Ready to proof -- Clare 8-10-22
KJ proofed on 8/15 and marked a comment for Clare below
CB proofed on 8/15 and added comment for Clare/KJ
Ready for author
Credit:monkeybusinessimages, Creatas Video+ / Getty Images Plus, via Getty Images
Inventive Routes
for the Preparation of Waterborne Acrylic Polyols
for 2K PU Protective Topcoats
By David Vanaken, Denis Heymans, Felix Feng and Nathalie Havaux, Hexion Research Belgium
New regulations, increased awareness, and the importance of environmental stewardship have led to a strongly increased demand for waterborne (WB) protective topcoats. However, matching the performance of solventborne (SB) two-component (2K) polyurethanes remains a challenge for resin and paint producers. Synthesis and formulation of primary or secondary dispersions are not straightforward.
For secondary dispersions, the removal of solvents from polyols prior to dispersion in water is technically challenging. The emulsion polymerization process producing primary dispersions often faces problems of water-phase homopolymerization of the hydroxyl monomers, resulting in a poor stability of the emulsions, high process grit, and insufficient crosslinking of the final coatings.
Waterborne acrylic polyols (APO) for 2K urethane finishes have played an important role in enabling regulatory compliance in the industrial market, yet their synthesis can be difficult. This article introduces two methods to produce high-performance, solvent-free waterborne acrylic polyols using either glycidyl neodecanoate or its acrylated adduct. The performance characteristics of coatings made with these waterborne polyols are also demonstrated.
Waterborne Technologies
Because of their lower environmental impact, both acrylic polyol dispersions and hydroxyl-functional (OH-functional) emulsions are state-of-the-art technologies for high-performance 2K WB industrial coatings applications. Both types of products may be crosslinked with diverse WB isocyanates. This article describes production routes for water-based APO dispersions and waterborne hydroxy-functional emulsions using unique versatile monomers leading to process and performance improvements.
Waterborne APO Secondary Dispersions
Glycidyl neodecanoate (CarduraTM glycidyl ester1) is a highly versatile building block containing a very reactive epoxy group, and a unique hydrophobic and highly branched tertiary substituted α-carbon structure (Figure 1). The epoxy group is used to incorporate the molecule into polymers through reaction with carboxylic acid functions, and the neodecanoate group imparts outstanding performance characteristics. Incorporation of glycidyl neodecanoate into polymers brings enhancements such as excellent resistance to acidic conditions, superior wet look appearance, very good weatherability, and low viscosity.
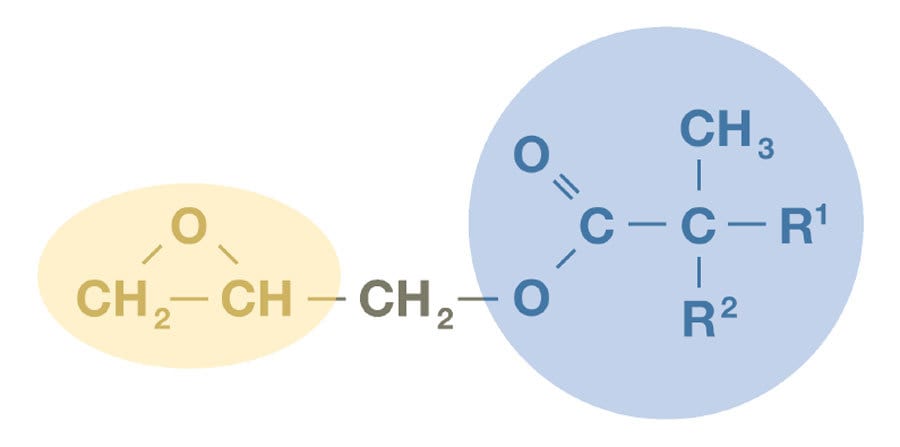
FIGURE 1 ǀ Glycidyl neodecanoate, Cardura glycidyl ester.
Glycidyl neodecanoate has been used for decades as a reactive solvent for solventborne acrylic polyol synthesis, and its value in enabling easy synthesis of low-viscosity2, high-performance, high-solids polymers is well documented3. The synthetic pathway that glycidyl ester provides to solventborne systems is greatly beneficial in waterborne acrylic polyol synthesis as well.
When used as a reactive solvent for acrylic polyol synthesis, glycidyl neodecanoate replaces part or all of the solvent that would otherwise be required to conduct the polymerization and that ends up in the final coating and therefore increases VOC. In this way, the need to conduct a solvent removal step to achieve low solvent content has been eliminated (Figure 2).
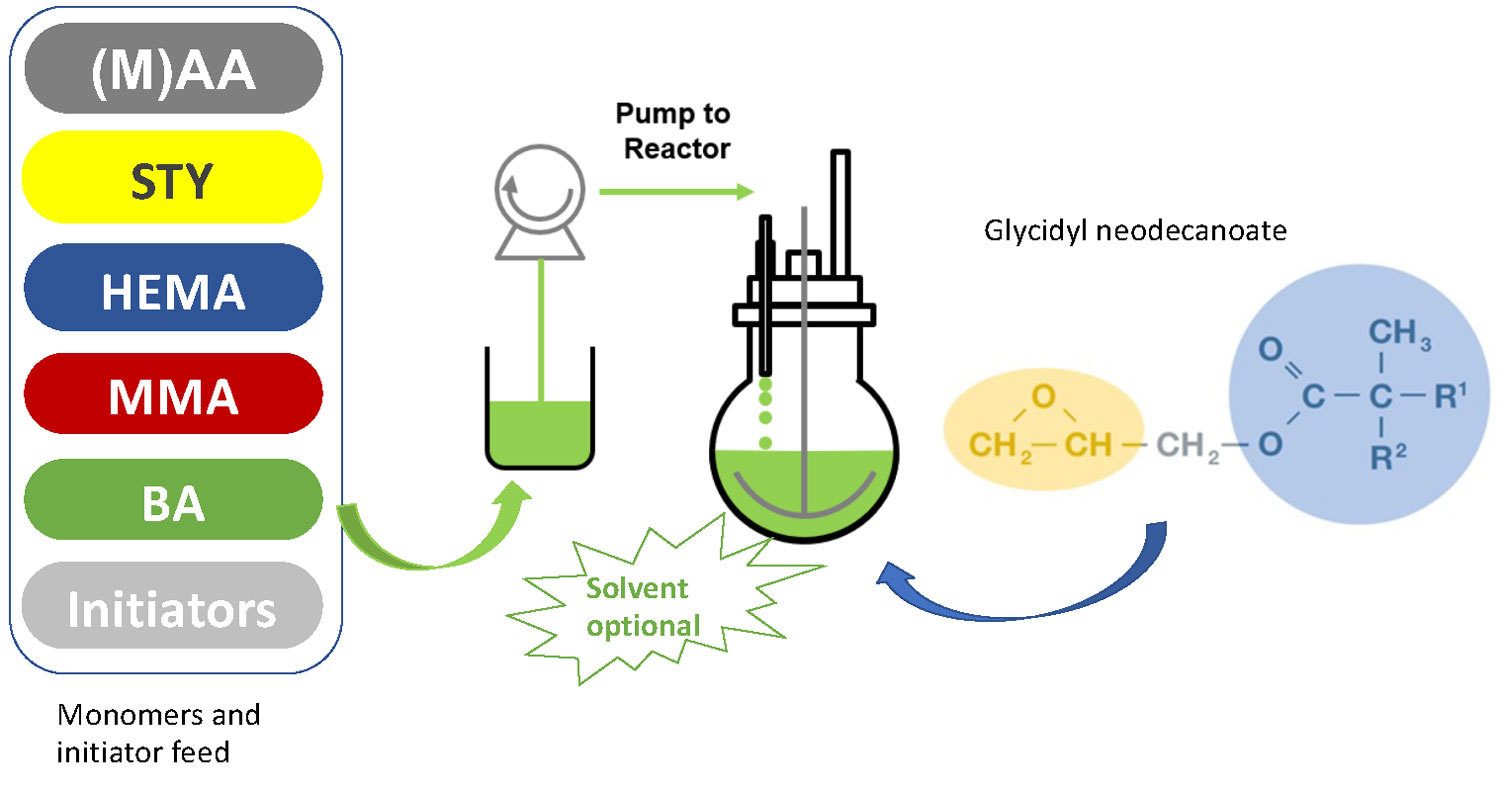
FIGURE 2 ǀ Glycidyl neodecanoate as reactive solvent in the initial reactor charge.
The initial reactor charge made of glycidyl neodecanoate and optionally some solvents, permits an easy polymerization process at very high polymerization temperature without pressure build-up thanks to the very high boiling temperature of glycidyl neodecanoate (>250 °C). Once the initial reactor charge has reached the polymerization temperature, the acrylic monomers can be dosed at the desired rate. This process allows the preparation of low-molecular-weight (Mw) resins with a solids content of up to 100%, which is ideal for the preparation of solvent-free, water-based APO dispersions.
Glycidyl neodecanoate is gradually incorporated into the polymer backbone during the monomer feed step by the reaction of its epoxy functionality with acid groups of acrylic or methacrylic acid present in the monomer feed. During this process, two reactions occur simultaneously: a conventional radical polymerization of the monomers, and the reaction of the glycidyl ester with some acrylic or methacrylic acid added to the monomer mixture, which grafts the glycidyl neodecanoate to the acrylic polyol (Figure 3).
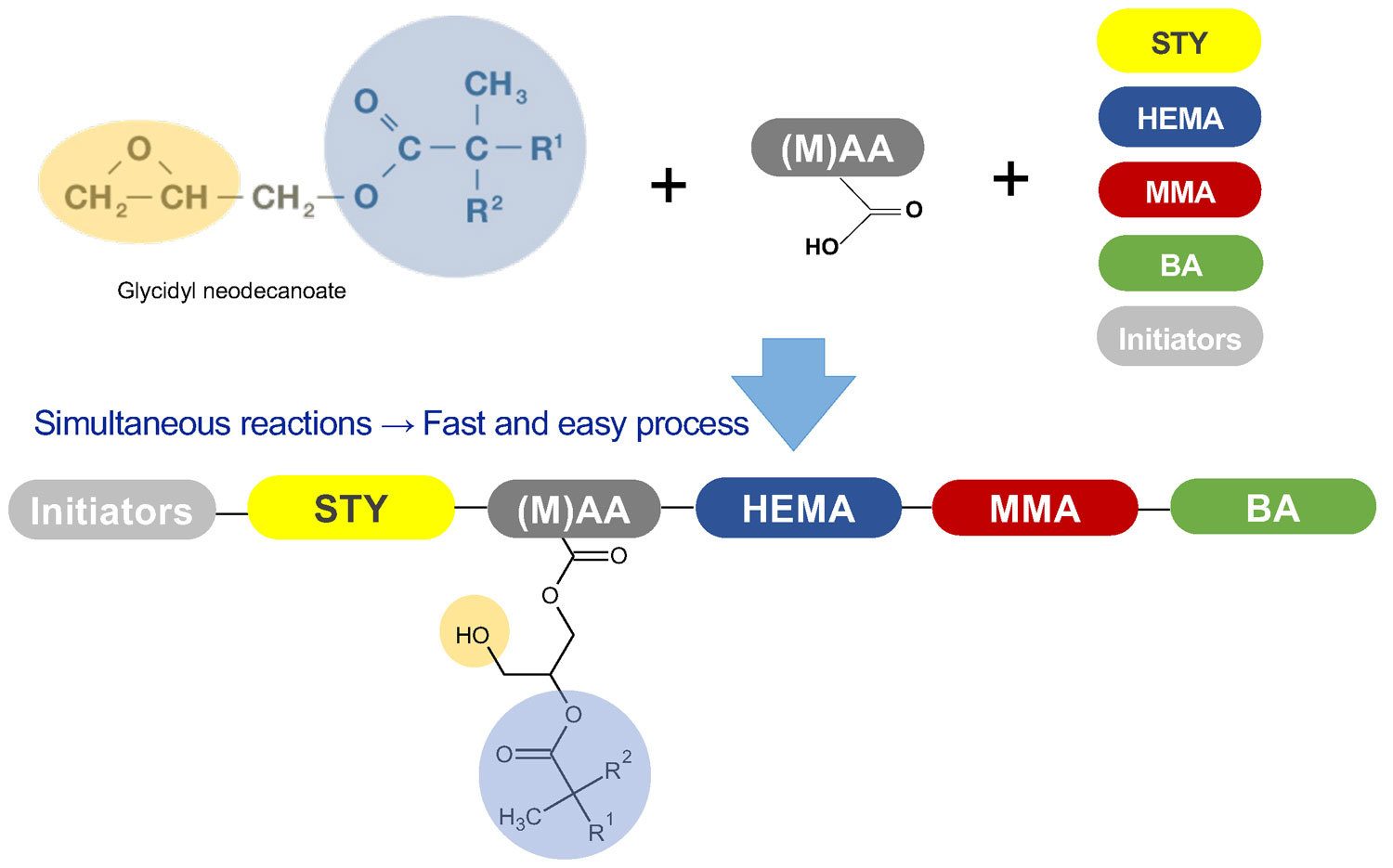
FIGURE 3 ǀ Preparation of glycidyl ester-based acrylic polyol, glycidyl ester incorporation in polymer backbone.
It is also interesting to note that the hydroxyls formed have been found to be mostly primary hydroxyls, which is essential to ensure a fast reaction rate with isocyanates, and thus an adequate hardness development rate of the coatings4.
In addition to an easy polymerization process at high temperature, glycidyl neodecanoate brings a number of benefits, including an improved topcoat appearance, durability, and lower VOC.
Synthesizing acrylic polyols at high temperatures is a simple and efficient way to produce low-molecular-weight, low-viscosity polymers without the need for high quantities of initiator or chain transfer agents, which both affect polymer performance and increase the cost. The low viscosity of the polyols synthesized with glycidyl neodecanoate also makes the dispersion process easier.
Waterborne acrylic polyols are typically prepared via a conventional radical polymerization process in solvent, like their analogues for solventborne coatings. Without special pressure reactors, processing temperature is limited to the boiling point of the process solvent.
The first role of the solvent is to provide a medium for the polymerization process, to enable stirring in the reactor. It also reduces the viscosity during polymerization, which is important to avoid auto-acceleration5, and in this way it ensures an adequate control of polymer molecular weight. After polymerization, the solvent also eases the dispersion in water and helps to reduce particle size. Finally, after application of the coatings, it facilitates the film formation process, improves the appearance of the final coatings, and reduces the film defects.
In addition to the usual ester monomers, the polymer composition may include specific acid monomers. Acrylic or methacrylic acid for instance, ensure for an easy dispersion in water after polymerization by imparting anionic character to the polymer. After the polymer is synthesized, these acid groups are neutralized with an amine to convey water dispersibility. This relatively high concentration of carboxylic acid groups may lead to issues during cure (interference with the isocyanate crosslinkers) and to moisture sensitivity of the cured films. Furthermore, to produce stable dispersions, such chains cannot be too long, and they usually have Mw values around 10,000 Da. Under similar cure conditions (catalyst and isocyanate concentration), these shorter chains exhibit slower cure response because they fall short in properties from physical drying.
One disadvantage of the polyols prepared via conventional process is their solvent content contributing to the VOC of the coatings; additionally they may affect colloidal stability. A solvent removal step is of course possible after polymerization, via vacuum distillation. However, to evaporate these solvents an energy and time-intensive distillation step is required. During this process, some chemical reactions lead to a broadening of the molecular weight distribution and therefore lower performance of the derived coatings. However, when the process makes optimal use of glycidyl neodecanoate reactive solvent, the need for conventional solvents is reduced and the evaporation step may be eliminated.
Performance of Waterborne Acrylic Polyols Based on Glycidyl Neodecanoate
To demonstrate the performance of solvent-free waterborne acrylic polyols made with glycidyl neodecanoate, a solvent-free polymer was designed with a Tg, hydroxyl number and acid value very similar to those of a commercial dispersion containing 12% solvent on polymer solids. These polymers were tested side by side in a 2K urethane clearcoat system and evaluated for a variety of film properties. The results demonstrate that glycidyl neodecanoate makes it possible to create solvent-free waterborne polyol dispersions that have performance on par with conventional solvent-containing waterborne polyol dispersions (Figure 4).
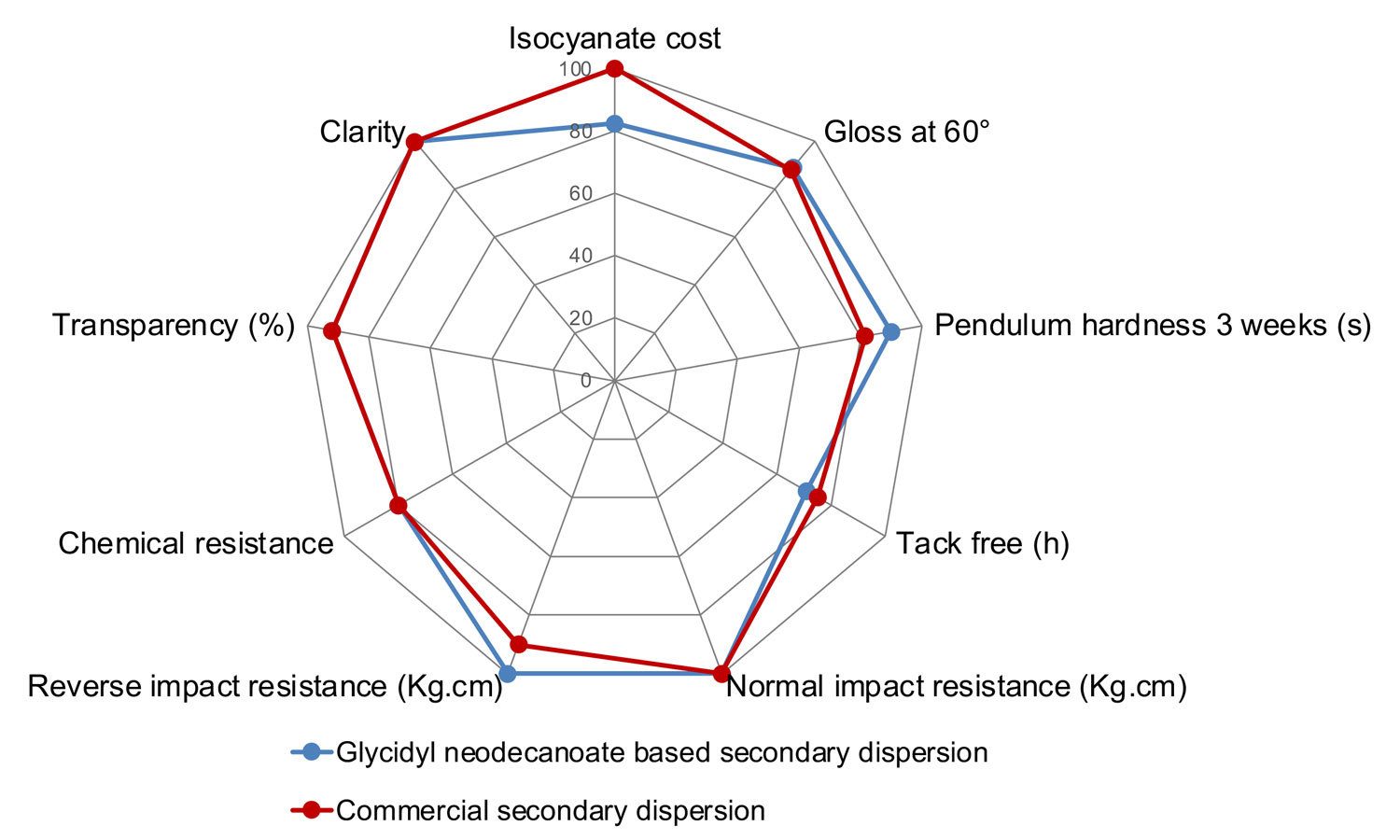
FIGURE 4 ǀ Comparison of a solvent-free acrylic polyol dispersion based on glycidyl neodecanoate and a conventional polyol dispersion containing solvent.
Waterborne APO Secondary Dispersions Conclusion
Acrylic polyols for 2K waterborne topcoats can be formulated with a much lower solvent level than solventborne systems, possibly to near-zero VOC levels. Additionally, these systems have a very good hardness development rate compared to their solventborne analogues. The use of glycidyl neodecanoate as reactive diluent to partially or totally replace the solvents during acrylic synthesis, remarkably simplifies their preparation and offers the possibility for the preparation of very low-VOC coatings.
The preparation of acrylic polyols via different processes combining radical polymerization and a condensation reaction with glycidyl neodecanoate offers various possibilities to adjust the polyol composition and properties for high-quality topcoats.
The use of unique glycidyl ester technology eliminates the need to distil solvent after production. Eliminating solvent removal from the process reduces cycle time, waste, and production costs.
Waterborne Hydroxy-Functional Emulsions
Acrylated glycidyl neodecanoate (AGN) (Figure 5) is a versatile molecule containing an acrylic unsaturation, OH functionality (mostly primary), and a very hydrophobic and highly branched tertiary substituted structure. AGN is obtained by the reaction of (meth)acrylic acid with glycidyl neodecanoate. The resulting monomer has an acrylic functionality, key to incorporate AGN into polymers through reaction with other unsaturated monomers. The OH group can be used for crosslinking with isocyanates, and the branched alkyl chain imparts outstanding performance characteristics.
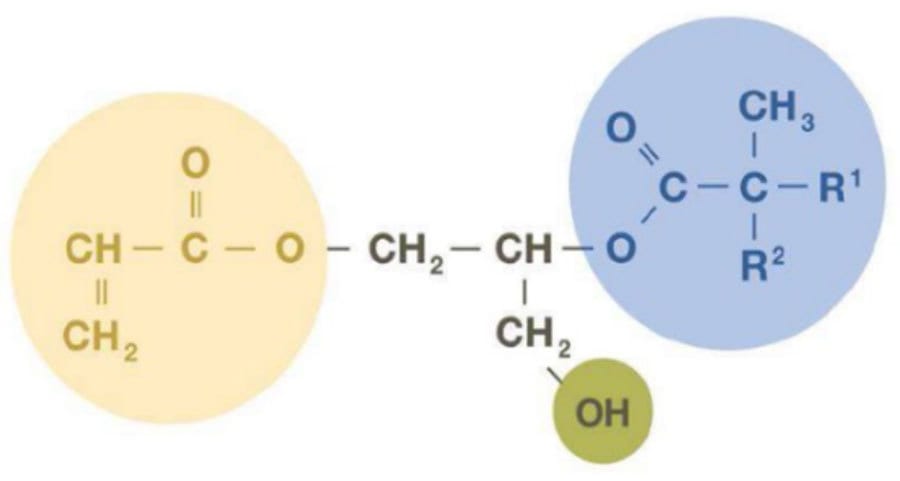
FIGURE 5 ǀ Acrylated glycidyl neodecanoate.
Primary vs. Secondary Dispersions
As described in the first part of this article, typical secondary dispersions involve polymerization (with or without solvent), neutralization of carboxylic acid groups, dispersion of the neutralized resin in water, and an additional fourth step of solvent removal. This last step may occur at different times, according to equipment and technology.
While polymerization and neutralization may be performed in the same vessel, the dispersion step will require high-shear mixing to ensure formation of a stable dispersion.
Emulsion polymerization is a simpler process performed in a single vessel with a rather simple design. It does not require the use of solvents, rather using water as polymerization medium, and can be performed at lower process temperatures than solventborne polymerization (Figure 6).
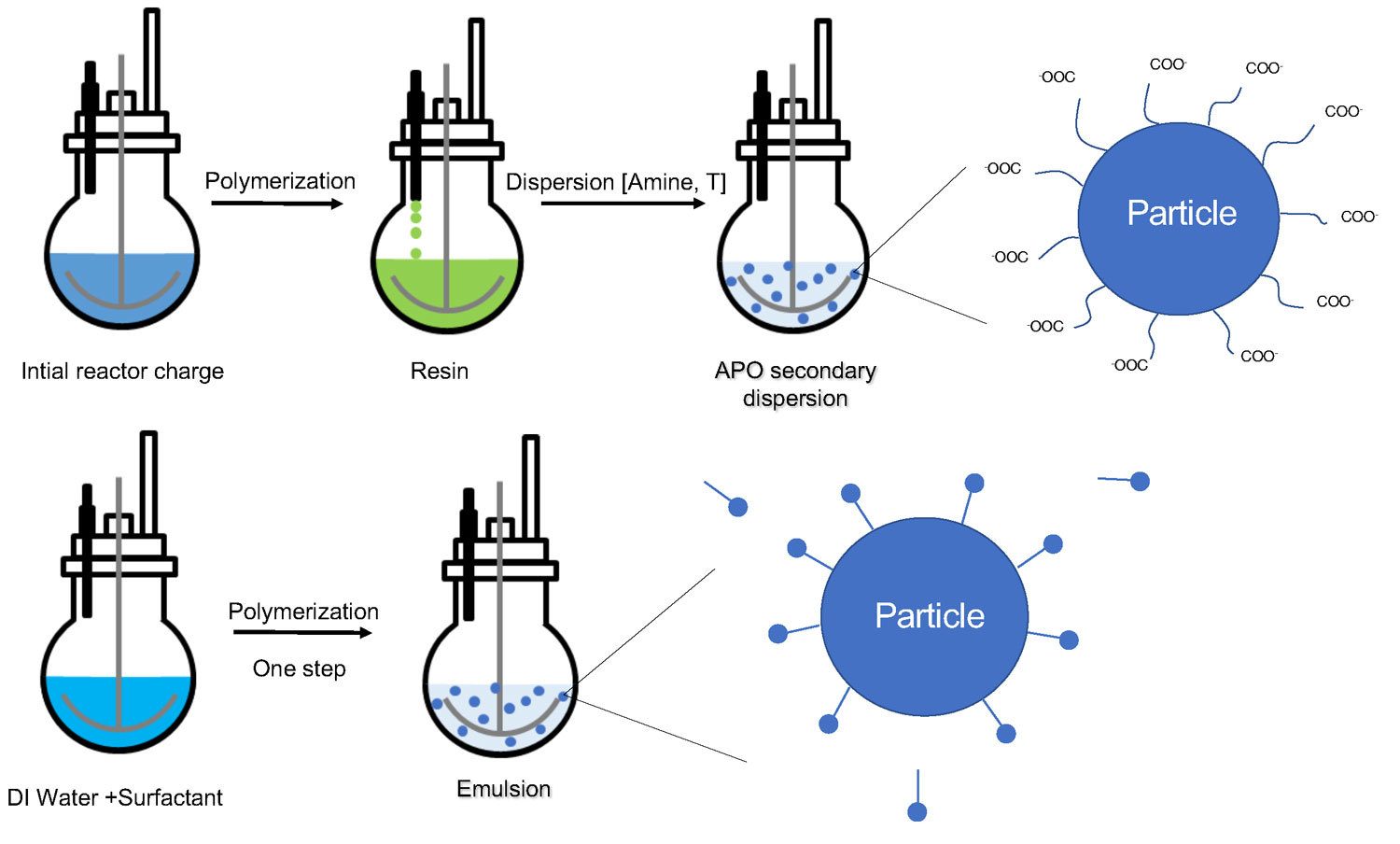
FIGURE 6 ǀ Comparison of synthesis and structure for WB APO secondary dispersions and WB APO emulsions.
Hydroxy-functional acrylic emulsions can be designed with a wide range of hydroxyl values and performance characteristics to address the needs of many different applications in plastic, wood, and construction coatings.
Emulsion polymerization can be compared to a multitude of parallel bulk reactions performed in nanosized reactors (the polymer particles). Emulsions are stabilized with surfactants, and high Mw values can be attained (upwards of 200,000 Da). Thus, once the emulsion-based coating has been applied and its film has coalesced, it will present physical properties before the onset of cure, solely because of the higher molecular weight. This will improve the apparent drying time and other characteristics, such as handling time. However, a key disadvantage of emulsion polymerization is the use of surfactants for the process, which affect the water sensitivity of derived coatings.
Novel OH-Functional Emulsions for High-Performance WB 2K PU Coatings
Most often, the source of OH functionality in hydroxy functional emulsions is HydroxyEthyl MethAcrylate monomer (HEMA). HEMA is a small, very polar molecule readily miscible with water. HEMA’s solubility in water creates some process problems. Actually, HEMA-rich monomer pre-emulsions tend to be less stable than those based on less soluble monomers6,7. Moreover,once fed into the polymerization reactor, HEMA tends to more easily homopolymerize in the water phase (and not in the micelles) — this leads to emulsions with higher grit formation and reduced HEMA concentration in the polymer micelles (HEMA does polymerize, albeit “in the wrong place”).
The use of AGN as another source of OH functionality addresses both issues above. Since the solubility of AGN in water is low, it readily migrates to the organic micelles. In doing that, AGN helps stabilize the polymer pre-emulsion and reduce grit formation. Figure 7 illustrates these benefits for an emulsion with 4.2 wt% OH on solids.
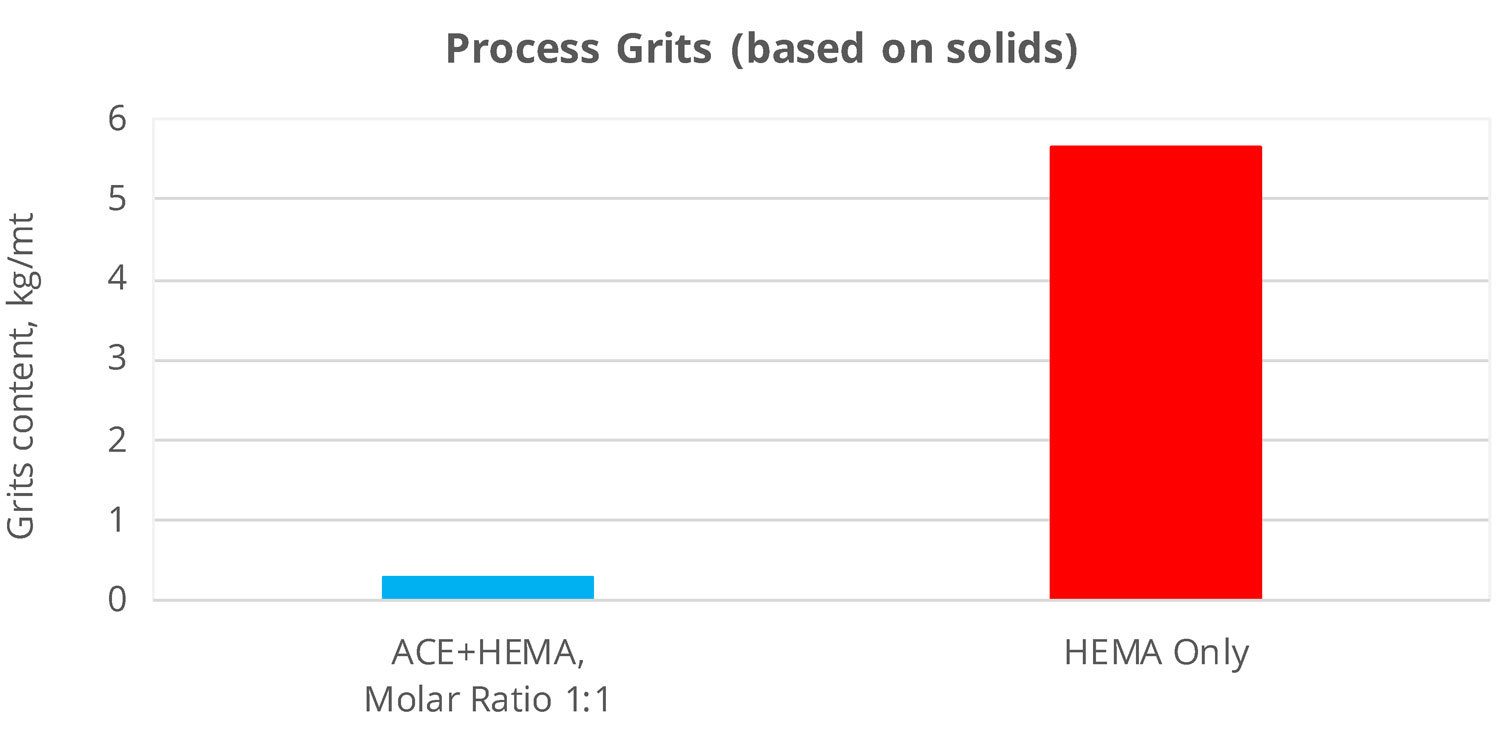
FIGURE 7 ǀ Reduced grit formation with AGN.
In addition to addressing process concerns, the use of AGN as a comonomer improves the emulsion polymer performance. As HEMA is very hydrophilic, it tends to stay on the surface of the polymer particles, either on the polymer backbone or in oligomer form. An emulsion that relies solely on HEMA as the source of OH functionality will thus have particles that will mostly crosslink on their surface. When acrylated glycidyl neodecanoate is used as a comonomer, OH groups are distributed inside the polymer particles, leading to a more homogenous distribution of reactive OH groups. Crosslinking occurs then both inside and outside the polymer particles, leading to a higher effective crosslink density.
Finally, one additional advantage of using acrylated glycidyl neodecanoate as a comonomer relates to compatibility with isocyanate crosslinkers. To properly cure, the emulsified resins must be compatible with the crosslinkers. Waterborne isocyanates are too viscous as supplied, so they are usually diluted with hydrophobic solvents (e.g. methoxy propyl acetate). The very non-polar neodecanoate groups in AGN increase the compatibility of emulsified polymers with non-polar (hydrophobic) solvents. This results in better mixing of the crosslinkers and polymers, which, in turn, leads to improved properties of the cured films.
Figure 8 compares the properties of clear films, one made with a regular HEMA-only emulsion and one with a 50/50 mole AGN/HEMA monomer blend. High OH content has been evaluated. In addition to process benefits, the use of AGN as comonomer brings clear benefits to coating performance. Hexion has developed a toolbox to tailor polymer composition to the required performance, including drying speed.
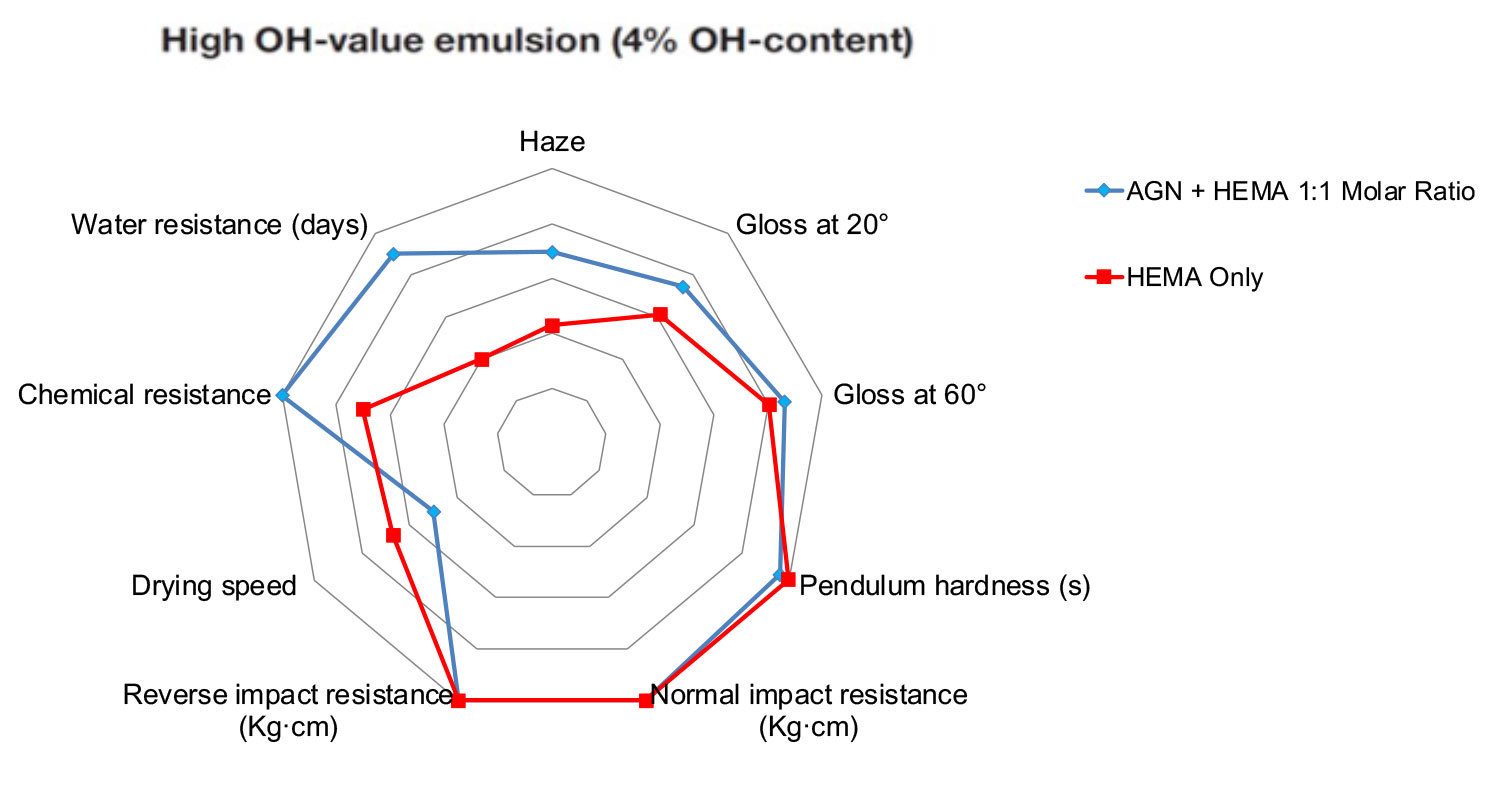
FIGURE 8 ǀ Comparison of cured film properties with and without AGN as comonomer (emulsion with 4% OH on solids).
Waterborne Hydroxy-Functional Emulsion Conclusions
The use of acrylated glycidyl neodecanoate as a comonomer for the synthesis of OH-functional emulsions bring significant process and performance benefits versus HEMA. Monomer pre-emulsions containing AGN will be more stable and the process will generate less grit, reducing polymer losses. In addition, the hydrophobic nature of AGN ensures that the OH groups in the final polymer are evenly distributed within the polymer particles, leading to better crosslinking, and therefore better solvent and water resistance. Furthermore, the hydrophobic nature of AGN improves miscibility of the isocyanates used for 2K WB PU coatings, resulting in better coating performance.
For more information, contact Nathalie Havaux at nathalie.havaux@hexion.com or visit www.hexion.com\cardura.
References
1 ® and ™ denote trademarks owned by or licensed to Hexion Specialty Chemicals Inc.
2 Steinbrecher, C.; Le Fevere de Ten Hove, C.; Heymans, D. “Hybridized Acrylic and Polyester Chemistries: High-Performance Polyols for Solventborne and Waterborne Polyurethane Topcoats”, at the conference “Automotive Coatings, on November 24th 2011, Berlin, Germany.
3 Petit, H.; Henry, N.; Krebs, A.; Uytterhoeven, G.; de Jong, F. Progress in Organic Coatings, 43 (2001) 41-49.
4 De Jong, F. et al. Adducts of Glycidylester of α,α-Branched Carboxylic Acids and Carboxylic Acids Process for Their Preparation, Resolution Research Nederland B.V. WO/2001/038287.
5 Dvornic, P.R.; Milhailo, J.S. The Viscosity Effect on Autoacceleration of the Rate of Free Radical Polymerization. Wiley InterScience. 6 December 2007.
6 Zhang, C.Y.; Zhu, Z.W.; Gong, S.L. Synthesis of Stable High Hydroxyl Content Self-Emulsifying Waterborne Polyacrylate Emulsion, Journal of Applied Polymer Science, 2017, DOI: 10.1002/APP44844.
7 Zhang, F.; Wang, Y.; Yuan, L.; Chai, C. Synthesis of Acrylic Emulsion Containing High Hydroxyl Content, Journal of Macromolecular Science, Part A, Volume 41, 2001, issue 1, 15-27.