Ready to proof -- Clare 8-12-22
KJ proofed on 8/15 and added one note for Clare below regarding Table 1
CB clean on my end
Ready for author
Credit: Andrey Semenov, Creatas Video+ / Getty Images Plus, via Getty Images
Best Practices for Selecting Rheological Additives in Latex Paints
and the Interpretation of Their Effectiveness
By Artur Palasz, Ph.D., Spektrochem, Poland
Rheology is a lore about the flow and deformation of substances. Regarding latex paints, this is the science of flowing behavior during storage and handling, both during and after application. Rheology in its scope of research covers everything related to the flow and properties of paints during mixing, pumping, application (brush, roller, spray, etc.), or mixing after adding colorants or diluting with water. It is an extensive range of knowledge concerning not only rheological additives (thickeners), but their interactions with other raw materials in the formulation.
Designing latex paint formulations is a task that is often difficult at the stage of selecting thickeners responsible for the entire range of rheological efficiency. The mere achievement of a resting viscosity, the so-called low-shear viscosity, is not difficult and usually comes down to a single thickener. But the market expects latex paint to have a number of properties, and rheological additives must satisfy these expectations, including easy application with a brush, roller, or spray (especially by people who are not professional painters). Additionally, the additives must ensure that there is no syneresis, no spattering, good leveling, etc.
This article has been prepared especially for novices in the field of latex paint formulation, but it will also help experienced formulators and R&D departments by providing an additional look at interpreting case study results, reading starter formulas and the possibilities offered by appropriately prepared extensive guide formulations.
In the article, I focus on the transfer of knowledge on the practical assessment of the effectiveness of rheological additives in latex paints, with an emphasis on the importance of properly prepared guide formulations. I have overlooked many aspects related to the basics of rheology and its definitions, as this can be found in many excellent publications and training materials on the rheology of latex paints.
Rheology Modifiers
Rheology modifiers in architectural latex paints are mandatory additives in every formulation. Their effective operation allows for paint stability during storage, packaging, mixing, pumping and application by various techniques (brush, roller or spray application). These thickeners also help to prevent paint from dripping once applied, as well as paint spattering. When choosing thickeners for the formulation of latex paints, one should first consider what the paint is intended for, what conditions it will be subjected to and what modifications are needed to enable these conditions, but also to simplify it as much as possible. Everyone has used different paints at least once in their lifetime and knows that they differ in the ease of application, for example in terms of brush drag. The ease of application and the quality of the coating appearance depend on the rheology modifiers (no sagging, good leveling).
Shear Forces
Liquid latex paints are subjected to various types of factors that set them in motion, such as mixing or spreading onto a surface. Each type of movement is described by phenomena described as shear forces. When we act on the paint, causing it to flow, shear is applied at the interface between the paint particles and the element against which it moves (stirrer, roller, substrate, etc.). Each type of interaction has a different force, hence we divide shear into low shear, mid shear, and high shear.
Figure 1 shows the flow behavior that can usually be achieved with various latex paint thickeners. Of course, these are not all the rheological behavior of liquids, however, with regard to latex paints, there are three: pseudoplasticity, thixotropy, and Newtonian flow. Each of these flow patterns is measured by the variability of the relationship between viscosity and shear rate. Latex paints show a pseudoplastic character with varying degrees of severity. Some are less and others more pseudoplastic, which depends on the formulation, pigment volume concentration (PVC) and the thickeners used. The pseudoplastic nature causes the viscosity to decrease with increasing shear rate. The extent to which the viscosity drops, and what the decrease looks like, is characterized by full-scale shear rate measurement methods. There is no single pseudoplastic flow, and the viscosity decrease in the high-shear-force area cannot be interpreted in any way by the initial viscosity decrease as the shear force increases in the low-shear-force area.
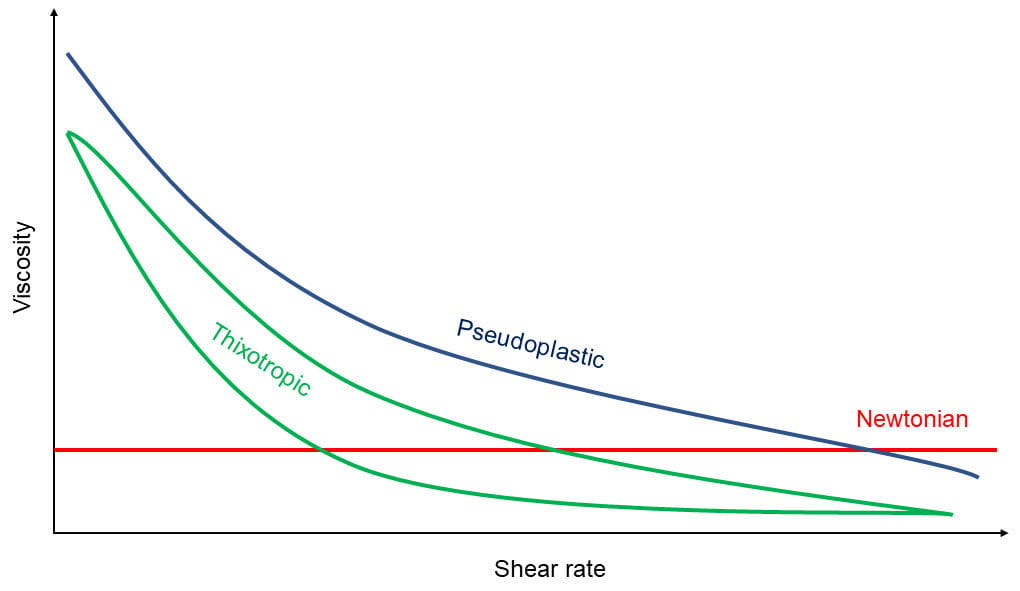
FIGURE 1 ǀ Rheological flow behavior.
Latex paints are basically all of the shear thinning types that describe pseudoplastic flow. The faster we start mixing the paint, the more it dilutes, that is, the viscosity drops. When the agitation subsides, the return to static viscosity occurs immediately. The decrease of this viscosity occurs in various ways, however, it is usually a curve which, when it reaches its minimum value, does not decrease any further. This decrease depends on how pseudoplastic the flow character imparted to the paint by the thickener is. The decrease in viscosity occurs with the increase of the shear rate, which is expressed in s-1 and denotes the ratio of the speed of the moving surfaces to the distance between them and between which the paint is located. This is how the viscosity is measured according to the physical definition of viscosity. Figure 2 shows a pictorial decrease in viscosity during pseudoplastic flow, with the marking of areas with different shear forces through which this decrease runs.
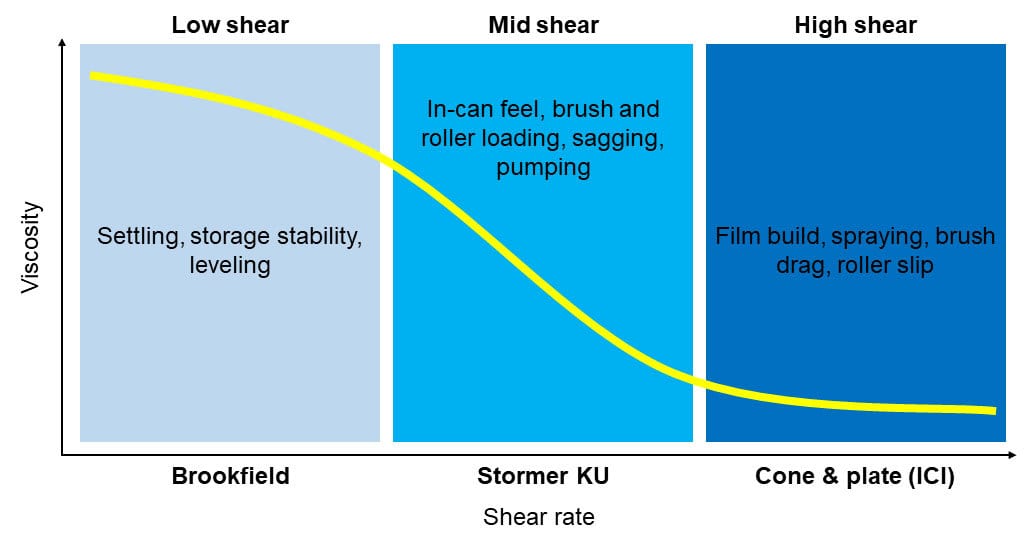
FIGURE 2 ǀ Areas of different shear forces and defining the viscosity in each of them.
Each of the shear force areas is responsible for different paint properties that must be ensured at an optimal level, and this is the role of the formulator. Therefore, providing data on thickeners in the form of guide formulations, and above all the characteristics of shear forces, is very important. On the basis of case studies, compatibility tests and ladder studies, the optimal scope of thickeners is determined. Sometimes they are designed to be viscous in one area of shear, and sometimes they are more optimal in one area and slightly less effective in another.
Low-Shear Thickeners
Paint at rest in a can is not free from the forces affecting it. The force of gravity has the greatest effect, and the pigment and filler particles have to resist in order not to fall to the bottom (preventing settling). Moreover, the interaction between the binder, pigment and filler, and surfactant particles leads to the squeezing of water onto the paint surface, leading to syneresis. This also must be prevented by thickeners. For this purpose, thickeners that are effective in the low-shear-force area (10-6 to 10-4 s-1) are used.
However, when the paint is still wet on the surface, leveling processes take place, which are supported by Newtonian thickeners and surface tension. In this case, the shear forces ranges from 10-2 to 10-1 s-1.
The thickeners that are needed to achieve the desired viscosity and rheological behavior are usually tested by methods that can evaluate the viscosity, e.g. Brookfield apparent viscosity, as well as leveling by standardized test blade according to the procedures described in the following section. It is very important that in the technical cards, and more precisely the recommendation cards for the use of a rheological additive, provide testing data showing whether a given thickener is dedicated to low-shear forces and how effectively it works in this area, e.g. on a scale from 0 to 5. This helps facilitate the choice for formulators, especially in the case of new thickeners not yet known in the paint industry such as thickeners made of renewable raw materials. In this area, the TVS-thickeners (tint viscosity stabilizing thickeners) must also be effective to buffer the viscosity after tinting with the addition of various pigment concentrates.
This group of thickeners for improving storage stability usually includes cellulose thickeners (cellulose ethers, e.g. HEC), mineral thickeners (e.g. smectite clay, attapulgite), alkali-swellable acrylic thickeners (HASE, ASE), as well as many HEUR polyurethane thickeners. To improve leveling, which is also in the area of low shear rates, many dedicated thickeners are used to give the paint a Newtonian profile as additional supporting thickeners. They are usually also HEUR thickeners.
Mid-Shear Thickeners
The viscosity at mid shear force is responsible for loading the paint onto a brush or roller, the feeling of viscosity in a can, sagging from vertical surfaces as well as pouring and pumping. Thickeners that work effectively in this area must have an impact on the above parameters, and their measurement is carried out using a Stormer viscometer or a multi-notched applicator for anti-sag index measurements. Mid-shear thickeners usually have to impart viscosity in the range of 90-110 KU.
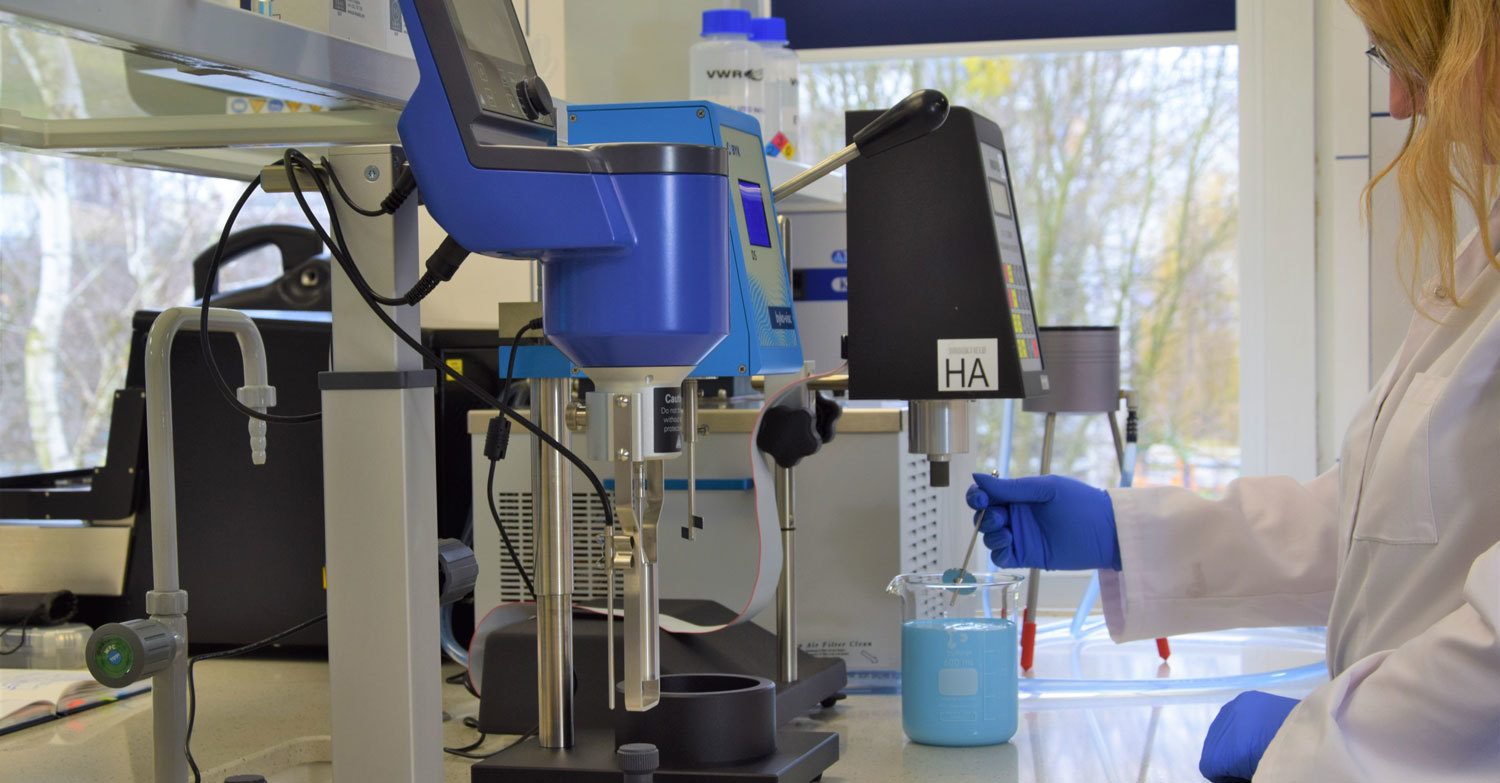
FIGURE 3 ǀ Laboratory stand for low- and mid-shear viscosity measurements at the Spektrochem raw materials lab.
Once the paint is applied to the substrate, it is subjected to the forces of gravity immediately after painting, which causes the paint to run down when the vertical surface has been painted. Sagging also occurs at low shear forces of 10-2 to 101 s-1.
Effective thickeners in this area are also cellulose derivatives, alkali-swellable acrylic modifiers, polyurethane, or mineral thickeners, however, their effectiveness is slightly further than low-shear thickeners. Therefore, it is very important to test them properly and also to classify how much this efficiency affects the viscosity in the mid-shear range.
High-Shear Thickeners
Thickening agents operating at the highest shear rates are the so-called ICI viscosity builders. Brush painting takes place at shear rates from 102 to 104 s-1, and spraying from 103 to 106 s-1. Effective action in this area is giving workability in order to ensure adequate roller slippage or optimization of drag when painting with a brush. High-shear thickeners are also responsible for building a film, so they are a type of rheological modifier that have a particularly strong influence on the application properties of latex paints.
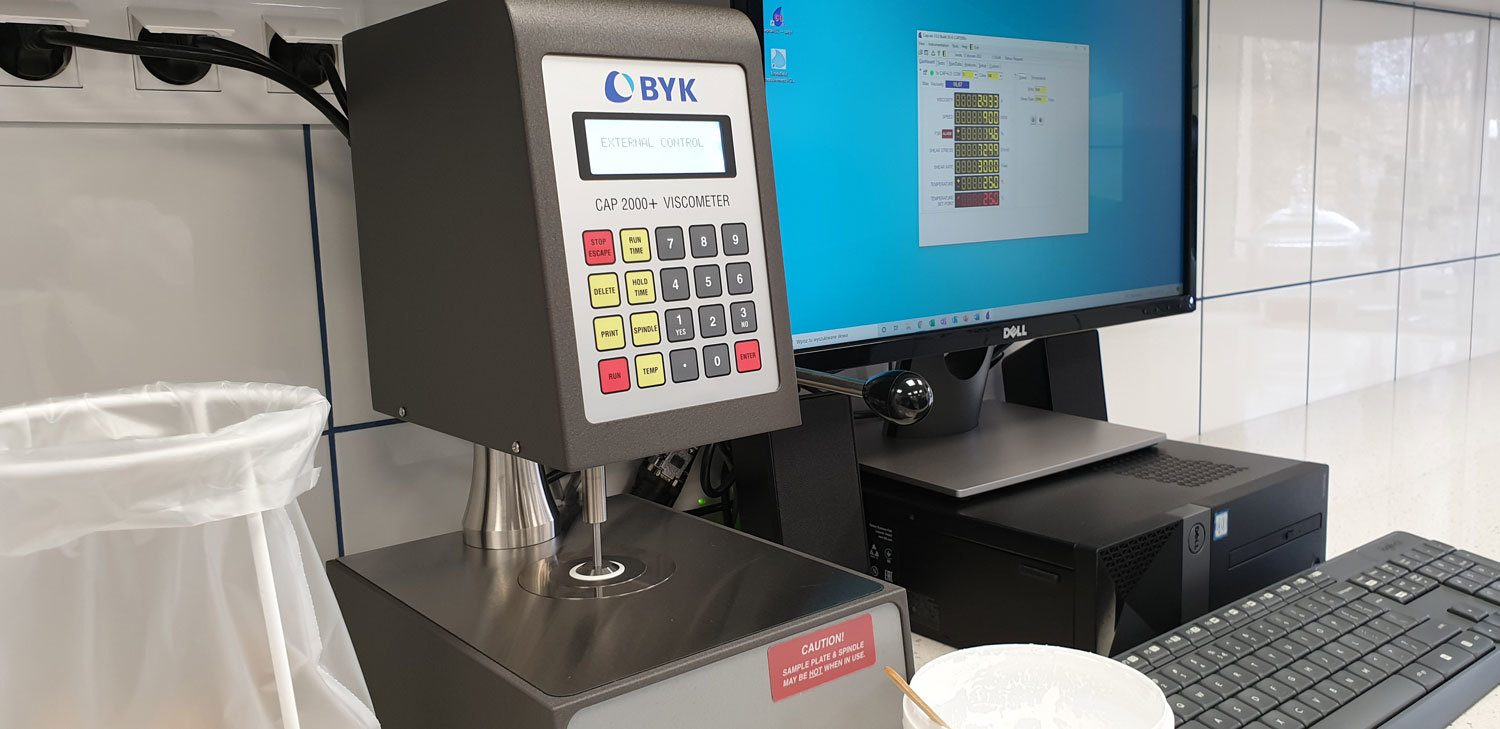
FIGURE 4 ǀ ICI viscometer BYK CAP2000+ (cone and plate) at the Spektrochem laboratory.
To measure viscosity at high-shear rates, cone and plate viscometers called ICI viscometers are used, and also often rheometers with coaxial cylinders. They are usually efficient polyurethane thickeners, but also acrylic thickeners. The hydrophobically modified HEC is also effective in the high-shear-force area, which helps reduce spattering during roller application.
Starting-Point Formulations
Starting-point formulations play a very important role in conveying knowledge on the use of specific types of rheological additives. However, not every starter recipe provides the appropriate knowledge, because in many of them there is simply a certain dose of thickener, which is no way documented in the test results as to why it was set at a given level, and often why another thickener is chosen to accompany it. Manufacturers of thickeners who want to stay ahead of their competition develop technical materials on the basis of various case studies, ladder studies (showing the effect of different doses), and guide formulations, showing how a given thickener works. Extensive case studies show how a specific type of thickener changes the viscosity of the system depending on the change in polymer dispersion, pH, surfactants, or coalescent, when the thickener is sensitive to environmental changes and thus influences the viscosity in the area of different shear forces.
It is very important to indicate on the basis of research when it is the best time to add a given thickener during the production of latex paints. There are reasons for adding some thickeners at the grinding stage, and others at the let-down stage, but here also it should be indicated whether the optimal efficiency is obtained when adding at the very end or at an intermediate stage. For many thickeners, especially polyurethane thickeners, but also often mineral ones, it turns out that better spreading efficiency, compatibility and rheological properties are obtained when the thickener is added in the form of a premix (polyurethane thickeners) or a suspension (mineral thickeners). Then, when developing the starting recipe, it is investigated how best to obtain a thickener premix, whether in water or in coalescents or other solvents of different polarity, and in the case of mineral thickeners, the optimal level of hydration, e.g. of smectite layers, is determined by different shear forces and their duration of action, type the water used to prepare the suspension (water hardness), etc.
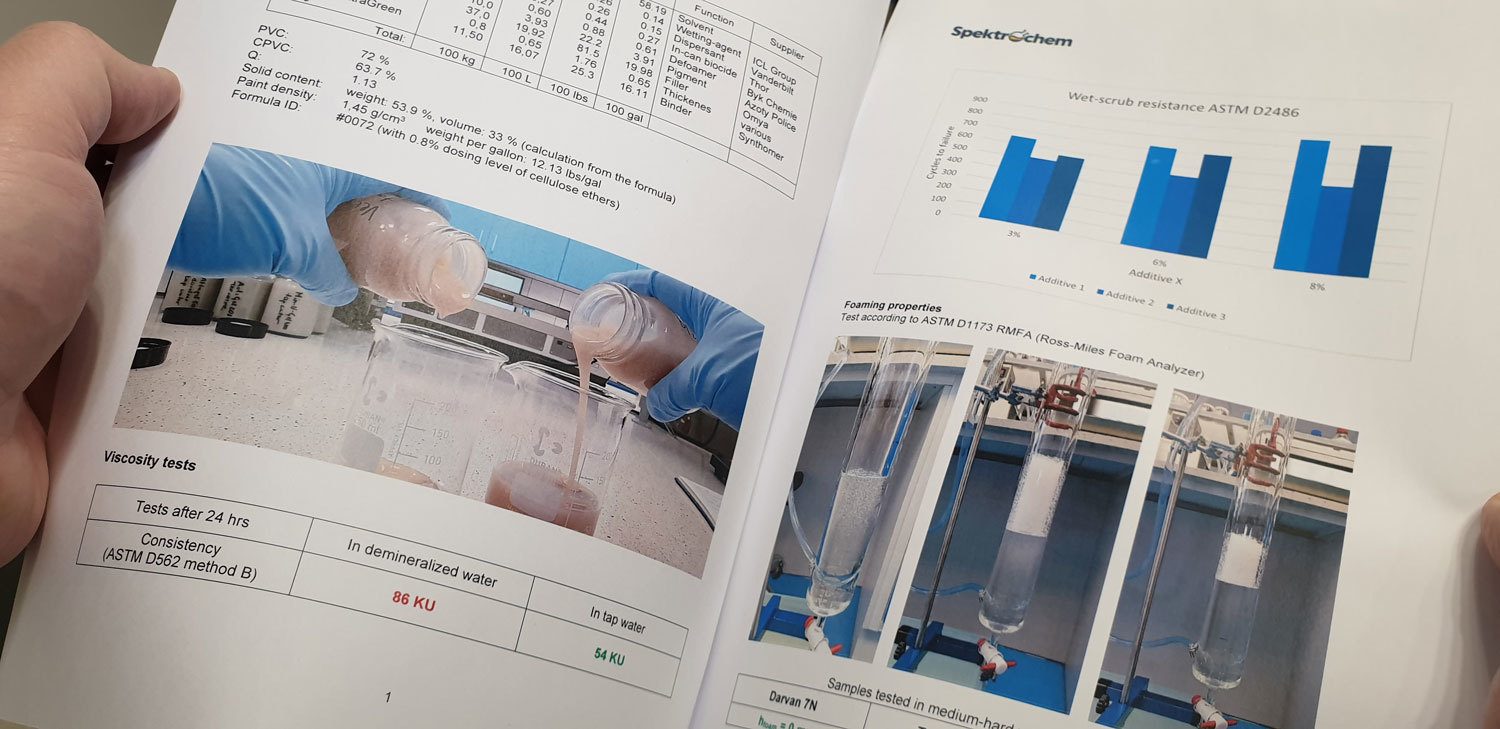
FIGURE 5 ǀ An example of a guide paper with case study results described in detail, developed in the Spektrochem lab.
Properly tailored starting-point formulations are also those that show the action of thickeners in individual areas of shear forces, but also in a wide range of PVC. The thickeners in 20% PVC and 80% PVC act differently, which depends on the amount of latex binder in the recipe and the ratio of the thickener's active substances to the film-forming substance.
Another important element in the education of thickeners are various publications, courses, and webinars organized by thickener producers and independent consultants. Technical materials in the form of case studies and guide formulations developed by laboratories such as ours are in turn helpful for producers of raw materials, in this case thickeners, in developing technical materials to support the marketing and sale of their products. Such materials not only help in making a decision about taking samples for testing, but significantly accelerate the testing of the thickener in a new or existing formulation at the paint manufacturer, because they show the way the thickener has been determined in terms of dose, compatibility, and effectiveness with other thickeners.
Where to Start?
The task of a paint manufacturer’s R&D department is to combine thickeners in such a way as to obtain optimal working properties with a specific painting technique ¾ no sagging, good leveling, no spattering when painting with a roller, and many other properties. Therefore, it is important to use the optimal doses of rheological additives, which, depending on the type, are not the cheapest. Therefore, it is best to start formulating recipes while getting acquainted with the extensive case studies and guide formulations provided by raw material producers (in this case producers of thickeners) in order to combine knowledge from various technical recommendations into one formulation.
The first step that we usually recommend is to work with guide formulations based on PVC similar to the one you want to obtain (in the case of new formulations) or to the one that is currently present (in the case of modifying existing formulations). The influence of thickeners on the behavior in various ranges of PVC is very significant, so it is good to build your own samples based on case studies conducted by someone in a similar PVC range, gloss, etc. It is also important to use a similar type of latex binder because it is difficult to translate the thickener's behavior from a formulation based on a vinyl acetate-acrylic copolymer dispersion into the formulation with a pure acrylic copolymer dispersion. Therefore, it is very important to properly build recommendations by raw materials producers that can fit into many typical binders on a given market.
The second step is to analyze at what stage of the production process to add a given thickener and what the indications are for combining the obtained thickener sample with the others to ensure optimal efficiency. If we are dealing with cellulose ether, it should be characterized in guide formulations whether it can be added at the grinding stage or in the form of a solution at the end. Here, of course, it is important at what stage to add at a certain level of PVC, as it is of particular importance in the case of cellulose ethers. Of further importance is whether it requires an additional alkalizing agent when used in solution, and what its swelling looks like after alkalinization (Figure 6). The next step is to analyze what additional rheology modifying agents can be used to improve the effectiveness of the ICI high-shear forces, as well as whether Newtonian additives have been tested to ensure improved flow and to what extent to use them to obtain the desired leveling without sagging. Finally, it should also be analyzed to what extent TVS occurs, i.e. how the rheological additive buffers the addition of various pigment pastes.
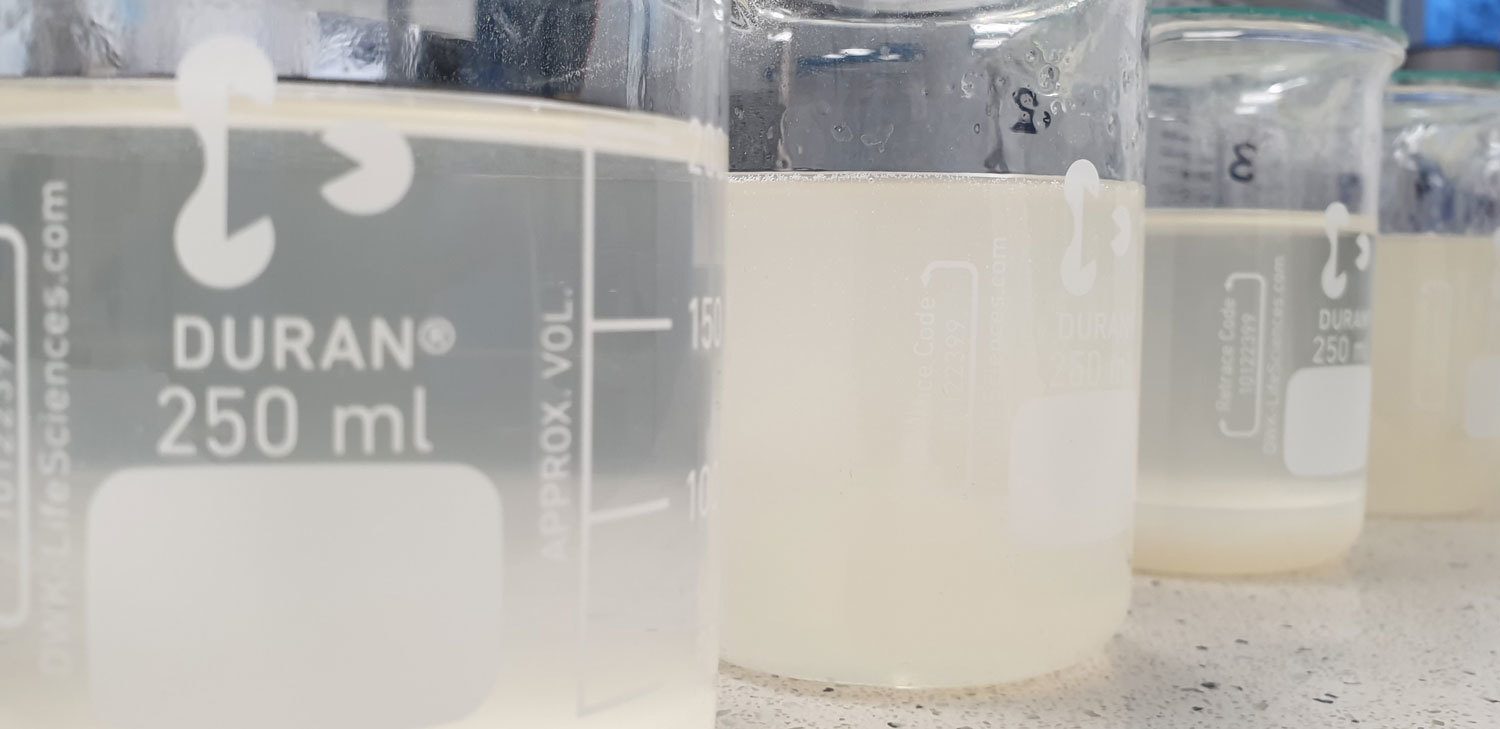
FIGURE 6 ǀ Cellulose ether solutions in beakers swollen to varying degrees due to correct and incorrect alkalization (at the stage of establishing starter formulations in the Spektrochem laboratory).
It should be remembered that each thickener affects the rheological behavior by diffusion of individual shear rate areas, therefore its behavior should be taken into account as a whole of the parameters obtained, not only in terms of viscosity measured at a specific shear rate. This especially applies to acrylic and polyurethane thickeners, the effectiveness of which also boils down to the impact on open time, color compatibility, etc.
Test Methods for Evaluating the Effectiveness of Thickeners
In order to properly assess the behavior of rheological additives after the preparation of formulations and laboratory samples, a series of determinations should be made using test methods. We recommend using ASTM International standards to provide the most reliable test results that can be compared and discussed easily with raw material suppliers. In addition to standard assessment methods performed by R&D and application laboratories, such as brush drag in accordance with ASTM D4958, and paint roller in accordance with ASTM D7073, standardized methods of measuring viscosity at various shear rates and determination of other rheological properties are used. Below I discuss an example of the most commonly used methods, along with some tips and insights from us as a laboratory using these methods on a daily basis.
Viscosity
The basic definition of low-shear viscosity is the measurement of apparent viscosity with a Brookfield viscometer in accordance with ASTM D2196 Method A. Disc spindle viscometers (the most common) and L-range viscometers with various cylinder sizes are used. When determining the viscosity in accordance with ASTM D2196 method A, the standard indicates the need to bring the paint to an appropriate reproducible thinning by mixing the sample for 10 minutes and standing for 60 to 65 minutes, and then taking the measurement. This practice is always advisable, as measurements are often made on samples prepared at different times, and as you know, this also affects the viscosity.
The ASTM D2196 method also indicates two additional procedures, B and C, which consist of determining the shear thinning index and thixotropy index. These are methods also used to characterize latex paints, and consist of a controlled change of the measurement speed in the low-shear range — for example in the range of 2-20 rpm or 5-50 rpm (method B) — and then intensive dilution and measurement of apparent viscosity after an abbreviated rest (method C) and determination of the thixotropy index. This is not a very popular method of determining the thixotropy index as it is based on measurements only in low-shear areas.
Of course, it should be remembered that each viscosity measurement should be performed on a sample that has been thermostated to a constant temperature, usually 25 °C (77 °F), as the influence of temperature is significant on the obtained viscosity results.
Mid-shear viscosity measurements are made with a Stormer viscometer in accordance with ASTM D562 method A, analog viscometer, and method B, digital viscometer. Viscosity determination is done in KU (Krebs Units) and it is one of the most popular methods of viscosity determination, also for quality control. The Stormer viscometer performs the measurement at a constant rotational speed of 200 rpm, and the mixing element is a paddle. Digital viscometers work by measuring the viscosity in KU units as well as in cP and grams, which is the result corresponding to the load that should be assumed to move the paddle and measure the viscosity in analog models. Figure 7 shows the Stormer viscometer while measuring the KU-viscosity of the latex paint.
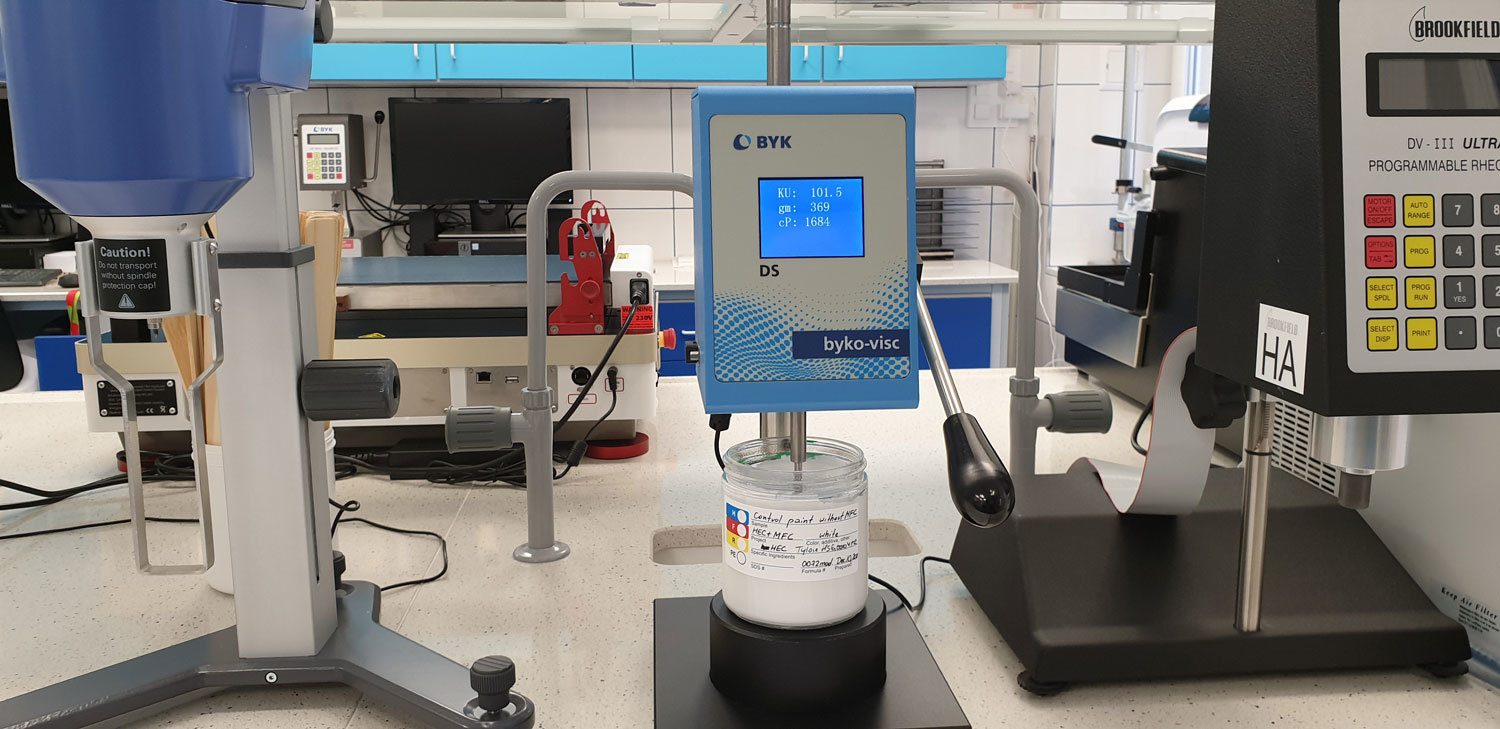
FIGURE 7 ǀ Determination of KU-viscosity with a Stormer viscometer (on the right a Brookfield viscometer for ranges H and on the left a viscometer for ranges L) at Spektrochem lab.
For measurements at high-shear rates, e.g. 12,000 s-1, cone and plate viscometers (ICI viscometers) are used. These types of viscometers work together with the software to determine viscosity over the full range of shear rates. The measurement is also carried out at a constant temperature by a thermostatic block under the plate, and the viscosity determination is carried out on a very small sample, usually from about 70 µL. Viscosity measurement with ICI viscometers (Figure 4) allows the interpretation of paint application behavior by brush, roller, and spraying.
Storage Stability
Determining the viscosity stability in terms of viscosity drift, but also syneresis or settling, is a procedure that requires the observation of paint samples over time. To accelerate the changes that may occur in samples with different thickeners, an accelerated storage stability test according to ASTM D1849 is performed. It involves exposing the sample to an elevated temperature in a laboratory oven at 52 °C (125 °F) for 1 month. The test is normally carried out in a 1-pint metal can, but for the purposes of assessing the effectiveness of rheological additives, this test is usually modified. It comes down to taking a test often over a period of 14 days, because usually after this time, at an elevated temperature, a tendency for changes in viscosity or the occurrence of syneresis can be found, and the packaging in which the test is carried out is modified, usually by replacing the metal can with a sealed glass jar to better monitor the occurrence of syneresis. After the test is completed, viscosity measurements are made using the methods described above and additional supplementary tests according to the requirements and internal standards.
Spattering Resistance
Spattering is a phenomenon that is particularly avoided when designing paints for DIY applications. We do not want a customer who is painting without special skills and often without proper protection of furniture or floors to have paint spots everywhere when painting with a roller. A supplementary test to evaluate the viscosity behavior in the ICI viscosity range is the spattering test according to ASTM D4707. This test is performed with a notched-spool roller to ensure repeatability of the test, as using paint rollers would add many variables to the test. In spattering resistance, 20 movements of the roller are made at a frequency determined by the metronome. Drops and splashes of paint scattered by the roller are caught on the paper under the coating. According to the reference photos, the ASTM D4707 standard gives the degree of spattering resistance on a scale of 0 to 10, where 10 is no spattering and 0 is the worst result (Figure 8).
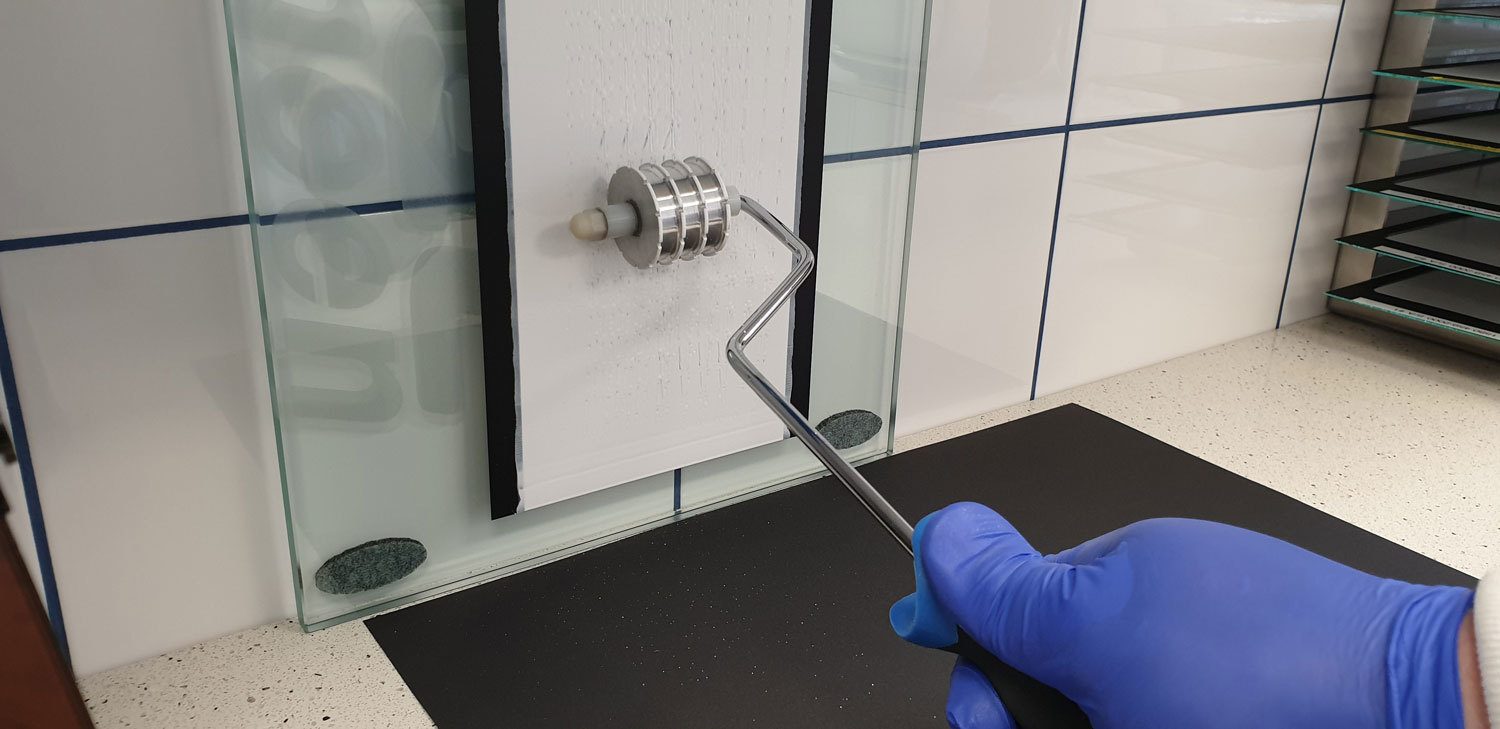
FIGURE 8 ǀ Running a notched-spool roller over the coating during spattering resistance test.
Leveling
The leveling test is performed using the Leneta Leveling Test Blade, carried at high speed (0.6 m/s) on the sealed chart and distributing the test paint using a spiral blade with defined groove dimensions. Before drawdown, the paint is applied in front of the blade with a syringe and a needle, which causes pre-shearing to simulate applications at high shear rates, such as when painting with a brush or roller. After drying, the coatings are graded according to the leveling standards and graded on a scale from 0 to 10, with 10 being the best leveling and 0 being the worst.
Anti-Sagging
The sagging test is performed according to ASTM D4400 using the notched applicator in the range of 4-24 mils (100-600 µm) for architectural paints. The applicator is used to obtain 11 stripes of paint with graded layer thickness, which are placed vertically after application to induce sagging. By identifying the applicator gap that has not sagged and interpreting the behavior of the next strip, the Anti-Sag Index is determined in accordance with ASTM D4400. The paint is also pre-sheared with a syringe and needle before the drawdown, and the drawdown is carried out with an automatic film applicator at a speed of 150 mm/s.
Case Studies
The article gives an example of the process of interpreting the results of case studies for the HEUR thickener used in the formulation of latex paint. The assumption of this case study was to prepare a formulation with three thickeners:
- Hydroxyethylcellulose (HEC) grade: 30,000 mPas, in 2% solution dosage 14.4 lb/100 gal;
- HEUR thickener No. 1: KU builder (mid shear), active content 25%, used in the formulation as 1:1 solution in water, dosage level 0.9 lb/100 gal;
- Tested HEUR thickener No. 2: active content 19%, dosage levels: 0.3% active and 0.6% active in the total formulation.
The use of HEC and KU builder (HEUR thickener No. 1) in the formulation indicates that these are thickeners used to impart viscosity in the low- and mid-shear area. Tested thickener HEUR No. 2 will therefore be tested for its effect on changes in viscosity behavior over the full range of shear rates.
In the case studies discussed here, the HEUR thickener is fully soluble in water and does not require the use of additional solvents. For HEUR thickeners it is important to carefully use the required additional solvents, which may increase the VOC content of the formulation.
Formulation
We will use the starting formulation in Table 1 to discuss the case study. A simple formulation was intentionally used to simplify the presentation of the interactions between the raw materials.
TABLE 1 ǀ Formulation.
Determination of the Viscosity of Paints
Observation of changes in viscosity from the moment the paints are prepared for the first few days provides a lot of information about the behavior and interaction of the thickener with other raw materials. Table 2 shows the changes in viscosity over the full range of shear rates.
TABLE 2 ǀ Viscosity test results.
Viscosity changes in the low-shear area (Brookfield) show that the samples will not show a significant change in viscosity among themselves despite a double change in the dosing of HEUR No. 2 (the difference in viscosity just after preparation is only 2%). On the other hand, the apparent viscosity (Brookfield) has stabilized to a slightly lower level after 7 days, however the difference in viscosity between the samples is still low (ca. 13%). This means that HEUR No. 2 is not an effective viscosity modifier in the low-shear region. Likewise, with the mid-shear area, where differences between samples in the dosing range 0.3% and 0.6% active are to be omitted. HEUR No. 2 is also ineffective in the mid-shear area, despite doubling the dosage.
Viscosity differences are visible in the high-shear area (ICI viscosity) and the measurements with a CAP 2000+ cone and plate viscometer. The viscosity, both immediately after preparation and after 7 days, shows differences resulting from changes in the dose of active substances of thickener No. 2 in formulation. This difference ranges from 61% (initial) to 69% (7-day viscosity) and shows that we are clearly dealing with a high-shear-force thickener. Viscosity close to 3 P (poise) indicates that the thickener at a dose of 0.6% of active parts effectively supports film building. These test results show that the thickener No. 2 can provide an additional rheology modifier to the viscosity to be easily applied through a variety of techniques (brush, roller, or spray).
Storage Stability
The results of the stability test at elevated temperature in terms of changes in viscosity and the appearance of syneresis provides information about the effectiveness of the thickener over an extended period of time when storing paints in the package. Figure 9 shows samples of the tested paints (on the left with a dose of 0.6% active and on the right with a dose of 0.3% active). As you can see, the tested thickener also influences the effectiveness of syneresis prevention during the monthly test at 125 °F. Although it did not affect viscosity changes in the low-shear-force area, its effectiveness can additionally be used to minimize syneresis.
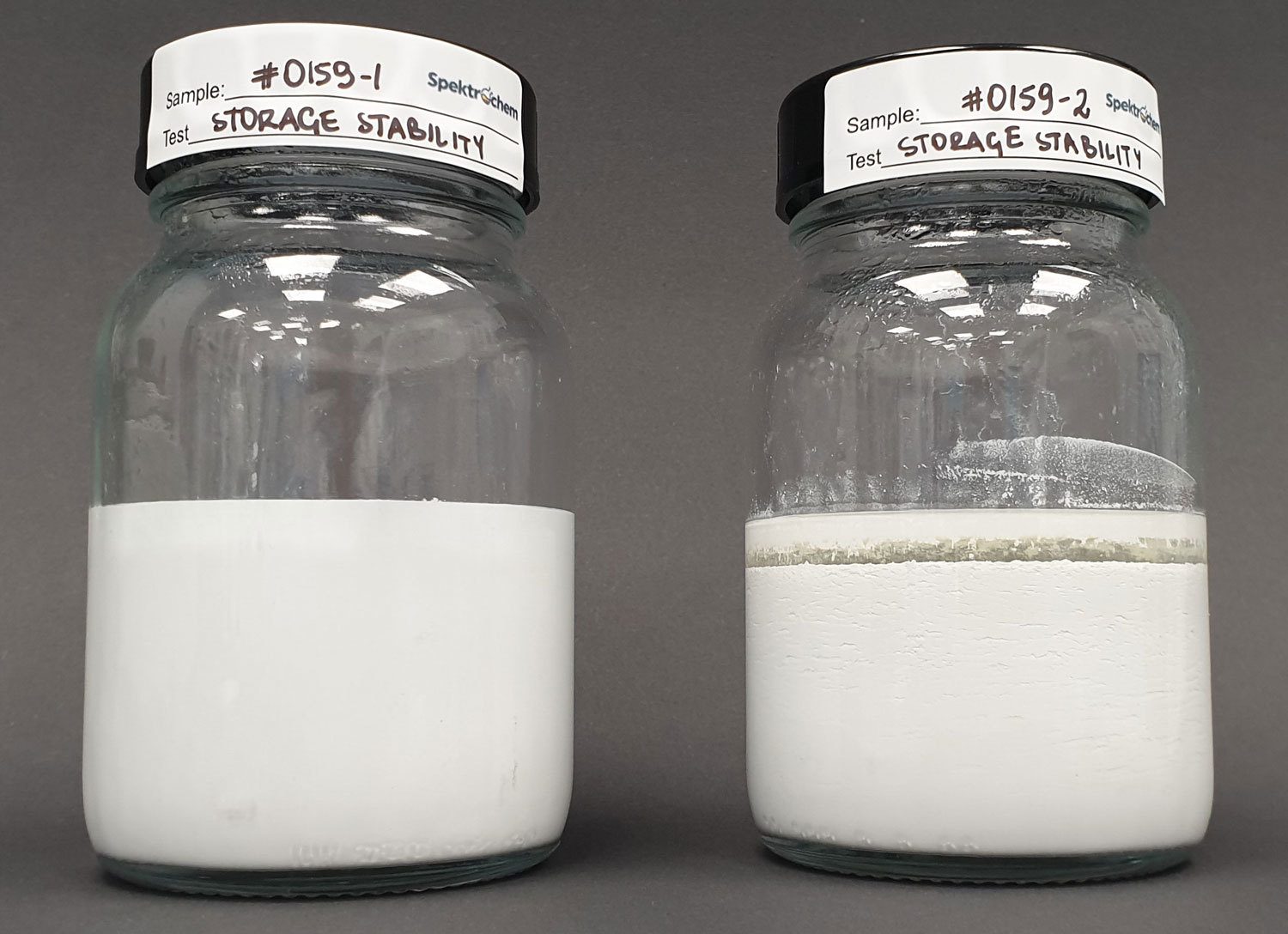
FIGURE 9 ǀ Syneresis test result after storage stability test.
Spattering Resistance
The spattering test by the standardized test ASTM D4707 (by notched spool roller) shows results that complement the determination for the high-shear area (ICI viscosity). It turns out that HEUR No. 2 minimizes the tendency to spattering better with the 0.3% dose than when increased to 0.6%. Although the rating differs only by one (Figure 10), the thickener, despite the good results of the ICI viscosity test, does not help reduce spattering with increasing the dose. This means that when formulating a paint formula for roller application, one would need to think about an additional material that reduces spattering (e.g. hydrophobically modified HEC or other HEUR thickeners).
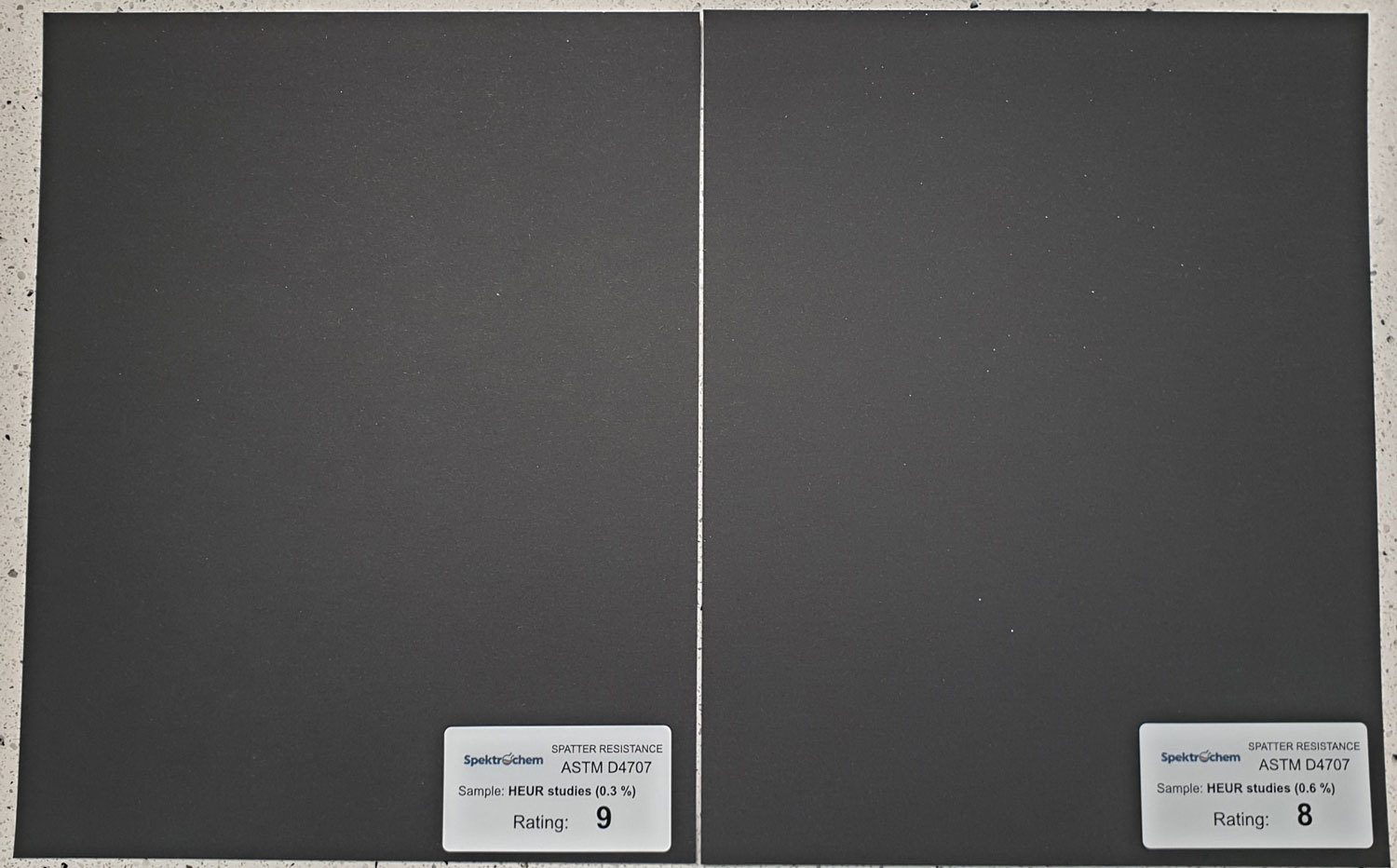
FIGURE 10 ǀ Spattering test results.
Tintability
After adding pigments in the form of pigment concentrates, the paints must retain their properties in the form of tint viscosity stability. One measure of TVS is to maintain an Anti-Sag Index. The Anti-Sag Index discussed here was carried out in accordance with ASTM D4400 of the multi-notch applicator in the range of 4-24 mils on tinted by PB 15:3 colorant (8.7 fl. oz per gallon)
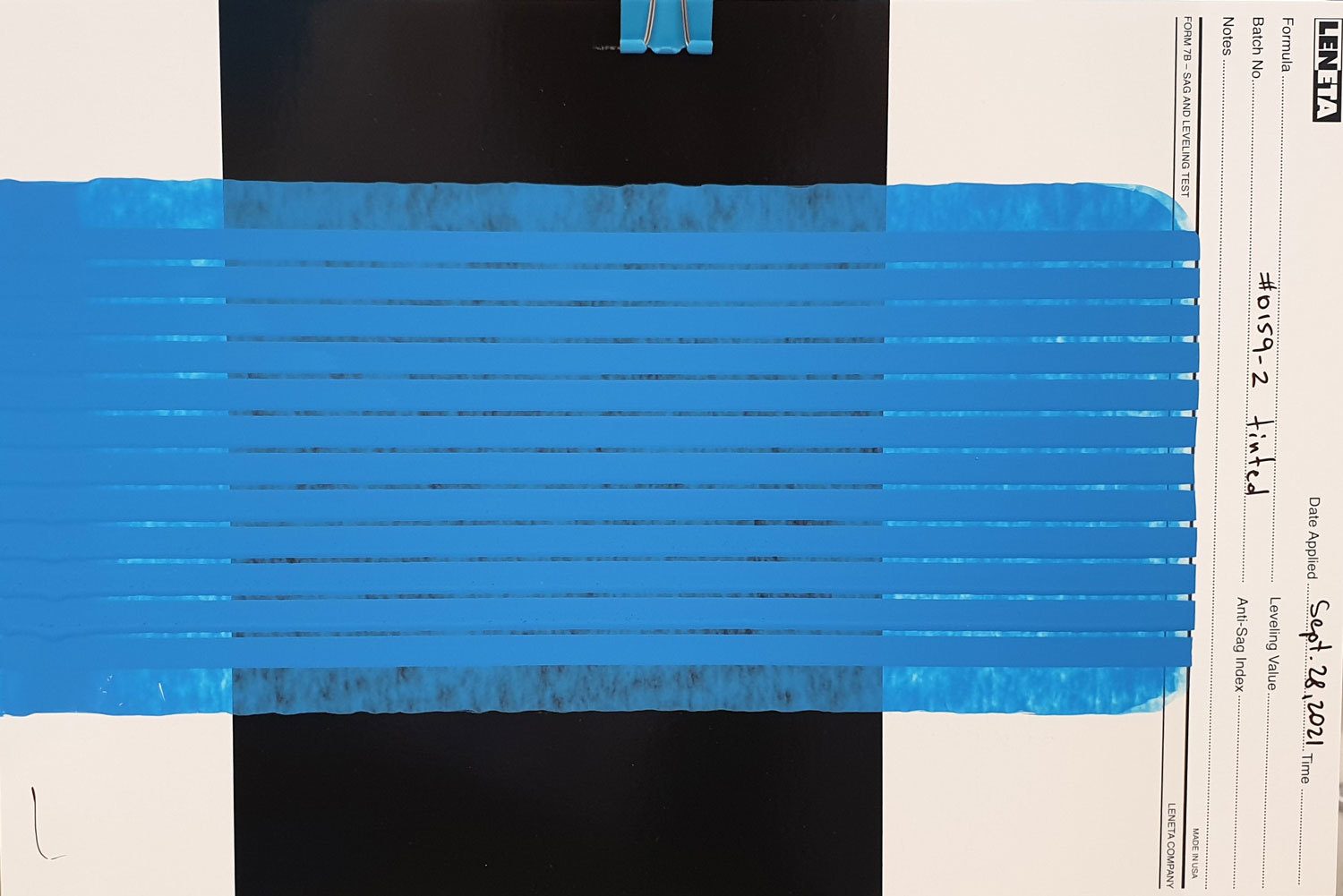
FIGURE 11 ǀ Sagging test results for sample with 0.3% active content of thickener.
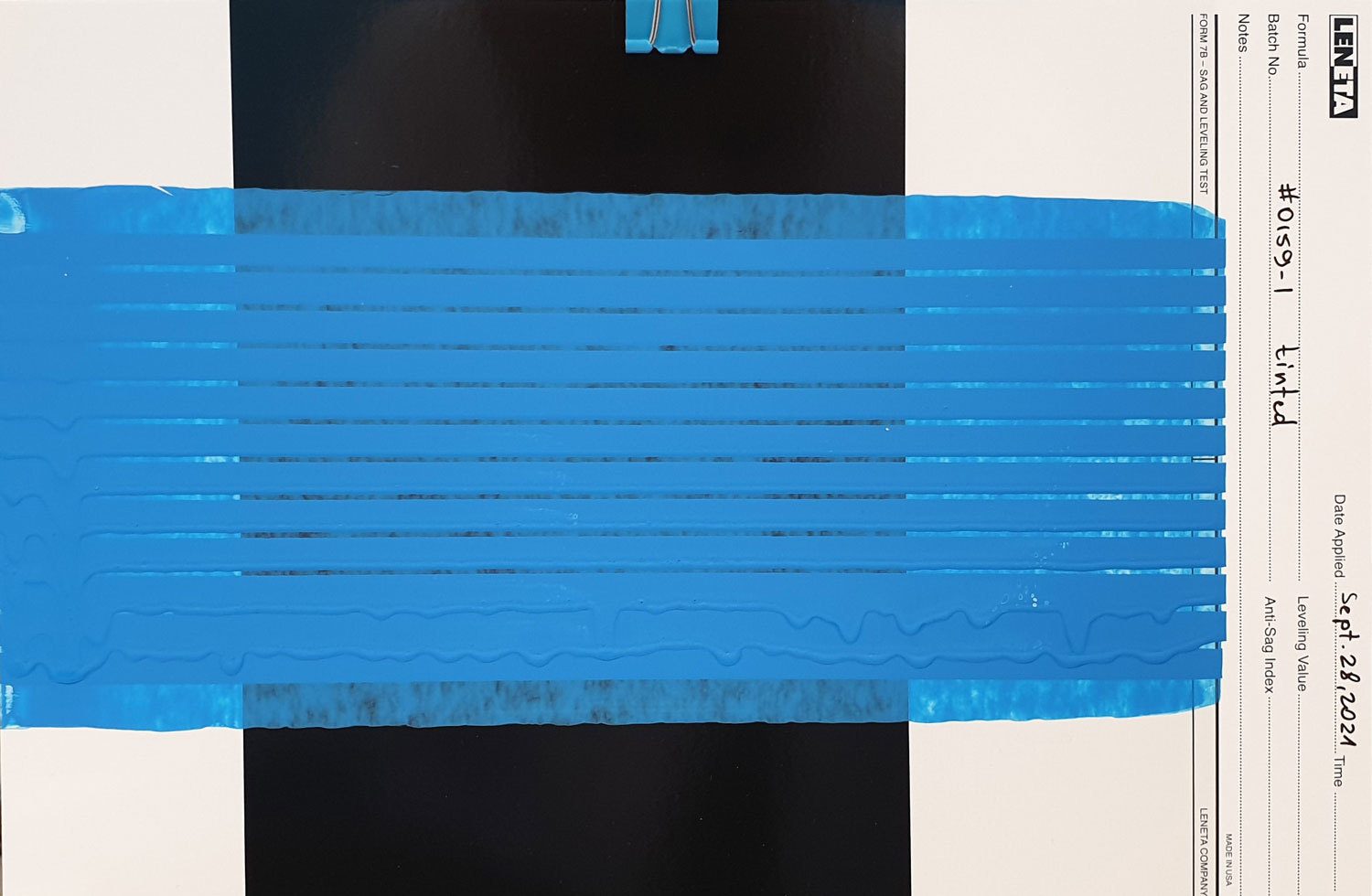
FIGURE 12 ǀ Sagging test results for sample with 0.6% active content of thickener.
The Anti-Sag Index shown in Figures 11 and 12 is 24 mils (no sagging at all) for the sample with HEUR No. 2 at a dose of 0.3% (Figure 11) and 22 mils for a sample with 0.6% active content (Figure 12). The results show that the thickener, despite increasing the dose of active substances, does not have good TVS in terms of anti-sagging retention. Of course, the difference is visible only in the range of 22-24 mils, however, this result should inform the formulator of a suspicion of not very good retention on the colorant used, which may also result in similar results for other colorants and their blends.
The last feature discussed for the colorant tested in this article is color retention. As you know, HEUR thickeners can influence color development, hence it was also checked here whether the dose of 0.3% and 0.6% active effect the color drift. Figure 13 shows the drawdown charts of both paints colored as above with blue pigment concentrate. Visually, there is no discernible color drift, which is also confirmed by spectrophotometric measurements. The hue difference is DE*ab = 0.52.
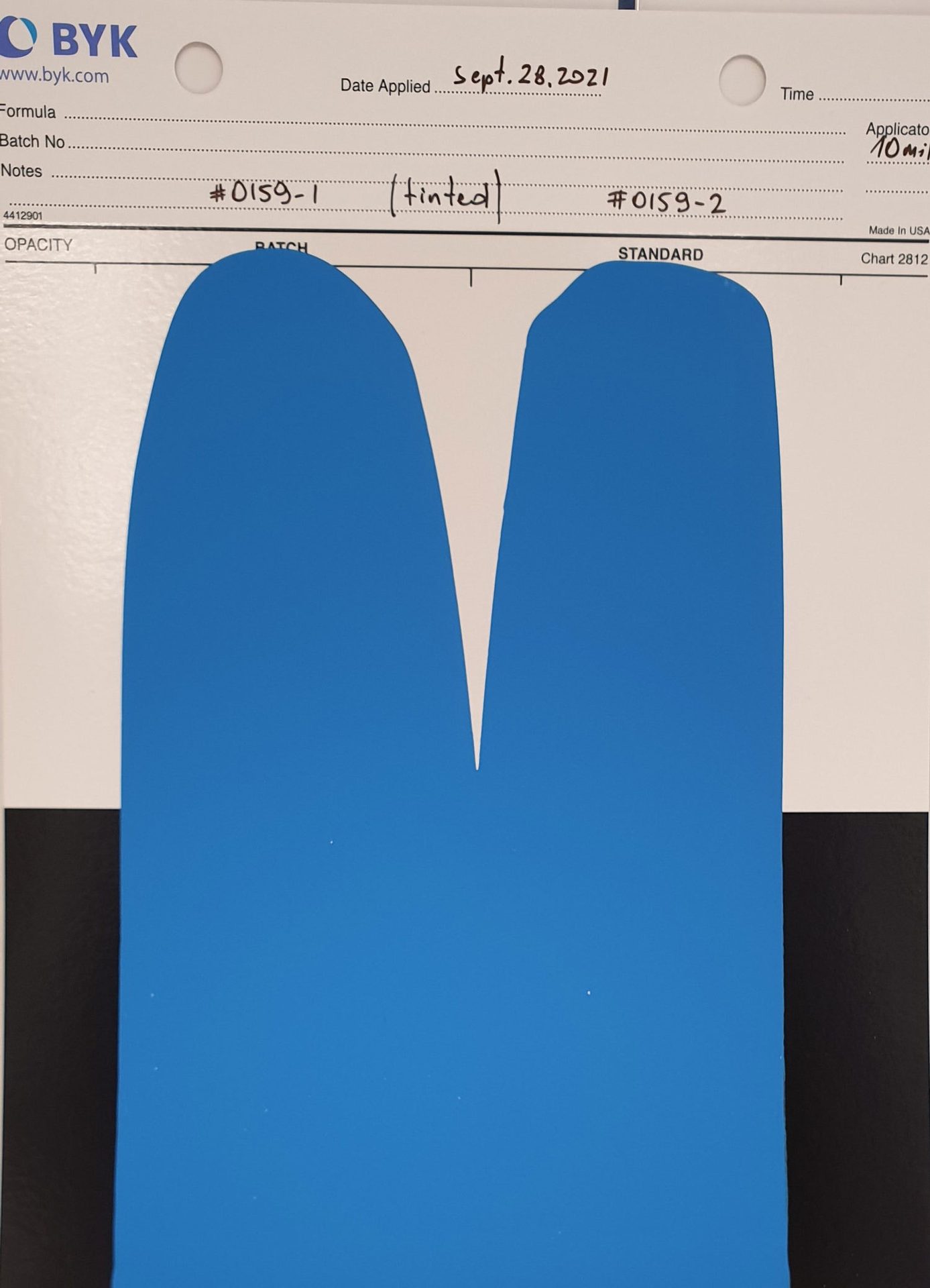
FIGURE 13 ǀ Color compatibility test results.
The tested HEUR thickener No. 2, therefore, does not show any effect on changes in the shade of color with the change of the dose in the range in which it was tested.
Summary
Novice latex paint formulators face the difficult task of selecting raw materials and testing them to develop paints that meet the demanding expectations of the market. In the case of thickeners as shown in this article, it is not easy to interpret each parameter after just one or two laboratory tests, especially as the thickener dose may not always improve the improvement as it increases in the formula. That is why it is so important for the raw material producers to adequately supply technical materials with extensive starter formulations and case studies for different raw materials, ladder doses and comparisons between competing raw materials. Properly prepared technical materials are the basis for a quick and efficient start of tests and drawing conclusions based on repeated case studies in specific paint manufacturer formulations.
For more information, e-mail artur.palasz@spektrochem.pl.