Ready to proof - 08/08/24 NB
CB proofed 8/8 - Niki, the tables are correct but there are a couple of other comments below.
KJ proofed 8/8: Ready for author
FORMULATING WITH MIKE
By Mike Praw, Technical Service and Development Manager – Coatings and Performance Products, Indorama Ventures: Integrated Oxides and Derivatives, The Woodlands, TX
The Keys to
Co-Solvent Selection
Video credit: Hamster3d, Vetta, via Getty Images.
Almost 15 years ago, I published an article1 on how different co-solvents will affect the early film properties of a coating—such as early hardness development and early water/blush resistance. With the changes in coatings and regulations over the past 15 years, it is time for an update.
Co-solvent choice is a significant challenge faced by waterborne coatings formulators. The co-solvent has more influence on early hardness development and early water resistance than the resin, and this is often overlooked. I classify co-solvents as solvents added to lower the minimum film forming temperature. And as they evaporate, the MFFT increases and eventually gets near or matches the glass transition temperature (Tg) of the polymer.
Some questions to think about:
- Do you choose hydrophilic or hydrophobic?
- Is slow or fast evaporating better?
- How do zero-VOC choices such as plasticizers compare to co-solvents?
Plasticizers or super-slow-evaporating solvents are similar to co-solvents, but since they evaporate so slowly, their effects on the coating are long term. This is why plasticizer choice is even more critical.
A study conducted shows the effect of co-solvent balance on early water (blush) resistance and hardness development. A higher-Tg acrylic emulsion (~40 °C) was chosen to highlight the co-solvent differences, and formulated into clear coatings. The final coating was 175 g/L VOC. If I repeated the study today, I would have used a lower Tg resin (~25 °C), and formulated for 50 g/L VOC. The co-solvents used were ethylene glycol mono-butyl ether (EBE, a fast hydrophilic); diethylene glycol mono-butyl ether (DBE, a slow hydrophilic); and dipropylene glycol normal-butyl ether (DPNBE, a slow hydrophobic). A ladder study by varying the co-solvent blend in 20% increments was done for fast and slow hydrophilic co-solvents. A similar study was done with a fast hydrophilic and slow hydrophobic co-solvent blend
The vapor pressures, relative evaporation rates, and solubility in water for the co-solvents are shown in Table 1.
TABLE 1 ǀ Co-solvent properties.
I summarized the learnings from this and other studies in Table 2.
TABLE 2 ǀ Co-solvent effects on a coating.
The coatings were measured for water/blush resistance at 16 hours, and pendulum hardness at 16 and 90 hours.
The 16 hour blush resistance results are shown in Figure 1. Coatings were given a 1-5 rating, with 5 being the best performing/least blushing. The faster the evaporation rate of hydrophilic co-solvents, the better the early blush resistance. Higher hydrophobic co-solvent levels improved early blush resistance.
FIGURE 1 ǀ Effects of different co-solvents on early blush resistance.
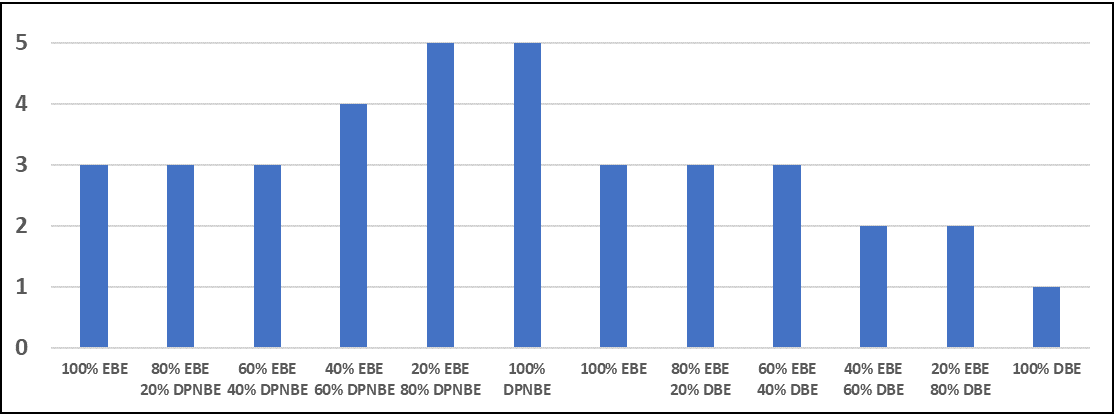
Hardness measurements at 16 and 90 hours are shown in Figure 2. They were measured using a Konig pendulum hardness tester. Hydrophobic co-solvents had a detrimental effect on hardness development. This could be caused by the polymer-hydrophobic co-solvent affinity slowing evaporation of the solvent. Even at 90 hours, the hardness of the coatings with hydrophobic co-solvents was lower.
FIGURE 2 ǀ Co-solvent effect on hardness development.
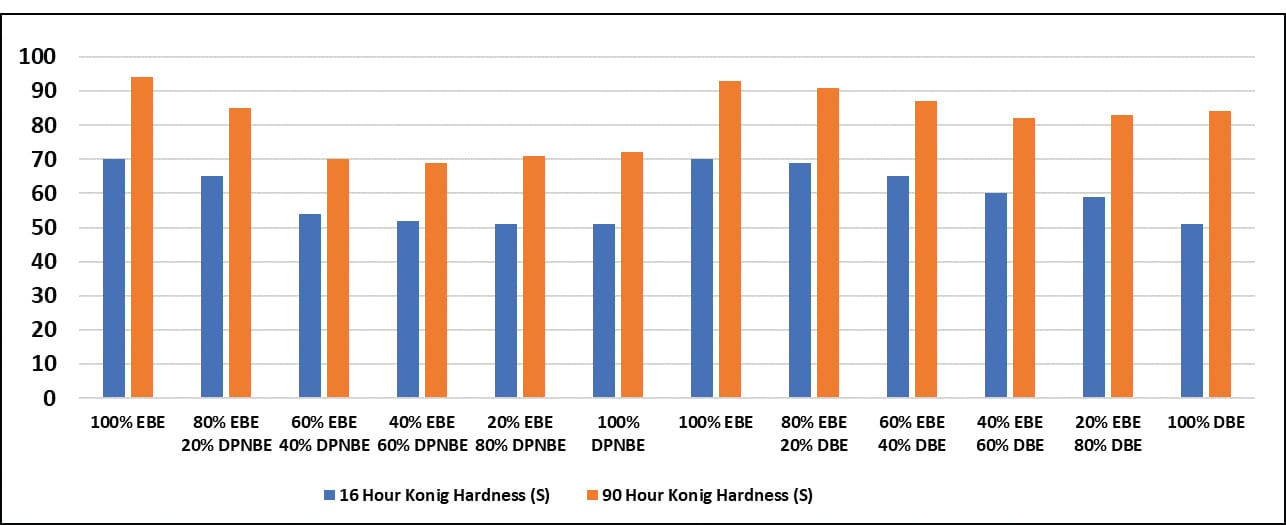
Hydrophobic co-solvents help early water resistance, but hurt early hardness development. For hydrophilic co-solvents, the faster the evaporation rate, the better both the hardness development and early water resistance.
So how do plasticizers compare? They should be classified as super-slow solvents and either hydrophilic or hydrophobic. Hydrophilic plasticizers have a long-term detrimental effect on water resistance and hardness development. Hydrophobic plasticizers will not have much of an effect on water resistance, but will have an increased softening of the film over hydrophilic plasticizers because of their increased compatibility with the polymer.
So which combination of co-solvents is best? The answer is: it depends on which properties of the film are most important, and which ones can be temporarily or permanently modified.
References
1 The original article was published in the May 2010 “Formulator’s Corner” of CoatingsTech.
All information contained herein is provided "as is" without any warranties, express or implied, and under no circumstances shall the author or Indorama be liable for any damages of any nature whatsoever resulting from the use or reliance upon such information. Nothing contained in this publication should be construed as a license under any intellectual property right of any entity, or as a suggestion, recommendation, or authorization to take any action that would infringe any patent. The term "Indorama" is used herein for convenience only, and refers to Indorama Ventures Oxides LLC, its direct and indirect affiliates, and their employees, officers, and directors.