Ready to proof -- Niki 08/07/24
CB proofed 8/8 - a couple comments for Niki below
KJ proofed 8/9. One note for Niki around Figures 4 and 5.
Ready for the author
Video Credit: branex, Creatas Video+, via Getty Images.
Development of More-Sustainable Water-Based DTM Coatings, Part II
Soy-Alkyd Dispersion Paints
By Debora Hense, Stonebridge Coatings Labs; and Kris Weigal, Omni Tech International
In April, we published the Development of More-Sustainable Water-Based DTM Coatings, Part I, which has a background in soy chemistry and sustainability. We also shared Phase 1 of our work comparing the performance of soy-based vs. petro-based coalescents in water-based DTM coatings. In this article, we are pleased to share the updated Life-Cycle Analysis, demonstrating how U.S. soy is one of the most sustainable bio-based feedstocks. Furthermore, Stonebridge Coatings Laboratory expanded its USB-funded research, demonstrating improved bio-based content and performance with soy-based alkyd dispersions in direct-to-metal coatings.
Improved Environmental Impact of U.S. Soybeans
Soybeans are a cornerstone of the global agricultural economy, with production skyrocketing from less than 50 million tons in 1970, to 161 million tons in 2000, and surpassing 350 million tons by 2020. As the second largest producer and exporter of soybeans, U.S. soy dominates, accounting for approximately 90% of oilseed production.
To enhance the environmental sustainability of soybean production, the United Soybean Board (USB) and the National Oilseed Processors Association (NOPA) initiated a comprehensive analysis in 2010. This study assessed the environmental footprints of soybeans and their derivatives. In 2015, a follow-up study updated the 2010 Life Cycle Assessment (LCA) dataset with more accurate, weighted average values reflecting actual processing conditions.
To enhance the environmental sustainability of soybean production, the United Soybean Board (USB) and the National Oilseed Processors Association (NOPA) initiated a comprehensive analysis in 2010. This study assessed the environmental footprints of soybeans and their derivatives. In 2015, a follow-up study updated the 2010 Life Cycle Assessment (LCA) dataset with more accurate, weighted average values reflecting actual processing conditions.
The latest Life Cycle Assessment (LCA) reveals a significant reduction in the U.S. soybean industry's global warming potential (GWP) in 2021 for whole soybeans, soybean meal, and soybean oil, compared to findings from 2015 and 2010. Critical environmental impact drivers included soybean cultivation and harvesting (herbicides, field operations, and fertilizer), transportation, and energy usage in processing.1
Conducted by Sustainable Solutions Corporation (SSC), the LCA analyzed soybean cultivation data from 454 farms across 16 states for 2020 and 2021. Additionally, it examined operational data from 52 soybean processors and 27 soy oil refiners across 18 states for 2021.1
The study shows notable decreases in GWP across all soybean products:1
- Whole soybeans: 19% reduction
- Soybean meal: 6% reduction
- Crude soy oil: 22% reduction
- Refined soy oil: 8% reduction
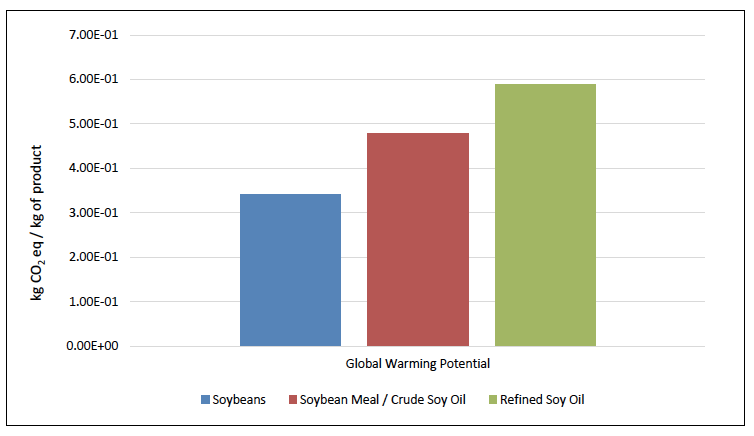
FIGURE 1 ǀ Global warming potential comparison.1
Factors contributing to the GWP reduction include:
- Land management: Improved soil health and water quality.
- Land efficiency: Enhanced seed quality led to a 24% yield increase since 2015.
- Pesticide application and energy consumption: Reduced chemical use, no-till practices, and expanded cover crops.
- Manufacturing: Technological advancements and efficiency improvements, such as switching from coal to natural gas.
These LCA results, commissioned by the United Soybean Board and the National Oilseed Processors Association, highlight the positive impact of prioritizing stewardship and sustainable collaboration.
United Soybean Board Funded Research
The United Soybean Board (USB) has a longstanding history of funding research on various soybean derivatives, spanning applications from waterborne architectural wood coatings to high-performance, low-VOC industrial direct-to-metal coatings.
USB has intensified its research efforts in the past two years in collaboration with Stonebridge Coatings Labs. This partnership aims to demonstrate the performance of sustainable, soy-based coating materials in real-world formulations, directly comparing them to benchmarks established by petroleum-based counterparts.
The collaborative research evaluates soy-based coatings' efficacy, durability, and environmental benefits. The objective is to highlight the potential of these sustainable materials to meet or exceed the performance standards of traditional coatings, thereby promoting their adoption in various industrial applications.
These efforts underscore the USB's commitment to advancing sustainable technologies, and reducing the environmental impact of coating materials.
Development of More-Sustainable Water-Based DTM Coatings with Soy Alkyd Dispersions
One method for achieving water-based DTM paints is using latex polymer resins. These resins result from the polymerization of monomers in a water medium, where tiny liquid particle droplets of organic resin are suspended in water. They require coalescing solvents to form a continuous, viable film. In the April 2024 issue of PCI Magazine, Stonebridge presented work illustrating good DTM performance using latex polymers with soy-based coalescing solvents.
Another approach to making water-based DTM coatings is using water-based alkyd dispersions. These resins are made by heating pre-polymerized alkyds to reduce viscosity and then dispersing them into a surfactant-water medium. The resulting dispersion resins contain 45-55% by-weight resin in water with very little to no solvents. Unlike latex DTM paints, no coalescing solvents are needed for the polymers to form a continuous film. Thus, very-low-VOC paint can be made.
Additionally, using water-based soy alkyds allows paint manufacturers to meet the USDA BioPreferred 20% bio-renewable content required for interior paints sold to the federal government. The latex DTM paints from Stonebridge's Part I of this study contained ~7-10% bio-renewable content with soy coalescing solvents. These alkyd-based paints will include 40-50% bio-renewable content on total paint solids, exceeding the bio-renewable content target.
Alkyd resins are manufactured at various oil lengths and can be modified with acrylic, oil, or urethane chemistries to achieve the desired performance. This study evaluated four types of water-based, bio-renewable soya alkyd dispersions for their effectiveness in a white DTM paint formulation, as listed in Table 1.
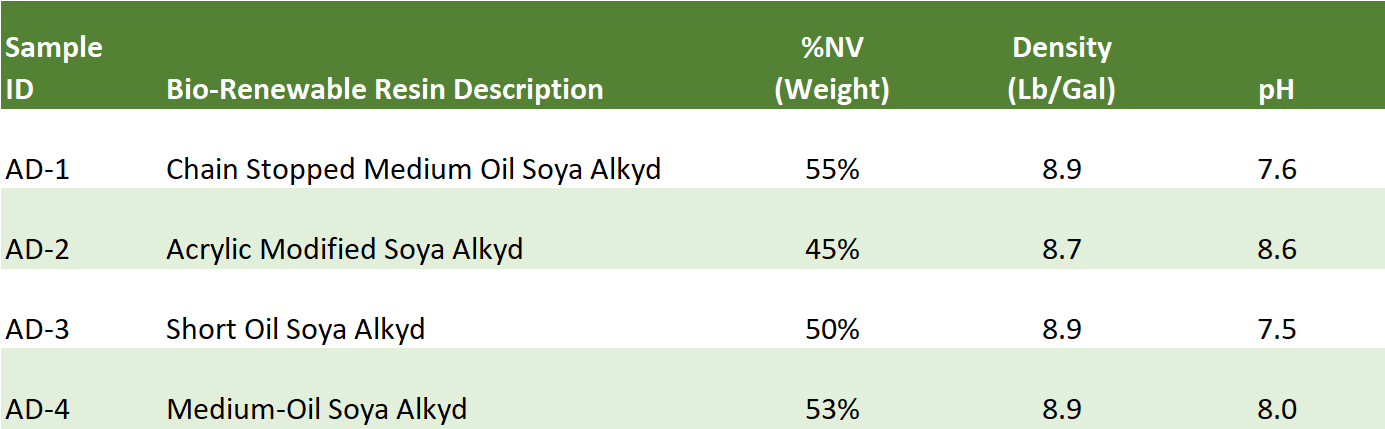
TABLE 1 ǀ List of samples and physical properties.
The four water-based alkyd resins were formulated into standard white semi-gloss paints. The formulations contained 20% corrosion-inhibiting pigment on TRS and titanium dioxide for a total pigment volume concentration (PVC) of 22%. Paints were adjusted to pH 8-8.5 and viscosities to 90 KU. The resulting paint volume solids were ~35% with 0-10g/L VOC. Table 2 illustrates a representative paint formulation used for all of the alkyds.
TABLE 2 ǀ Semi-gloss white DTM paint formulation.
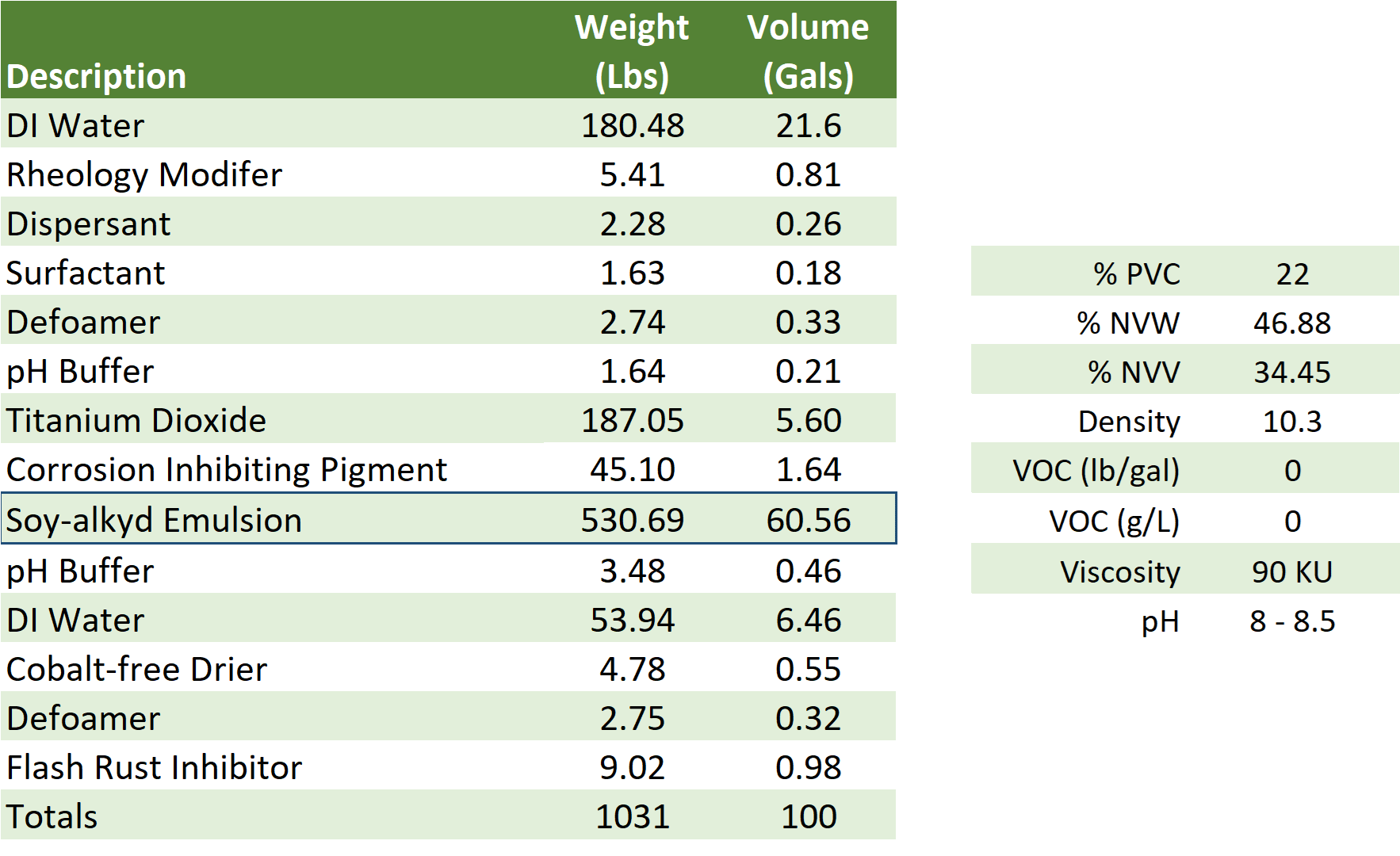
The liquid coatings were tested for pH, Stormer viscosity, and dry times. The paints were applied to sealed opacity charts and steel test panels via drawdown bars and wire wound rods targeting a dry film thickness of 2.0-2.5 mils. Aluminum panels were used for UV weathering. All charts and panels were allowed to age under ambient conditions for 28 days before testing. The dried films were tested for gloss, opacity, hardness, adhesion, flexibility, impact, UV, and corrosion resistance. The paints were tested for corrosion resistance in single and double coats, 2.5 and 5 mils DFT, respectively.
In addition to testing the four paints made by Stonebridge, two commercial latex DTM paints were included as competitive benchmarks, CB1 and CB2.
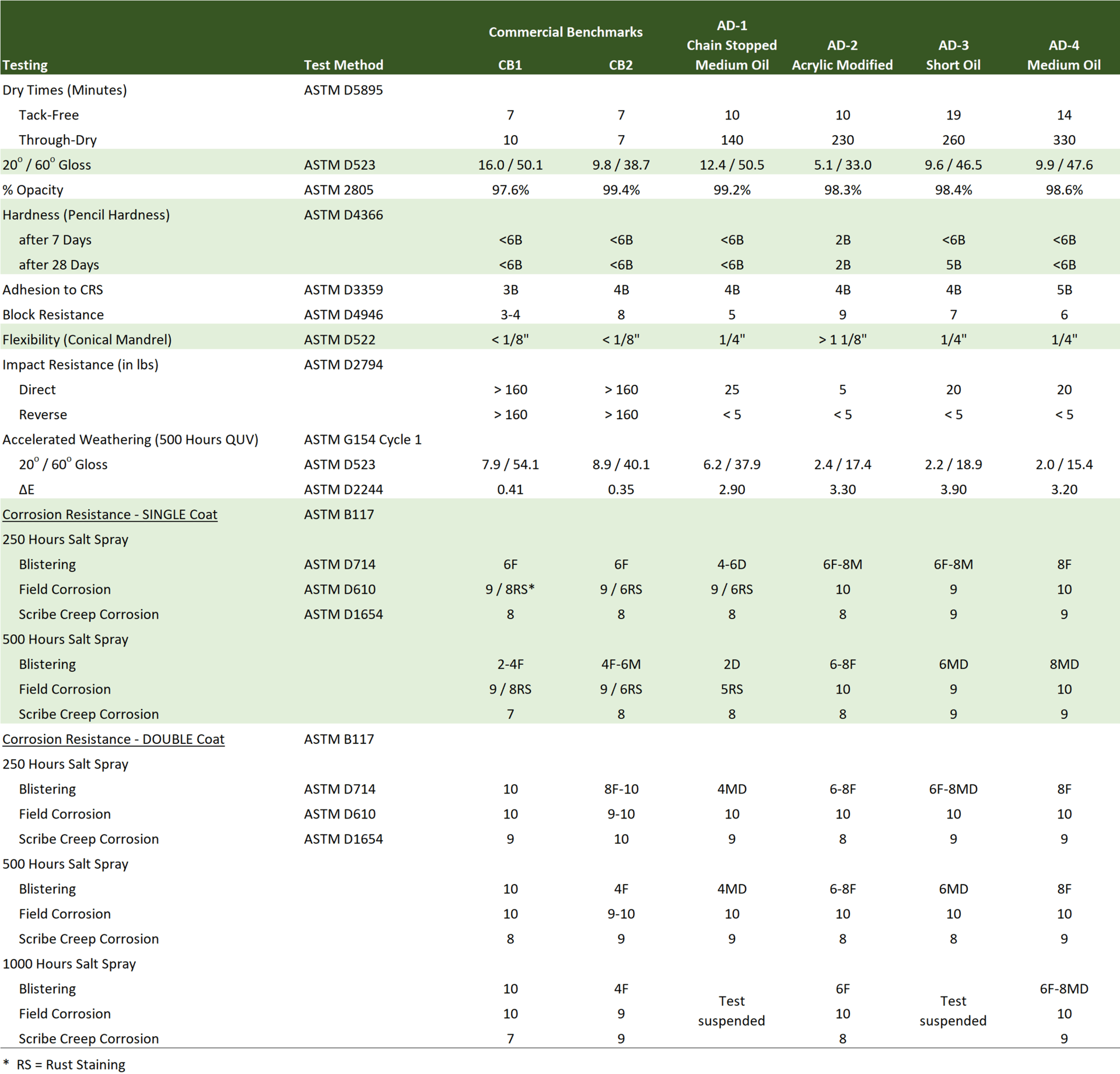
TABLE 3 ǀ Detailed test results and test methods for each test.
Application and Appearance Properties
All the water-based alkyds produced gloss levels in the semi-gloss range with good opacity similar to the competitive benchmark latex paints. The acrylic-modified alkyd yielded a lower gloss than the rest. The dry times of the alkyds were similar to the latex DTM paints in tack-free time but took longer to achieve through-dry time, as is common with alkyds.
Physical/Mechanical Properties
The commercial latex paints and most alkyd paints were soft, with pencil hardness ratings of <6B. The acrylic-modified alkyd yielded the highest hardness at 2B, followed by the short oil alkyd at 5B. The acrylic-modified alkyd also showed the best block resistance of all of the paints, while the latex benchmark CB1 showed the worst. The alkyd paints showed comparable-to-improved adhesion to cold rolled steel, with the short oil alkyd having the best adhesion. Flexibility was good for all samples except the acrylic-modified alkyd, which was more brittle with cracking as high as a 1" mandrel bend. The latex paints were superior in impact resistance.
UV Resistance
The paints were exposed to 500 hours of QUV weathering and measured for gloss loss and color change. The latex benchmark paints performed better than the alkyd paints in gloss retention and color change. The soya alkyds' color change (ΔE) was primarily due to their slightly yellow color bleaching upon UV exposure. The chain-stopped alkyd showed the best gloss retention of the four alkyd paints.
Corrosion Resistance
The paints were tested in single and double coats for ASTM B117 salt spray corrosion resistance at 2.5 and 5 mils DFT. For the single coats, all the alkyds except the chain-stopped alkyd yielded comparable or improved results versus the latex benchmarks. The double-coat samples produced good corrosion resistance with some blistering; the chain stopped showing the most blistering. The top-performing alkyd paints were tested with up to 1,000 hours of salt spray and the latex benchmarks. The acrylic-modified and medium oil alkyd paints showed better results than CB2 and better scribe creep corrosion resistance than CB1. Figures 2 and 3 illustrate photos of the single and double-coat panels after 500 hours of salt spray exposure.
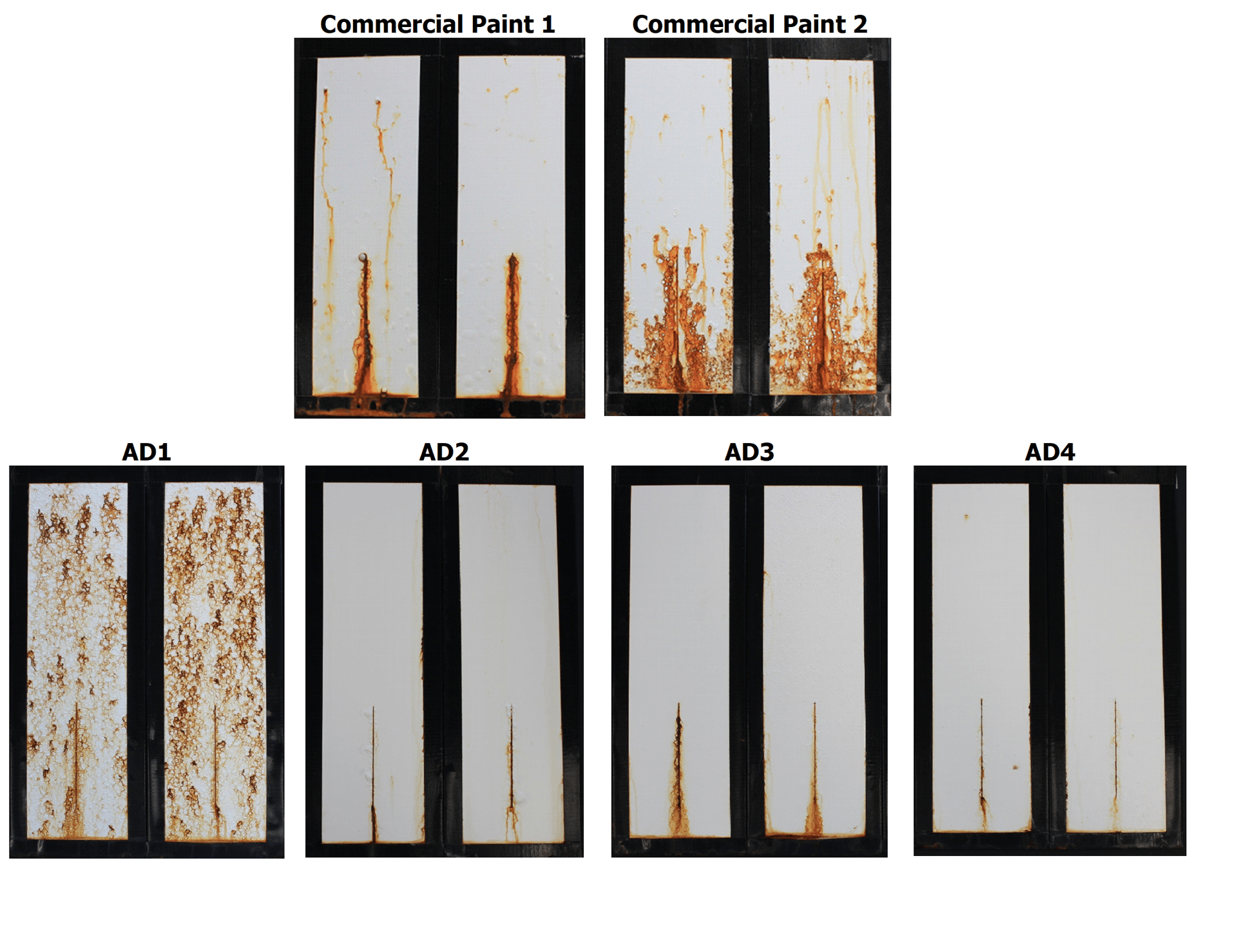
FIGURE 2 ǀ 500 hours of salt spray exposure—single coats (2.5 mils DFT over CRS).
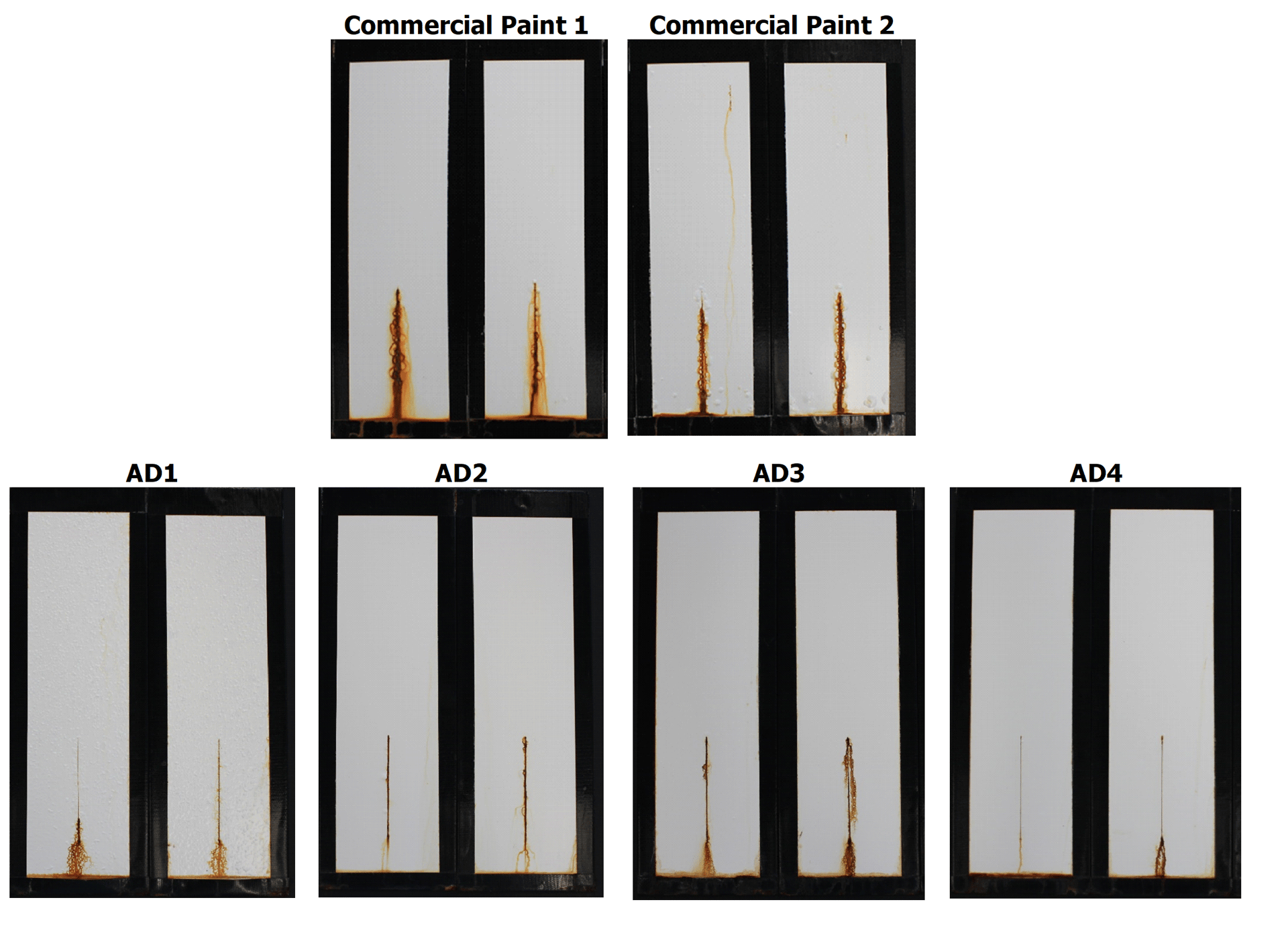
FIGURE 3 ǀ 500 hours of salt spray exposure—double coats (5 mils DFT over CRS).
All the test data was normalized to create total comparison scores, with each property equally weighted. Figure 4 illustrates the total scores and balance of properties by looking at the water-based alkyds for exterior DTM applications, while Figure 5 illustrates the same with UV resistance removed from the scoring for interior use.
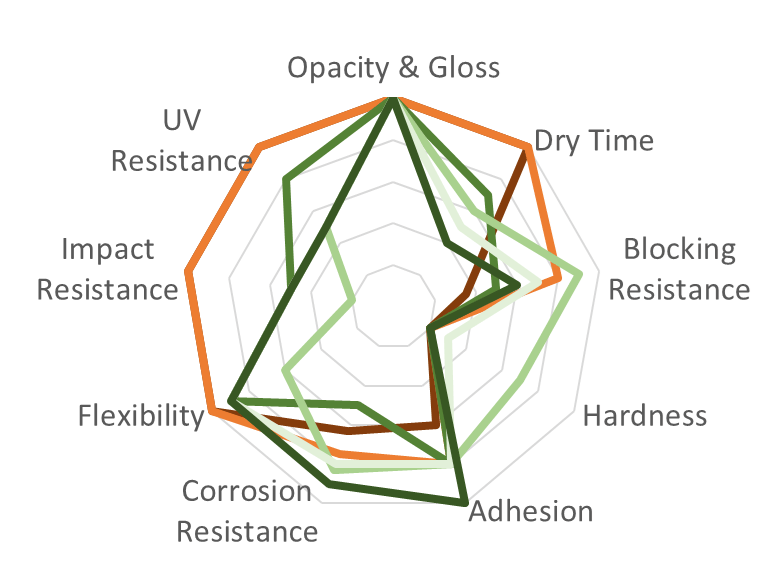
FIGURE 4 ǀ Performance comparisons and total scores for exterior DTM applications.
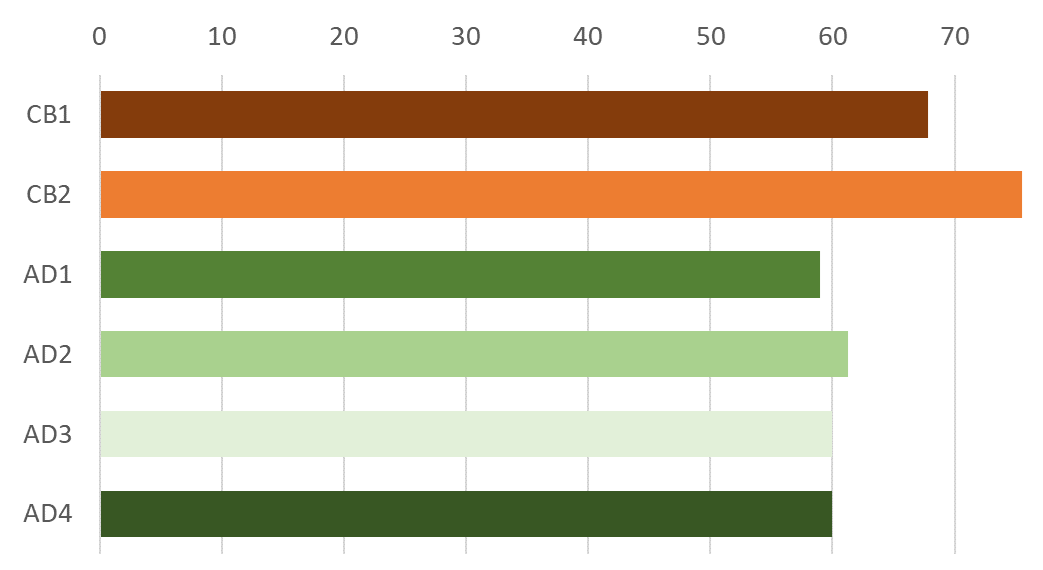
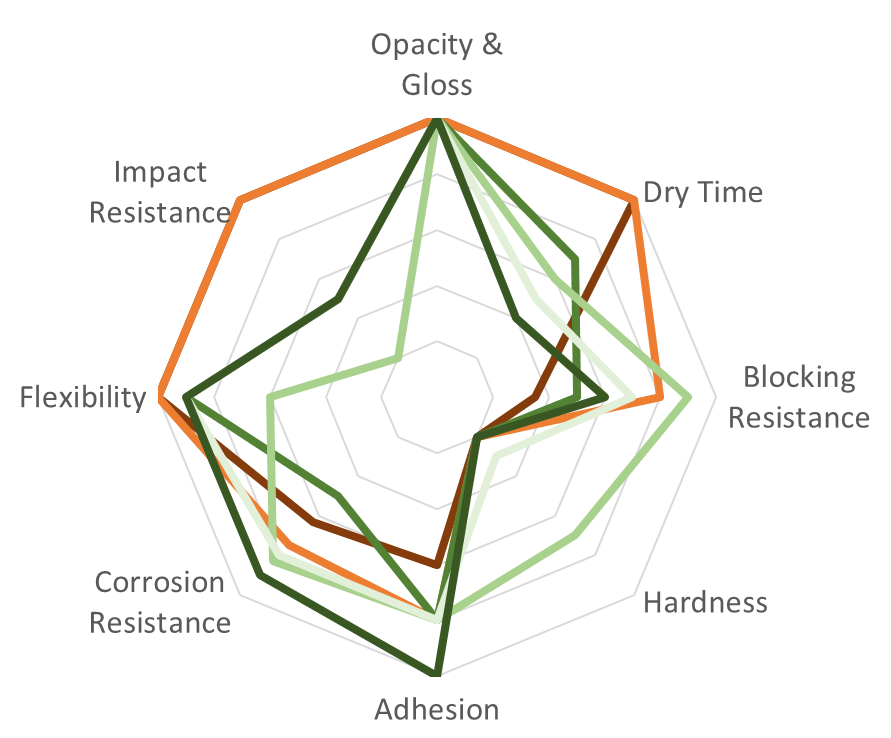
FIGURE 5 ǀ Performance comparisons and total scores for interior DTM applications.
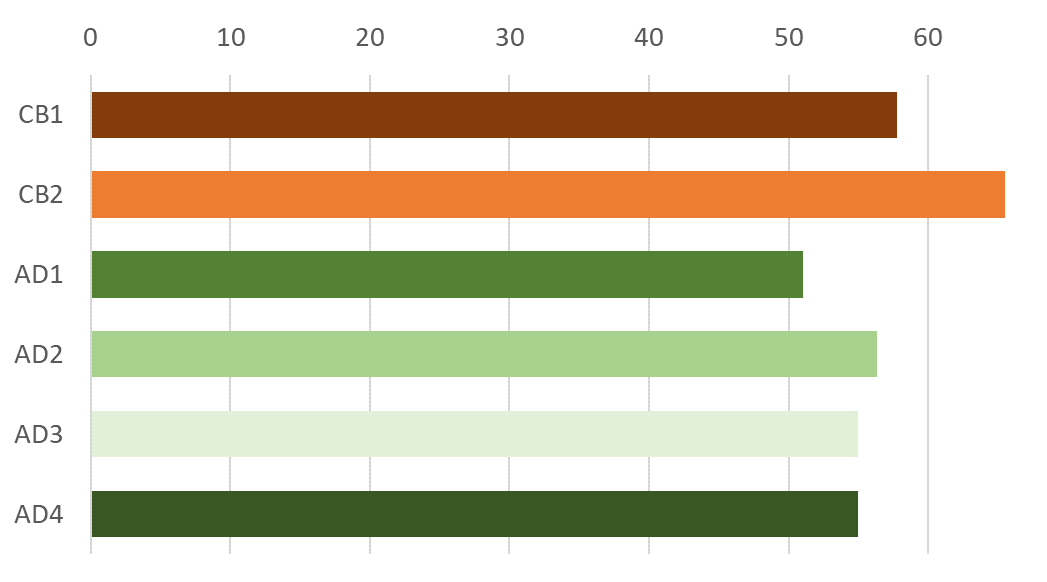
Overall, the commercial latex DTM paints outperformed the water-based alkyd paints. However, the soy alkyd dispersions demonstrated acceptable viability in some DTM applications. More importantly, they proved an excellent approach to meeting the BioPreferred bio-renewable content targets. They showed comparable to improved performance in adhesion, hardness, block, and corrosion resistance. They were slower in through-dry times, had less impact resistance, and had less UV resistance, contributing to their lower total scores and limiting their use to primers or interior paints. Formula optimization may improve these properties.
In conclusion, soybean oil, produced from sustainably farmed U.S. soybeans, is a cost-effective and abundantly available renewable resource. Its hydrophobic characteristics and double bonds enable advanced chemistries that significantly improve film hardness and resistance. This results in superior durability against water and corrosion, making soybean oil a compelling alternative to petrochemical-based materials for direct-to-metal and architectural coating applications.
Ongoing Work
Stonebridge is currently assessing the utility of water-based soy alkyd dispersions for interior and exterior wood applications and using soy solvents in solvent-based, low-VOC coatings. Future work includes a technology assessment of soy-based polyol resins for use in single- and dual-component air-dry and bake coating applications.
Acknowledgments
The authors would like to acknowledge the assistance of our colleagues Brandie Bennett, Jane MacDonell, and Jessica Lake and express gratitude for funding from the United Soybean Board (Projects 23-106-D-A-1-A and 24-106-D-A-1-A).
References
1 Life Cycle Assessment of U.S. Soybeans, Soybean Meal, and Soy Oil. United Soybean Board and the National Oilseed Processors Association. 2024.