Ready to proof -- Clare 9-15-22
KJ proofed on 9/15. I have no changes to the text, however I can't open the original figures, so I can't double check that they are in the rigtht spot. Courtney, if you can open them, can you be sure to look at each figure in here - compared to what was sent - and make sure they are correct? They are all so similar, but there are slight adjustments in each bar chart with the height of the bars, or where the colored triangles are - so you should be able to identify each one. If you can't open them Clare can convert their files to jpgs for us. Thanks!
CB proofed 9/15 - clean on my end
Credit: mevans, iStock / Getty Images Plus, via Getty Images
Measuring Black – but How?
By Kai Krauß, Andrea Höpke and Markus Mahn, Orion Engineered Carbons
Special measurement techniques, sample preparation, and attention to detail are prerequisites for the measurement of high-gloss, deep-black coatings. Many believe that the device they use to measure colorful surfaces on a daily basis can also be applied for black measurements without any issues. However, as reflection values approach zero, as is the case for deep-black surfaces, certain technical aspects mean the colorimetric evaluation cannot be carried out reliably and reproducibly. As many are not aware of this, measurement results are often obtained that suggest excessive blackness values or overly blue undertones.
In our last publication on color measurements in Paint and Coatings Industry Magazine in May of 20221, we focused on sample preparation and correct calibration, which have a significant influence on the measurement result. In this part, we look at another aspect, namely which measurement geometry is best suited for each range of color depths.
Optical Color Perception
All measurements should strive to establish a correlation between the measurement result and what can be seen visually. The human eye, in the absence of defects of vision, is still the best measurement instrument we have. Published data, often suggesting very high color depth values or blue undertones, are of little use if they do not reflect the optical perception and can only be achieved through the selection of a certain measurement geometry.
Therefore, this study uses three typical measurement instruments (two tabletop devices with different measurement geometries, and one handheld device) that are often used in the industry:
- Instrument A: Tabletop device with a geometry of d/8°
- Instrument B: Handheld device with a geometry of 45°/0°
- Instrument C: Tabletop device with a geometry of 45°/0°
The objective of the study was to assess how these geometries influence color values and whether a certain measurement geometry should be preferred. The introduction provides a short explanation of measurement technology and the approach to characterize black coatings. More detailed information can be found in references 1, 2, and 3.
Blackness Values
Measured values for black coatings are to be found in the L*a*b* color space, with values below five on the L* axis. This is equivalent to less than 0.1% light reflection. With deep-black, high-gloss coatings, such as the standard topcoats used by automotive OEMs, the values of L* can easily be less than one. The colorimetric properties of a coating system containing carbon blacks can be described using the hue-independent blackness value (jetness, MY). The measurement method is specified in DIN 55979. This is complemented by the absolute contribution of hue, dM, which is often also called the undertone. The blackness value specifies the black content, in other words how deep the black is from a colorimetric or optical perspective. The undertone describes the colorimetric or optical perception of the color shade. The undertone is referred to as blue if dM is greater than zero and brown if dM is less than zero.
A blue undertone is generally preferred for technical applications, especially in automotive topcoat systems, as it yields a more saturated finish and an impression of brilliant color. Brown undertones are preferred for interior applications, and for wood coatings in particular.
Measurement Geometries
The measurement described in DIN 55979 was introduced to facilitate better differentiation in the region of lowest reflection and to determine the blackness of black coatings with high color depths. This places great demands on the measurement technology itself.
A large measurement aperture is necessary for accurate measurements, to ensure that the maximum possible amount of reflected light reaches the detector. In addition, the instrument must guarantee an accuracy of at least four decimal places in the measured reflection values, and the software used must be able to process this as well. Replicate measurements should show very small standard deviations to ensure instrumental noise is at a minimum. The calibration standard employed should be a black hollow body (light trap) since the blackness levels of commercially available black calibration plates usually do not cover the deep-black range of interest for the present measurements.
The measurement geometry generally varies between 45°/0° or 0°/45° and d/8° or d/0°. In this article, the two most common geometries are compared to each other. The first of these is the 45°/0° geometry, as shown in the upper panel of Figure 1. The sample is illuminated at an angle of 45° using a circular lamp and measured perpendicular to the surface at 0°.
For comparison purposes, the equally common d/8° geometry was selected. Here, the Ulbricht sphere, a spherical measurement geometry, is used to generate diffuse light (Figure 1, below). This measurement geometry includes a gloss trap. The results vary depending on whether the trap is open or closed. When it is closed (gloss included), the measurement yields surface-independent color values, which the human eye is not capable of perceiving by itself. When it is open (gloss excluded), the measured values are close to the impression of the human eye. Therefore, the present experiments were performed excluding the effect of gloss on the measurement (gloss trap open).
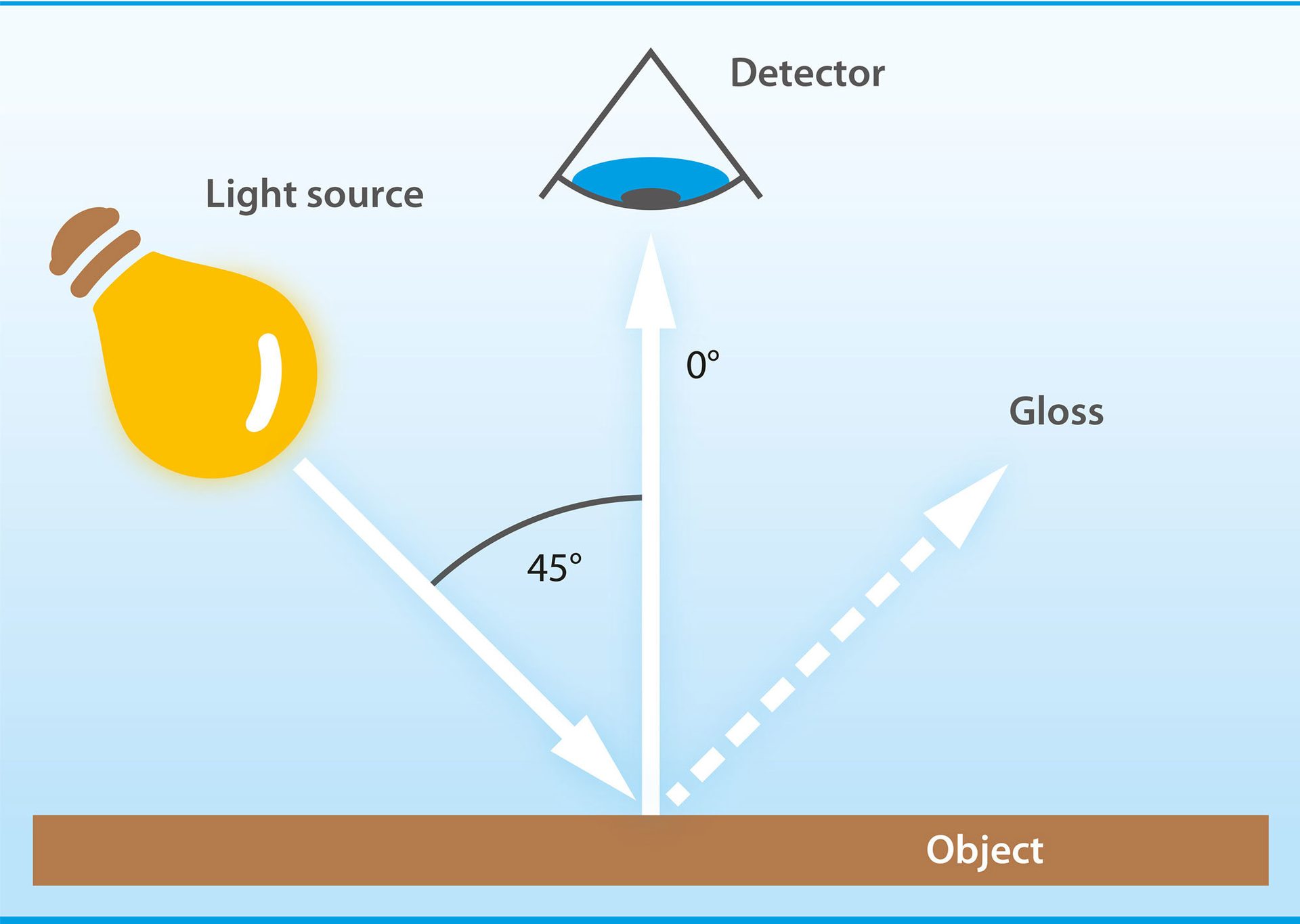
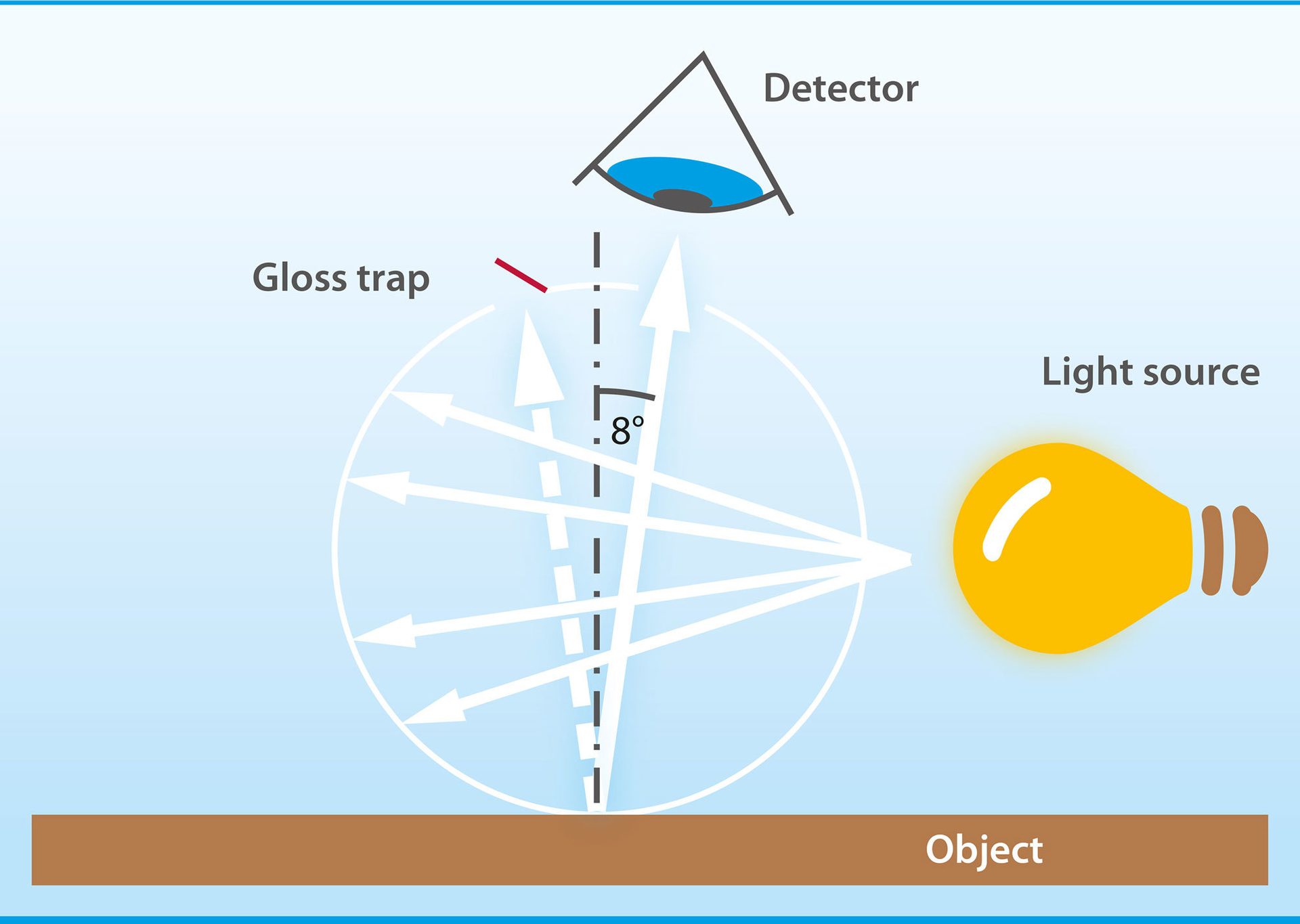
FIGURE 1 ǀ 45°/0° geometry (top) and d/8° geometry (bottom) to measure jetness and undertone.
Careful Preparation and Handling
The measurement instrument should ideally be placed in a clean, air-conditioned environment, since even temperature fluctuations can influence the results in the present measurements, which are close to the instrumental noise level. Each instrument uses its own calibration standards, which can also lead to inconsistent results. Because the state of zero reflection is defined using the black standard, the design and cleanliness of the standard is of crucial importance. Another important prerequisite is that calibrations must be carried out for all measurements; calibration curves stored by the instrument must not be used. Moreover, the careful preparation and handling of samples, described in detail in Reference 1 must be taken into account. If there are a lot of dirt or dust particles in the air, or on the sample to be measured, their reflections can also result in blackness values that are too low. This is especially true when calibrating the instrument.
With all measurements described here (except for the single measurements in the final section), each reported value is the mean of five different individual measurements, which should help avoid outliers. These five individual measurements are always made on the same spot on the sample, which is a coated plate.
Low to Medium Color Depths
In the first stage, three different samples that fall into the low-to-medium color depth range were measured. This essentially covers the range of typical architectural and industrial coatings. The coated plates were placed on the tabletop devices or beneath the handheld device, and three measurements were made at different points on each sample. At each of these three points (Sample 1a, 1b, 1c in Figure 2), five measurements were made three different times, which for example are plotted as three bars for MY and three diamonds for dM. Figures 2-4 show very good reproducibility of the jetness measurements for each of the measurement instruments and different geometries used. All bars for the same spots, as well as the bars for different spots, are of approximately the same height. In terms of the undertones (dM values), the d/8° device demonstrates significantly more scatter than the two 45°/0° devices. When making measurements in this range of color depth, which should be sufficient for most users, the measurement geometry does not have a significant influence. Even a handheld device can provide reproducible results, assuming that it has been calibrated correctly and the sample has been prepared with appropriate care. When using a d/8° measurement device, however, one must also be aware of possible scatter in the values, particularly when measuring the undertone. In case of doubt, the obtained values should be double checked using a 45°/0° instrument.
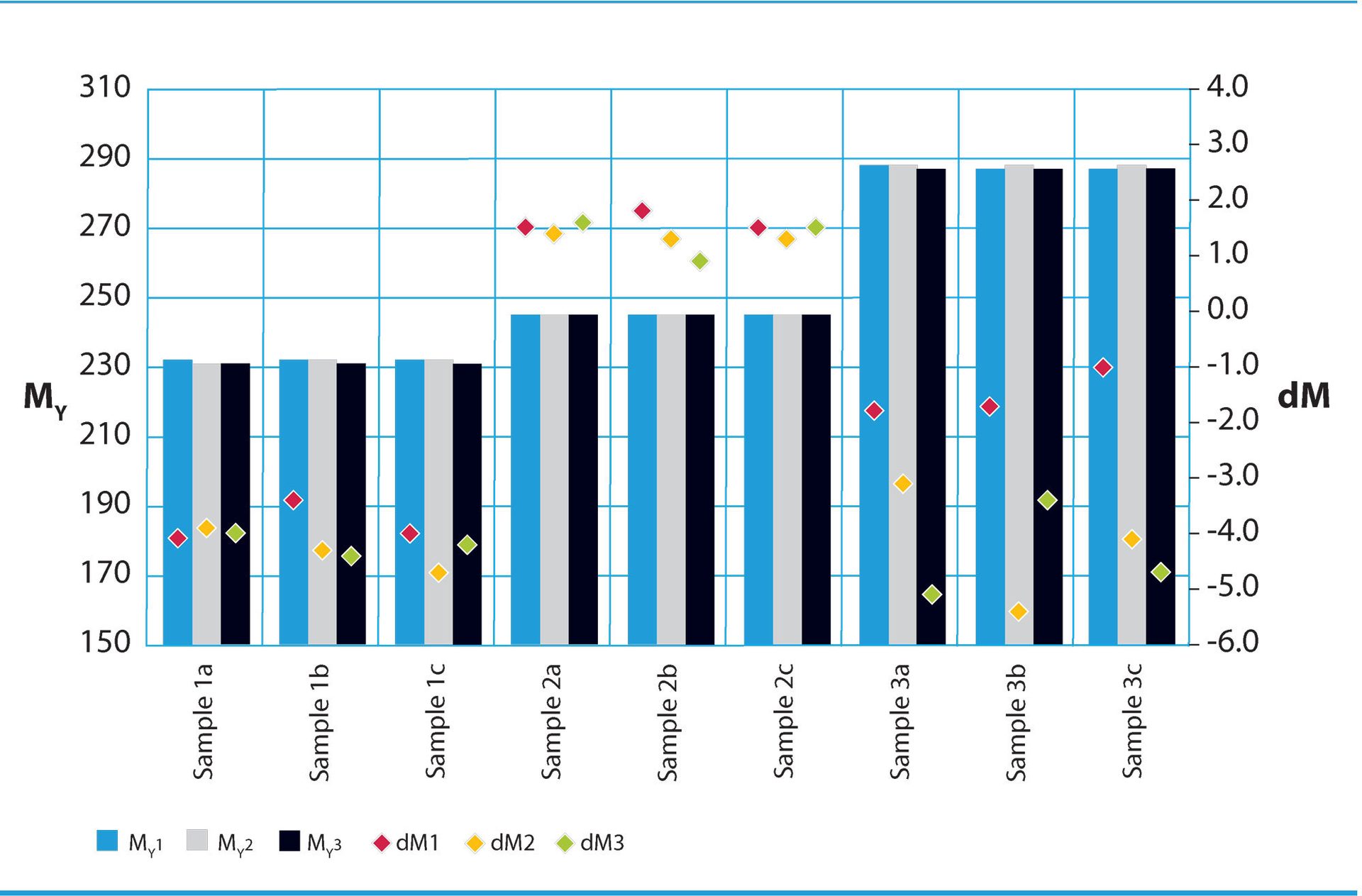
FIGURE 2 ǀ Jetness (MY) and undertone (dM) of Samples 1-3, measured using the d/8° tabletop instrument at three different spots a, b, c. For each spot, three mean values were determined from five measurements each: MY and dM 1, 2, 3.
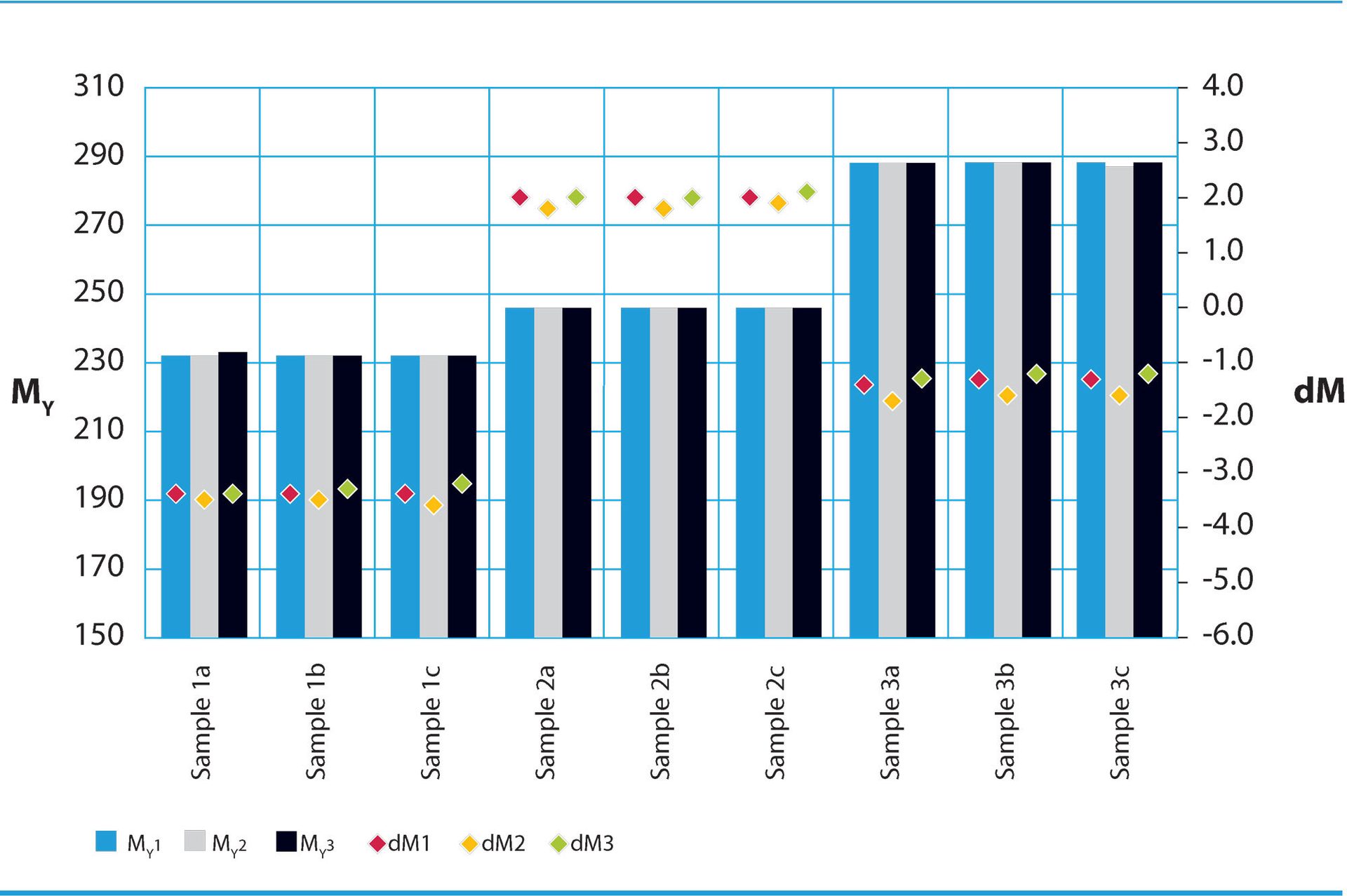
FIGURE 3 ǀ Jetness (MY) and undertone (dM) of Samples 1-3, measured using the 45°/0° handheld instrument at three different spots a, b, c. For each spot, three mean values were determined from five measurements each: MY and dM 1, 2, 3.
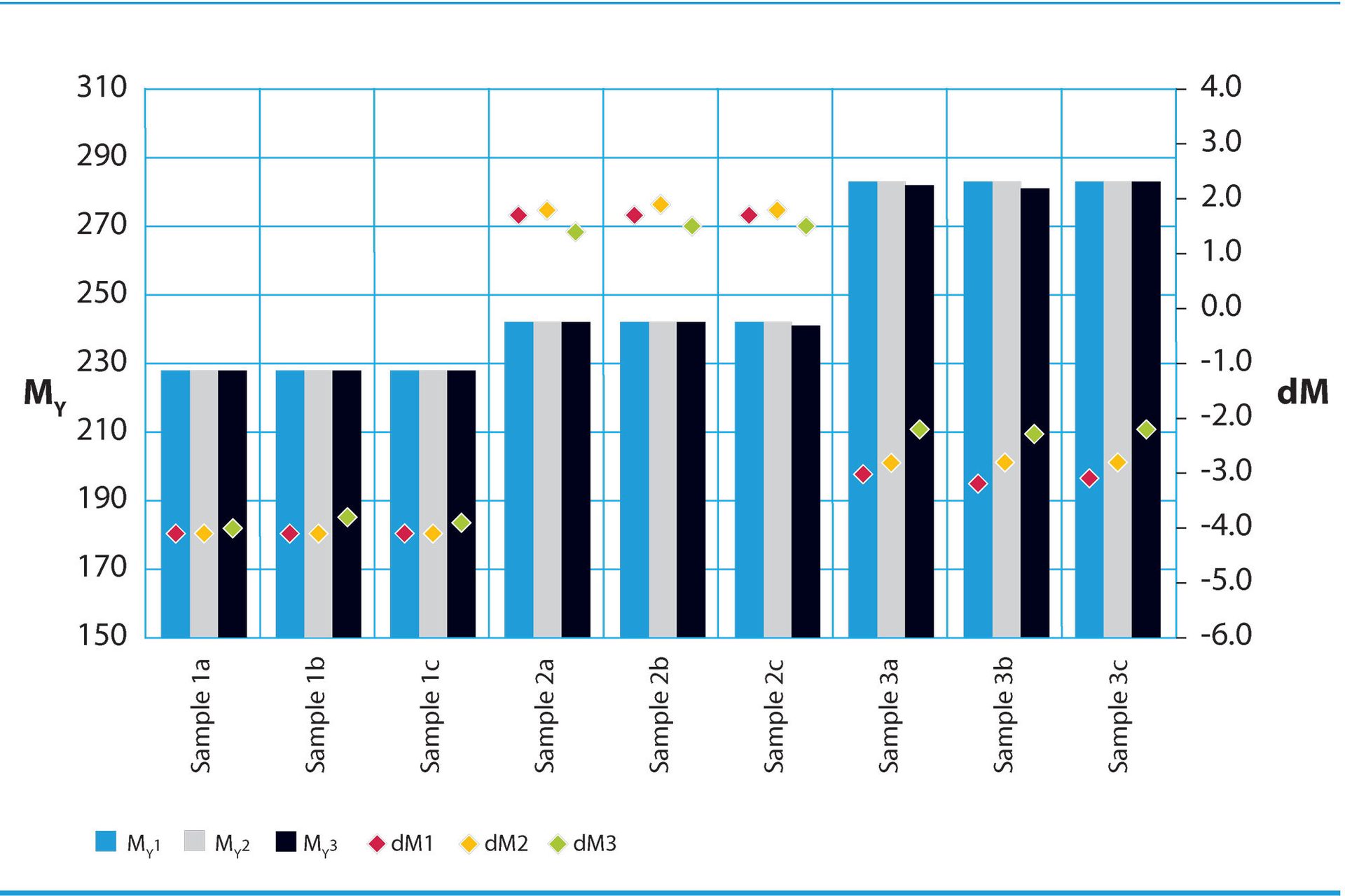
FIGURE 4 ǀ Jetness (MY) and undertone (dM) of Samples 1-3, measured using the 45°/0° tabletop instrument at three different spots a, b, c. For each spot, three mean values were determined from five measurements each: MY and dM 1, 2, 3.
High to Very-High Color Depths
As manufacturers of carbon black, most of the requests we receive to support customers in our laboratories are naturally geared toward the very-high color depth range. Typical fields of application are automotive topcoats, as well as coatings for high-end industrial applications and electronic devices. For this measurement range, we once again placed three plates on or beneath the respective instruments and carried out successive measurements on three different spots. Again, at each spot five measurements were made three different times, without moving the plates in between.
Figures 5-7 indicate that the d/8° geometry is still appropriate for MY values up to approximately 300 (Sample 4), if small decreases in the accuracy of the undertones are acceptable, like the case for Samples 1, 2, and 3. For Samples 5 and 6, on the other hand, there is already significant scatter in the values obtained in the repeatability measurements – in other words, when measuring exactly the same spot in three series of five measurements without moving the plate. Therefore, it cannot be assumed that this geometry yields reliable results.
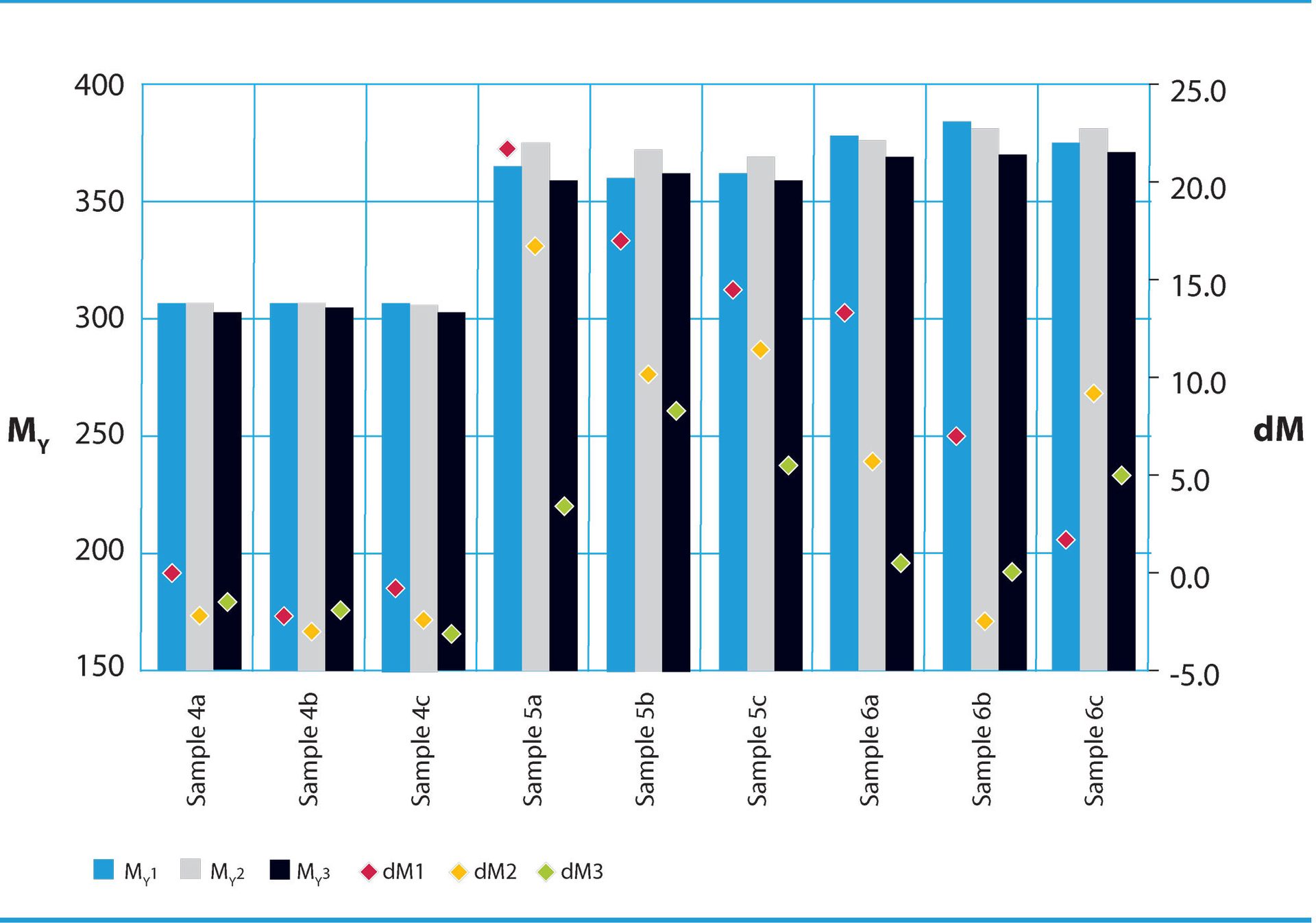
FIGURE 5 ǀ Jetness (MY) and undertone (dM) of Samples 4-6, measured using the d/8° tabletop instrument at three different spots a, b, c. For each spot, three mean values were determined from five measurements each: MY and dM 1, 2, 3.
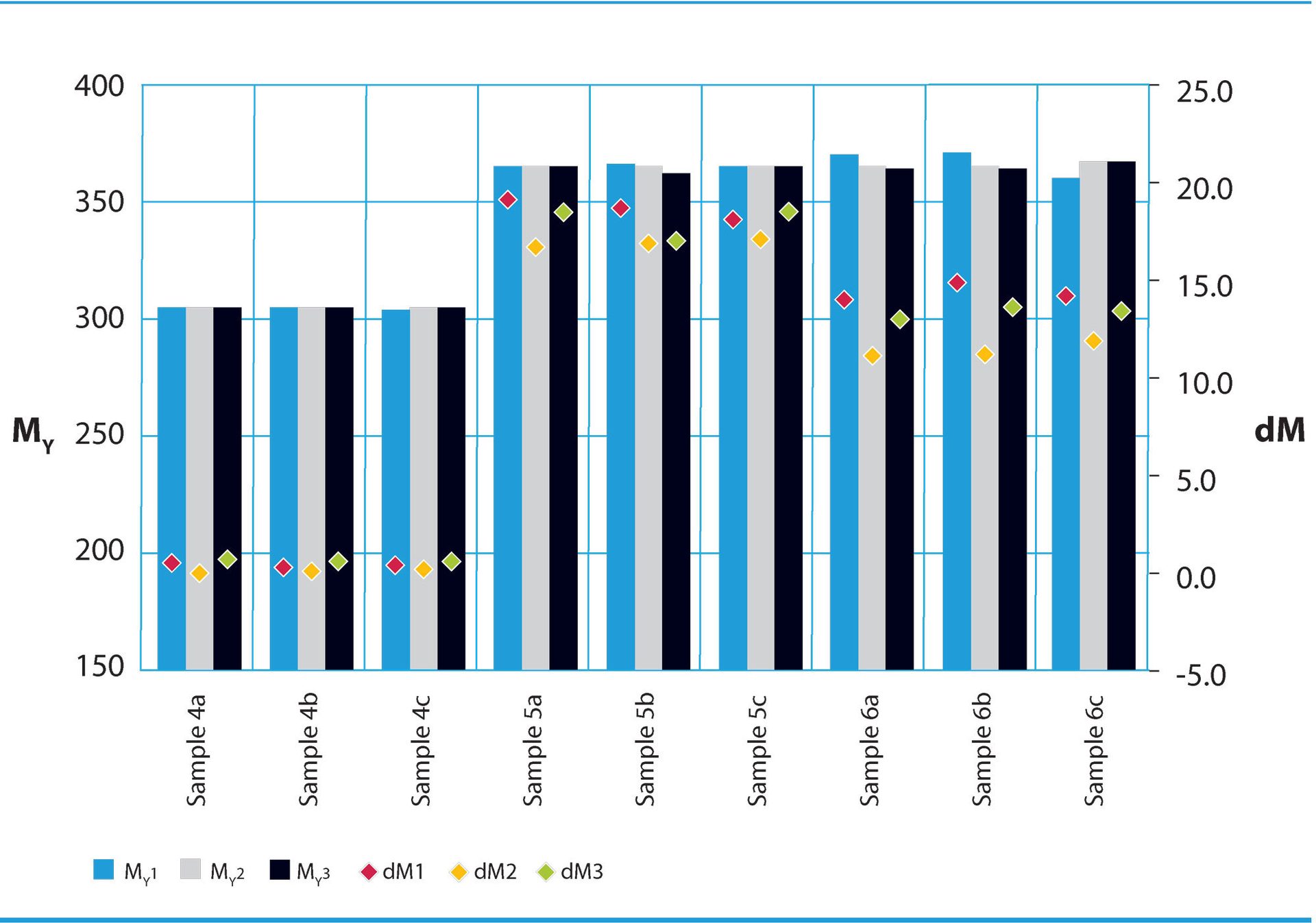
FIGURE 6 ǀ Jetness (MY) and undertone (dM) of Samples 4-6, measured using the 45°/0° handheld instrument at three different spots a, b, c. For each spot, three mean values were determined from five measurements each: MY and dM 1, 2, 3.
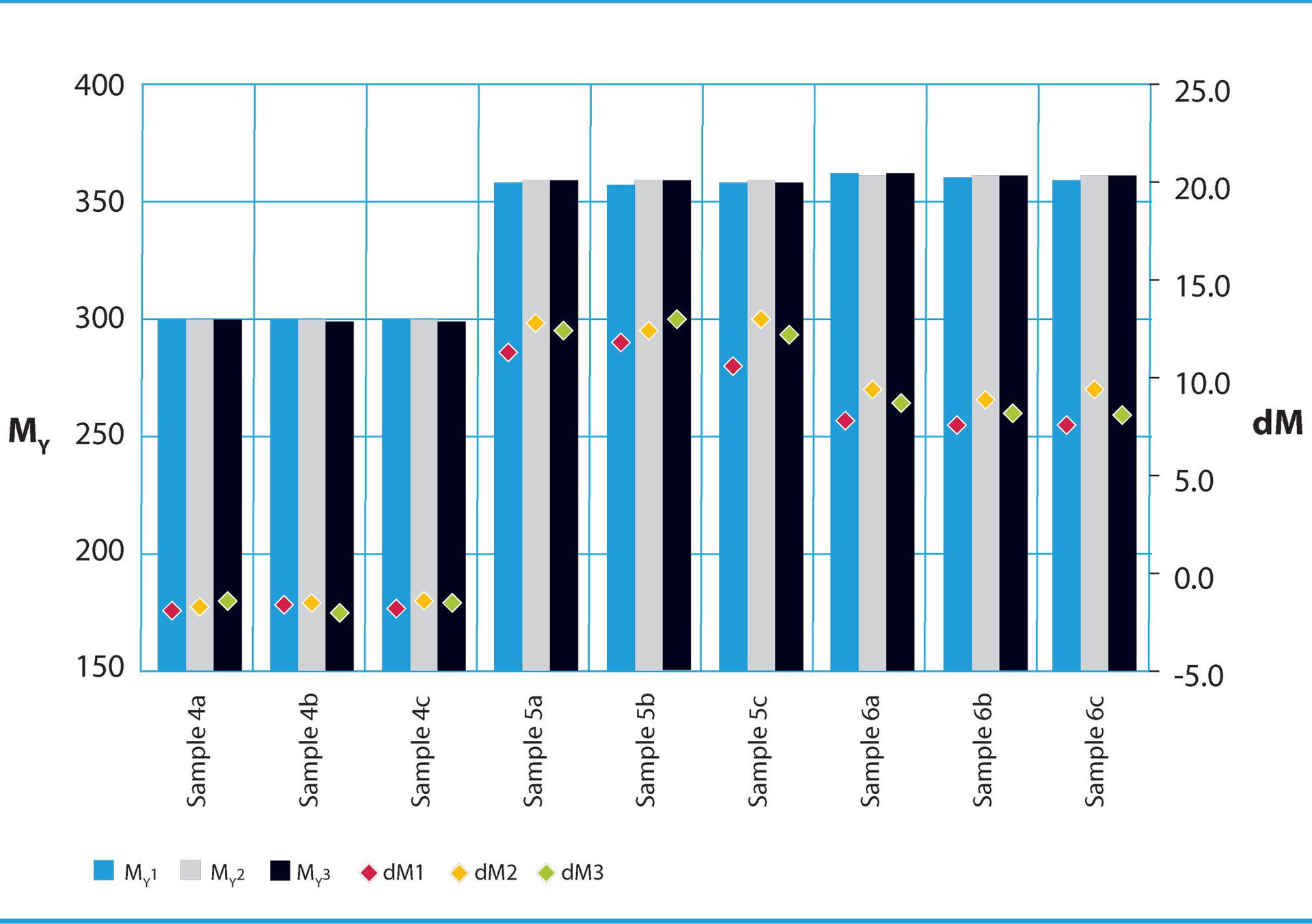
FIGURE 7 ǀ Jetness (MY) and undertone (dM) of Samples 4-6, measured using the 45°/0° tabletop instrument at three different spots a, b, c. For each spot, three mean values were determined from five measurements each: MY and dM 1, 2, 3.
In particular, the results for the undertone, dM, illustrate the poor reproducibility of the measurements. Moreover, the MY values determined using the d/8° geometry tend to be much higher than with the 45°/0° geometry. This is an interesting point for product marketing; but, along with the lack of reproducibility, the question arises whether published MY values measured in this manner are reputable. For this reason, we have opted to use the 45°/0° geometry. While significantly higher values obtained using a d/8° geometry do continue to appear in the literature, we prefer to publish values that, although they may be lower, were obtained through reproducible measurements with a more scientific approach.
Reproducibility at Very-High Color Depths
In the next stage, we compared six single measurements and six averaged measurements in the highest color depth range (Sample 6). The averaged measurements were obtained by making five sequential measurements for each point and taking the mean. Here, we only compared the two tabletop devices with different geometries. The bars (MY) plotted on the left and the diamonds (dM) for each measurement in Figures 8 and 9 represent the single measurements. The bars (MY) on the right and the diamonds (dM) for each measurement represent the averaged values, each the result of five repeated measurements. For each of these series, the measurement spot – the position of the measurement plate on the instrument – remained unchanged. These measurements demonstrate the excellent reproducibility of the 45°/0° geometry and the significant scatter for the d/8 geometry. Even carrying only single instead of multiple (in this case, five) measurements to determine one measurement result, a 45°/0° instrument would still provide better reproducibility than a d/8° setup. In some cases, the latter provides again extremely high MY and dM values.
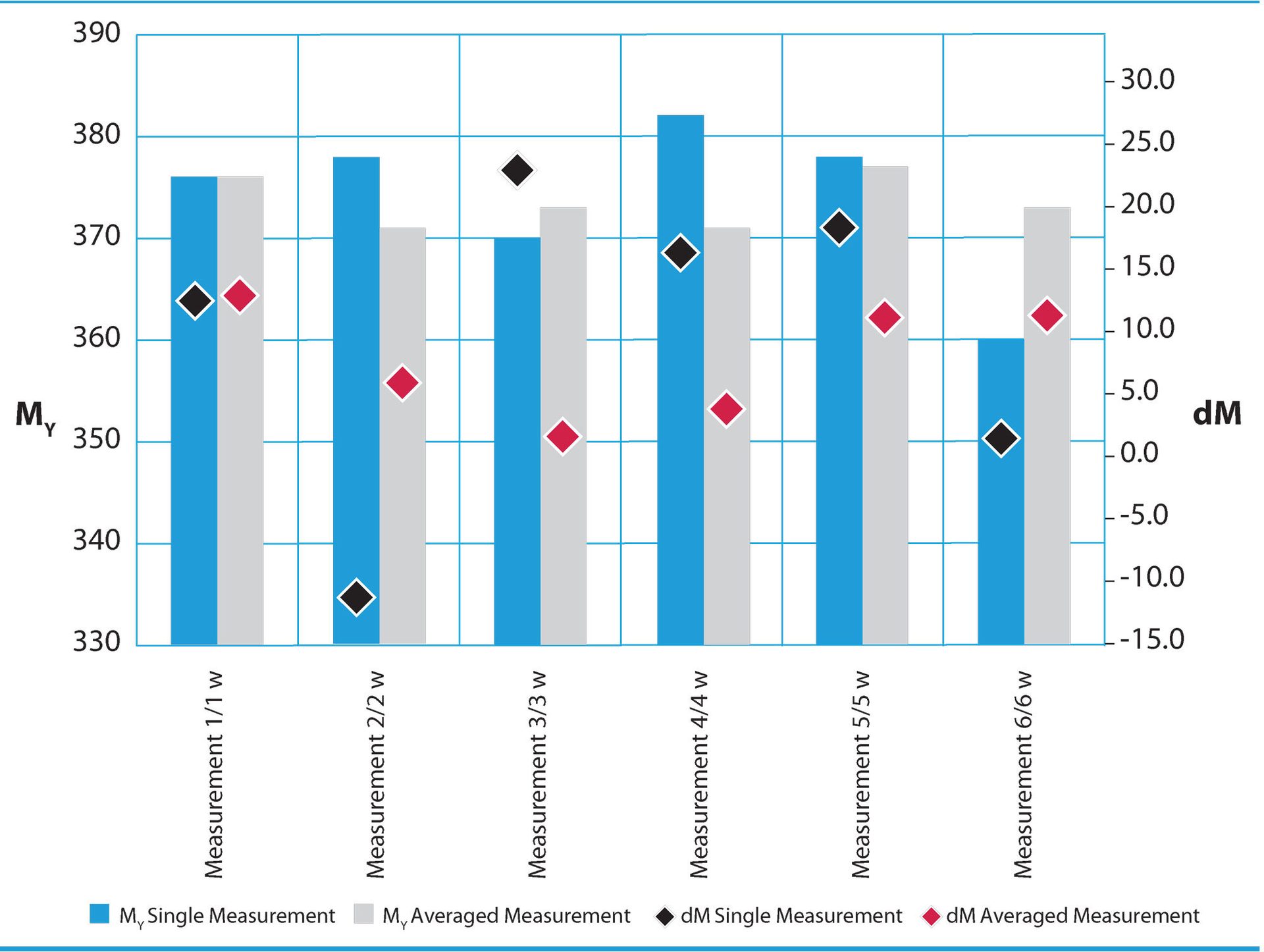
FIGURE 8 ǀ Jetness (MY) and undertone (dM) of Sample 6, measured using the d/8° tabletop instrument; six times as a single measurement on the same spot (1–6) and six times taking the average of five measurements (1w–6w).
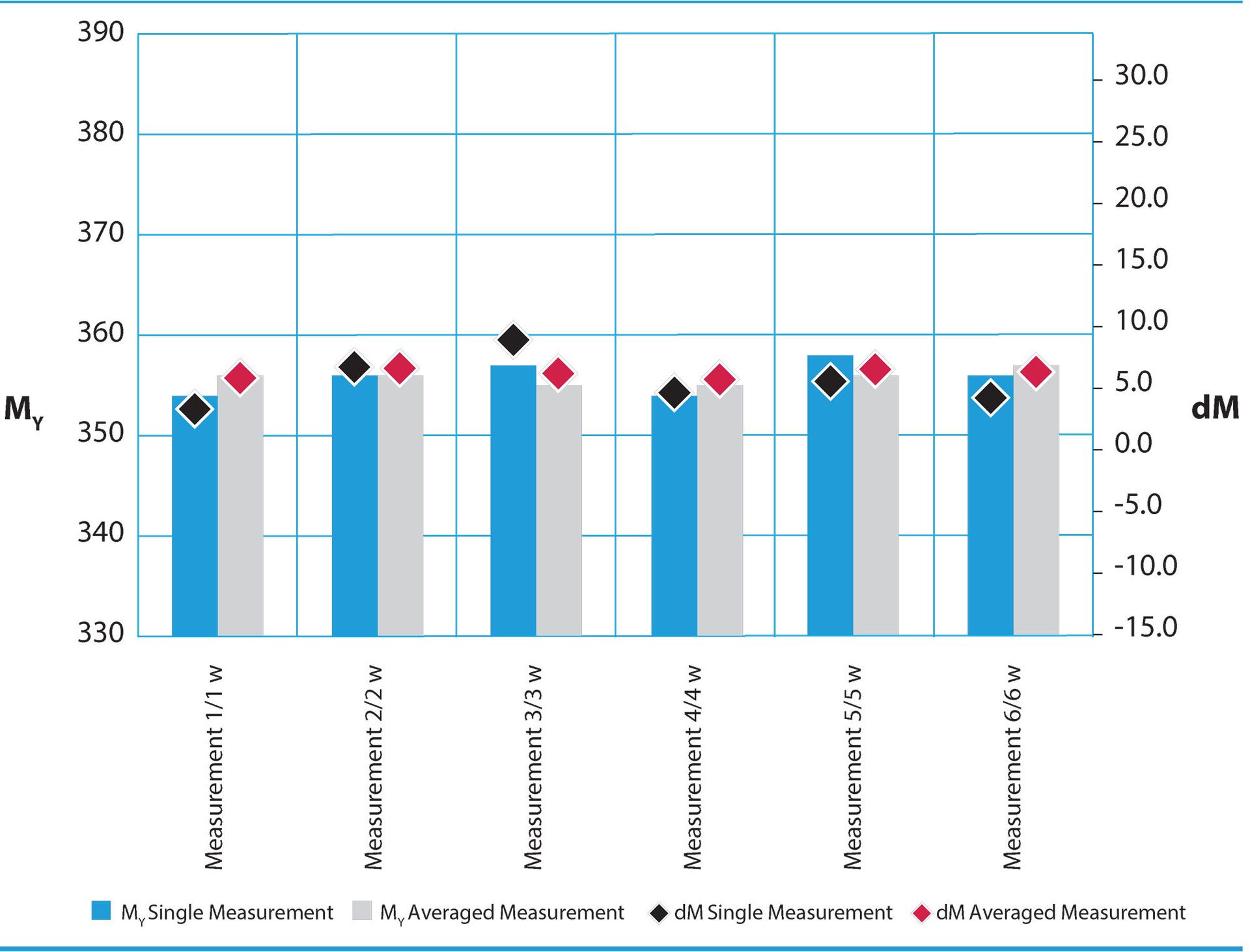
FIGURE 9 ǀ Jetness (MY) and undertone (dM) of Sample 6, measured using the 45°/0° tabletop instrument; six times as a single measurement on the same spot (1–6) and six times taking the average of five measurements (1w–6w).
The dM values range from brownish (negative dM values) to very strong blue hues (over 20). Based on our findings, whenever such high MY or dM values are found, it is advisable to examine the measurement methodology.
Measurements over Several Days
As a general rule, if the results are to be compared to one other, measurements should always be made on the same day using the same calibration. Despite this principle, we decided to carry out measurements in the deep-black range on consecutive days using a new calibration each time, and compare the measurements (Figure 10). This was once again done for all three instruments by measuring a single spot (mean value from five repeated measurements) using plates 5 and 6.
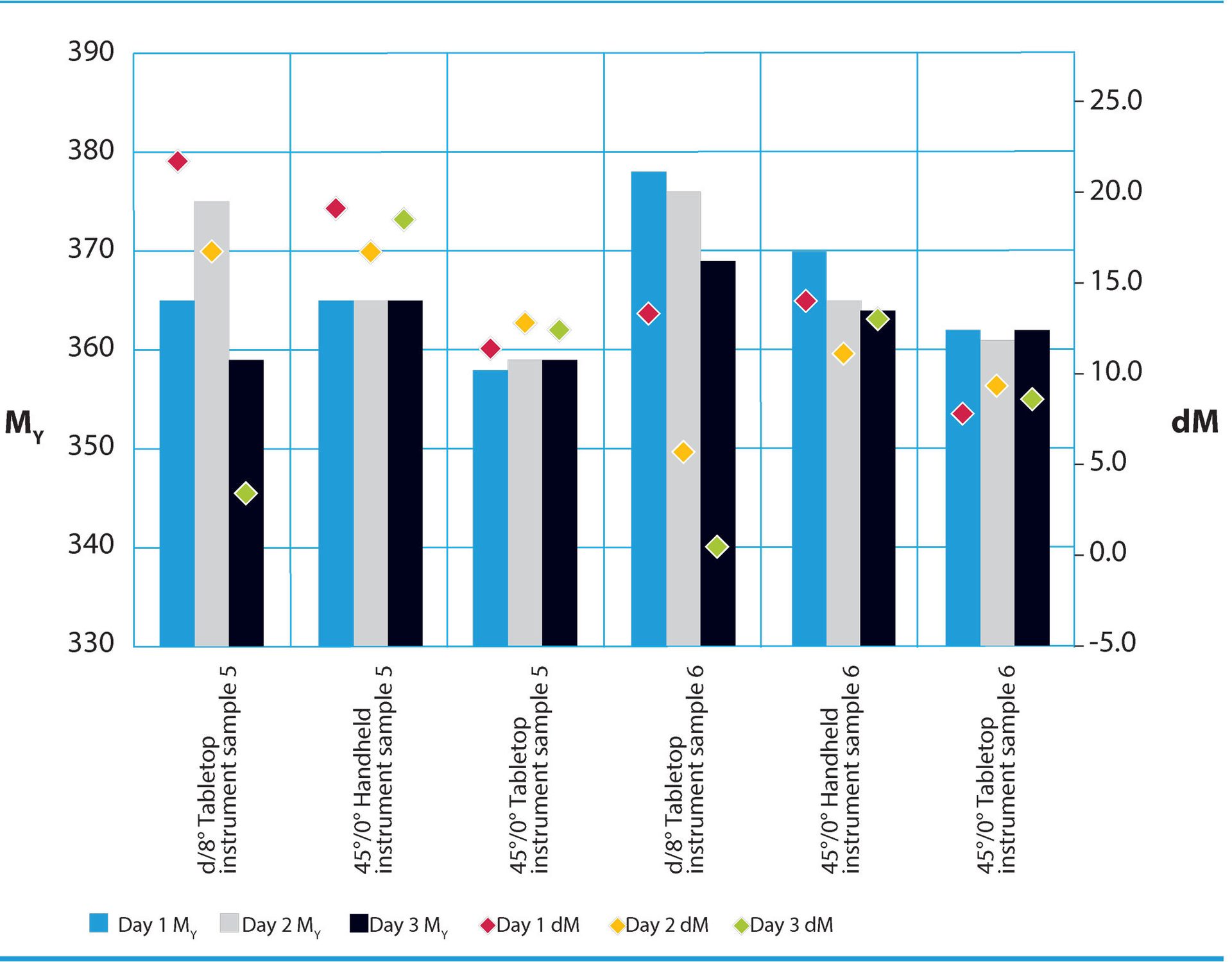
FIGURE 10 ǀ Jetness (MY) and undertone (dM) of Samples 5 and 6, measured on three consecutive days with a new calibration each day, as an average of five measurements.
If all secondary conditions, including siting the instrument in an air-conditioned room, are observed, the 45°/0° geometry still yields comparable measurement results. The d/8° setup did not perform as well, especially in terms of the reproducibility of dM values. The handheld 45°/0° device, with an acceptable level of scatter, comes in second place, while the tabletop 45°/0° instrument shows minimal scatter and is the best option.
To summarize; when carrying out measurements in this very specialized class of jetness, as represented by plates 5 and 6, a 45°/0° geometry should be chosen and multiple measurements always carried out.
Why We Prefer the 45°/0° Measurement Geometry
In conclusion, both measurement geometries (45°/0° and d/8°) have their merits. When measuring high-gloss, deep-black samples, the measurement range one wishes to cover should be taken into consideration.
If the jetness does not exceed MY 300, a d/8° setup will generally produce reliable results. This range covers most applications involving tinting or mass-tone applications of carbon black in, for example, architectural and industrial coatings.
In the area of deep or deepest black coatings, which are regularly used in the automotive industry in particular, our experience and the results presented here show that instruments with a 45°/0° geometry should be used for development and quality control purposes. Color depths (MY) and undertones (dM) can only be determined reliably and reproducibly using this geometry. Whenever extremely high color depths and blueness values are published, they should be critically assessed, and the measurement methodology used to obtain them verified. In the end, the optical perception under directed light is what counts, because the human eye is still the best measurement instrument we have.
*This article originally appeared in the June 2020 issue of the European Coatings Journal.
References
- Krauss, K.; Hopke, A.; Mahn, Black – the Fine Details. Paint and Coatings Industry Magazine, 38, 2022.
- Lippok-Lohmer, K. Farbe und Lack, 11, 1024, 1986.
- Orion Engineered Carbons GmBH. Coloristic Properties of Specialty Carbon Blacks in Full Tone and Tinting Applications for Coatings – Technical Information, 1464, 2015.
- Orion Engineered Carbons GmBH. Specialty Carbon Blacks in Modern Coating Systems – Industry Information, 0402, 2017.