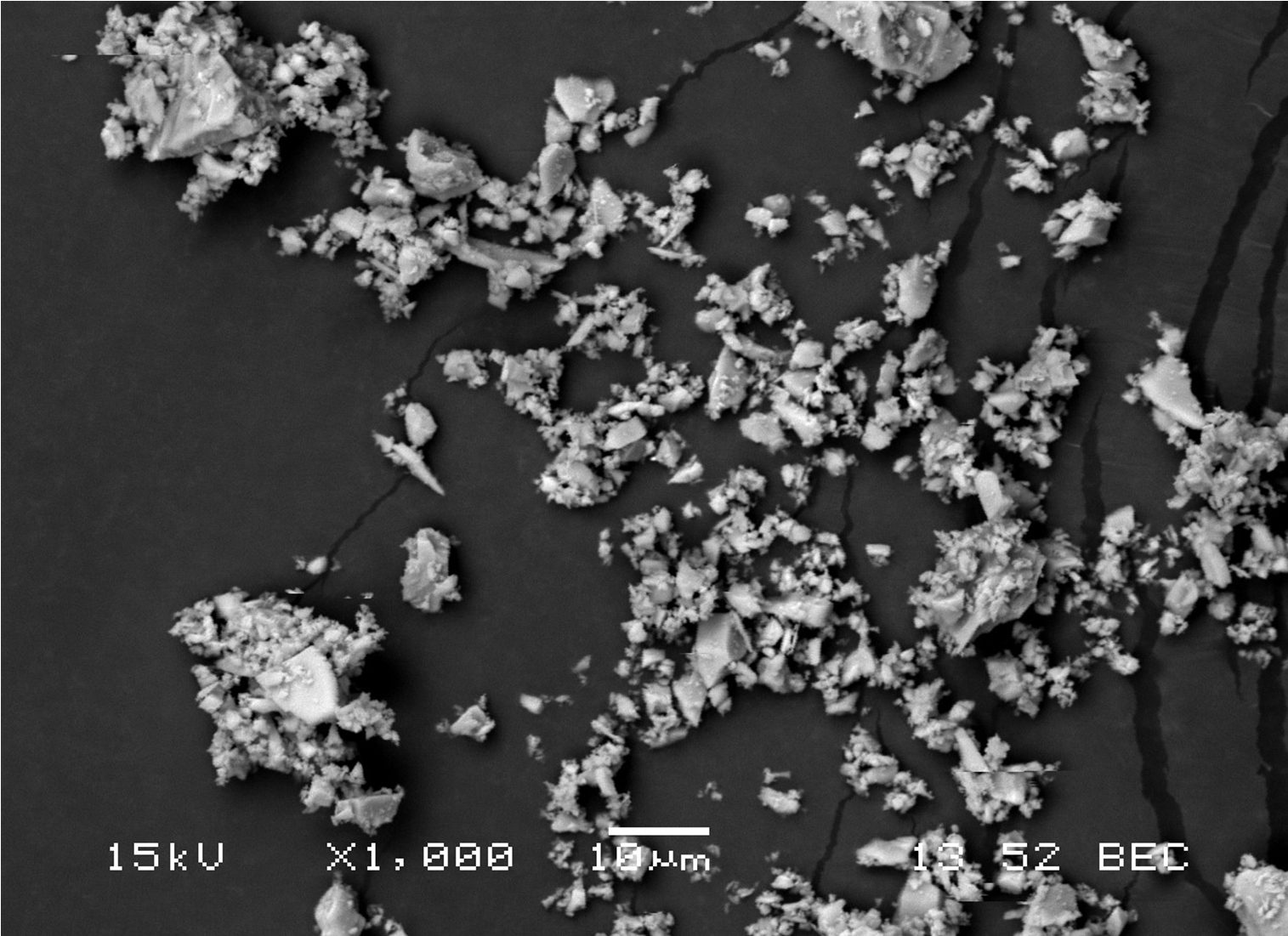
FIGURE 1 ǀ Scanning electron micrograph of nepheline syenite of 2.5 μm median particle size.
Recently, 3M introduced white ceramic microspheres that are spherical sodium aluminosilicates with Mohs hardness values of approximately 6.2 These particles have been reported to provide improvements in wet scrub and burnish resistance in flat architectural paints, and the three commercial grades are stated to have 90th percent particle sizes (by volume) of ≤ 12, ≤ 21 and ≤ 32 microns, respectively.
However, even with these improvements, there is still a need for additional tools to enable interior paints based on all types of resins to achieve similar levels of burnish and scrub resistance.
A Novel Precipitated Silica Process
When Hagar and Gallis first developed their continuous process for producing spherical precipitated silica and alkali aluminosilicates, the utility of these unique particles as abrasive cleaning agents in dentifrice compositions was quickly recognized3 - 6. Interestingly, this novel process, in which an acidulating agent and alkali metal silicate are continuously fed into a loop reaction zone comprising a stream of liquid reaction medium, can be run using a broad range of reaction conditions to generate spherical silica particles with significantly lower than expected Einlehner abrasion values and higher refractive index values. They are also compatible with cationic ingredients, such as cetylpyridinium chloride — desired properties for dentifrices but previously unattainable using conventional precipitated silica products.
The greater versatility of this novel precipitated silica process was then discovered when the ability to produce spherical precipitated silica particles with very low surface area, low oil absorption, and an extremely narrow particle size distribution was realized7. These properties enabled the production of precipitated silica particles particularly useful in coatings formulations because these spheroidal precipitated silicas did not cause significant viscosity increases, unlike the majority of commercial precipitated silicas and aluminosilicates that have much higher oil absorption values. As seen in the scanning electron micrograph in Figure 2, the morphology of this novel precipitated silica is distinctly different from that of ground minerals like nepheline syenite. Advantageously, these novel silica particles were found to be useful in increasing the burnish resistance and, to a lesser extent, scrub resistance of interior architectural coatings, and in providing matting and physical property improvements in powder coating formulations8-9.
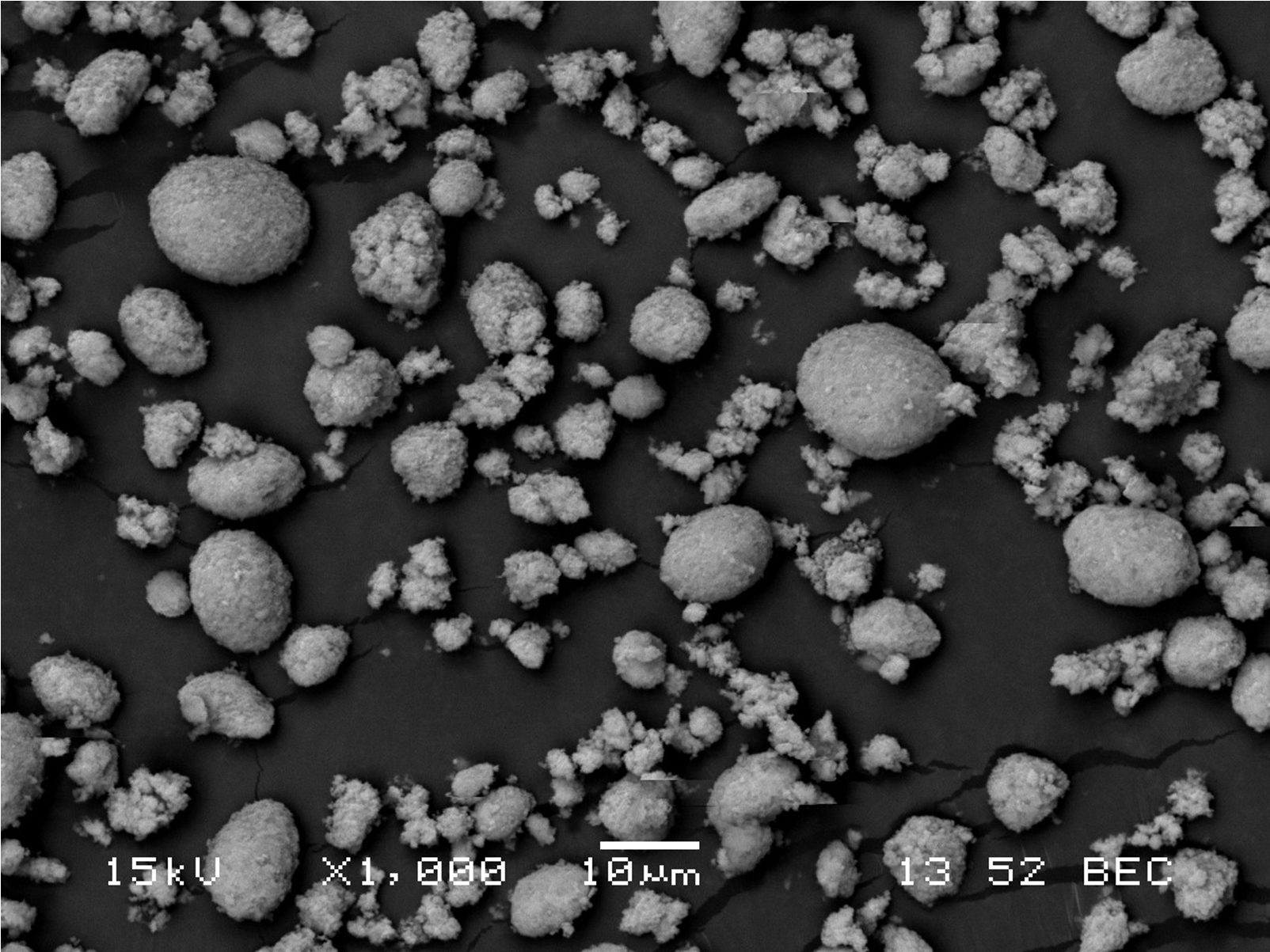
FIGURE 2 ǀ Scanning electron micrograph of spherical precipitated silica of 5.5 μm median particle size.
The initial investigations in architectural coatings focused on spherical silica with average particle sizes between 5 and 15 microns, replacing the softer calcium carbonate with the harder spheroidal silica. The work presented here explores both larger and smaller particle size spherical silicas, and replacing the harder nepheline syenite in both flat/matte and eggshell formulations to determine if similar or additional benefits would be observed.
Results and Discussion
Experimental
Materials
Drikalite™ calcium carbonate from Imerys has a median particle size of 7 microns, Mohs hardness of 3, pH 8 - 9 and a specific gravity of 2.7 g/cc. Minex® 4 and Minex 10 are nepheline syenite grades from Covia that have median particle sizes of 7.6 and 2.5 microns, respectively. Nepheline syenite has a Mohs hardness of 6 and a specific gravity of 2.6 g/cc. 3M® ceramic microspheres (CMS) W-210, W-410 and W-610 were obtained from 3M; they have a specific gravity of 2.4 g/cc and a pH of 9.9 - 12.0 (ASTM E70).
Precipitated spherical silica particles (SPH) were prepared according to the methods described in the patent literature3-6. Precipitated silica has a Mohs hardness of 6, a specific gravity of 2.0 g/cc, and a pH of 6.5-8.5 at 5% in water; all grades studied here have nitrogen surface areas (B.E.T.) of less than 12 m2/g and oil absorption values between approximately 30-50 mL/100 g (ASTM D 281). The particle size distribution data for the specific particles evaluated in this work was measured using an internally developed test method that follows ISO 13320 and employs a Coulter LS particle size analyzer; median (d50), as well as d10, d90, d95 and d99 particle size data are summarized in Table 1. For simplicity, the particles were named in a manner to reflect their median particle sizes; however, the broad and bimodal particle size distributions of the ceramic microspheres result in CMS 9.0 containing more larger particles than CMS 9.9.
TABLE 1 ǀ Typical properties of select spherical precipitated silicas (SPH) and alkali aluminosilicate ceramic microspheres (CMS).
A much clearer understanding of the differences in particle size distribution profiles for the spherical silicas (SPH) relative to the ceramic microspheres (CMS) can be gained by plotting the data as shown in Figures 3 and 4 for the larger and smaller particles, respectively. From this data, one can see that the ceramic microspheres have broader particle size distributions than the spherical precipitated silicas. Additionally, the bimodal particle size distribution seen for the smallest ceramic microspheres, CMS 5.1, can present a challenge because the larger number of fine particles can result in an undesired viscosity increase due to their higher surface area.
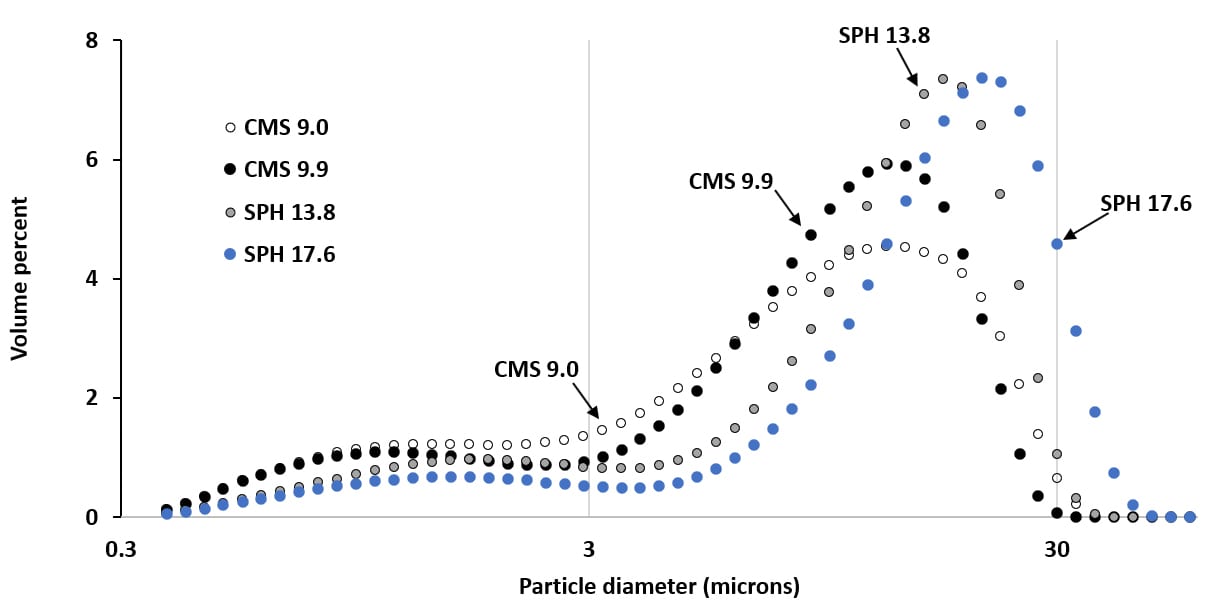
FIGURE 3 ǀ Comparison of particle size distribution profiles for larger particle size spherical precipitated silicas and ceramic microspheres.
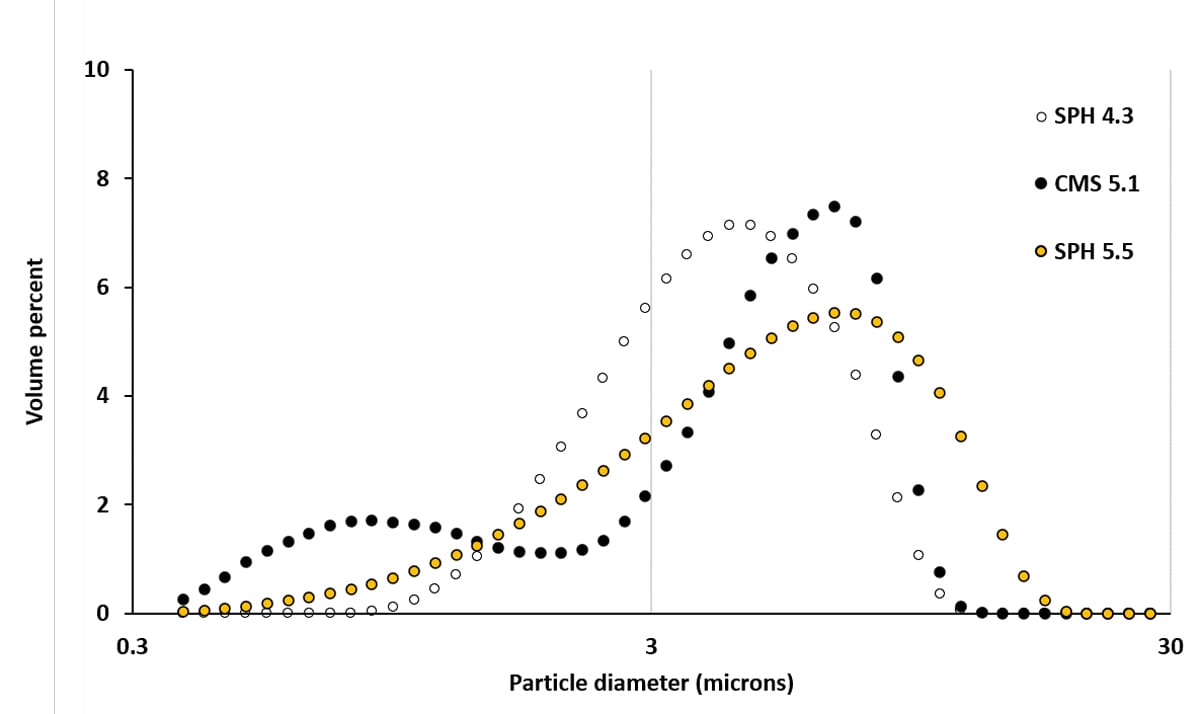
FIGURE 4 ǀ Comparison of particle size distribution profiles for smaller particle size spherical precipitated silicas and ceramic microspheres.
Coating Formulations
Waterborne architectural coatings formulations were prepared using the formulations shown in Tables 2 through 4. The larger particle size spherical precipitated silicas, SPH 13.8 and SPH 17.6, were evaluated in both flat paints, and CMS 9.0 was evaluated in the vinyl-acrylic flat paint. The two smaller particle size spherical precipitated silicas, SPH 4.3 and SPH 5.5, were evaluated in the vinyl-acrylic eggshell formulation. When either CMS or SPH were substituted for another filler, the substitution was done on a volume basis to maintain the same pigment volume concentration (PVC) for all paints within a given study.
TABLE 2 ǀ 62% PVC low-VOC vinyl-acrylic interior flat paint formulations.
TABLE 3 ǀ 52% PVC ultra-low-VOC premium vinyl acetate-ethylene (VAE) interior flat paints.
TABLE 4 ǀ 43% PVC low-VOC vinyl-acrylic interior eggshell paint formulations.
Testing of Paint Formulations
All paint application was conducted in a controlled temperature-humidity room consistent with ASTM D1640/D1640M-14. Paints were applied one day after preparation by drawdown on sealed Leneta 5DX charts using a seven mils Dow latex film caster and a BYK-Gardner Byko-drive automated film applicator. Gloss values were measured using a BYK-Gardner micro-TRI-gloss meter, taking readings at three points along the middle of the drawdown, and opacity measurements were taken using a BYK-Gardner spectro-guide 45/0 gloss spectrophotometer. Burnish resistance was measured using ASTM D6736 – 08 (Reapproved 2019) and wet scrub resistance was determined using ASTM D2486 – 17, Test Method A.
Results
Evaluations in Interior Flat Paints
The 62% PVC low-VOC vinyl-acrylic interior flat paint formulations shown in Table 2 were evaluated, and the results for burnish resistance testing and wet scrub resistance are shown in Figures 5 and 6, respectively. It should be noted that all paints had opacity values within 0.7% of that of the control paint. In this study, the replacement of the calcium carbonate with an equal volume of the largest particle-containing ceramic microsphere grade (CMS 9.0) and the largest commercial grade of spherical silica (SPH 13.8) was conducted first. The larger particle size SPH 13.8 gave very slightly lower initial 85° gloss and slightly better burnish resistance than the CMS 9.0 and the control paint. The SPH 13.8 also slightly improved wet scrub resistance when it replaced calcium carbonate, but the CMS 9.0 appeared to have no significant effect on wet scrub resistance when it replaced calcium carbonate.
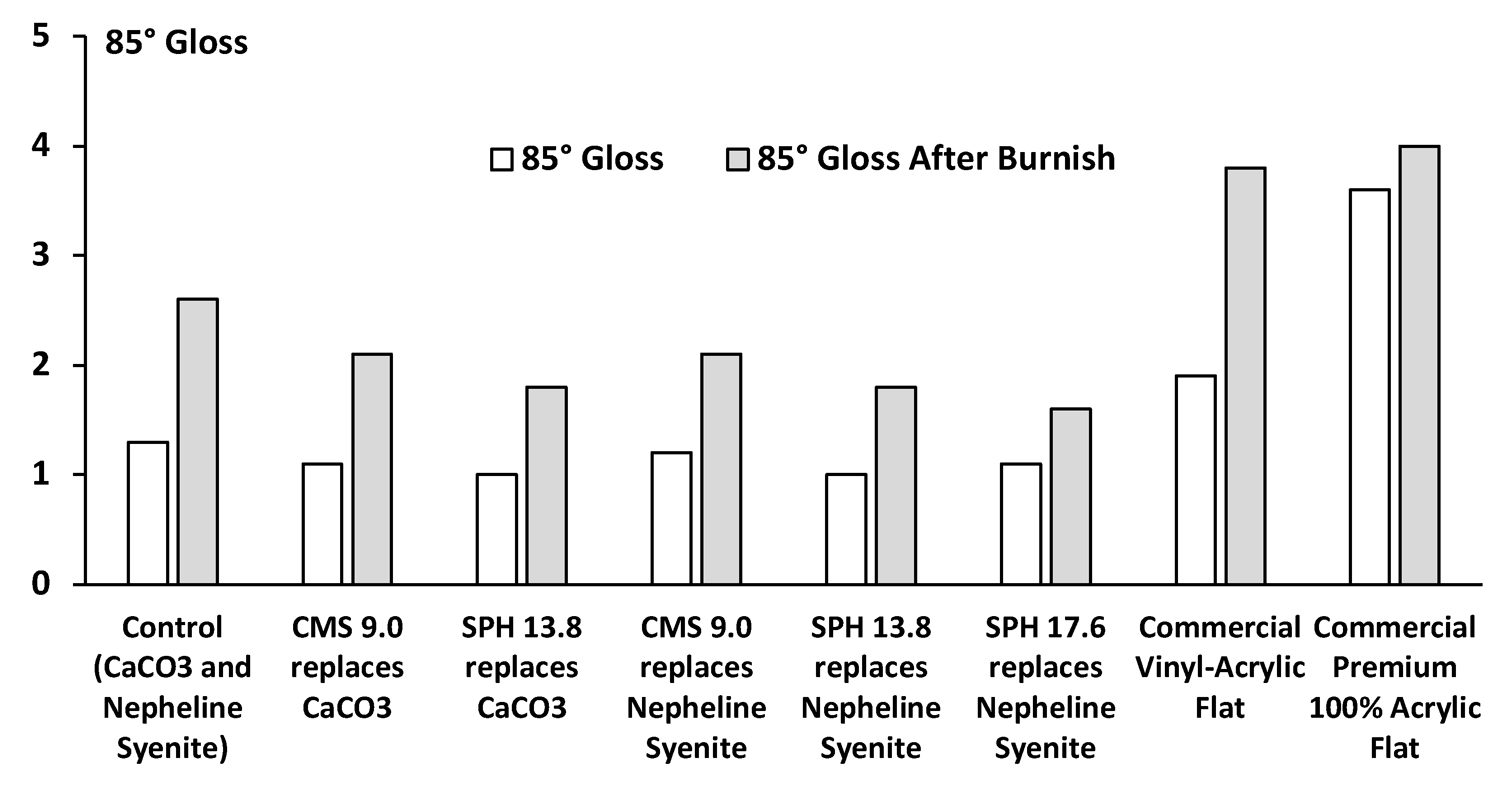
FIGURE 5 ǀ Comparison of 85° gloss before and after burnishing of vinyl-acrylic flat paints.
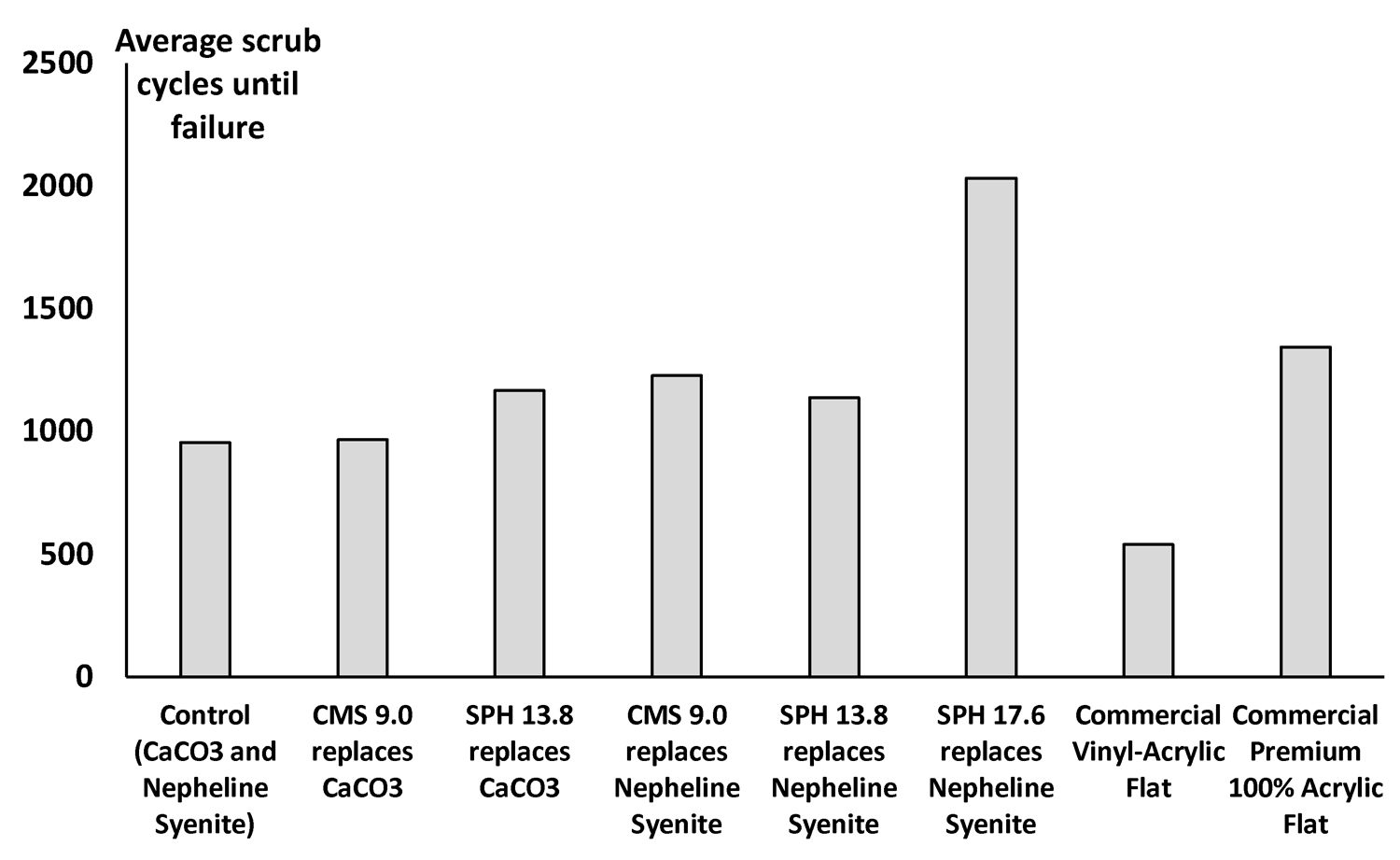
FIGURE 6 ǀ Wet scrub resistance of vinyl-acrylic flat paints.
When the spherical particles were used to replace the full volume of nepheline syenite, similar burnish resistance behavior was observed with both CMS 9.0 and SPH 13.8; however, the largest particle size spherical precipitated silica, SPH 17.6, showed even better burnish resistance. Surprisingly, the vinyl-acrylic flat paint containing the largest particle size spherical precipitated silica, SPH 17.6, showed significantly better burnish resistance than the commercial vinyl-acrylic flat paint and far exceeded the wet scrub resistance of both the commercial vinyl-acrylic and the premium 100%-acrylic paints.
The 52% PVC ultra-low-VOC premium VAE interior flat paint formulations shown in Table 3 were studied next, and only the two spherical precipitated silicas, SPH 13.8 and SPH 17.6, were carried forward into this second round of evaluations. The burnish and scrub resistance results are shown in Figures 7 and 8, respectively. While the best burnish and scrub resistance can be achieved by replacing all the nepheline syenite with an equal volume of SPH 17.6, significant improvements can be seen when only 50% of the nepheline syenite volume is replaced with the SPH 17.6. Therefore, the ability to optimize both cost and performance of a VAE flat paint to compete with a 100% acrylic flat paint is possible through clever formulation using various specialty fillers, including the large particle size spherical precipitated silica, SPH 17.6.
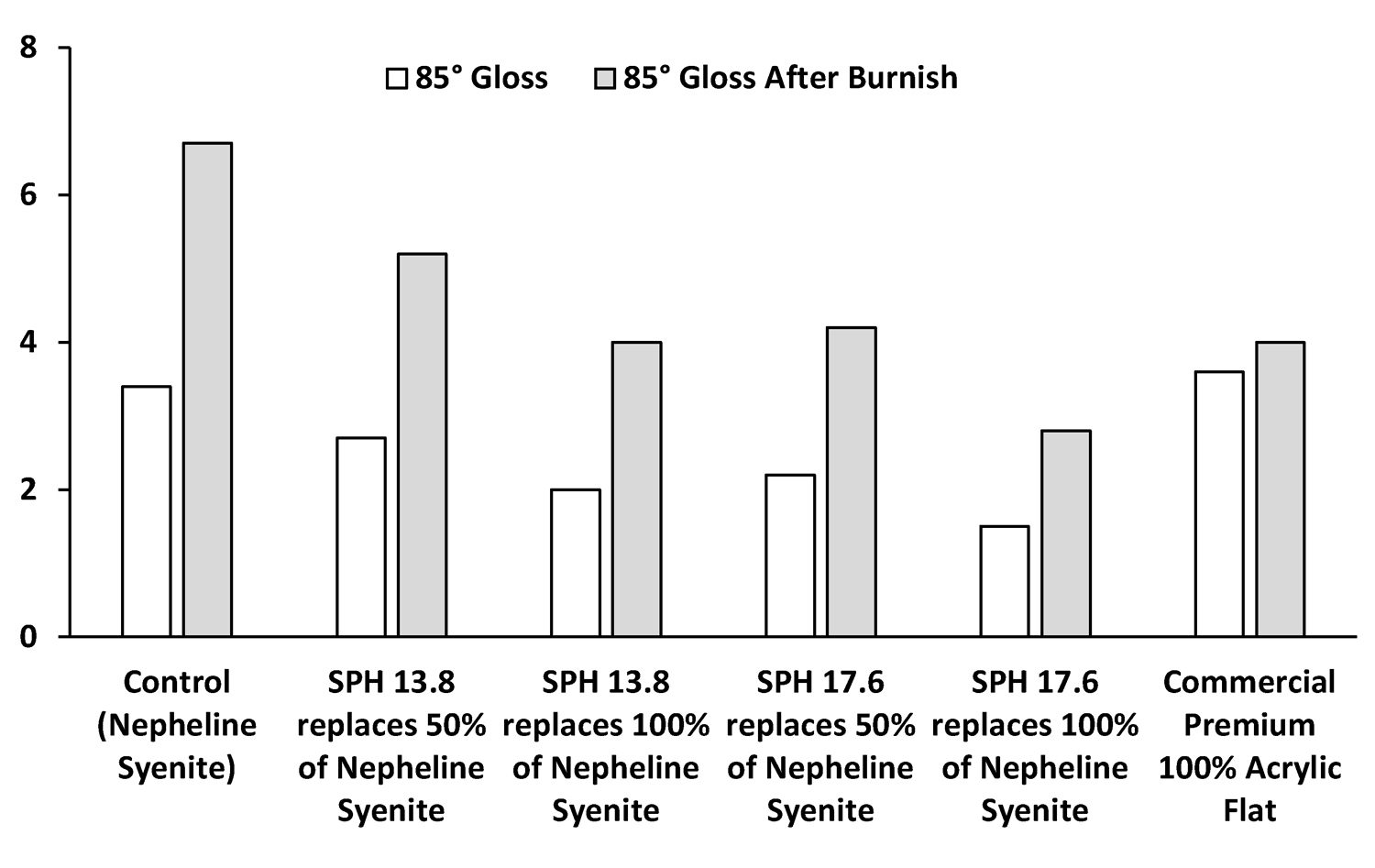
FIGURE 7 ǀ Comparison of 85° gloss before and after burnishing of 52% PVC VAE flat paints.
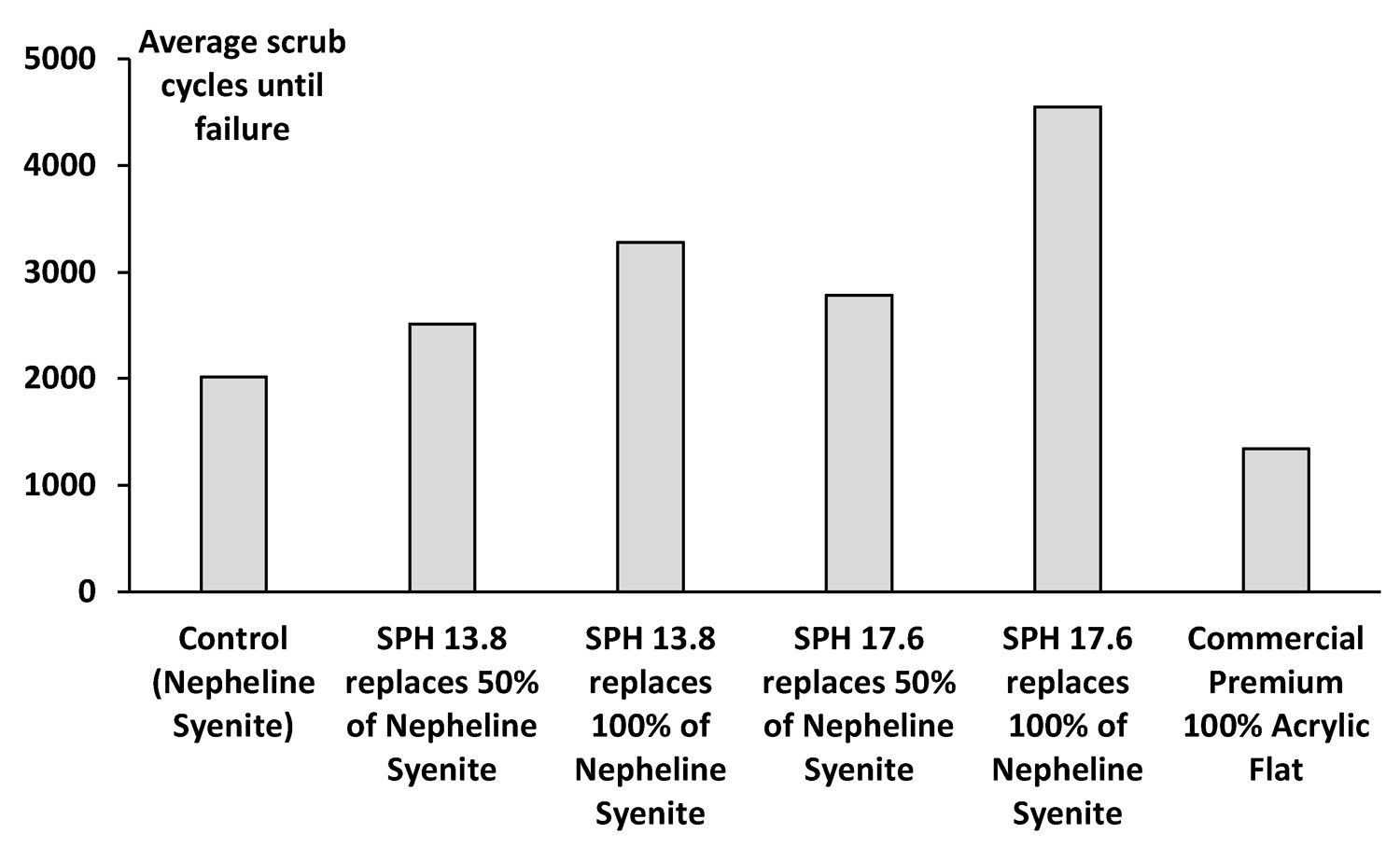
FIGURE 8 ǀ Wet scrub resistance of 52% PVC VAE flat paints.
Evaluations in Interior Eggshell Paint
The 43% PVC low-VOC vinyl-acrylic interior eggshellpaint formulations shown in Table 4 were then studied using the two smaller particle size spherical precipitated silicas, SPH 4.3 and SPH 5.5, to replace nepheline syenite on a volume basis. All paints had opacity values within 1.5% of that of the control formulation. The burnish resistance results in Figure 9 reveal that the larger particle size SPH 5.5 causes a 9.8 GU drop in initial 85° gloss while the smaller particle size SPH 4.3 has much less impact on initial gloss — only causing a 4.3 GU reduction in initial 85° gloss — when each is used to replace the total volume of nepheline syenite. The commercial premium 100%-acrylic eggshell paint has outstanding performance, as its 85° gloss increases only 1.7 GU, while the control vinyl-acrylic eggshell experiences a substantial 5.0 GU increase on burnishing. Replacing the full volume of nepheline syenite in the vinyl-acrylic formulation with SPH 5.5 results in the best burnish resistance (only a 1.3 GU increase in 85° gloss on burnishing).
The smaller particle size spherical precipitated silica, SPH 4.3, is also able to improve burnish resistance in this paint. Replacing 100% of the nepheline syenite volume with SPH 4.3 results in a 2.3 GU up-sheen but using 50 - 75% (v/v) of the SPH 4.3 in combination with nepheline syenite can also provide improvements in burnish resistance.
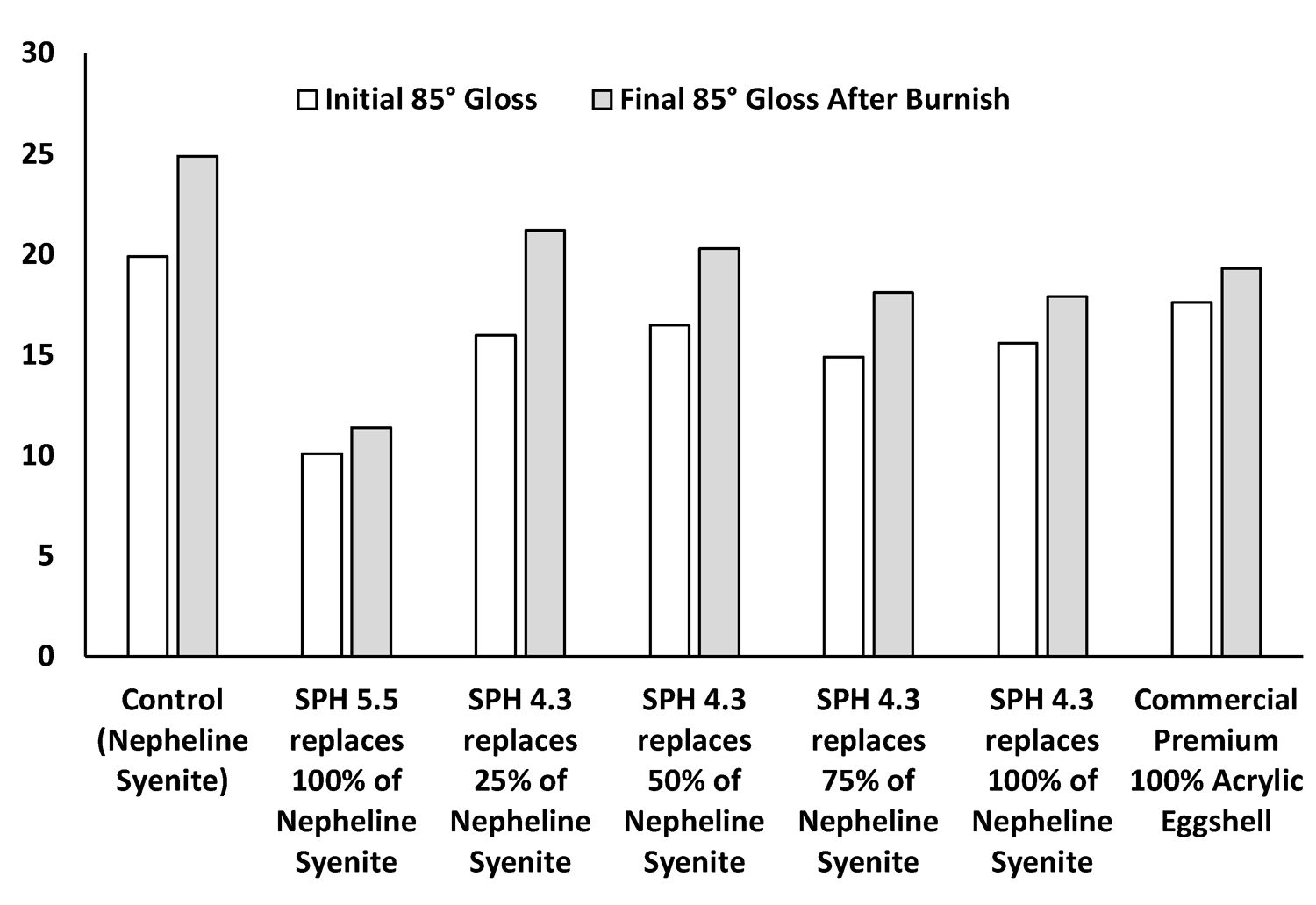
FIGURE 9 ǀ Comparison of 85° gloss before and after burnishing of 43% PVC vinyl-acrylic eggshell paints.
The wet scrub resistance data for the 43% PVC vinyl-acrylic eggshell paints is shown in Figure 10. Surprisingly, the commercial premium 100%-acrylic paint failed after far fewer scrub cycles than any of the vinyl-acrylic paints, and the control vinyl-acrylic eggshell paint performed quite well. The addition of either SPH 5.5 or SPH 4.3, even at 25% of the filler volume, significantly improved the scrub resistance of this vinyl-acrylic eggshell, bringing performance into the realm of higher quality paints.
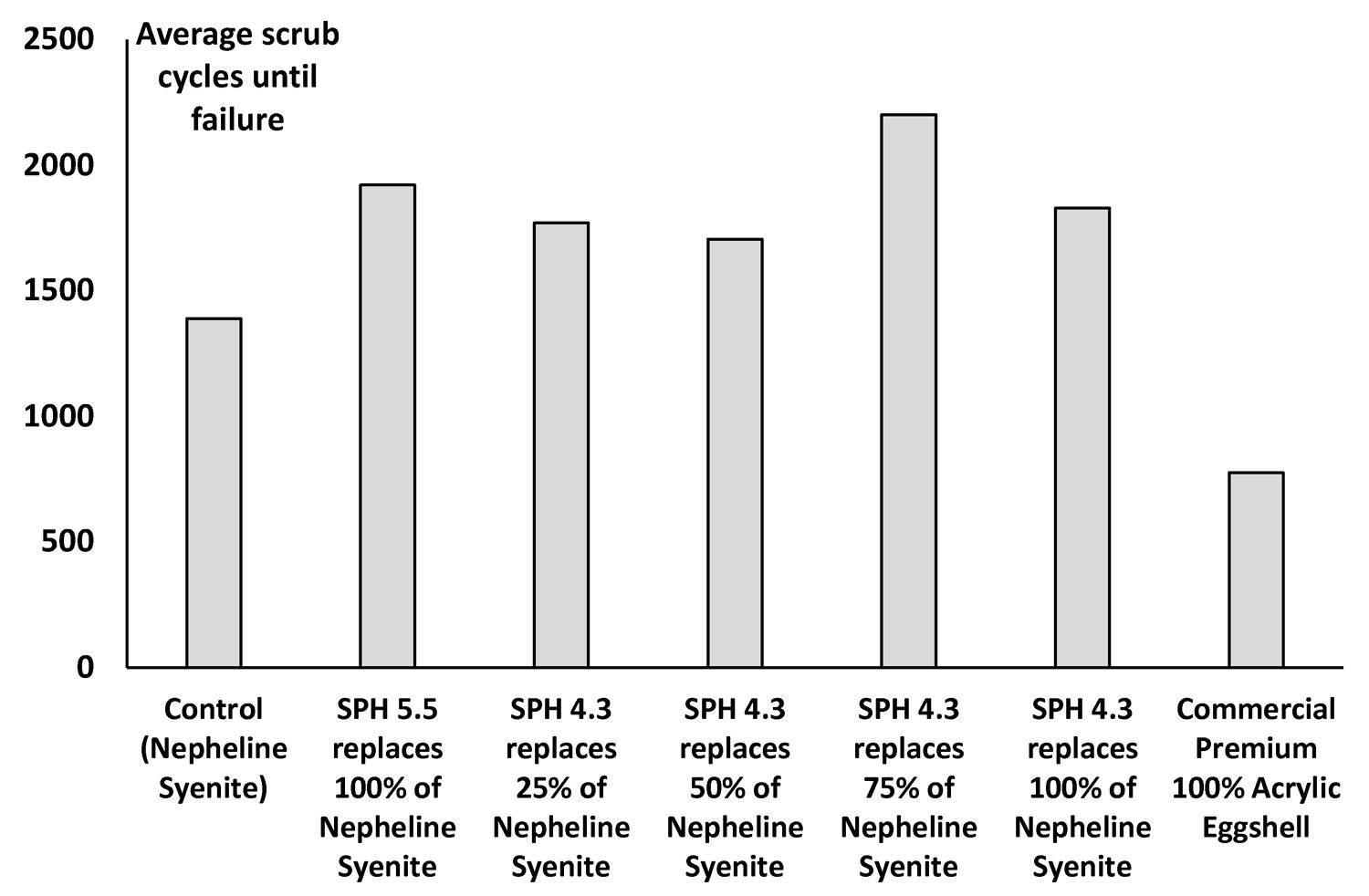
FIGURE 10 ǀ Wet scrub resistance of 43% PVC vinyl-acrylic eggshell paints.
Discussion
The results of these evaluations with spherical precipitated silica particles in the interior flat and eggshell paints bring to light several important learnings. As expected, the larger particle size materials have a stronger impact on the 85° gloss of a paint. Therefore, the SPH 13.8 and SPH 17.6 are best used in flat/matte paints where very low gloss values are desired; in these formulations, the larger particle size SPH 17.6 has a greater impact on both burnish and scrub resistance and can be used efficiently to achieve improved performance by replacing at least a portion of the nepheline syenite in the formulation. As a result, vinyl-acrylic and VAE flat paints that exceeded the scrub resistance of a premium 100%-acrylic paint were achieved.
Particle size is even more important in higher sheen paints, as even the spherical precipitated silica, SPH 5.5, significantly reduces the 85° gloss of the eggshell formulation tested here. While a little less efficient in improving burnish resistance, the slightly smaller SPH 4.3 can be used to greatly improve wet scrub resistance and it has far less impact on the initial gloss of the paint. This smaller grade of spherical precipitated silica can enable high performing vinyl-acrylic eggshell paints that rival the performance of a premium 100%-acrylic formulation.
Comparison of scanning electron micrographs of dried eggshell paints containing either nepheline syenite (Figure 11) or a small size spherical precipitated silica (Figure 12) as the only filler give insight into the mechanism of action of these unique particles. Burnishing appears to remove the larger nepheline syenite particles from the surface of the coating, leaving reduced surface roughness, with much smaller nepheline syenite particles visible under the surface. In Figure 12, more of the larger spherical precipitated silica particles are visible at or near the surface of the coating that contains SPH 5.5. Burnishing abrades a few of the spheres at the surface, but many of the spherical particles remain to provide a topography that can still scatter light. In the coating that contains the spherical precipitated silica, the binder appears to have well coated the individual silica spheres rather than agglomerates of smaller particles. This is likely due to the silica being spherical and having a narrower particle size distribution; therefore, it contains far fewer fine particles than the nepheline syenite grade used in Figure 11.
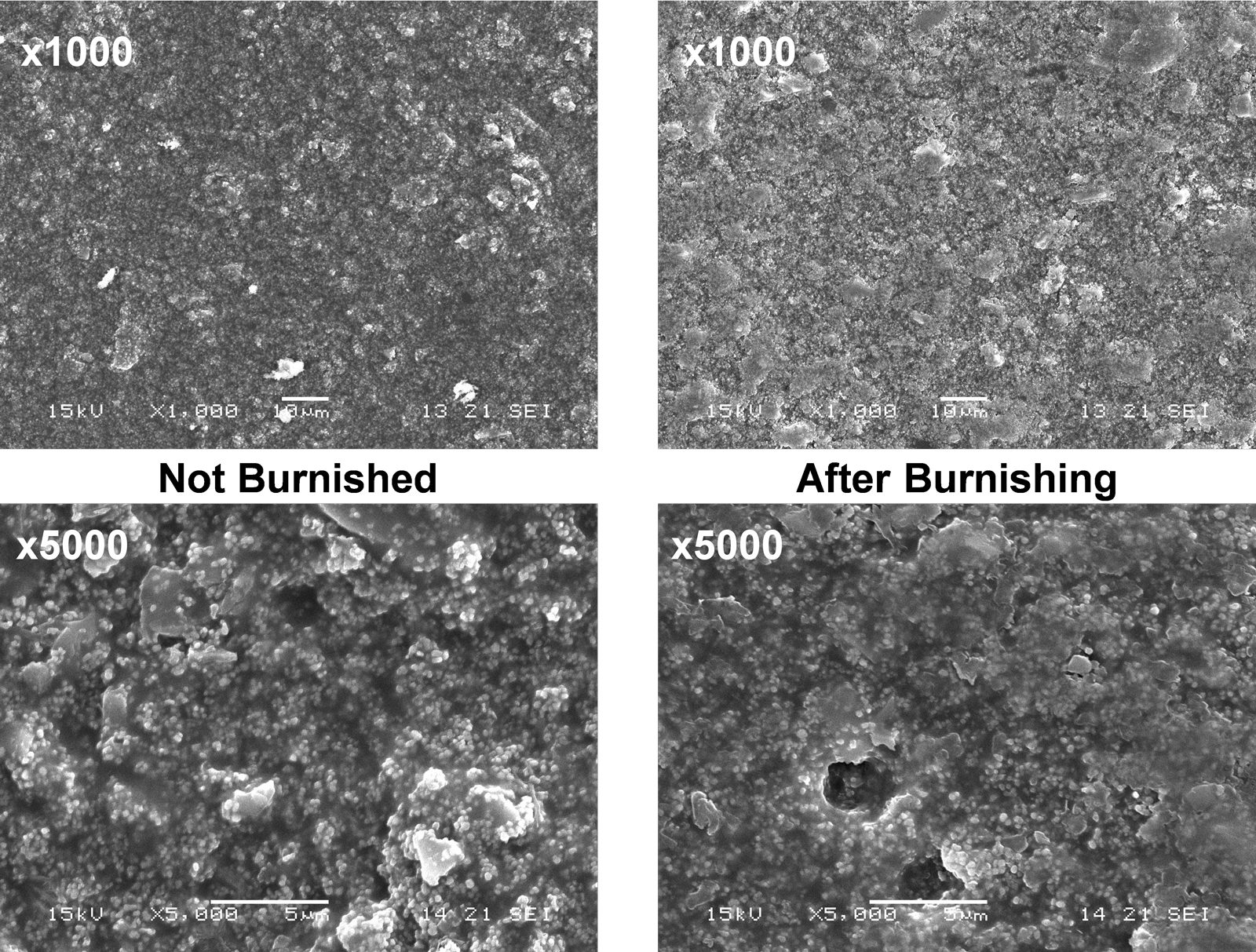
FIGURE 11 ǀ Scanning electron micrographs of VAE eggshell paint containing nepheline syenite of 2.5 μm median particle size before and after burnishing.
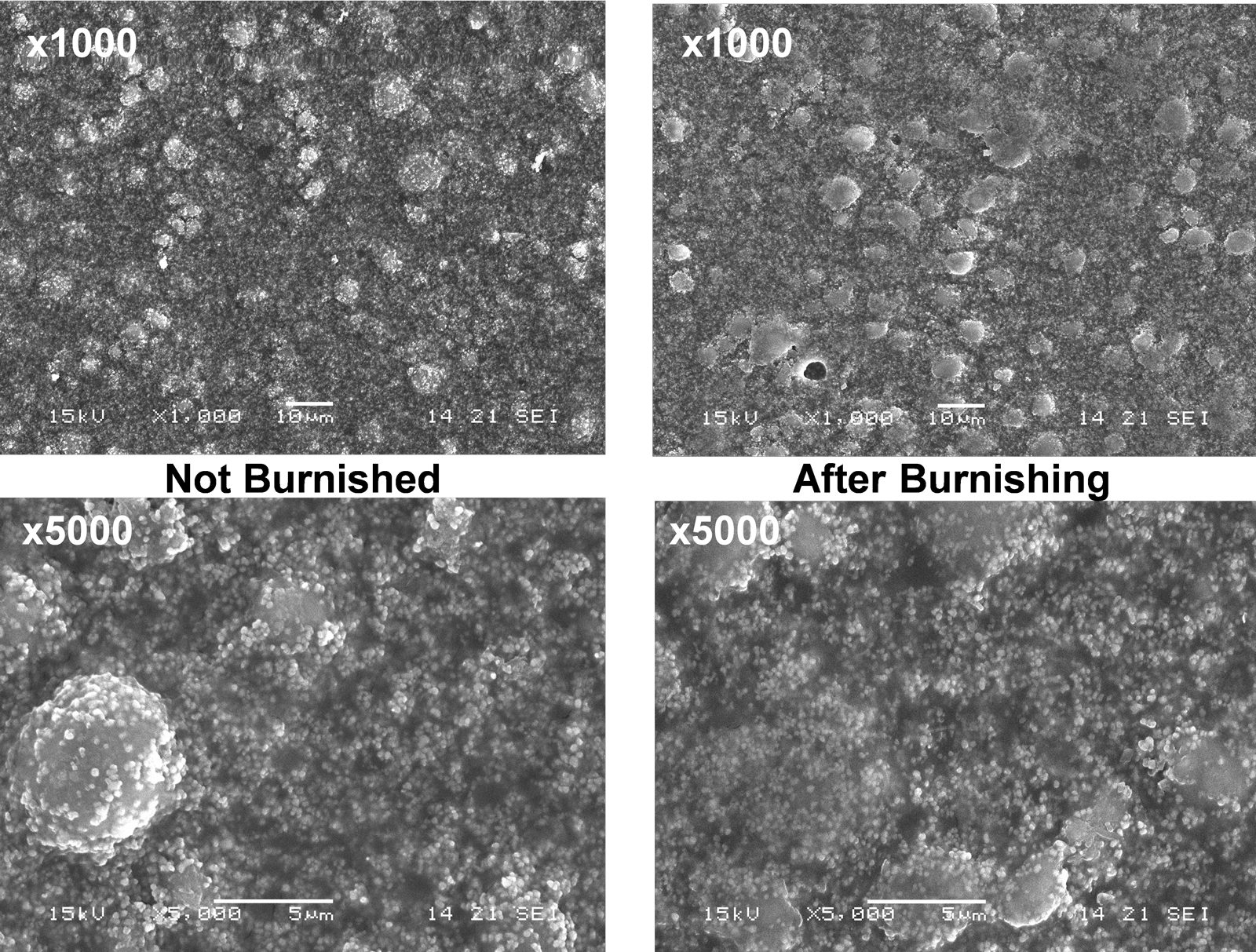
FIGURE 12 ǀ Scanning electron micrographs of VAE eggshell paint containing spherical precipitated silica of 4 μm median particle size before and after burnishing.
Conclusions
Spherical precipitated silica particles can dramatically improve wet scrub resistance, as well as burnish resistance, of interior architectural paints. These benefits can be leveraged to increase coating performance and even improve vinyl-acrylic and vinyl acetate-ethylene copolymer-based paints to exceed the wet scrub resistance of a premium 100%-acrylic flat paint by partially or completely replacing the nepheline syenite filler with a spherical precipitated silica with a median particle size of 17.6 microns. Similarly, a vinyl-acrylic eggshell formulation with significantly better wet scrub and burnish resistance could be achieved by using a spherical precipitated silica with a median particle size of 4.3 microns. Thus, these unique particles prove useful tools that can be leveraged alone or in combination with one or more other fillers to formulate high-quality yet cost-effective interior architectural coatings.
Acknowledgments
The authors would like to thank Karl Gallis for designing and arranging the production of pilot and production scale spherical precipitated silicas, Jonathan Sefko for conducting evaluations in the VAE flat paint, and Doris Simoes and Dennis Begley for obtaining the particle size analysis data.
References
1 Wieroniey, T. Life-Cycle Assessment of Architectural Coatings, CoatingsTech, 2021, 44 - 48.
2 Shefelbine, T.; Forehand, C.; Rink, K. 3M™ Ceramic Microspheres in Architectural Paint, www.3M.com/paintsandcoatings, 2015.
3 Hagar, W.J.; Gallis, K.W. Continuous Silica Production Process and Silica Product Prepared from Same, US Patent 8,609,068 B2, 2013.
4 Hagar, W.J.; Gallis, K.W. Continuous Silica Production Process and Silica Product Prepared from Same, US Patent 8,945,517 B2, 2015.
5 Hagar, W.J.; Gallis, K.W. Continuous Silica Production Process and Silica Product Prepared from Same, US Patent 9,327,988 B2, 2016.
6 Hagar, W.J.; Gallis, K.W. Continuous Silica Production Process and Silica Product Prepared from Same, US Patent 9,617,162 B2, 2017.
7 Hagar, W.J.; Romer, R.L.; Fultz, W.C.; Gallis, K.W. Coating Compositions Comprising Spheroid Silica or Silicate, US Patent 9,028,605 B2, 2015.
8 Romer, R. Spherical Precipitated Silica, Paint & Coatings Industry Magazine, 2017.
9 Resch, B. Novel Synthetic Silica for Matting Powder Coatings, Presentation at Powder Coating Summit, 2021.